A Curved Mahogany Bar Top
This discussion of a curved bar top job gets into wood choices, joinery, templating, fabricating, and more. February 13, 2009
Question
I am bidding a bar to be made from 1 1/2" mahogany. It is rather large, at 30' plus, and overall width is around 26", and has a slight curve. I'm looking for suggestions and things to look out for. Material is said to be random length and widths. What is the max width of board to use to prevent cupping? Bar will be about 16" wide overall. Alternate growth rings?
Forum Responses
(Cabinetmaking Forum)
From contributor R:
Is the bar radiused on both the inside and outside? And is the random width/length specified by the designer, or what your supplier told you? First, I would go pick the stock myself at the supplier's yard (can't stress that enough, otherwise you will get the first X feet off the top of the lift). Look for pieces that are closest to quarter sawn (or if you can work it into the budget, use quartersawn) so you should have minimum cupping, although mahogany seems to behave better than some of the other species once it is machined.
At 30 feet, what is the radius you are going to make? Are each of the boards going to be cut to that radius, or are you going to cut the radius after you glue it up? What is the finish going to be? Do you have the ability to do the final coat onsite? If so, you may want to make it in 3 pieces so that you can join it there, making it easier all around.
We did a bar about 2 years ago and some of the pieces of mahogany were 10 inches wide by 1-3/4" thick. Have had no problems with cupping and very little movement. Granted it's not 30 feet long, but it is almost 30" wide and about 12' long. All the panels and stiles/rails are also solid mahogany with ML Campbell's Magnamax lacquer finish.
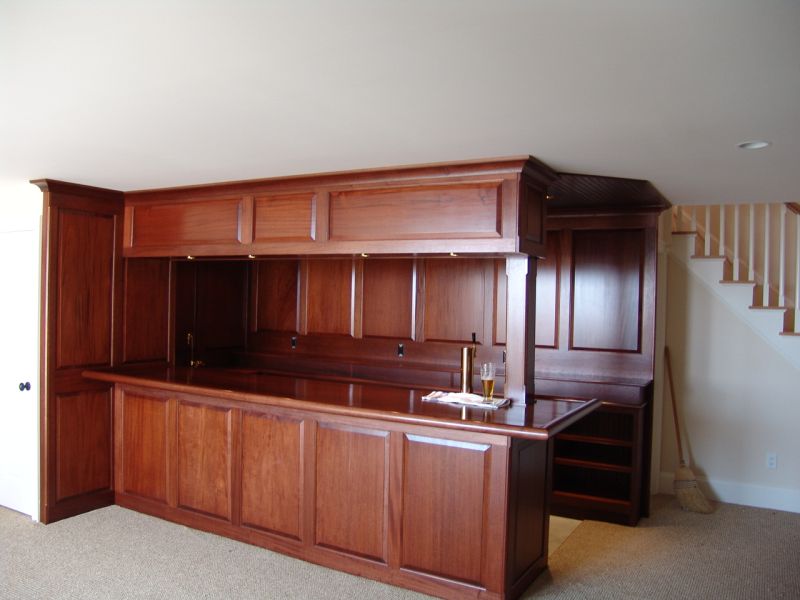
Click here for higher quality, full size image
From the original questioner:
The radius will follow an existing wall. It is just a slight curve, maybe 2-3' from end to end, and have no idea what radius would be. I planned on making a template and making top offsite and assembling in 3 pieces with toggle bolts and biscuits.
Also top will be curved on both sides of bar. I was thinking of laying up planks straight and cutting to radius. Outside edge will just have a radius profile. Material is coming from owner on a truck with the rest of material, as this is just a part of a larger job. He wasn't sure the widths and lengths, but thought they were pretty wide - 8" +.
Wow - 10" wide pieces? Were they quarter sawn? Thanks.
From contributor R:
Okay, if you have a 30' length and a 2' depth, your radius would be 57.25'. If it is a 3' depth, the radius would be 39'. The best look would be to cut each piece to the radius. Only going to be cost effective if you know someone with a CNC machine. If you template the bar and then have someone with a CNC mill the parts, you will only have to glue them up and scribe to the wall. That detail will really make it pop. Also, it would separate your work from some of the others bidding on the job. I would explore that option as an alternative to you milling and mitering each piece to fit the radius and then cutting it yourself.
Even in 3 pieces you will want it all assembled in your shop so that you can cut the radius, flatten it, sand it, etc. With the CNC everything will be numbered and you just do the laminations and final machining on each section. Much easier to handle. The radius will be all done for you.
One thing - don't template on the floor. Set up some horses and template at the height the bar is going to be at. Use a top quality adhesive and a good durable finish on both top and bottom and you should be fine. Also with the CNC it will be easier to have them set it up with staggered joints so that you have no visible seams once it is installed.
The pieces we used on the bar pictured above were not quartersawn. If memory serves me correctly, the entire bar was made from pattern grade South American mahogany with an analine dye and then the Magnamax. After all was done, we gave it a surface finish of Briwax.
This sounds like a really great and challenging job!
From contributor J:
Are you talking about SA mahogany or one of the African mahoganies? In my experience the SA mahogany is a very stable wood, which is probably why it's used so frequently for this purpose. I made up an 11' long top a couple years ago using 8" and 9" pieces and have not had enough movement in any direction that you could notice it.
I haven't used much of the African versions, so not sure how they behave.
As for the radius, I'll offer one other option. Rather than outsource the work, have a shop with a CNC mill up a template for you to the radius required. You can then use that template with a router to put the radius on all your pieces before glue-up. Much cheaper for you than having them mill all the pieces. I agree with contributor R that this would be the best look.
From contributor R:
That is a great idea.
SA mahogany is definitely the best choice. I have worked with the African mahogany and I am not real crazy about it. The last batch I worked with came in all twisty and we had a tough time machining it, as it would tear out on the moulder, etc. Also just didn't have that mahogany feel to it.
From contributor J:
I know what you mean. I did a job earlier this year with Sapele. First and only time I worked with it, so wasn't sure if I just got the cull pile or what. Had to be the worst twisted pile of sticks I've seen yet, and it was all 6 and 8/4 stock.
From contributor R:
I have worked extensively with sapele. It is not the same as African mahogany. I will say that plain sawn sapele can be a challenge to work with because the grain can be quite crazy, but try the ribbon sapele (quartersawn) - it has to be some of the most gorgeous stuff I have worked with, and not as prone to warping and twisting. The grain detail can be stunning with a good lacquer build up and some aniline dye. On the other hand, African mahogany can be one obstinate piece of work to get to stay flat once you have machined it and to not tear out all over the place. It is also very inconsistent in coloring, ranging from almost white to dark orange. At least with SA mahogany you get fairly consistent pickings.
From the original questioner:
The bar is going to sit on top of the wall, so no scribing will be necessary. It is going to be African mahogany, and you guys are scaring me! I hope it isn't too bad to work with. I have access to a CNC and that would be cool, but not sure it's an option. Maybe I should give them two options? What would be the next best way to lay this thing up? Thanks.
From contributor R:
The CNC template would be great and definitely a time saver for you. I would seriously consider going that route. A good template and a good sharp router bit will give you a good jointed edge to glue up to the next radius piece. (Note: you will need a template for each consecutive row, which you can probably get from a couple of sheets of MDF. Can't see it costing you more than a couple of hundred dollars to have the templates made and I think I am guessing high. You will burn that up just laying out the miters.)
I didn't mean to scare you with my experience with the African mahogany. Hopefully your customer is sending you 8/4 stock. I would let it rest in your shop for a few days then skip plane it. Let it rest for another day, then once you have your layout and can plan your cuts, rough cut the pieces to length and flatten one side on the jointer. Again sticker them and let them rest. I know I am sounding elementary, but I think that would be the best way to relieve any stress in the boards and still have something to work with if they walk.
African mahogany seems to be gaining popularity with the distributors because it is inexpensive. If you plan it right and watch the grain when you are machining it you should be fine. Remember, stagger the joints and use dowels to join each section. Stronger than biscuits. Tape off where you don't want the glue to go when you glue up each section so that you can fit them afterwards. Also, I have found it easier to keep the surface flat by only gluing 2 or 3 rows at a time. Half hour in the clamps and you can add another row or 2 and keep going until you get the desired number of laminations.
From contributor A:
I agree with contributor R about the sapele. It behaves exactly the opposite of the other "African" mahoganies. The ribbon stripe actually mills the best. It is absolutely beautiful. I paneled an entire bathroom with the ribbon stripe. The vast majority of the SA has been junk for years. Bad grain, worm holes, poor color, and stupidly expensive.
From contributor J:
Contributor R, would you scarf the butt joints on a top like this, or do you think that's overkill?
Contributor A, in my area there are very few guys that have decent SA mahogany stock since it's been getting harder to find. But the one I use has a direct contact down there and they're still bringing up some very nice stuff. Definitely not cheap though.
From contributor R:
I think scarfing the joints would be overkill. If you have a good, clean and, for lack of a better term, square (since we are talking a radius here) cut, then glue and dowel the butts, it should be fine. One thing you may consider is using "dog bones" to draw the sections together and get the joint tight. If the bar is going to be 1-1/2 thick at final, I would use at least a 1/2 to 5/8 dowel, 2 per lamination.
From the original questioner:
I was planning on mounting a plywood base (probably CNCed with radius) to top of wall and edge banding it black and holding it short so you can't see it. I was also going to screw the top from underneath with oversized holes to allow it to expand/contract. Sound like a good plan? More tips on how to lay this up is appreciated. I am thinking of just having the plywood base CNCed and laying top up straight in 3 sections with the least amount of end grain showing on edge.
From contributor J:
On a straight top I fasten the back of the counter securely, and put the elongated holes at the front. This keeps the back edge in place and any seasonal movement happens at the front unnoticed. I would think this method should be fine for a curved top also.
From contributor R:
The plywood base isn't a bad idea, as it would give you a flat, consistent surface to lay the bar top on while you are assembling it. Just make sure you leave yourself access to get at the dog bones to draw the sections together. You want those joints to look just like all the others. Also, have you considered any type of bracket for support? Will it stand up to someone sitting on it or getting up and dancing on it once it is done? The radius will give it a lot of support that way, but maybe a few brackets spaced around the inside and cut in such a way as to not interfere with the seating.
From the original questioner:
What type of glue works best in this situation?
From contributor R:
Titebond 3 should be fine. I am pretty sure it has an FDA approval for food contact as
Titebond 1 and 2. The benefit is it is waterproof once cured. When you do your layup, make sure you mask off the sections you don't want the glue to adhere to so that you can separate them when you are ready to transport it. Probably wax on the edges and ends. Once you get onsite, you can either leave the joint dry and just draw it together with the threaded connectors, or strip the wax with denatured alcohol and add glue at that time.
From the original questioner:
Project is almost ready. Material is 8/4 African mahogany, roughly 7" wide and 15' long. Any advice on putting this together? I wasn't expecting such large material.
From contributor R:
Did you get your templates to cut the radius out of the stock? You will need to lay it all out. Try to come up with a pattern that is pleasing or, better yet, consistent. Then review what I said earlier. If you dowel each piece together, 1) it will keep them from shifting when you glue them up, allowing you to establish a pattern and build it in sections, and 2) allow you to align the ends when you do your field assembly. Before you plane them, plan your cuts to ensure you will have enough and rough cut to the length of each lamination. That will make them much easier to handle and flatten.