Addressing Cupping in Solid Wood Cabinet Doors
A veneer technique would be better. But is there a way to get wide solid wood doors to stay flat? February 17, 2011
Question
I'm building some mid century furniture. My client insisted on solid glue-up white doors and drawer fronts. I'm having an issue with single doors cupping too much (singles at 28") for wood strong-backs. I am thinking of soaking the cup side of the doors and back clamping them and let dry (swelling the wood). Has anyone tried this to help flatten out a bow? The rip sizes of the glue-up planks are 3 1/2". My door vendor did state no guarantee. I figured that much going into these doors. The door material is white Birch.
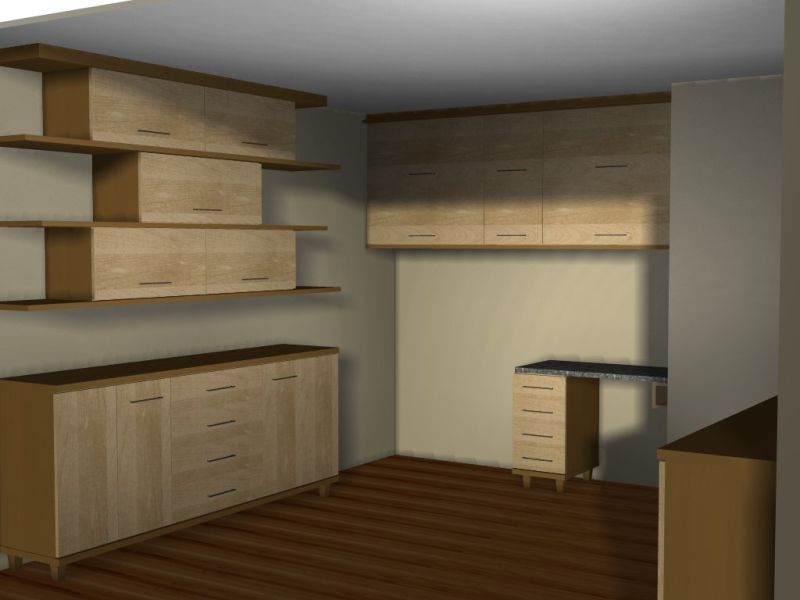
Click here for higher quality, full size image
Forum Responses
(Architectural Woodworking Forum)
From contributor Z:
Heywood Wakefield used solid slab yellow birch doors, with wood strongbacks about 1.25" x .75". I don't think they did any nearly that wide, but I think you could try it. Just make sure you slot those screw holes.
From the original questioner:
I know that I can slice veneers and press. I have one door temp clamped with 3/4 x3/4 metal strong backs and they do hold the doors flat. I was then going to cover them with wood to match the existing strong backs of the other doors (16 1/2 is the max for them). I also sized the rips to be able to split a glue joint and build as a pair. The original was asked to see if someone has tried to back bend a bow, moisten for some grain expansion, and then allowed to dry.
From contributor L:
I've had clients that insisted on solid wood where it was a bad idea. I know it's hard to do but if you can't educate them you have to tell them no. It will almost always come back to bite you. I've noticed that having them sign off on something doesn't work. They still think you should have made it so it does work
From contributor O:
The doors cup as a reaction to different RH from one side to the other, and different from where/when they were made. The notion of adding water to one side (conversely, drying out the other side) is fine on paper, but hard to control or stabilize. The moisture you add (or remove) will eventually move back out (in) of the panels as the reach their equilibrium RH. Some of the strategies to prevent this include: Insure the shop RH is about 30% and the lumber is around 7-8% MC. Pre-finish everything before it leaves your shop. Add battens with slotted screws to the backs before finishing. Insure the doors will still fit the openings as the RH changes by use of the Shrinkulator. Before installation, insure the RH on the job is stable and close to 30%. After install, leave the doors open for 48-72 hours as they acclimate.
One of the hallmarks of what is called Mid-Century furniture are panels of veneered plywood that appear to be solid wood. Therefore, many people unfamiliar with the actual construction of furniture will call something solid when it is not. Also, there is the savvy buyer that thinks by insisting on solid wood he is getting something superior. And considering the ubiquitous iron-on edge band and tattered corners and short life of modern panel work, he may be on to something.
Wood Shrinkage Calculator
From contributor T:
You can try to wet the one side (a damp towel if you have a finish on it) and slowly over time add pressure to the clamps. You will need to over bend, not just flat. You are expanding one face and compressing the other. Then once over bent let it dry. Although this may work I am doubtful as a lasting fix. If that does not work you could cut those doors apart and glue them back together alternating the grain. You may need to get creative to make up the size.
28'' is way too wide for a slab door, unless you design and build a way to keep them flat. Starting with the M/C, it needs to match the client’s home exactly. I have thought about adding steel to a groove cut into the end grain. My mentor said he had drilled and hammered steel rods through. Maybe a brass or s/s U-channel top and bottom would work? Quarter sawn wood would help also.
From the original questioner:
Done deal, I split the doors in the middle down the glue line, strong backed, fit, and detailed for finish. I did do a dry fit with U channel to the 28" doors and they held flat. I was going to rabbit it in 1/4" then slot the wood strong backs, to cap the metal. The client had no problem going to a pair, so I'll go the safe route.
From contributor V:
So how do you keep the doors from curving? How much force will be needed to hold the doors straight? There is no easy answer, but here is what I would do. Do nothing to the original doors, work on a panel you can mess up and experiment with. Use the same wood under the same conditions to make this panel. Allow it to cup. This curve will either have the concave side out or the convex side out. You are going to have to place the panel onto a flat surface back side up and make one or two sticks which are dimensioned so that when correctly placed between the panel and the flat surface the panel touches the flat surface and the dimensioned stick(s) hold the panel slightly curved in the opposite direction to the original curve when clamped to the flat surface. Thus this panel is clamped to the flat surface and is now slightly bent past flat in the wrong direction.
Take a router with a dovetail bit in it and rout into the panel half the thickness of the panel. If the panel is 3/4 inch think I would rout 3/8 inch into the panel. I would make the slot at least 1 1/2 inch wide. For the strong back I would make it thicker than the depth of the slot perhaps 3/4 inch thick and 1 1/2 in wide to fit and slide in the dovetail track in the panel. This strong back should be stout enough to hold the panel flat or bent in the wrong direction slightly after the clamps are removed. Make the strong back to fit into this slot and allow it to slide with some force but do not hammer it in. Do not glue it in! Now when two strong backs are placed into the door I would say about 3 -4 inches from the ends of the panel, making sure not to be near the hinges, so they work without interruption. Unclamp the panel from the flat surface and allow it to do whatever it will.
Now after some time is the door flat? If it is not and the strong backs are doing too much, make the strong backs thinner. If they are not doing enough, put another strong back into the center of the panel making sure to re-stress it by clamping it back to the flat surface as was first done. If the panel is still not flat I would put two more in the back of the panel and center them between the others. When you find the sweet point you have a solution. I would screw the strong back to the panel with one screw placed near the hinged side of the door or the top of the drawer front. Now this strong back is going to look nice after you are done but as the project ages the strong back and the panel are going to grow and shrink, so if there is a problem with things not being flush on the far side of the panel this is to be expected.
From the original questioner:
Here are a couple of the pieces. I’m letting the finish off-gas, then its delivery time.
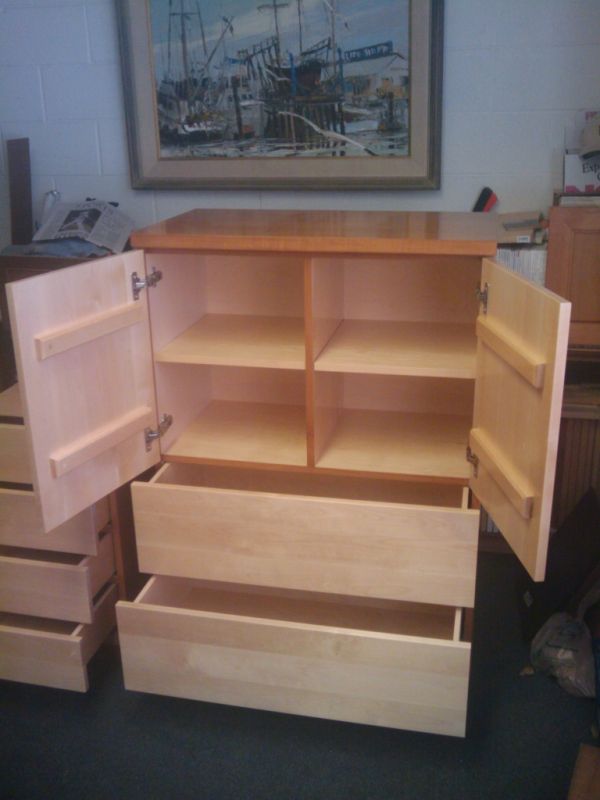
Click here for higher quality, full size image
From contributor V:
Looks good. I cannot tell if you glued or screwed these strong backs onto the panel. If screws are used they need to be in a slot so when the panel expands and contracts the strong back held by the screws do not allow for the boards in the panel to separate. If you have a shop that is about the same humidity as the place they are going to live then you may be alright.