Drying with Moderate Heat
Here's info on how various types of wood will respond to conditions in a home-built drying room that doesn't get much warmer than 120°F. There's a useful lecture here on how case-hardening occurs. May 16, 2008
Question
I have built a shed on a cement slab, 16' x 24'. It is insulated and sheeted with OSB on the inside. It has a woodstove 4' from the end with a 4' fan behind the stove. If I let the fire rip, it can reach 102 degrees, but if I damper it down, it cruises at about 85 - 90. There is no dehumidifier, but I would like some advice on all aspects of my plan. I just can't spend much more money on this because my wife will make me sleep in it if I do. This has been in use for 3 weeks and I don't start a fire every day, but that is because I am not in a big hurry. This wood is maple, alder and hemlock for my own use in my wood shop; I don't have any interest in drying wood for others. I will be making my own cabinets and moulding for houses that I build to sell and also small diameter alder logs for log furniture. Any input on this primitive system would be great. I live in the great Northwest and our weather is somewhat mild compared to other parts of the country.
Forum Responses
(Sawing and Drying Forum)
From contributor L:
I'm in the NW also and from what I've been told, an attic is a good place for small amounts of wood to get dry. I'm not an expert on much of anything, but it's my understanding for small projects the main advantage of drying at a high temp is to set the sap and to kill any bugs that might be in the wood. From what I can gather, a temp of 130 degrees is needed for several days to do both. I don't think (I hope) my attic gets that hot.
I think a person has to strap hemlock pretty good or it will want to twist just a little.
From the original questioner:
Thanks. I am not trying to dry wood for others, but I am trying to dry a lot more than I would ever want to carry up into an attic. I will post a picture of items I have built from wood that I harvested on my 10 acres sawed with my B20 mill and dried over the winter on shelves in my woodstove heated wood shop. My new drying shed is 16 x 24, and it can hold a lot of wood and the MC is dropping 1-2% each day according to my Wagner meter. I just don't know what kind of quality I will end up with.
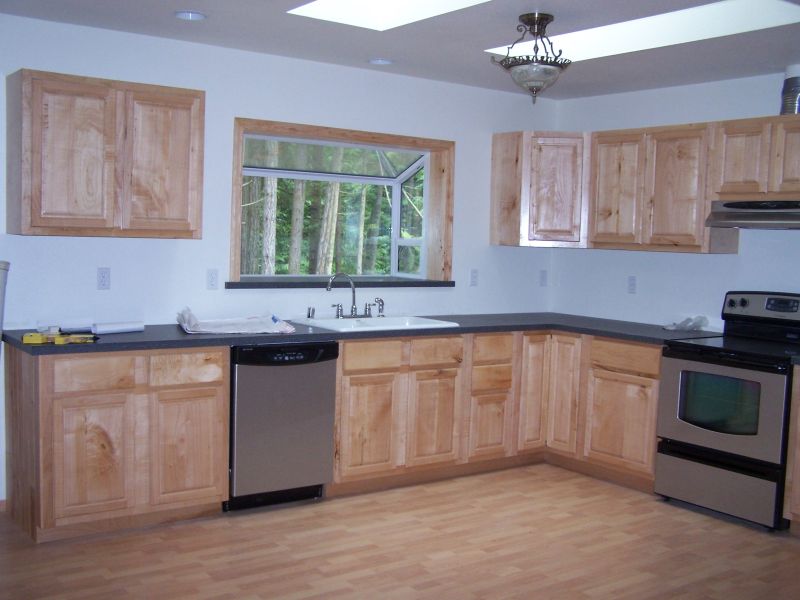
Click here for higher quality, full size image
From contributor T:
Forgive me for chiming in here - it's just that I've considered similar setups and also have customers doing the same. I can (as pointed out) see some gaps in this type of setup. I'm curious if the sapwood of your local maple specie will remain white or turn gray when drying at such a slow rate?
Also, if the end result of your method gets the moisture content low enough, would a small separate kiln that is capable of setting the sap and killing the insects (finishing the job) be practical for your operation (i.e., would the throughput be fast enough to be practical for your needs)?
From the original questioner:
The maple in the cabinets above was cut and sawed by me, then it was stacked in my heated shop for a year before I ran it through the jointer and planer. I don't have any discolor at all and there doesn't seem to be any pitch or bug problems either. One of the things I want to know is, can I damage my wood with too dry air, and when do I try to bring it up to sterile temp? Before it is dry or when the MC is way down? I have the option of putting a 4000 watt electric heater in the shed for a while.
From Professor Gene Wengert, forum technical advisor:
Wood will dry whenever the EMC of the air (related to RH) is lower than the MC of the wood. Temperature makes the wood dry faster and in a closed system will also lower the EMC. For quality drying we control the temperature and EMC (or RH) to within narrow limits. Drying outside these limits may reduce the dry lumber quality, but not in all cases. For this reason, you will be able to dry some wood at high quality in an uncontrolled condition. The acceptable limits from a quality standpoint are very wide if the MC is under 30% MC and the lumber is 8/4 or less. Often slow drying (which means higher RH) above 30% MC will produce high quality, except for color.
From contributor S:
Your drying setup sounds okay if you are not in a hurry. The lumber closest to the heat source might get dried sooner than the rest. But here's an idea. Build a cheapo sheet metal enclosure around the woodstove. You could use metal roofing or maybe get a quote from a ductwork guy. Anyway, trap the heat in the enclosure, round up an old furnace blower and then use flexible heating duct to distribute the heat evenly. You could try adding some home dehumidifiers to the setup, but they might not last long if you are drying oak. Also get some more fans and try blowing air through the pile, not just from behind the stove. If you can pick up that airflow, you can speed things up somewhat.
From the original questioner:
Thank you. Can I cause case hardening with too much heat? And at what point in the drying process do I raise the heat to sterilize the wood and set the pitch? The only wood available to me is alder, maple, hemlock, doug fir and western red cedar. I only seem to see pitch in the fir and I don't dry it very often, only if I get my hands on some old growth.
From contributor S:
I'm no expert, but from what I can remember, case hardening occurs when you dry the lumber too quickly, especially at the early stages. If you are air drying your lumber first and then keep the kiln drying rate from going too high, too fast, you should be okay. As far as setting the sap, I think you have to get the temp up pretty high, like 180 or so, for 24 hours after the lumber is kiln dried. So if your kiln setup won't go that high, I don't know what else you can do.
From Professor Gene Wengert, forum technical advisor:
It is virtually impossible to prevent casehardening when drying lumber in a kiln starting at fairly high MCs. Casehardening, which is not that the shell is harder than the core, but instead refers to a stress situation, may be slight when air drying as it is relieved with high RH. Likewise in solar drying. Otherwise, you will have casehardening. However, it may be slight enough to not cause much problem, or you may not be doing much remanufacturing.
Casehardening develops very early in drying and results from the outside shell trying to shrink normally, but the shrinkage is restrained by the wet inside, which is not shrinking. As a result, the outside actually dries to a larger size than if it had been free to shrink. The core subsequently dries and is able to shrink more. So at the end of drying, you have a stress situation... The shell is in compression and the core is in tension. This stress pattern is called casehardening. In general, the faster you dry, the more casehardening you get. We usually set the pitch in softwoods at the end of drying at 160 F. In your case, this is hemlock, doug fir and western red cedar. There is no pitch in alder and maple.
Note that for softwoods, especially the three you are drying, the final MC is 10% to 12% MC. Drier wood becomes too brittle and this cannot be easily reversed. This means that you probably should never go under 50% RH. You will find that this high RH will not be achieved if you add much heat. For maple and alder, we need to dry fast to keep the white color of maple. (Read 'Drying Hardwood Lumber' for more info.) For maple, we need about 6.5% MC final. For the alder logs for furniture, you probably want about 10% MC, unless they are for interior use. So, you cannot mix all the species together. Further, hemlock has sinker stock which may take twice as long as D-F to dry. It is tricky to prevent the D-F from overdrying and still dry the hemlock.
In short, there is more to drying than just removing water. This is why we do not mix species and we carefully control the drying conditions... temperature, RH and air flow.
From the original questioner:
Thank you very much - that was completely helpful and exactly what I was hoping to learn.