Boring Long Holes
Suggestions for how to make long holes in wood pieces, as for the wiring chase in a wooden floor lamp. July 28, 2006
Question
I'm looking for guidance on how to end profile and through bore blanks. The first piece is 10/4, 17" long and I need to get a straight 3/4" diameter hole through it. The second piece is more complicated, with a larger bore, 1 1/8", but shorter at 8", with steps to a smaller through bore at 7/8", and a taper with shoulders to accept a cap on the ends. Any suggestions where to start? We could stand them up and use the CNC, but holding them rigidly enough is going to be difficult, and we can't get the clearance overhead with the tooling in place. I'm sure there's a machine to do this, I just can't think of it or find one.
Forum Responses
(Solid Wood Machining Forum)
From contributor L:
I know this isn't what you want, but could you use 1/2 pieces and CNC a half circle (corebox bit) and then glue it up? If your machinery can handle the 17" height, then why don't you just build a pyramid out of 3/4 ply with a space for the blank? Should be sturdy enough to keep it steady.
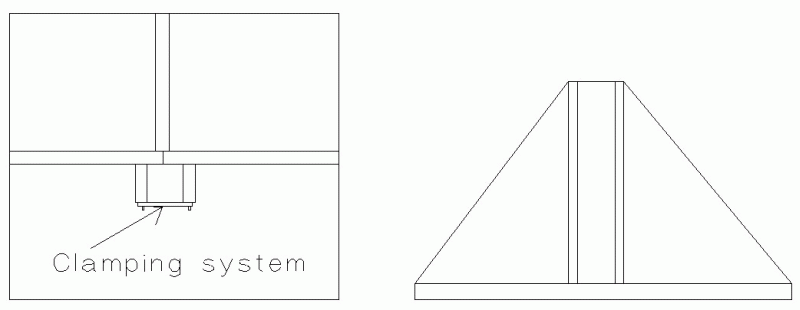
Click here for full size image
From contributor P:
I would use a lathe with a fourjaw chuck and a drill with a morse taper to fit your tailstock, which can be found at any tooling company. This method seems to me the most efficient way. Basically, it's a "gundrill," which is used as well for boring lamps and light posts for electrical work.
From contributor C:
In my shop, I would use the "two halves with a groove down the middle" technique. The groove needn't be full size. A drill will follow a smaller square hole right through the blank to give the final hole dimension. Routing the groove with a roundnose bit is an elegant solution, though.
From contributor A:
I'm thinking along the same path as contributor P. Drilling things on a lathe is common in the machine shops, but seemingly unknown in most woodshops. I'm thinking you could bore the 17" from both ends. You are going to need a machinist lathe. It might be easier to sub this to a machine shop.