Building Your Own Bandsaw Mill
Other Versions
Spanish
French
Thoughts on the practicality of building your own bandmill, from those who have done it (or chosen not to). April 11, 2008
Question
I know this has probably been asked and answered but I'm thinking of building a bandsaw. I'll most likely build the Bill Rake style. I'm not worried about building it. I'm concerned about how well they work. Does anyone use one like this?
Forum Responses
(Sawing and Drying Forum)
From contributor H:
My son and I built a bandsaw based on Bill Rake's plans about a year and a half ago. My son is a welder and metal fabricator, so he did most of the building. We did make some modifications to the plans though. It's a big job and is a lot of work to get everything accurate.
We started out with bearings to track the blade, but did end up getting regular pre-made roller guides from Cooks Saw. We also used a hand crank winch to move the carriage into the log and have a 12 volt winch to raise and lower the head. It does a good job of cutting, but as I stated before, it's a big job to build. If you don't do much welding or fabrication, I wouldn't recommend building a mill. We started out with a 10 horse Briggs engine and later switched to a 13 horse Honda electric start.
From contributor H:
Here's a picture of the mill shortly after being finished. I don't have any current pictures with the head lift winch on it. I will post a more close-up picture of the head next. These pictures also show the Briggs 10 horse motor which has since been changed to a 13 horse.
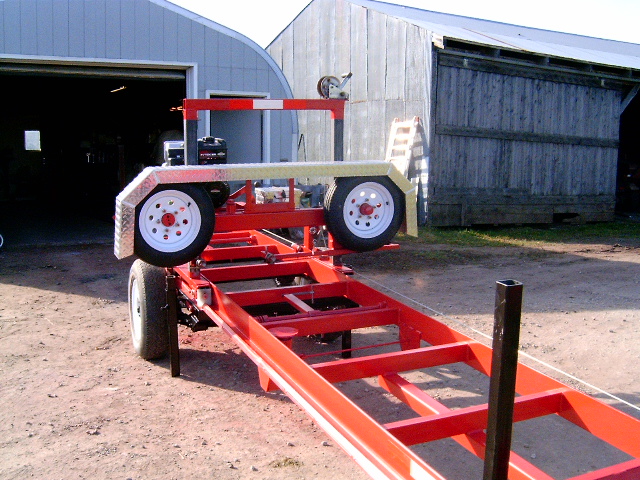
Click here for full size image
From contributor H:
Here's another picture with a close-up of the head assembly.
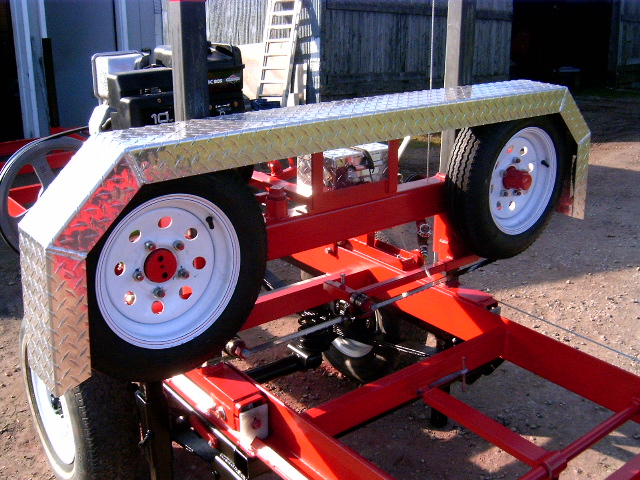
Click here for full size image
From contributor A:
I made my mill using Bill Rake's pictures on the internet. I did some of my own modifications to the design like to the roller guides, wheels, and acme rod to move the head up and down. If you take your time and make use of a machine shop were needed your saw will cut accurate. I also used 16 hp and would not go smaller.
From contributor R:
I was thinking at one time of building my own mill until I came across a Turner mill. I ended up purchasing one from Bill Turner.
From contributor L:
As a owner of a Turner mill I think you were right on using tires instead of metal wheels. To be honest I prefer standing behind a full metal shield when cutting. I would urge anyone thinking of building a mill to remember Murphy's law and build to make a mill as safe as possible.
From contributor T:
I built my mill, looking at pictures of mills on the internet. My plan was to push the saw through the log. I installed hydraulics to raise and lower saw and also move it through the log. It sounds like you know how to build one, go ahead and add the helping hydraulics. Mine cuts just as straight as any others. I have 18 hp which isn't the fastest, but gives me enough time to remove boards as they are cut. Always think about safety.
Hydraulics
From contributor R:
For me I don't know how to weld. Then I figured out the cost of the steel and bought a welder so I figured it would be cheaper to buy a mill from Bill Turner. I used it to build a house with and when I sold the house I sold the new owners the mill.
If I ever get back into milling again I will buy a hydraulic one from Bill. I was going to keep the one I bought from him and just upgrade since they are the same and all you have to do is add too it if you want.
I guess if you can get the steel for free and want to do it for the learning experience then that’s a different matter altogether.
I bought mine without the motor and I put on a 10hp 1phase electric motor and I had all the power I needed. It was next to impossible to bog the motor down even when using 1 1/2'' blades. It’s best to use the 1 1/4'' though because they work just as well or better than the 1 1/2''.
From contributor D:
I built a mill using some of Rake's ideas. Mine is a 4 post mill using Acme threaded rod to raise and lower the head. Power is from an industrial 5 HP electric motor. I used 9" Ford axles from a junkyard to mount the wheels. The frame is 4x4 angle iron. The wheels are roller bearings. Blade guides are roller bearings as well. I use a gravity feed drip system for lubrication.
When built, I had about $800 in it. You could probably double that now due to steel cost. It saws very well. I have sawn as much as 800 bd ft of 8/4 yellow poplar in a day by myself. My max log size is about 22" with a max length of 24'. I can work by myself up to about 18" material. Bigger than that and I have to have help to turn the log. I enjoyed putting it together. Here’s an image below.
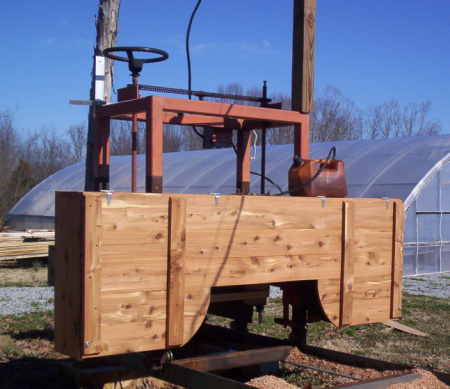
Click here for full size image