Cabinet and Millwork Installation Forum -- Coping Choices for Crown Moulding
Trim installers debate the relative merits of coping saws, jigsaws, grinders, and worm-drive circular saws for fine trimwork. October 3, 2006
Question
I am curious as to how most of you cope your crown molding. We have done it for years the old fashioned way with a coping saw. We tried a coping foot that was available for jig saw but that didn't work for us. I am looking for a faster way to get the job done and wondering how the rest of you guys are doing it.
Forum Responses
(Cabinet and Millwork Installation Forum)
From contributor A:
We use a 4.5" angle grinder with a 60 sanding disk. It works pretty fast.
From contributor B:
I’m still doing it the old fashioned way too. I just use a Dremel with a sanding drum on it for the final profiling. Get close to the line with the saw and you can go pretty fast if you don't have to be perfect. Then touch it up with the Dremel. It’s not super quick but faster than if you try to be perfect with a coping saw. There is also a machine to do it. I think the name of the machine is Copemaster.
From contributor C:
Did you get a chance to see that guy demo that coping foot? It is pretty impressive. My guess is that with some practice that's an awesome little attachment. I own one but have yet to devote the time to really learn to use it. I've also seen the Copemaster demo and it too is an awesome tool. It is pricey and there is also a learning curve. We're a custom cabinet shop, so we don't do a lot of coping. All our stuff is square and so miters usually work. We'll do it on the bench if it's even remotely possible. For those occasions that we need to cope a large maple profile though, I have to believe that there's an easier way than a hand held coping saw.
From contributor D:
I only do three or four finish carpentry jobs a year. I use a coping saw and a good blade. I use a variety of different shaped files and even chisels to sweeten the cope when necessary. It is like any other hand work to me. If you really pay attention to what you are doing it gets easier and faster every time. If all I did was install trim I might look into one of the gadgets.
From the original questioner:
I am familiar with the coping machine but as I recall it is around a couple thousand dollars and we don't do that much coping. I just was wondering if anybody had a faster method that I'm already using. I do use the angle grinder with the disk also but it is hard to get into some of the tighter turns of the molding adequately so you end up filing or rasping or whatever to get the final finish. This seems slow to me.
From contributor E:
One of those little bench top bandsaws is what I'm going to try for coping. It works well on the shop bandsaw but it's not exactly portable enough. We also pre-cope several pieces at the shop, so on site all we have to cut are miters and straight. A quick and easy on site option would be good.
From contributor F:
Part of my sordid past includes time spent as a production trim guy. Repetition is the mother of all learning and I believe that a coping saw is as good as anything - fast and accurate. Please don't be offended if you already know this but the coping saw is the only western style saw that works on the pull stroke. I have in my travels crossed paths with frustrated folks that tried to use it the other way around. Don't for get to back cut lots more than you would for base.
From contributor G:
Crowns do not need anymore back clearance then baseboard. Most walls are 1 degree + - out of square. 2 degrees is 5" out of square over a 12' wall. When is the last time you saw a 12' room 5" out of square. The problem arises when you go to shift the crown up to close up a gap at the top. Now you need to create some back clearance in the up and down direction. You should not have to shift your crown to close a gap. That gap is because of a long miter saw cut and or the square cut piece was set at the wrong wall and ceiling projection.
From contributor H:
We use the Collins coping foot for coping base as well as crown moldings. Once you get used to holding a jigsaw upside down, it is simple. It does make a huge difference what blades you use. The more aggressive blades actually work better. We also use a Dremel tool to touch up tight areas but I have an upside down cone shaped grinding bit that works really well.
From contributor I:
I cope every inside 90 - crown, base, even shoe - both stain and paint grade. I'm not a speed demon, but my method is reasonably fast with tight joints. Being a righty, I like to cut copes on the right side of the board. I shoot to plan my work that way.
1. Bosch jig saw. Crown laying flat on some horses facing up. Hold jigsaw by barrel upside-down (blade pointing towards sky) and just cut close to the line. 1/8" is good enough.
2. 4" angle grinder with a sanding disc. Depending on the profile, usually 36 grit is best. I'll sometimes run two grinders - a 24 grit for heavy hogging and a 50 for lighter thinning. With a little practice, you can follow almost to the line. And wear your glasses, those chunks are moving fast.
3. Files - get some good sharp files, not grandpa's hand-me-downs. I use two or three different diameter round, flat, triangle. I usually have about 5 laid out when coping. You should need just a few strokes to clean up. It should be from 30 seconds to 3 - 4 minutes depending on detail.
I like to make a 18" test cope prior to starting, so when nailing the straight end, you can test spring angle + cope fit. For example, I ran 255' of 6" crown this past Thursday and Friday with one helper - 38 corners plus 3 mitered returns. All insides coped onsite, primed poplar, for 9' ceilings. We setup and started on Thursday, and crown was done about 2 on Friday. Please don't take this any kind of bragging, since I don't think it is fast. I’m posting it as a point of reference that coping is not slow, and gives a much better fit.
From contributor J:
I coped a lot of crown in my days as a trim carpenter and never had the desire to use anything but an old fashioned coping saw with a good blade. A little wax or lube on the blade helps. A lot of times I would cut all of the pieces to rough length and do all of the coping on the bench at one time on the right hand end. I cut the curved portion from below and the straight parts from above. Repetition and practice equals speed. With some practice you will be able to do most of the work with the saw and trim it up a little with a sharp totality knife.
From contributor K:
I have 20 yrs as a trimmer, and in my opinion, the coping saw is the only way to travel. With a small amount of time you will get quite good at it and it is fastest and best found so far.
From contributor L:
In my experience there is no "only way to travel" when it comes to coping. For instance, had the Copemaster been developed earlier, I would have been doing most all my base and crown from 1979 onward with it because I worked for myself and did nothing but trim - for the most part trim with fancy profiles. There just is no faster or better way to do it. I started using a jig saw in the mid seventies for most profiles, though I kept (and keep) a coping saw handy as well as triangular and rat tail files and a 4way rasp. A jig saw seems to me to be basically a motorized coping saw, and I have never met anyone who could cope large crown molding faster, or any better, with a manual coping saw than I can with my motorized one.
From contributor M:
From a craftsman’s standpoint, I think a cabinetmaker or trim man should have mastered a coping saw in his or her early days. I don't see the need to spend money on some fancy contraption dedicated to coping. If you are dealing with custom cabinets they should be square and a miter should give a good tight joint, but if a cope is required, pull out that old coping saw and go to town. Unless you are sawing 7 inch crown or hickory or something it should only take a couple of minutes. I don't mean to offend anyone, but the early woodworkers would have laughed at this forum for even bringing up an alternative to such an effective method. My standpoint is, learn to use the tools of the trade and don't rely on technology to make routine jobs easier.
From Gary Katz, technical advisor, Cabinet and Millwork Installation Forum
Excuse me for saying so, but I think many of those old craftsmen would have said "WOW", seeing as how they were working by the hour, the day, or the piece, too. Money does tend to make us look for ways to improve. That's probably one of the reasons progress is considered a double-edged sword, but I won't go there, and I don't mean any disrespect for those who still use a coping saw. I know how hard it is to learn new techniques. I coped with a coping saw for more than 25 years before forcing myself to learn how to use a coping foot. I'd never consider going back. I'd also never consider using a grinder - too dusty and noisy and can't get into tight beads. I don't need files or Dremel tools or anything else. Used correctly, with the right blade, the coping foot is magic. And I've also met a lot of production guys who make much better profits on crown and base using a copemaster, but then you need to be installing hundreds of feet of molding all the time.
Technology has its merits. I sure prefer my compound miter saw over my old radial arm - dragging that to the jobsite wasn't fun at all. And I sure like fast-acting glues, and nail guns, and my door plane, and, well, I think you get the picture.
From contributor O:
I think that everyone in this trade should learn to master the hand tools. Good hand skills are lacking in the apprentices that I get these days. In my opinion guys who are skilled with hand tools get better results with power tools. I also remember an old carpenter when I was an apprentice who couldn't straighten his fingers out. They were almost like claws - he has nerve damage from a career planing doors with a massive fore plane. He was also bent over and listed to one side from being bent over working on doors and slugging them for 50 years. I don't know how many other guys that I know who had to leave the trade prematurely because their crippled up from slugging. I get paid for results, and I'll take any labor saving device I can get. Get the job done fast - make lots of money - and have time to spend with family and friends. I have some free time this week. I had the planes, chisels and handsaw out in the shop. I spent all day making something I could do in an hour if I wanted to. But at work it's down and dirty, get it done. I mainly use a jig saw to cope but I also use a coping saw, mini grinder, Skilsaw, files, sandpaper glued to dowels and a utility knife. If I were doing the volume to justify it, I'd definitely get the Copemaster.
From contributor I:
To Gary Katz, forum technical advisor: I'd probably clean up with the jigsaw more. I just never picked up the Collins foot. Thus with the standard flat jig base, it is harder to angle from the back. I agree the 10,000 rpm grinder is dusty, but fast (and needs a steady hand). On my last job, the home was being lived in, so I would cut the 45s for the copes on 2 to 5 pieces and my helper would take them outside for the coping. As for getting into tight beads, the grinder sanding disk is what, about a 1/16" thick? Any tighter, and just back-grind, and you just need a few strokes with a file. This was the 6" crown that I mentioned, pretty easy profile. For caulk, they'll need more on the humpy walls than in the corners.
Also, at the end of your Collins foot review, you show a method for leaving the sliver for a miter when the profile goes horizontal. It's probably just me, but I can't carry one of those more than 3 feet without bumping or breaking that tip off. I'll always go with the butt-cut on the paint grade.
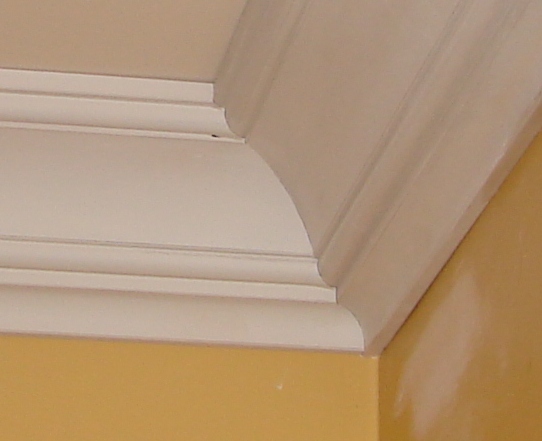
Click here for full size image
From Gary Katz, technical advisor, Cabinet and Millwork Installation Forum:
To contributor I: Yes, that little sliver used to break off on the first step up the ladder. Now I cut them about 1/8 in. thick, which I can do free hand, without the block of wood. It is much quicker. It doesn't matter how deep you cut the mitered mortise in the butt-end piece. The cope and sliver always cover it.
From contributor D:
My take on hand tools versus machines is this: machines are wonderful inventions that help speed the work. Used correctly they can also help prevent us from being in poor physical condition in our twilight years. After banging away at most of the affiliated branches of woodworking for decades I have discovered this: machines don’t replace hand tools. Machines supplement hand tools and vice versa. My career became much more fulfilling after I learned to sharpen, maintain, and use saws, chisels, planes, spokeshaves, scrapers etc. I became aware that there are and always will be tasks for which a hand tool is the more efficient choice, and often, the only choice.
From contributor L:
I agree with you. Most power and hand tools complement each other. I too use a coping saw often and prefer it over a jig saw for base cap. As late as 1977 I was hewing beams out of logs with an adze and turning them with a peavey. I was also mortising them with a bit brace, corner chisel and mortising chisels. Unfortunately, the logs were cut during the summer; had they been cut when the sap was running I would have peeled them first with a bark spud and would not have been so filthy at the end of each day of hewing. The sawmill owner I bought the logs from (and whose field I used to work in) thought I was crazy. That was the hardest trim job I ever did as well as the most beautiful, the most valuable, and the most fulfilling. But I must admit - it was far from the most lucrative. Too bad it wasn't my house. I've always used a hand saw for finishing birdmouths instead of overcutting with a worm drive. I still use an offset back saw and shooting board when doing jobsite jackmiters. I still use chisels for all kinds of stuff, and not too long ago did a raised panel job where the field of the panels was hand planed with my favorite Bailey Sweeheart jointer plane.
From contributor O:
A note on using a mini grinder - I use a 4-1/2" Walter backing plate and 5" 3M green sanding discs. The Walter backing plate is really thin and the 3M discs are really stiff. I use 2 sanding discs back to back so I can use both edges of the sanding disc to get into tight spots. The mini grinder is a great tool for scribing too. I use it mainly for tops - the belt sander rarely sees the light of day any more.
I find the issue of hand tool use really frustrating, especially with the young guys. Even with stuff like door hardware - of I have an apprentice to install some locksets they invariably go for the cordless drill. I want them to use screwdrivers, especially in hollow metal where it's easy to overtighten, but it's like it's more fun with power tools and "I'll get bored if I don't use power tools". Most of these kids don't even own a set of screwdrivers but they have a cordless drill and titanium hammers. I had a second year carpenter a couple of years back ask me to "lend me your wedge thing" which of course referred to my chisel. The same kid said "wow, that is so cool" when I took a block plane out of my apron to fit a panel. He had never seen anyone use a plane before.
Part of the responsibility for this I lay at the feet of the schools. I just finished trimming a new high school, and the shop class had work benches with no vises, but they had a CNC router a stroke sander and a wide belt sander and all the other big stationary tools. It's all very nice to program a CNC machine to drill your cribbage board but I would much prefer to have kids coming out of shop classes able to dress lumber and use hand tools. How can you learn to use hand tools when you don't have a vise on your workbench? The other culprit is the cult of the power tool. Why do you need hand tools, math skills and theory when a laser guided cordless tape measure can do it for you?
From contributor F:
When I came out in favor of the coping saw over the jigsaw in an above post I was probably being a little misleading. I have a couple of Bosch jigsaws that are absolutely indispensable. I periodically cope crown with them but I like using the coping saw better. Power tools are a fact of life now for all of us. It isn't a bad thing but it is a different way of working.
The standards that we work to have changed with the development of power tools as well. The house that I live in was very competently built in 1949. The trim is all douglas fir that is knot free. The miters on the casing are not as tight as what I can do in seconds with my SCMS but I actually like the work that was done here 50+ years ago more than some of the work that I do now. Most of us now only go for the hand tools when it really can't be done with power tools. In case I have started to sound a little nostalgic I want to say that while I will be happy to keep playing with my coping saw a little while longer, the miter box that I started with can keep on living where ever it ended up.
The comments below were added after this Forum discussion was archived as a Knowledge Base article (add your comment).
Comment from contributor A:
I use a jig saw to rough-out then use a 1 1/8" Makita belt sander to fine tune the cope. I love the sander because it's faster than a rasp and can get into tight places.
Comment from contributor B:
I agree with Contributor O. I still maintain and use a variety of hand planes and chisels yet for coping and scribing my angle grinder with a 36g disk is indispensable. I rarely need to file, and yes my copes are very tight. Sometimes I adhere a 100g sanding disk to a piece of the molding I'm coping and use it to clean the profile. I learned with a coping saw but have not used one in years. My only fear is the arthritis now settling in my wrists will prohibit me from having the steady hand needed to do it.