Conference Table Stability Concerns
A custom conference table design draws criticism for being top-heavy (and easy to scratch). February 17, 2011
Question
The only way I can see this working is with a steel frame. I'm thinking a 1" tube frame with two layers of 1/2" MDF overlapping seams on top, and 1/4" MDF bottom and maple edging. The legs would have to be bolted to the top and floor as not to tip over. We have never built a table of this size, so any input would be greatly appreciated - especially any
thoughts on wood movement. Can we glue a solid wood edging to the MDF?
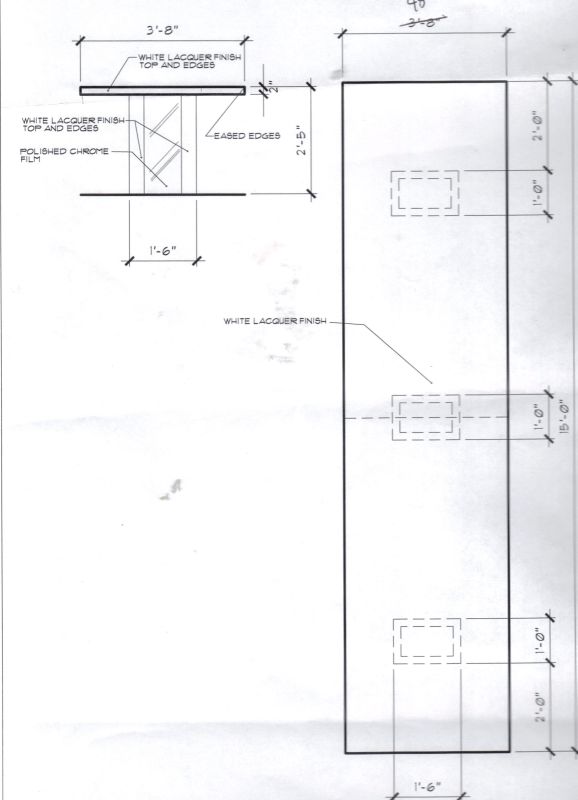
Click here for higher quality, full size image
Forum Responses
(Architectural Woodworking Forum)
From contributor C:
No problem with steel tube frame and solid wood edging over MDF. On legs like yours, I also epoxy 5mm veneer directly on to sheet metal. The only problem I have is with your legs: white lacquer and shoe marks are not a good combo.
Also, to provide stability, I fill my hollow legs with sand (make sure it's dry) or use steel ballast. And yes, the legs are bolted on after you've managed this beast up 'x' amount of stairs or have had to hire a crane to bring it in through a window.
From contributor R:
Better make sure your liability insurance is up to date if you build that as shown. If that thing ever goes over, it's going to kill someone. I had a similar project, but it was a pedestal design. They wanted to put a computer tower in the base as well. This was before wireless. I had a steel angle iron base made and bolted it to the floor. I slipped a box with doors (for computer access and bolt access) over the base, and then dropped the top on. The top was a torsion box with internal steel plates and bolts welded in them. The bolts went through oversize holes in the base. You could have parked a truck on it when it was all bolted together.
From contributor G:
If it is way up in a building will it fit in an elevator? Hiring riggers to move it up through a window will cost a fortune. I also agree with the others, unless the pedestals are bolted to the top and the floor it is going to tip over at the worst possible time and hurt people.
From contributor O:
My doubts rest in the wood to MDF joint telegraphing, preventing the seamless virginal white surface desired. It will telegraph and the butt joints in the length, even glued and sanded will show, as will any out of perfectly dead flat level sanding. White seamless is not wood, it is plastic. You will not be able to make the wood look like plastic - no one can.
You can count on this tipping. When people see something the size of an aircraft flight deck, they unconsciously see it as solid. So they will park their butt on it, then someone else will do the same. You could easily have 4 people putting 150 lbs each along one edge and there it goes. Core drilling into floor structure or a footprint the same width as the table is the only way to prevent this.
Then there is the finish - is that table really 14' long? How will that spray? The folks that do these all the time get top dollar, as they should. These things are not just a big table as most designers and owners will think in a desperate hope to minimize costs. That same hope to keep it 'within reason' is what drives so many of them to circle around until they find someone willing to quote a big table, then award it to the low bidder. I have seen some spectacular failures over the years. Once you have the specs all together, shop it to three shops that do these all the time and therefore know what the costs are. I'm betting you will be surprised at the costs, as will your potential customer.
From contributor N:
Thanks for the insight everyone. This would be going on the first floor with double door entrances. I was anticipating bolting to the floor to keep stable. What options are there to get a seamless appearance without telegraphing? Would a bar top finish like mirror-coat hide any telegraphing or accent it? I'd like to explore different options before I claim "it can't be done".
From contributor D:
Do you think they would consider a solid surface product? You can do the top in two parts then once installed fill the seam and it will be as close to seamless as you are going to get. If they want a glossy look then it will show every imperfection depending on how the light hits it. You can still do the bases white, but I would see if you can do those in laminate. You have to widen the bases, even if you are going to bolt to the floor. The bases will look too small for the size of top.
From contributor V:
Besides all the problems and answer you have had mentioned to you so far think of this. This is really about stability. I have build tables four feet wide and 20 feet long one piece. The center of gravity has to be made to be as close to the floor as possible. The best way to do this would be to put a solid base near the floor substantially held to the upright supports. Fill the legs with lead shot and fill them to the top. The center of gravity will be on the center line with the length of the table and depending on the weight of the table top and the amount of lead shot should get the center of gravity as low as possible. I do not know if you know this but the Space needle in Seattle has the center of gravity in its base below the line of ground. The lower this point the more stable it will be. Have a good insurance policy, you may be determined to be responsible for something you have no control over. If you are looking for a finish that will look somewhat like plastic check out coloring conversion varnish or ask a commercial supplier.