Cleaning Out a CNC Auto-Lube System
A shop owner gets help figuring out how to get the auto-lube system on an old, poorly-maintained Biesse Rover up and running again.August 22, 2013
Question (WOODWEB Member) :
I have another issue with our Rover that I hope someone can help with. It is a Rover 27, year 2000 running NC 1000. The Auto-Lube system doesn’t seem to be working. It’s most likely due to the grease in the lines being more than three years old. I have ordered lube and I will replace all the old grease when it gets here. I’m not in the U.S. but I ordered from BVC. I can’t find in the controller where the lubrication schedule is. I assume it pumps grease every few minutes of operation or something like that.
I want to manually override the lube cycles in an attempt to flush the lines. If the pump can’t push the grease through the bearings, I can pull the lines off and flush them that way. I see there are settings in the PLC window but it is beyond my understanding. I suspect there is an M-code or some utility I have not discovered. I have no manuals except some kinds WOOWEB members shared with me.
I hope there is an easy way to force the system to cycle. If not I can hot-wire the solenoids that control it. It looks like there are two, one for the pneumatic pressure to the pump and another at the grease distribution block. Or the one at the grease manifold could be a flow sensor of some sort. I have not traced the lines back to the MOD or wherever it goes.
Forum Responses
(CNC Forum)
From contributor C:
Open the control cabinet (4" square box with a black button) press it a couple of times with five second intervals while the machine is running. That is the manual override, I'm not sure how it works in the auto, but mine goes through grease regularly.
From the original questioner:
Is it a regular 24v contacter or something special? I think I can match the tags on the wires. I am including a pic of the electrical cabinet. Can you see it in there? If it is just a normal contacter I can trace it.
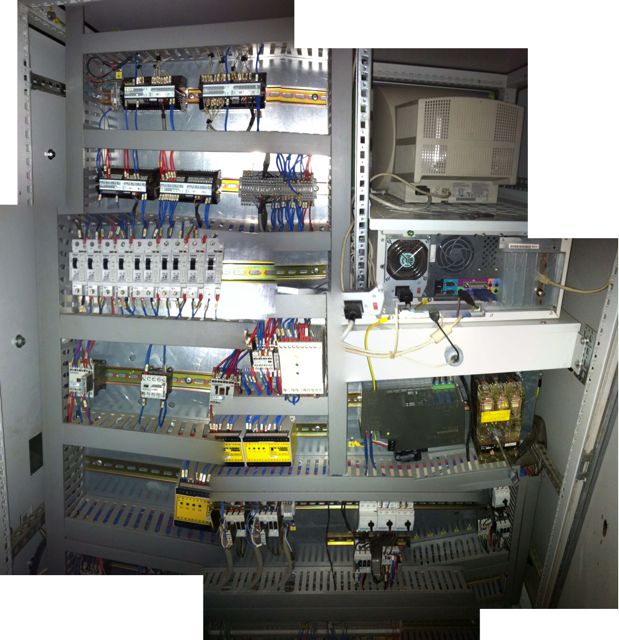
Click here for higher quality, full size image
From contributor Y:
Not the correct side of the cabinet. It’s in the front on the right, actually a gray button towards the bottom left. If it’s not in there it’s near the tear-drop button on the plc console. The machine has to have a green button or control power.
From the original questioner:
I don’t have the schematics for this machine so it would have taken me hours to trace it back to the front part of the cabinet. I forgot there are a couple of relays in there. Is it is a single gray momentary push button? Sorry I keep confirming the location switch - I just want to make sure.
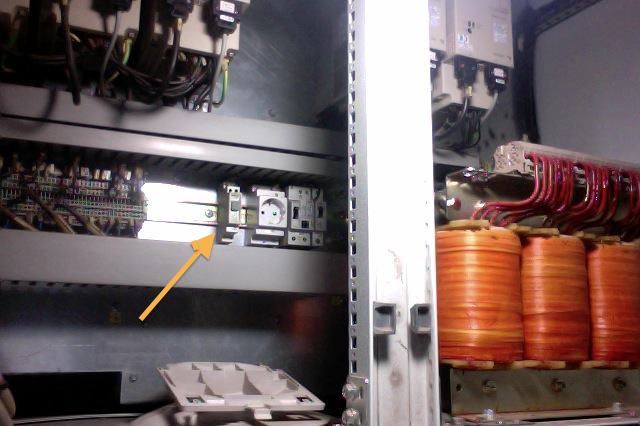
Click here for higher quality, full size image
From contributor Y:
Yes that is it - press and you will hear the valve fire.
From contributor M:
Go to Technical data, PLC tables, "Lub". Hora is how many hours and pompa is how many pumps. I'm guessing hora says 25 and pompa says 1. You need to change the hours to 7 and pumps to 2. This will give 2 pumps every 7 hours. Wipe fingers on linear rails and Z ball screw to see thin layer of grease. Don't forget to grease both X and Y rack and pinion with EP0.
From the original questioner:
All the air is out of the system and the linear rails are looking good. I think I will have to replace the linear bearing rubber seals (if this is an easy repair). They do not seem to be sealing tight to the guide.
The grease is so old the oil has separated from the thickeners. It is amazing that a machine like this could sit around for so long not being used. What is worse when it was used it was ran without dust collection and no maintenance. The gunk was so thick on the bearings and operating head that you could not make out the individual components. I have modified the PLC table as recommended as well.
From contributor D:
Is the grease getting to the bearings? If it has the wrong grease in it, it will harden and not flow through the lines. If this is the case, you can get a push connector fitting for the grease gun and connectors for the grease lines. Disconnect the line at the bearing and on the long lines and cut them about half way. Connect your grease gun with a slip on fitting and pump slowly until you get good clear grease running out the ends. Connect the line and use a fitting to repair where you cut them. You can get fittings from Grainger and other industrial supply houses.
From contributor M:
Contributor D is right. Some people cheat the system and get Mobilux EP1 because they can't find EP0 in a cartridge (BVC has it) which is thicker and will not cycle through the 1mm hole in the linear bearings.
From the original questioner:
There is no telling what the last guy’s put in there. It is tan in color and looks like EP0 but it might be Vaseline mixed with baby powder for all I know. I think the real issue is this grease has likely been in the system for the last several years and the machine has not run more than three hours in that time; at least not until I started reconditioning it.
I have replaced more than 150 meters of PU hose on the machine and there are still lines blowing every time I start it up. The dust and grime was caked on so thick the linear bearings were not visible. The muck was so thick on the machine head that you could not see the aluminum of the boring block. Dust was packed into the narrow spaces so deep I had to use improvised scrapers to clear out the passages.
There were missing screws, loose connections, lots of bailing wire holding things together and more. The crazy thing is I am pretty sure this machine has less than 100 hours of run time on the clock. No one has ever been able to make it productive since it was delivered to the Philippines in 2001! The sorry condition is not from overuse it is from no use and running with no dust collection or maintenance.
I ordered 5 cartridges of EP0 from BVC and all the other lubes. Until they arrive I will just keep manually monitoring the guides. When I looked at the PLC table there was a long list of parameters but none that matched up with your instructions. I would like to increase the frequency of the lube cycle. I have never heard it cycle at all, except when I manually hit the magic grease button. For now I have to go find more 6mm PU hose! I used up the 50 meters I bought last month.
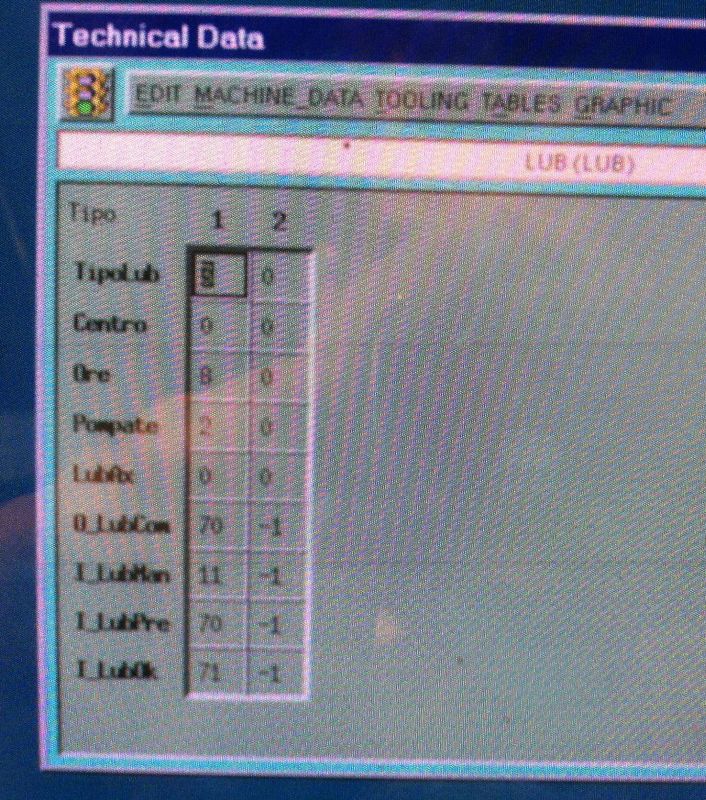
Click here for higher quality, full size image
From contributor D:
Go to Statistics Editor, Reliability Statistics and look at the bottom of the list to see the lube counts. Press the manual button, wait a few seconds to see the count change. Go back there after running for 10 or 15 hours to see if the count has increased.
From the original questioner:
This procedure would confirm its operation manually and allow me to monitor the frequency, but I don’t see the parameters you mentioned in the PLC Tables. I would like to set it to your suggested settings.
I really need training on this machine but the local techs are not as knowledgeable about the systems on this machine. They can show me the process for loading and executing programs but I want a more technical training session. Once the machine is running reliably (it still blows PU hoses once a day) and all the tooling is set up I will try to find a tech that can do web based live conferencing. Or even just Skype.
From the original questioner:
I am waiting for the Becker rebuild kit, lube, gaskets and other maintenance supplies I ordered from BVC. I am afraid to run the machine too hard as it is now. I also have no tooling yet except for a couple of straight flute insert tools the cut very poorly. I am putting together the tooling list and getting prices right now. After all that is done I will get the training set up. Biesse has techs based in Singapore that are supposed to be good, but I have been burned too many times with incompetent factory techs in this corner of the world