CNC Machinery for Solid Wood Joinery Versus Panel Processing
A discussion of CNC machine characteristics as they relate to the type of woodworking being considered. August 3, 2009
Question
I have been in talks with Masterwood, SCM, Morbidelli, Buselatto etc. and there is one thing they all love to say about each other and that is "don't buy that make, it's not a joinery machine it's for panels." So, my question is: what is the difference between a panel machine and a joinery machine?
I gather that the bed on joinery machines only need to be 4' deep and not 5' like the panel machines. The reason being that the operator has all on reaching 4' to place a component and 5' is impossible, so anything over 4' is a waste of space. For a joinery machine the clamps and pods have to be easily interchangeable without having to remove allen key screws which is very time consuming. The bed for a joinery machine needs to have a working bed length of around 16' to fit a stair string on.
A joinery machine needs to have a working material thickness a lot greater than a panel machine. I have come to the conclusion a 4 axis joinery machine would need about 7" material thickness and a 5 axis would need about 12". I am open minded about this because I have no actual operator experience. Can anyone else please help me outline anymore differences?
Forum Responses
(CNC Forum)
From contributor B:
Someone may correct me here but it sounds to me like you are talking about the difference between a CNC router and a Point to Point machine. The basic difference between the two is a CNC router has a flat surface typically with a bleed board MDF hold down system for panel processing. Whereas most panels might be 4x8, a lot of people prefer to purchase a 5x10 or larger machine for the extra capacity.
A Point to Point is typically has a rail and pod hold down system. The pods can be located anywhere along the rails for specific wood part placement. Since the rails and pods have no flat bed below them, the part is in effect, suspended in mid-air so that the router head can come in from the top as well as the sides of the parts, allowing for top and edge processing of parts. Doing this type of work on the flat bed CNC router requires the installation of custom fixtures to hold the part above the table.
Both types of machines (depending upon brands and spindles) can accommodate aggregate heads that expand the capabilities of the machines. So, generally speaking the primary difference between the two types of machines is the hold down system. CNC routers do better with panel processing and Point to Points do better with wood parts machining processing.
Jeff
From contributor F:
When evaluating travels on 5 axis machines you always need to consider the pitch axis pivot length. This is the distance from the end of the spindle to the center of the pitch axis rotation. This varies from 1 machine to another from 6" to over 10". Add the tool holder and cutter stick out to that total and you can easily have a 12" pivot distance. Now, take this and multiply it by two for the total useable work envelope you have X, and Y when the pitch axis is at 90 degrees. A five foot travel becomes three feet. Also, consider the Z axis since parts will need to be elevated off the table the height of the pivot to the center of the cutter line. If a part is elevated 9" with a 3" tool sticking out you have to subtract the 9" part elevation and the 3" tool from the total Z axis travel. A 5 axis machine with a 24" Z travel in this case would only allow 12" of useable work envelope.
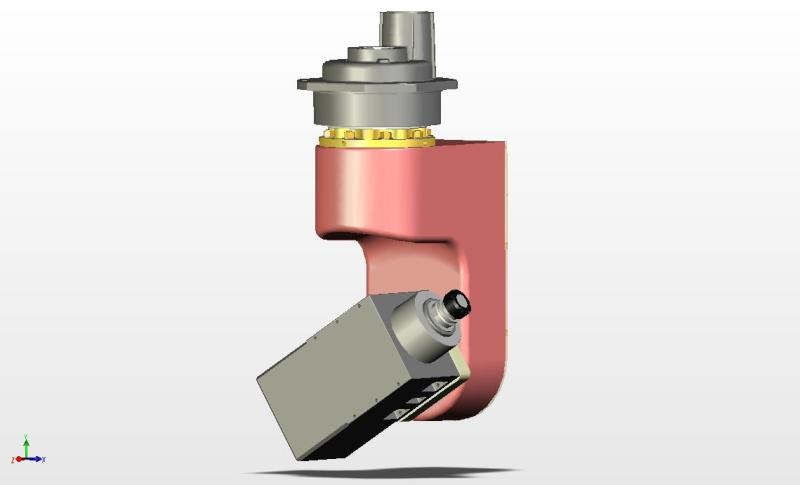
Click here for full size image
From contributor J:
In reality, there's no such thing as point-to-point machine. All modern CNC processing centers are capable of interpolation. It's time that such archaic terms as point-to-point and joinery machines are no longer used to describe CNC processing centers.
From contributor M:
You can also consider a hybrid machine like the one we have. It's a Busellato, and has a 5 x 20 foot work area. It is then divided into two primary zones of 5 x10 foot. On the left we have a flatbed table for NBM work, and on the right we have traditional rails and pods. It's the best of both worlds in one machine. If we need extra length we can put a false spoil board over the pods which then makes them level with the flat table. We have done parts up to 16 feet in length using this method.
From the original questioner:
I see now why people need 5' deep beds. I have wondered this for some time and the answer is so simple: 4' x 8' sheets. The Busellato 5 axis has a 5' deep bed. A 5' machine would have a lot heavier construction than a 4' machine and thus be a needless expense for me. I don't think I need 5' because I am going to be machining stairs and windows, so I feel 4' is enough. I'm also limited on space and a 4' machine takes up less room than a 5' machine. I didn't like the Busellato because the clamps and cups are interchangeable via four screws on the saddles. We do a lot of one off jobs so we will be doing a lot of swopping and I don't think we would appreciate all those screws. I didn't consider splitting a CNC bed into one half flat and the other half pod and rail. Maybe this would be something for me to consider in the future. Pitch axis pivot. I have never heard of this but I can sort of understand what it is about. The thing is, as far as I can see I will only be machining out curved handrail in the 5 axis mode so I think I should have enough room for this.