Building a bandmill from scratch
Other Versions
Spanish
Advice and examples concerning home-built mills. (From WOODWEB's Sawing and Drying Forum) January 21, 2003
Question
Has anyone made a band mill from scratch, using car wheels and axles to drive the blade?
Forum Responses
(Sawing and Drying Forum)
There was a recent Mother Earth News Magazine with many articles about sawmills in general. In there was a short article about a guy who homebuilt a band sawmill for $700 using tires and the like. The issue has a mule/donkey on the front. December/January 2002/3 issue.
Mine is nearly finished. I used parts from a boat trailer axle. I built a Mizer type.
I built one based on a design by Bill Rake. Having said that, I am not sure I would do it again. I had fun building it but I think a commercial mill might be more practical.
Unless you have the skills and equipment and know something about sawmills, all you are going to have is lot of headaches. The money you spend on home-built equipment can not generally be recouped. People are afraid to buy it because it may have design errors and poor workmanship.
I would suggest you buy used and repair and rebuild it for wear. Factory built equipment generally has the bugs worked out.
If you have the time and money and like this kind of work, a sawmill can be built at home, but don't expect to save money over buying. I have seen people make sawmills using plywood for wheels, but myself, I like better quality than this.
I'm not sure I'd agree with you. As I have posted here before, my brother built one with mostly scrap and is still using it today. He had no milling experience before building it, and has made hardly any changes to it since doing so.
I am working on the hydraulics on my unit now - the hydraulic log stops, hydraulic log clamps, and the two hydraulic log levelers with 26" long 4" diameter roller, and the hydraulics for the raising and lowering of the carriage are completed. I am starting to work on the hydraulic log turner, the hydraulic log loader, and the hydraulic carriage feed now. Currently I have about $2500 dollars tied up in it that includes new rams, pump, and hydraulic motors. It's powered by a 30HP 4 cylinder Wisconsin. I am ordering the hydraulic spool valve unit this week. Should have around $6000 tied up in it all together. Not bad for a fully hydraulic sawmill. Had a couple offers already from people for quite a bit more money than what I have in it. Nothing is impossible. Everyone had to start from somewhere to get where they are today.
I built all of my own sawmill equipment. My first sawmill started out as an 18" meat saw.
A little common sense can go a long way. It helps to have a wirewelder, lathe and milling machine lying around.
I was wondering why a fella couldn't build a shop band saw (18-19") similar to this? I can get spare tire donuts from cars for free - all you would need is spindles and a pulley to fit the azle on one, and build an upright frame?
I would think that building one's own sawmill would be as satisfying as building a house with one's own wood. I went as far as to design my entire mill, different from any I have ever seen, before deciding that I would never be sawing lumber with it. I know myself! I opted to buy a used mill, but I'll always believe that my mill would have been the best ever built. I say if you have the drive and the vision, go for it.
To an extent I agree that it would be hard for most to build a satisfactory mill. However, for some it might not be a choice. It might boil down to build a mill or do without a mill. If this is the case, take the time to do it right and not slop it together. And look for mills you can inspect and follow the designs of a proven product. If you're experienced with welding and fabricating, you shouldn't find it to be much of a challenge.
From contributor R:
I finished mine last spring. It is based on the Bill Rake design. While I was faithful to the design to avoid any unforeseen problems, I did stray some and had to make further adjustments, mainly due to some of the materials I used. I spent less than $500 including the power and mostly new steel. I took it up to the farm where I had several logs waiting to be cut up. It's worked surprisingly well. A bit slow on the large red oak, but if I have a new blade it cuts fine. This is with a 5hp electric running the band at 5200 fpm. The electric is nice because you can shut it off at the end of a cut, remove the board and reposition the saw head for the next cut. I use mine to cut up blow-downs. I take my time and average 250 bf for a long afternoon. It's not too exciting working in the hot sun, with sawdust blowing in your eyes. Or forgetting to lower the log dogs and running into them with the blade. Or lowering the blade while it's hanging over the log and putting a nice kink in it. It sure is nice to see that stack of lumber at the end of the day, though. I've also learned a lot about milling lumber.
Here's the other side.
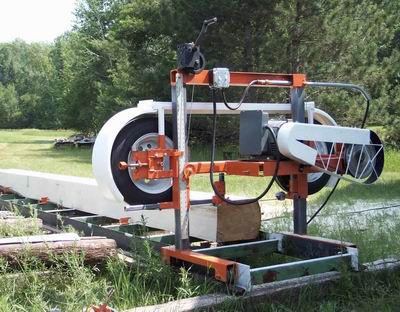
Nice looking job and you have it well shielded. Two questions: about how many hours to fab? And any problems with vibration? Be careful stopping and starting motor after each cut - it will overheat and burn out the starting winding.
From contributor R:
It's hard to say how much time I spent working on it. The project was in the shop for about a year, with some pauses in activity. I did spend a lot of time staring into space trying to figure out some of the details and at the same time to keep it simple. Getting the drive hub adapter set up true was a little tricky, especially since it runs at 60 mph. It runs pretty smooth, now. I'd still like to get the wheels balanced. The fenders are a bit minimal compared to the factory models, but it's a snap to change blades and I can see what's going on while I saw (if I'm looking). The one time the blade came off when I was trying to back out of a cut (mistake), nothing much happened. So far no broken blades. The motor is off almost the same amount of time it is running, but if it does fry, I'm going to a 7.5 or 10 hp electric. So far I've been peeling most of my logs, which is a time consuming job. I've been thinking of using a biscuit joiner as a debarking saw. They're fairly compact, have a lot of power and a wide kerf small diameter blade, but probably a relatively short life.
The comments below were added after this Forum discussion was archived as a Knowledge Base article (add your comment).
Comment from contributor A:
My father and I build sawmills for a living. I love to cut logs into lumber. I have found a nice product to debark logs. It goes on your chainsaw and is called the Log Wizzard. It uses 3 1/4" planer blades. It helps you save bandsaw blades from dirt and rocks when you skid them.
Comment from contributor B:
I looked at every picture I could find on the Net. Put all of that together in my head, made a sketch in about 5 minutes, then went to my 10'x20' shed with my $350.00 wire welder, $350.00 torches and my $10.00 4" angle grinder, and got to work. With a lot of bed frame, all thred, lawn mower parts, bike parts, etc, I built a small band mill. I have $425.23 in it. The only thing it lacks is log dogs. I have already cut some trial pices and speced them. They are within 1/32". I put about 4 hours per night and 8 hours Saturday and Sunday for 3 1/2 weeks, but well worth it. Down side: too small. I used lawn mower tires and 105" band, so I can only cut about a 19" log. I think I will finish this one and use it while I build a bigger one. Don't forget to check out your local scrap yard. They sell me steel for what they pay for it - I just have to dig. Saves a load of money.