Construction Hole Boring Accuracy Tips
Here's advice on how to get consistent, high-accuracy performance from a construction boring machine. October 3, 2011
Question
I bought a 21 spin construction hole machine not too long ago and I am wondering how other shops bore cab parts. We do not use a true 32 system. Parts are not in 32mm increments. We use 50mm confirmats and offer a melamine or a pre-finished maple interior.
1) Do you reference the edgebanded face of your parts when boring from the left and right fences, or from just one - either left or right? I have been trying to use both fences for left and right wall sides and left and right bottom ends due to plywood thickness variations. Problem is it's a lot more complicated and I wind up with a lot of extra holes.
2) Do your 5mm x 44mm drills walk off when drilling plywood?
3) Do you end up using spacers between fence and parts to get things to work out right?
Forum Responses
(Cabinetmaking Forum)
From contributor Y:
1) I use left and right stops for both sides and horizontal shelves. The stops are never moved. They are adjusted as close as I can get them. For confirmats you have a little play to flush the fronts (drilling an 8 mm hole in the sides). This helps account for the difference in material thickness. You don't have to readjust the height for different materials. You could use one stop for the sides if you always through drill for confirmats.
2) The brad point bits should not walk.
3) You should not have to use the spacers.
From contributor M:
The left and right fences should be exactly the same distance from the first bit. I use 37mm but I used to use 32mm. Set them as close as you can with a good steel rule, then edge bore the narrow end of two pieces of squarely cut material around 100 by 300 mm. Butt joint the two pieces with a single dowel and use your finger to check the edges and bottom faces are absolutely flush. Perfection is possible. It is standard procedure for the operator to do this check before every batch. It is almost never out of adjustment, but it takes only a couple minutes to check.
If your test pieces are perfectly flush and you are still having issues, check your saw. Doweling requires a perfectly operating panel saw. Even the slightest amount of squareness will prevent a flush joint. Use the 5-cut method to test your saw and use calipers to measure the last off-cut. I usually have around .1 or .15mm of variance over a 1200mm panel. This means the saw is .1mm divided by 4 (or 4 squared?) over a 4 foot cut out of square.
The best way to set these machines up is not with dial gauges and rulers, but to use good stock and read the results of the test cuts/bores.
From contributor L:
Have never seen 5x44mm boring bits...? Any variation in your panels being out of square can cause problems. A partial solution is using left and right stops, not fences. Side fences will reference the widest area, not necessarily the area closest to the bits. Are your bits inserted directly into the spindles, or are you using quick change holders? Quick changes allow some slop. Spacers fix the symptoms, not the problem! Plywood can cause some walk of the bits.
If you are using Confirmats, they actually can be tweaked a bit during assembly. Take a couple of old Philips 6"+- screw drivers and grind them to a dull point. Use them to align the panels as you put them in place. By putting some pressure on the aligning devices you can get some movement and hold that position while final tightening the Confirmat.
Plywood sometimes has a problem with big screws. The plies want to separate. There are slightly oversized 5mm bits available. Check out European Tooling System. They have 57 and 70mm boring bits (but not 44mm) in 5.0, 5.1, 5.2mm dowel bits, 10mm shanks! Best to use 7mm for the outer hole; that's what Confirmats are designed for.
From the original questioner:
Thanks. The bits are 70mm. I was just measuring the cutting portion. My panels are very square. (Hendrick panel saw.) My machine does not have stops, but I will look into installing some, as I see your point. Do not have quick change chucks, although I wish I had. Using 7mm holes for confirmat clearance. Bought this machine used and the head was out of alignment badly. I have pretty much dialed in now. Just need to get familiar with the proper boring sequence. The stretchers are giving me the most trouble.
From the original questioner:
I notice that the drill chucks are bored at different depths, making some bored holes deeper than others. Is that by design? My thinking is that they don't want all the bits to hit the work piece at the same time.
From contributor U:
Adjust the length of your bits using the set screw at the back end of your bits. You can make them all flush.
Eliminate the stretchers. Use a solid top deck. I have been doing so for twenty years, and it makes my life easy.
From contributor L:
When he said "stretchers" I thought he meant drawer stretchers/rails. True, the screws in the bits are for adjusting the bits. Always seat the bits all the way to the bottom of the socket.
From contributor D:
Trying to bore everything with the same layout (drawing) is not ideal and typically requires more holes, especially when you want to include stretchers. Quick change collets make things a lot easier. While the examples are in 32mm increments, you can +/- however you want on the back edge.
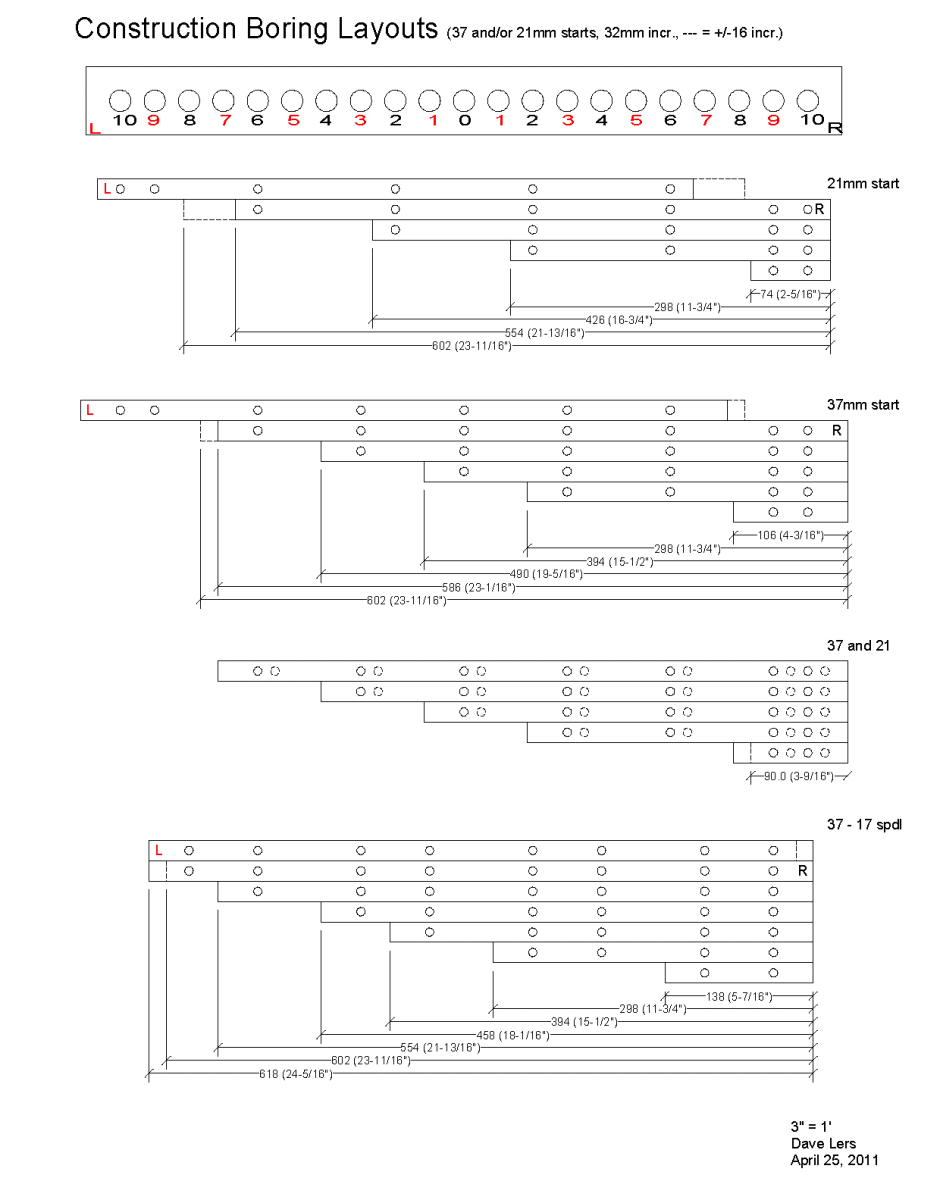
Click here for higher quality, full size image
From contributor Y:
Two more. Start at 32mm or 41.5mm from the front edge. Use the same stop (the very important lead stop) for 32 mm line drill (hinges, slides, shelves) and construction drilling.
From the original questioner:
Thanks - that drawing really helps. I use a different machine for line boring.