16'x12' Solid Wood Pocket Door
This project was mostly a pipe dream — but the discussion produced some interesting thoughts and information about honeycomb-core veneered panels as a lightweight door or moveable wall solution. April 24, 2012
Question
I've got a contractor asking me to build a door for him that no one else seems to be able to do. It's a pocket door 16 feet wide by 12 feet tall and calls for a quarter-sawn white oak finish. I'm not a door maker, and I have no desire to be, but it might be easier for me to deal with than fight about.
My shop has kicked around a few ideas as to how to join panels into either 4 or 6 foot widths and then piece them together. I don't really think that a tongue and groove, dovetail, or finger joint will hold the entire length of the door. I think the first time someone bumps into a joint or knocks the door, it will split along the joint. The designer won't let me break it into multiple sections. It essentially has to become a flat 1-piece sliding wood rectangle.
How would you build it?
Forum Responses
(Architectural Woodworking Forum)
From contributor J:
Easier to deal with than fight about? I wouldn't bet on that.
I can't imagine this as a solid slab. It would weigh a ton (literally), and would move all over the place. Maybe a welded aluminum frame, with veneered panels hung on it?
From contributor L:
If the door making crews that he has tried to get to build this don't want the job, there is probably a good reason.
From contributor K:
I'm with contributor J on the aluminum frame, and while I was at it, I would try to use the aluminum honeycomb in the panels, if it is to look like a frame and panel.
From contributor C:
This sounds like an opportunity to try out a torsion box design. They are rigid and relatively light in weight. They are great in door applications.
I recently did a project for a restaurant that included a gliding door that was about 6 feet long and 32” tall. This called for zebrawood panels, and it was easy to seamlessly match up the butt joints on them.
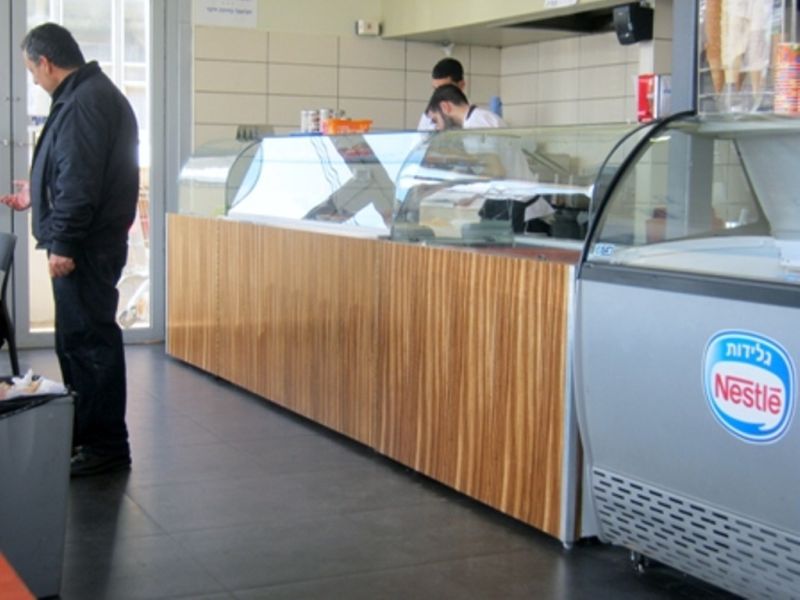
Click here for higher quality, full size image
From contributor M:
I think contributors J and C are on the right track. Check out the nana wall site. They build huge sliding glass wall panels. With veneer applied to a stable, lightweight torsion box design on hardware designed for the weight, it should be doable. Get lots of money for the job.
From contributor D:
White oak that big definitely makes me think torsion box. This is a weight saving building technique on wooden boat decks. Traditional door construction will be way too heavy. Many of the folks building garage doors think out of the box, so to speak, because of weight issues. One fellow in our town actually has a patented technique and builds the biggest custom garage doors in the industry. Not a project for the meek...
From contributor I:
How are they planning on getting this door into the building?
From contributor V:
First, stop referring to the project as a "door." This is a moving wall, and a large one at that. The fact that the contractor calls it a door keeps it within a certain mental and physical budget, when this is an extraordinary project and needs first to be recognized as such. How many of these have you ever seen? Is there a reason?
I agree with the torsion box solutions. This will yield a smooth surface, much like a flush door. The weight will be manageable, but this thing will be very difficult to build, transport or install. Be sure you know what makes for a good torsion box or this could curl like a potato chip. If your guy wants a frame and panel look, then you go to plan B.
However, you need to be sure the plane this door will move in is dead flat, and then you have to make the torsion box dead flat. How you create a dead flat work space for this is the question. See the photo of a flying rig for a sailmaker. Even a 1/2" deviation in either the door or the opening (or both!) will cause problems. Make sure that the builder knows the real difficulty in this request, and is willing to pay to make the door over should it not succeed on the first attempt. I would push towards a full overlay sliding door, with floor guides at either end of the opening rather than true pocket door.
If you are not experienced with this type of project and/or the builder, I would suspect the customer is looking for a patsy to push responsibility onto so he won't have to bear it. Especially if others have turned it down. Why didn't he call you first? I know I am way too cynical, but I have seen it happen many times.
From contributor Y:
If you got the short straw, the torsion box is most likely your best bet. You will definitely have to make it in at least 2 sections, as you won't be able to transport it to the site. Also, can you get white oak ply in 10 foot pieces? You may have to do your own laminations over a lightweight substrate to get a full height veneer and still keep the weight to a minimum. I can only imagine the size of the vacuum bag you will need.
From contributor L:
The only problem I see here is the decorator. Even done as a torsion box, there are all sorts of potential problems. How much space has been allowed for thickness? Additional space to allow for some "non-flat" condition that will likely occur. I'd ask the decorator for a detailed construction drawing and I sure wouldn't guarantee his/her design.
Hafele has some good hardware for such things but mostly designed for moving individual sections (like this project should use). Even as a torsion box this thing will be heavy. What stops it? Smashed fingers?
From contributor J:
I have to thank everyone for their ideas. I have to admit, there is really no way on earth I would ever actually agree to build this. That said, I needed the mental exercise. I hadn't thought about using a torsion box. That's not a bad idea, but as somebody mentioned, it makes for a big piece to bring in the front door. I think I'll use the concept of a "moving wall" (I really like describing it like that) when explaining all of this to everyone else involved.
From contributor X:
Check out Sing Square Log Homes in Washington State. They specialize in oversized pocket doors made of lightweight, stable sandwich core. They use a veneer/foam torsion box core panel. Sing can even use aluminum skin for a contemporary finish. They've worked with DIY customers before, so it looks like you don't have to be a pro. Hope this helps you or the next person.