Baby Steps toward More Efficient Sanding
A small shop owner considers stepping up to a drum sander or stroke sander, or just investing in more compressor capacity and some pneumatic hand sanders. October 27, 2011
Question
I'm in need of a faster method of sanding. I currently use a 5" PC ROS sander. I'm happy with the results, but the time this thing devours has become unacceptable. The solution would be used mostly for custom furniture, with the occasional cabinet type job.
My business is still young, so my budget is pretty modest. I'd like to get in and out of this problem for somewhere around $600, but could go up to the $1000 area if necessary and if I delayed the purchase for a little while. My options as I see them:
1) A Festool 6" ROS (or other high quality brand), maybe with a new dust extractor as well. Perhaps the Rotex?
2) An entry-level drum sander, such as a 10" or 12" Grizzly or Jet. Not the end-all-be-all by any means, but would make quick work of removing milling marks.
3) A larger air compressor so I can run a DA (I already have a couple 6" Ingersoll Rand 300G sanders lying around). I'm thinking an IR SS3L3 (3hp/60gal/~11CFM@90psi) if I can get away with it or an SS5L5 (5hp/60gal/~18CFM@90psi) or used 5HP Speedaire if not. I wouldn't mind some more air for my HVLP gun, too.
Back when you were getting started, what was your first baby step towards more efficient sanding?
Forum Responses
(Business and Management Forum)
From contributor C:
I am still getting started, but worked in a well-equipped shop for quite a while. I would say your first step is getting a decent sized air compressor. The reason is it will benefit more than just your sanding process.
Automated sanding requires good dust collection, so you may need to upgrade in that area before any improvements in the sanding process.
From contributor M:
Get yourself the best compressor you can afford so you don't have to buy another one next year as you grow.
Last year I spent a lot of cash on Festool (money wasted). Now I just bought a big compressor and a new Dynabrade. There is no comparison - a Dynabrade is a lot faster than Festool. It's also 100 times more comfortable to operate.
From contributor K:
Stroke sander at auction. If you have not used one, you will not believe what it can do. My Oliver is the last tool I'll ever part with.
From contributor L:
I have to second the stroke sander. I bought an old one at auction that I set up to do 4x8 panels and lots of other stuff. Much faster than a RO. I paid $200 and there is that much iron in it. Runs like a champ. Takes good dust collection.
As for compressors, don't go by HP. There are a lot of cheater 5hp ones out there. Go by standard CFM. Your air tools will last a lot longer if you also have a real air drier, not just a filter and trap. A cheater 5hp won't even keep up with a Dynabrade and you will kill the cheap made compressor if you run it steady. A decent compressor will put out just short of 4cfm/hp @ 90psi. Tank size really only counts if you run a major air consumer in short bursts. Won't help much at all for continuous running something, i.e. RO sander.
From contributor C:
Stroke sanders are great, but just pointing out the dust collection again. So that has to be figured into the cost if you don't already have sufficient dust collection.
Sometimes I would forget to open the blast gate and in about 30 seconds the 800 sq ft corner where the stroke sander was would be full of dust. We had a 20hp bag house. Not sure what minimum size is, although horse power isn't the only thing to look at.
From the original questioner:
Only on WOODWEB can you get so many informative responses in so little time - thanks! I figured a stroke sander would be out of budget, though it appears that might not be the case. I've got a cyclone dust collector with a 7" inlet, so I think I have enough dust collection for most of the options within my budget.
I have never used a stroke sander, but my concern is that it is seems to be limited as far as stock length is concerned? I have a 7' long table top to sand next month, and I would love to use my new tool to do it, whatever it may be. Otherwise, it seems like a great option.
It's good to hear feedback regarding premium electric sanders vs air sanders. On paper, air sanders seem to require a good 16 CFM at least. Is it so in practice? What's a real-world minimum air requirement for a good quality palm-sized DA (say a Dynabrade for example)?
I make one-off custom furniture using a variety of materials, so nothing's ever the same. Next week I start on a single-casting concrete executive's desk (the gloss finish will be sanded a la lacquer), a few weeks later a 7' walnut dining table and bench. After that, an oak buffet. I know I've got to bow to the reality of disparate materials, but versatility is important on some level. Maybe that points towards air?
The things I like about a cheap drum sander is that they're not limited by length and they're automated in that you stick stock in one end and take it out the other. Do they have any other redeeming qualities?
You guys are awesome - thanks for the feedback.
From contributor C:
It all depends on how much floor space you want to give up. The shop I worked at had a giant one with a ten foot table. I've seen big beasts like this go for about $50 at auction because they are a pain to move and not many shops want to give up the room.
I used it mostly to flatten panels/doors and sand down butcher blocks. You still have to finish with a random orbit or jitterbug in many cases, so I still vote to upgrade the compressor and get a pneumatic sander first.
Oh, and sanders do use a lot of CFM, but I don't remember the exact number. I'm pretty sure you need a two stage pump to avoid burning out the motor.
From contributor I:
Back when we did a lot of sanding, we had two people sanding 8 hours per day. We were milling our own components and had several different profiles that required a lot of hands on sanding. At that point we were a small shop with a tight budget. The most significant upgrade we made during the early years was going to an 80 gallon 2 stage compressor and purchasing 2 Dynabrade sanders. I would suggest you get at least 1 sander and definitely get the compressor. Next was getting a drum sander for the flat surfaces. These purchases seem large now, but the $1400.00 compressor lasted 15 years and the sanders probably 10 years average. I rebuilt one of them and still use it everyday, so it has lasted about 12 or 13 years. When considering the life and time savings of these tools, it works out pretty cheap.
From contributor M:
I don't think a drum sander is the answer for you, and here is why. The ones in your budget are junk! They are very slow and don't do a good job. I have been down that road - you're better off going without until you can justify a wide belt.
You need a good orbital and you will definitely need a decent compressor at some point. Spend your money on a true 5 hp 80 gallon 2 stage. If you can't afford both the compressor and sander, you should start with the compressor and it probably won't take long to save for the Dynabrade.
From contributor L:
Dynabrade's web site lists air consumption as 3 to 18 cfm. The reality is you will almost always run it wide open = 18cfm. Good compressor puts out almost 4cfm/hp! Simple math, but expensive to run - speed costs! I've been around enough of the cheap drum sanders to decide they are a waste of money. Others will disagree. The old style stroke sanders have independent pedestals and support tables so you can set the pedestals any distance apart you want, bolted to the floor. I've seen them setup to take 16' long pews. Ours runs a 6" x 338" 150 grit belt producing a ready to finish surface, no further sanding required. It takes some time to get to the point you can master them, but they are fast for the money. I'd personally like to have an electronic platen 53" wide belt but at over $80K, not today! Like others have said, get good dust collection - you can't buy new lungs.
From contributor D:
If you're a one man shop building high quality, solid wood furniture, for $350.00 you can get a Lie Nielsen smooth plane that will give a smoother surface than any sander. If it's set up and sharpened right, it's fast, quiet, dust free, and doesn't take up much space. It doesn't use electricity and it'll outlive you.
From contributor U:
I am a one man shop, and was in your shoes a few years ago. I went from a 5" random orbit to a 6"
Festool, both the right angle, and the standard RO, and I really like both of them a lot.
I tried the air sanders, but the one I tried didn't have good dust collection like the Festool, and when you figure cost of air tools, you really have to figure the cost of maintaining the compressor and drying the air. I ended up getting a Powermatic open end wide belt a couple of years ago, and that helps a lot, but I still really like my Festool sanders for day to day use.
For your current budget and needs, I don't see how you could go wrong with the 6" sander and vac setup. The Bosch is pretty nice as well, if you don't want to spring for a Festool.
From contributor W:
I was very apprehensive about buying a drum sander because of all the negative reviews. But I purchased a 24" 2 stage single speed Grizzly and added Velcro. I love it! I took my time to set up right. It can sand rough lumber from my
Wood-Mizer in about 4-5 passes (per side). Had to do this on some walnut forks that were too wide to fit through 15" planer. I run most everything through it.
Lines from planer are not a problem anymore. Quick palm sanding is all that's left. Does require 2 4" dust ports. If you forget to open gates, it will remind you.
From contributor C:
This is as much a question as it is a statement. I am confused by the comments that throw compressor maintenance into the costs of getting pneumatic sanders.
Don't you need to get a nice 2 stage compressor eventually regardless of if you use pneumatic sanders? There are so many other operations that can be done with pneumatic tools, so once you divide the maintenance costs into all the different operations it is actually much more cost effective to go pneumatic, especially when you figure in the long life-cycle and cheap rebuild costs of pneumatic tools. That's what I've been told anyway. But my uncle is an industrial compressor salesman and my Dad used to be part-owner in a custom compressor business, so I may be working from a biased information source.
Anyway, my thinking is that the original poster would see benefits beyond the sanding operation if he bought a nice compressor. Am I missing something?
From contributor L:
I'm not at all sure you need a 2 stage compressor. Compressing air much past where you will use it costs a lot of energy. The advantage of a 2 stage is having a cushion to offset the small output capability of most small shop compressors. Going to a large tank can provide some of the same but if it once bleeds off it takes a long time to recover. Same is of course true of a 2 stage to reach shut off level. Big shops with more constant demand usually go to screws, some without even having a tank. To run economically, a screw needs to have controls that reduce energy by unloaders, shut downs during longer idle times, or electronically controlling the speed. Compressed air is expensive; buying too little will prove frustrating, and too much a waste of money.
From contributor C:
I still don't see why compressed air is expensive. I use my dad's 5 horse 80 gallon two stage compressor and the amount of power it uses is barely noticeable. It will run a lot of high cfm tools like buffers, cut-off tools, sanders, etc., although you need to be a little careful and pay attention to how much the compressor is running.
I guess since I grew up using a lot of pneumatic tools, I think of a decent compressor as a necessity. My uncle even sells compressors and pneumatic tools to the Amish because it is more efficient to run a compressor off a generator then run the tools off the compressor than it is to run the tools off the generator.
Not saying you are wrong, just trying to understand as I am interested in understanding my energy costs. And I am referring to a standard 5 hp two stage compressor.
From contributor Q:
Look at the new DC motor sanders... as fast as a DA without a compressor.
From contributor P:
Compressors are expensive to run because of their efficiency, typically 60% or less.
From contributor M:
I don't think contributor L means that a 5 hp compressor is expensive. What is expensive is getting proper air, which most don't do - it would mean a quality compressor, line dryer, proper filters and lines, etc. The compressor alone is really the cheap part. When you get into large screw compressors, as contributor L mentioned, there is a big price tag and they do take a lot of electricity.
From contributor P:
In a previous life, we ran a 25HP Hydrovane constant volume compressor with a chiller, a dryer and several hundred feet of 2" piping. Water traps and drains everywhere. Lots of clean dry air. On the other hand, the cost of a 25HP motor running constantly isn't cheap.
From contributor C:
As far as sanding goes, I just read up on the newer DC sanders and it looks like they are getting to be more wear-resistant (significantly less wear components) which I guess for me is the main issue. 5+ years ago, it seemed like pneumatic sanders lasted 2-3 times longer than the Bosch random orbits. Some sanders are also claiming to have similar torque to a pneumatic. So my experience seems to be outdated.
As far as dry air is concerned, is it really necessary to have an air dryer if you are not spraying? I just have a couple of drains and filters and my tool life seems to be reasonable.
From contributor X:
Think about it this way - go open up an electric RO palm sander and take the motor out and hold it up to the 5hp motor on the compressor (needed to run one sander). Now multiply that by the number or sanders used... Big difference. If you want to run an air grinder off household 110 circuit, you don't have enough power to run a big enough compressor, yet you can run 3-4 electric grinders of the same circuit.
To the original questioner: One thing that has cut down on my sanding time has been a spiral cutter head on my planer. It's actually faster just to RO sand straight out the planer than to RO sand the marks from the drum sander. I used to run all my lumber though the sander after planing but I now skip that step and use the drum sander half as much. You can get a decent sized used drum sander for your budget, but a minimum 5hp compressor and air sander, drill, screwdriver are more important for most people. I've had good luck with cheap air tools - even Harbor Freight. Since your budget is tight, it's a great way to get what you need now and replace as you need later.
From contributor M:
Here is what I am using, and I feel it is the best for a small/medium shop. The only thing I don't like is that I have to turn on the vac manually instead of it coming on automatically with the
Festool sanders.
The Dynabrade does an awesome job and is faster than the Festool. I am happy with the dust collection. It's not quite as good as the Festool's, but still very good.
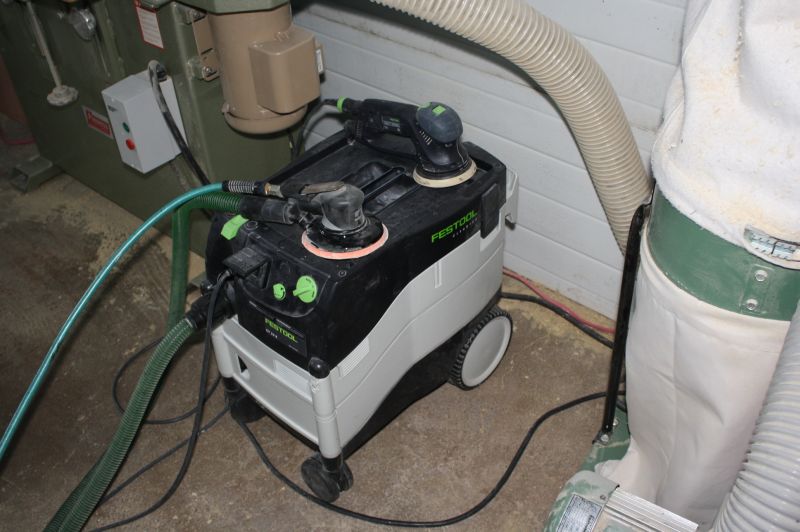
Click here for higher quality, full size image