Cutting Complex Shapes in 1/2-inch MDO
A long thread of advice and discussion for an unusual CNC project. December 6, 2006
Question
I have to cut 700 of these trees. One tree per sheet of half inch plywood. The sheet size is 48" x 96".
1.) What is your bit recommendation and how many should we buy?
2.) What is your cutting speed and RPM recommendation?
3.) How many sheets would you stack per cut?
4.) What depth would you cut each pass?
5.) How would you clamp the job down?
Our router has a maximum shank size of 7/8" and 21,000 maximum RPMs. I believe that it is a 5 hp router. Below is a sample for this project.
Forum Responses
(CNC Forum)
From contributor G:
Based on some of the tight radii, you should use two tools.
#1 CUD-250-2 1/4" compression @ 400IPM @ 15,000 Rpm's, climb cut, 1 pass
#2 CD-125-2 , 1/8" down shear, @ 100IPM @ 18K, 2 passes
Not knowing the type of material - hard, soft, etc - it would be near impossible to determine tool life. Close guess, CUD - 30-50 sheets, CD about the same.
From contributor C:
I don't see how you could stack that mess... maybe I'm way off? I would use a vacuum pump to hold it down and leave an onion skin of maybe 0.040" and sand through on a wide belt. That thing will chatter.
From the original questioner:
The customer is okay with some of their inside edges being rounded off by a larger size bit. I do not have much experience cutting wood on a CNC, but I was thinking that we could use a 1/2" solid carbide up spiral bit (or a compression bit) running around 40 IPM (at ??? RPMs) and cut through a stack of four half inch sheets in a single pass.
Can a 1/2" solid carbide up spiral bit (or a compression bit) handle cutting a solid 2" piece of plywood at 40 IPM... or faster? If so, what RPM should we run it at?
Regarding clamping, I was thinking that we would clamp down four sheets and cut around the clamp. Then move the clamps and complete the cut.
Again, I am a newbie and I could be totally off base with this approach. The material that we need to cut is 1/2" plywood with some type of light brown, thin paper-like skin on the outside. I am not sure what the industry name is for this type of plywood. I am looking into it.
From contributor G:
You can use a 1/2" compression, @ 12K. May we (Courmatt) suggest a 1/2" ruffer for the first cut with 2 passes and the final cut using the compression. This way you have increased the tool life on the finishing tool, without sacrificing cut quality. Don't use an up shear, as the material will move once part is cut.
From contributor C:
The material is Crezon. I hope you mean 40 meters/min. At 40 inches per minute, cutting through 2 inches of material, you'll be smokin' - literally. Maybe even some flames, too. I think contributor G's tooling approach is appropriate.
From contributor C:
Contributor G got his response in before me, so I like his first tooling approach best. The second is an option if (that's a big if) you decide to stack, but that would be one heck of a clamping job. How do you hold down regular stuff on your CNC?
From contributor D:
I think they call the material sign board.
I also think contributor G was right with the bits, though I would go a little faster with the out line tool, maybe 600 ipm. If you can clean up the tight radius with a 1/4" down sheer, you could get faster cuts in one pass. If you can go those speeds, you will only need to cut one at a time to achieve the same or greater quantity of parts in same amount of time. I wouldn't even mess with getting any clamps in the way - you may just be looking for trouble.
From the original questioner:
We are cutting primarily EPS foam and we use duct tape to hold it down.
Since we need to cut 700 of these, I was thinking that we would want to stack them to reduce labor. I did some tests cutting two stacked 1/2" sheets (a total of 1") using a straight edge, carbide tipped 3/8 bit, 1.25" long with a 1/2" shank. I ran the test at 60 IPM (1800 RPM) and I broke two bits. Is it possible that we are running too slow and this is causing the bits to break? The factory defaults for 2D cutting wood in ArtCam are pretty conservative. They only recommend a single pass cutting depth that is around the same diameter of the bit. Where can I find industry standard cutting speeds and depths for different bits and materials?
From contributor C:
You would break them at that speed. You might also be breaking them because the two layers are chattering together. I understand the necessity of reducing labour, trust me. There really is no "standard" in the industry - you just have to test and figure out what works best for you. And yes, you are cutting too slow. For new materials, I start at 300 ipm and 18K rpm. I have cut Crezon before with a 3/4" diameter 1-1/8" long cutter at 500ipm @18K rpm, but that was with simple straight and curved parts. Nothing like you're working on.
From the original questioner:
I have not had the opportunity to work with anyone with CNC experience, so I am really just trusting that the ArtCam factory presets are somewhere in the correct ballpark. But it seems as though you guys are cutting much, much faster and deeper in a single pass than the ArtCam defaults.
I assumed that because I was breaking bits, I needed to slow down, not cut as deep, or use a thicker shank. But it sounds like, if I understand correctly, I should be cutting at a much faster speed than 60ipm?
I do not want to confuse things, but what kind of cutting speeds and bits do you use to cut a single sheet of 3/4" MDF? And finally, do you run into dust extraction issues when running at these higher speeds? When I get above 100ipm, it seems like I have dust flying everywhere.
From contributor C:
Slower feed rate equals heat. Heat equals broken bits. You want to go as fast as you can while still getting a quality cut. I run 3/4" MDF at 500ipm and 18K rpm, but I have an older machine; you could run faster if you had higher max speeds. There will be dust everywhere - most wood CNC's have dust collection on them. If not, people rig up a shop vac or whatever. Even with the best possible collection system, you'll still get dust on the floor.
From the original questioner:
Why on earth would ArtCam's default cutting speeds be so slow? So how do you determine how deep you can cut a single pass? For example, on your 3/4" MDF that you are cutting at 500ipm. Other than just experience, is there a general rule of thumb or formula that you use to determine cutting speeds and depths?
From contributor C:
Mostly just experience... Type of material, tooling, what you are cutting (i.e. shape and size). Matching the diameter of the cutter with the depth of cut is a good start. Test, test, test... Did I mention testing? Woodworking in general is not a perfect science and now you're adding the variables of a CNC.
From contributor G:
Artcam traditionally always, always uses a slower feed speed, because traditionally they use a smaller diameter tool, such as .125, .062 ball end.
Contributor C, slow your rpm's to 15K - better tool life.
Cutting this foam material, you need the correct tool. A TCT type will not work.
From contributor D:
I cut 3/4" melamine particle core with a 1/2" mortise compression bit at 950 imp. Have never broken a bit and can get 200-250 4x8 sheets of cabinet parts per bit. I also use Artcam, though I set up all my own feeds and speeds. When I cut 3/4" solid wood (oak, hickory, maple), I will not cut through in one pass. I will run 6 passes in 1/8" increments using a 1/2" 2 flute down sheer at a speed of around 600 ipm. I find I get a better finish and no movement no matter how small the part.
From contributor D:
All the spindle speeds on my previous post are 18000 rpm.
From contributor C:
Thanks, contributor G - I'll try that next time I get into some MDF.
From contributor T:
To the original questioner: If I am reading your post correctly, the tree is ~4'x8'? If it is, you should have no problem just holding down with the vacuum. I just got done cutting sign board for a job, and I was running a 1/2" diameter diamond compression bit at around 17000rpm and 250 ipm, cutting the full 3/4 in one pass. Artcam's presets for their roughing tools are off, so don't go by them.
From contributor E:
To the original questioner: Your RPM's need to be increased tenfold. Your IPM's fivefold.
From contributor O:
"Why on earth would ArtCam's default cutting speeds be so slow?"
Otherwise you could really screw things up. Personally, I wouldn't even bother stacking the parts. That way you can use the "bridges" to hold the pieces while machining. (See image.) I use double sided tape to hold the plywood to the spoil board, then stake the corners with screws. For ply, I prefer compound shear or down shear tools. (See image).
How fast should you cut? As fast as you can. You are trying to make money, right? If I'm sure how a material cuts, I set most of my ArtCAM tool defaults to 300 ipm for (xy axis) and 75 in (z). Then just adjust the feed rate override on the controller. Turn it down to 25% for the first pass. Go up from there. Or you could do the math.
CL means Chip Load
FR means Feed Rate
#CE means Number of Cutting Edges
S(RPM) means Speed
To Calculate:
CL= FR/(RPM x #CE)
FR= RPM x (#CE xCL)
S(RPM)= FR x (#CExCL)[/i]
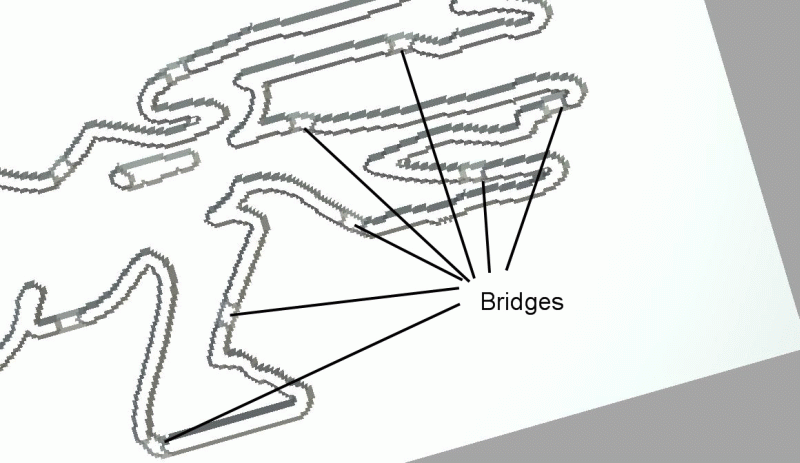
Click here for higher quality, full size image
Compound shear and down shear tooling:

Click here for higher quality, full size image
From the original questioner:
Thanks, contributor O, for your detailed feedback. I will look into the tools that you recommended. We do not have a vacuum table or vacuum clamping system, but we are looking into adding one to our table for this job. Do you guys recommend a standard vacuum table with a spill board or some sort of pod clamping system? Any recommendations on where to purchase an aftermarket vacuum table or vacuum clamping system?
From contributor O:
I got a 20hp vacuum setup. Hooked it up and turned it on once. Then decided it was too loud. LOL. I'm glad to have it, but it's not necessary. Then again, I've never had to cut 700 sheets of ply.
From contributor A:
I assume you are a sign shop and need to cut these out of wood. While I applaud your desire to do this yourself, I don't know if it is worth your while unless you are going to get into wood stuff going forward. As you have already seen, the feeds and speeds are very different. The machine needed for the two are basically the same, but the setups are different. Hold down is different. For this, you would really need vacuum. If you have a t-slot table, you can get away with attaching the spoil board and screwing the material down. You can cut 4 sheets at a time, but you have to cut something like .60 for each sheet and remove the cutout. It would be better to onion skin and two pass it.
Call your tool manufacturer and ask them how to do it with the setup you have. Call the CNC manufacturer and ask them what you can do. Start with your original salesman. Also be aware you need a few woodworking tools that you might not have - sanders, chisels, etc. to clean up the parts as needed. If I were you and this was a one time deal with wood, I would outsource the job to a wood shop. Mark up each tree 5 bucks over the cost a woodshop will charge and make $3500.
From contributor W:
Contributor A makes a good point about setup being every bit (no pun intended) as important as the machine in this case. If your setup isn't right, you will suffer through this one and loose your !@#. If you're continuing to do this moving forward, then by all means, spend the jack and get set up for it. If not, have someone else cut it and don't take the unneeded risk.
From the original questioner:
The job is coming in this week. It sounds like I need to acquire a vacuum hold down system. Do you recommend the spill board approach or a pod type setup?
From contributor N:
You have the job coming in and you don't know how to run it? Well, you should have a vacuum pump installed for this application with the use of a spoilboard. You'll go through a learning curve on how to do this. If you figure out what the proper pump you need is and then order it, schedule your electrician, you'll have suction in about 3-6 weeks depending if they have to build a control panel. There's $10,000.00 to $17,000.00. This will give you enough time to design and build your vacuum table. Based on the original feed speeds you used to figure out what you are charging for the job, load/unload time, shop cleanup, etc., your run time on this job is about 6-8 weeks. These are the jobs that come flying into our shop followed by a frantic customer.
From the original questioner:
I appreciate your feedback, but how are you coming up with these numbers? It's hard to take your pricing and run time estimates seriously when there are so many variables that you do not know. For example, the size of our CNC bed? Access to electrician? How many shifts we run? How many days per week we operate? Size and scope of the project beyond the wood cutting portion of this project? Regardless... these things are not important. My original questions were not about pricing or business advice on whether or not it makes sense (or if it's even feasible) to try and purchase and install a vacuum system in time to use on this project.
What I am looking for is opinions on tools, cutting speeds. Spillboard hold down systems versus pod or jig type clamping systems. What would be helpful to hear is why you recommend one type of vacuum hold down system over another. I see some do-it-yourself vacuum clamping systems that are less than $500. Is anyone using something like this?
From contributor A:
We are only trying to help you. It appears you are entering a world of CNC that you know very little about. From what I can understand from the information given, you are about to lose a pile of money. However, I will try to answer your questions.
Bits - depends on how many sheets you are cutting. The Onsrud website has a cutting chart for speed and rpm. Without a vacuum, I would not recommend more than one sheet at a time. I would use a 3/8 compression bit. Depending on what your router can do, you run it as fast (ipm) and as slow (RPM) as you can and still get a good cut. Heat (from cutting friction) will break tools very fast. You're doing it right if right after the cutter stops spinning and you touch it, it's only warm, not hot. Hot is bad, and will lead to bit breakage.
How many to buy? A correctly set up machine should cut all the sheets with 2-4 bits. I would order 10 to be safe. If the machine is not set up correctly, you can break all 10 bits with the first 3 sheets.
Cutting speed and RPM. See the cutting test. I would start with something like 300 IPM and 15k RPM. I do the cutter touch test to see where I need to go from there. If you don't have a vacuum, you will need to onion skin or use tabs. Or slow the last pass considerably. Say something around 75 ipm to keep the material on the table. You need to decrease the lateral forces as much as you can.
I would only cut one sheet at a time. It is very hard to cut multiple sheets without using screws. If you can screw through the material or use thin brads, you can mechanically fasten. However, you will have to brad through the waste as well as the finished product to have this work.
For one sheet, full cut one sheet is the best. If you onion skin, first pass is something like .495, with the second pass .008.
I would clamp as stated in my previous post. Mechanically attach the spoilboard to the table and attach the material to the spoilboard with screws. I did this for a year before I got my vacuum.
From experience, this will not be an easy job. If you are not careful, you will lose piles of money. Your best bet is to outsource this to a wood shop with the correct CNC setup. But I've answered your questions to the best of my ability. I hope it helps you. I would like to know how the job turns out. If you can make it work, you stand to make a pile of money. This is one of those cherry jobs we are all looking for.
Contributor N, I purchased a 25hp FPZ in December of last year. I finally got it up and working 4 months later. Took 3 pumps before I got one that worked. The whole setup ran me approximately 15k for table, electrician, etc. My CNC was down for almost 3 weeks swapping out pumps. I would say the 3-6 week timeframe is optimistic, from my experience. But the numbers were right on for a pump that would work in this case.
From the original questioner:
So... what's your opinion on pod clamping systems?
From contributor C:
For this job I would use a full table vacuum system.
From the original questioner:
Is this recommendation because of the small size of the long and skinny branches that we need to cut... or other reasons? How small of a part can you hold down with a bleeder board type vacuum table?
From contributor C:
This is my preference in general, but for you I guess it depends on your table right now. As for how small of a part you can cut, it all depends on how you cut it and hold it down. I've cut plexi letters as small as 1/2" tall and 1/8" wide by using my vacuum and a small amount of contact cement on the spoilboard and the plexi.
Plus for the tree you'd need a 4x8 pod anyway, so why not vacuum the whole table? What type of vacuum are you looking at?
From the original questioner:
Here is an update on the project. The job is complete and it ran smoothly without any problems at all. In fact, it ran much faster and easier than we had anticipated. Just before starting the job, the customer increased the project size to 1,050 units.
We cut the project out of 1/2" MDO plywood that was supplied by the customer. We spent a couple of days doing tests with different router bits. We tested both 1/4" and 3/8" solid carbide compressions bits and a 3/8" straight end mill. We experimented with different cutting speeds and ended up running the job at 500 inches per minute. We really did not see much difference in edge quality between the different bits, so we ended up using a 3/8" solid carbide end mill instead of the compression bits.
We do not have a vacuum table, so we ended up using a drywall screw in each corner of the sheet to hold it down. The total investment for the box of screws was about $3. We abandoned the idea of trying to cut multiple stacked sheets and ended up cutting a single sheet with a single pass. We did the first couple of tests with bridges, but we discovered that we really did not need any bridges at all.
We ended up cutting 14 different variations of the profile. Some of them took longer than others. We averaged 10 to 12 units per hour with a single operator. We ran two 8 hour shifts per day Monday through Friday.
Some of you guys had me a little concerned with your comments... which I still do not understand, because this job was a piece of cake to run. The customer increased the size of the job by more than 40% and it still took less than two weeks to complete it. Thanks for everyone's suggestions, feedback and advice.
From contributor E:
I'm glad all went well for this job. How did you keep the part that was being cut out from vibrating or moving as you were machining, especially in the thin areas?
From the original questioner:
Surprisingly, we only had the vibrating issue on a few of the designs, but it really was never an issue. When we noticed a vibrating problem, I was able to eliminate most of it by moving the start position to a different location. We only secured the sheet to the table, but not the part being cut.
From contributor S:
I admire you. An outside of the box thinker can go a long way. I really like the $3 box of screws. In your position, I probably would have rigged pins to keep the sheets secure and use a 3/8 downcut bit.