Advantages of Pocket Screw Construction
Fans of pocket screws explain why they like to use them for assembling face frame cabinets. April 26, 2006
Question
After reading the obvious scorn for pocket screw construction of one poster, I would like to hear about your methods of face frame construction and methods of attaching to the case. Do you feel pocket screws are inferior?
Forum Responses
(Cabinetmaking Forum)
From contributor D:
1 vote for pocket screws.
From contributor J:
That's two votes of pocket screws. I've used M&T, biscuits, dowels and pocket screws for face frames. Now I use only pocket screws. For me and my shop setup and equipment availability, it's the most practical way to go, primarily because it eliminates clamping. I also use them to attach the frames to the boxes, even though I dado/glue the boxes to the frames. As a matter of fact, I use them everywhere I can. I like the mechanical joint.
From the original questioner:
Do you (or anyone else that would like to respond) plug the pocket holes? Or do you leave them open?
From contributor B:
I prefer the 1 1/4" hi/lo thread sq. drive with washer head so I can use the same screws for attaching face frame to carcass, setting p/lam tops and installing drawer fronts.
From contributor K:
I would suggest pocket screws, too. I pocket screw the rails to the stiles and then pocket screw the frame to the carcass from any area that isn't going to be visible. For the areas such as center partitions, I will glue and clamp. (The entire frame is glued to the carcass and screwed, but only glued when screws cannot be used.) I'm sure that biscuits are just Jim Dandy, but after I screw my frame to the cabinet, I can sand it and be done with it, whereas I would have to wait until the glue is dry if I used biscuits. Obviously though, you can't use pocket screws for everything, although some people believe a plug looks okay.
From contributor A:
Who would scorn pocket screw face frames? Furniture deserves better, but regular casework? Using pocket screws is by far the fastest method of FF construction. Strength-wise, it's a tossup. I can't imagine switching back to m/t, biscuits, or dowels. As far as plugging the holes, who is going to see them anyway? There are industry standards as to what you can do where (from a visibility standpoint). Basically, if you have to literally lie on your back and stick your head into the cabinet, then it doesn't matter. One place to be aware is on the lower rail of uppers.
From contributor V:
Definitely pocket screws. (That is glue and pocket screws). Nope, don't plug the holes either.
From contributor S:
I think that the scorn was directed at using pocket screws to assemble the cabinet box, which I still think is sound, solid construction. My theory is that if the cabinet can make it through the delivery and installation process, it's as strong as it will ever need to be.
From contributor Z:
I've only used plugs one time and I didn't like them. They're aggravating to install and take forever to sand flat. This was also a situation where I used pocket screws that I shouldn't have. It was for the inside dividers of a paint grade wall curio cabinet. I was covering holes where I attached inside dividers. In hindsight, I should have done what's mentioned above - dadoed, glued and clamped the dividers. The screws held fine but looked marginal and took up way too much time.
As for face frames and box construction, generally, pocket screws work best for me. I don't see any need for the plugs with those. Above is a good point about the washer heads; they work well for just about everything.
From contributor O:
I guess I'm the 50th vote for pocket screws. Fast and simple. I also used to connect face frames to boxes and don't plug. I will always put in an inconspicuous area if possible and have been looking for a better method to connect ff to box, but haven't found it yet. I think of it this way - if you have 15 holes in the sides for adjustable shelves, and the ones that don't get used don't get filled, then what's one or two more holes, properly spaced between the shelf holes? When cabs are filled, no one sees them anyway. And on lowers you can get the top one or two where the drawer is and the rest where the slideouts are. Just my rationalization.
From contributor M:
Well, I'm going to jump in here and get my head chopped off. I prefer dowels. I have a horizontal boring machine to do the drilling and I find it fast and accurate. I'm not slamming you guys that use pocket screws, but the doweled frame is much stronger. I will admit that it's overkill for a kitchen cabinet, but when I show it to my customers, they love it and it has helped me sell a lot of jobs where I've been able to beat others out because of my "better " construction. The place that a doweled FF really paid off for me was the time I was delivering a large liquor storage cabinet to a bar and the guy on the other end of it dropped his end on the ground when he lost his grip and the whole thing held together. That doweled frame and having it glued to the cabinet saved me. The big plus of the pocket screw system is that it doesn't require the investment in an expensive machine to do the horizontal boring needed for dowels. I add these comments just for a different perspective, not to criticize.
From the original questioner:
Thanks to everyone for the input. I use pocket screws also and seems that I follow about the same as everyone else. I dado my boxes and glue and pocket screw. Is that overkill? What type glue are you using on your face frames?
From contributor P:
Well, I agree that dowels are a good method, but one problem they've always had is they're prone to weakening over time due to expansion and contraction. Granted, depending on assembly and glue used and surface coverage, this can take a short or long time, but is nevertheless inevitable. Don't forget, with dowels, you eventually take the clamp off after glue-up, but with pocket screws the clamp remains in place after glue-up.
But if you glue and pocket screw your face frame together, dado and then glue the frame to your box with pocket screws, how exactly is it going to come apart?! The answer is, it's not... So then, from a business perspective, the justification becomes speed of process (product out the door), and labor savings (money in your pocket), which greatly outweigh any perceived advantage of doweling, in my opinion.
Besides, if you really want to test the strength of a dowel vs. a metal fastener in a piece of wood, try installing the cabinet with a dowel setup. Now of course you wouldn't do this as it's impractical. But even if it was feasible, it would not hold up against a screw, nor would it be efficient, which is the point/benefit of using pocket screws in the first place. Here's how we use pocket screws.
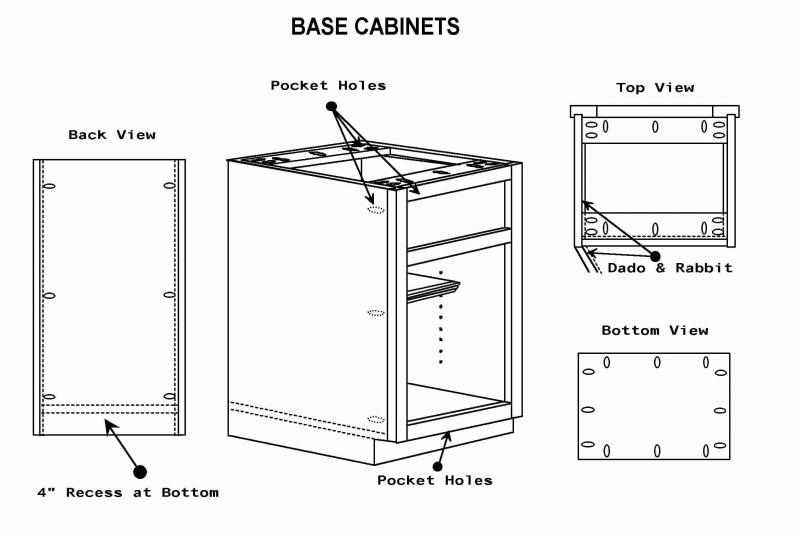
Click here for full size image
From contributor M:
I understand what you're saying, but disagree on a couple of points. First of all, the expansion and contraction really is a non issue. The amount of movement over the distances we're talking about is quite small. We are dealing with KD lumber that's going inside a house. Furthermore, the same movement is happening with the pocket screws, at least as it pertains to the FF. As for strength, I have no doubt that if you were to take 2 pieces of wood, one being doweled and the other pocket screwed into an L and tried to break them apart, the pocket screw would fail first. I go back to a point I made in my last post - yes, it may be overkill for kitchen cabinets, but as I said, I use it as a sales tool also. I totally agree when you pocket screw your frame to the cabinet, you have a bombproof structure.
From contributor K:
I agree with dowels being stronger, but let's think about how much stress a frame is actually going to take. It's not like you are going to be standing on it all day every day and, in fact, because it is glued to the case, I don't think it has any more stress on it than a door does. I think both methods will outlast all of us but one method will make us more profit in the end.
From contributor T:
I also use pocket screws, but one point has been made that I am confused about. KAP says that he uses pocket screws and dado on his boxes. I use pocket holes on all joints except the stiles, which are 3/8 x 3/8 dado. If I were to add pocket screws to the dado joint it seems to me that the screw would not be holding much as there is only 3/8 inch thickness left in the rail for the screw to grab. When you look at a Type 17 auger point, that does not leave much thread grabbing power. Am I missing something here?
From contributor V:
If you dado the back of the face frame to be received by the cabinet sides, you only dado it 1/4". Just enough to true up the box and for it to nest into the slot. Run some glue in the dado and use 1 1/4" screws. It will give you approximately a 7/16" bite onto the face frame, which basically holds the face frame in place till the glue dries. If you want to dado your decks into the cab sides, you would do the same thing as well.
From contributor N:
Pocket screws with a little different slant. I use pocket screws for the face frames and also to attach the FF to the box. However, I don't use any glue. The FF is dadoed 1/8 inch, enough to keep everything aligned and still leave lots of stock for the screws. I use 3/4 inch stock for my boxes and insert 3 to 4 screws in each side plus a screw every 8 to 10 inches in the deck and top. My feeling is that on a drawer bank, how much stress is on the FF? Even if the cabinet has doors, how much weight is that? If 14 to 28 hardened screws into hardwood will not hold a box together or support the weight of 12 to 14 sq ft of doors, I would be surprised.
I just finished a job that was an hour drive from my shop and had a cabinet get damaged while waiting to be installed. The FF was unscrewed, brought to the shop, repaired and screwed back on. A lot more time would have been needed if it had been glued to the box.
In no way am I saying this is the best method, heck, I'm not even saying it is a good way of doing it, it is just the way I happen to do it. So far there has not been a failure. If one fails, then I will go back to adding the glue, like I use to do.
Thanks to all for sharing your methods and ideas. I really enjoy reading this forum.
From contributor T:
Thanks for the response. Sometimes I get stuck in the "I have always done it this way" grind. Working by myself I have no one, other than those here, to show me a different way. In 3/4 ply I have always used 3/8 x 3/8 dado in ff and 3/8 rabbet in sides. Glue, clamp and wait for dry. Now thanks to you all on this site I can glue and screw without having to clamp and wait for the glue to dry. This means I now have to work more. No down time waiting for glue to dry.
From contributor G:
I use pocket screws to assemble my FF, and use dados and cleats for frame attachment, for obvious reasons.
The comments below were added after this Forum discussion was archived as a Knowledge Base article (add your comment).
Comment from contributor E:
How about another slant on cabinet construction? We used to dowel our frames and glue and nail them to the boxes. Now we just glue and pocket screw the frames together then glue and clamp the frames to the boxes. The tops and bottoms of carcasses are dadoed 1/8" deep for alignment and glued. I know this takes more time waiting for the glue to dry, but with enough clamps, by the time all the clamps are used up, the first frame is ready to unclamp. And no nail holes to deal with. Actually, the glue people claim that 1/2 hour is all that's needed for clamp time, but we give them at least an hour. We use 1/2" ply for our boxes also. We have done some testing on our own, and if you tear one of these apart, the wood fails, not the glue. The glue is very strong, more than I think most people give it credit for.
Comment from contributor F:
CSH 800 882-0009 has developed #7 Washer head pocket screws with Hi/Low thread with sharp type 17 points to avoid splitting. #8 Washer head screws have also been developed - 1/2" - 3" long, for softer woods.