Efficiently Ripping a Straight Edge on Rough Stock
A spirited discussion on jigs, equipment, and how investing in the right machinery can make you money. February 27, 2015
Question
Is there any efficient, yet accurate way to rip a good edge on 4/4 rough stock? Typically I will screw an eight foot piece of 1/2 plywood strip to the worse side of the board.
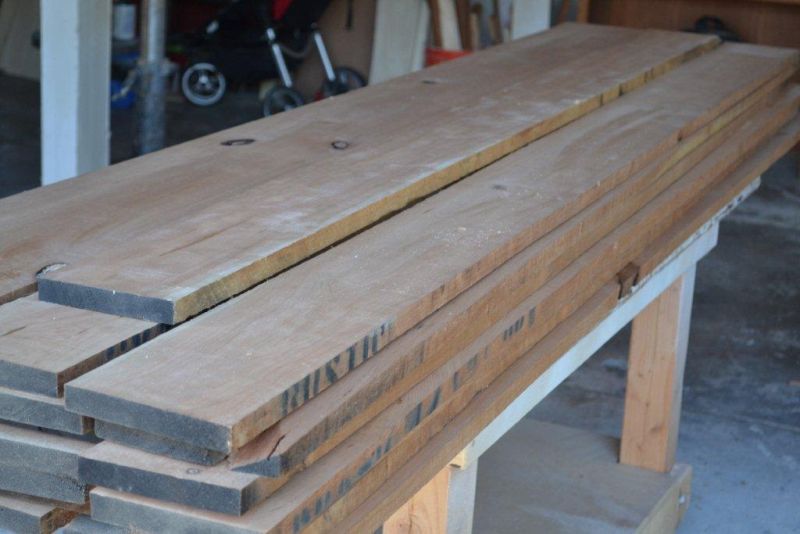
Click here for higher quality, full size image
Forum Responses
(Cabinetmaking Forum)
From Contributor Z:
I keep a straight line jig for my Unisaw shown in the Knowledge Base link below. The jig rides in a miter slot. I still have and use it but you would need to make one a little longer.
Straight-Line Ripping on a Bandmill or Table Saw
From contributor X:
Doesn't your hardwood supplier offer a straight line rip? All of my suppliers do and it's so cheap it's not worth my time messing with even a 10' slider. Sometimes the edges aren't pretty, but they are straight and give you something to work off of.
From Contributor L:
For very small shops any of the above or a large jointer should work. If you reach the point of ripping a few 100 board feet a day a SL rip saw really makes a difference. You can achieve big time savings because you can glue your panels right off the saw. I didn't realize how much more efficient they were and had delayed buying one too long.
From contributor G:
We use our sliding table-saw to strait rip up to ten feet longer than that we use a
Festool TS75 track saw. The track saw is not a bad option and it has other uses in a small shop or onsite.
From contributor P:
I second the
Festool method. Definitely need the bigger saw (TS75) for ripping hardwood. I have the 106" track, but have tied multiple tracks together for longer boards.
From contributor R:
We use a straight board, toggle clamps and run the edge of the straight board along the uni-fence. We also use this to make tapered boards when we need them.
From contributor C:
Like Contributor X I get mine straight line ripped from my supplier but have used my vertical panel saw to straight line up to about 12' lumber.
From contributor H:
You can do it with a power feeder and a straight piece of plywood. Glue a piece of old sanding belt to the bottom of the plywood which will provide grip between the parts when feeding.
From contributor D:
Jointer anyone? All stock needs to be flattened so straight line while already standing at the jointer. I get the best yield out of my stock as humanly possible with the way I process. The best method/machine depends on if you are making
cabinet doors or moulding. For moulding all day strait line gang rip is best. Contributor H I think that sounds like a recipe for an accident.
From contributor H:
Contributor D that method is so slick, although I have not others doing it. You lay the straight plywood on top of your part to be straight lined. The plywood rides against a fence set high over the blade (the blade is completely covered) and the power feeder sends both through the saw cutting the board under and not the top plywood. Not as fast as a SLR but better than most methods used in small shops. You can see exactly where the blade will cut before you send it through the saw and safe because you and your fingers are not anywhere near the blade. Kickback is not an issue because you are only cutting off the edge so no stress. This method can be used with a riving knife as well.
From Contributor O:
Man, I'm getting old. Straightening lumber is so basic as to be second nature. Small shops do it with a joiner, since all stock must be faced and edged (straightened) before anything else, right? Larger shops do it with a SLR - Straight Line Ripsaw. Get yourself to IWF in Atlanta to see how many ways this is done. Toggle clamps? Sanding belt glued to plywood?
Festool? How much money have you guys spent with such methods? I mean no disrespect, but if you add up the hours, I would guarantee that you already have spent the money for better equipment, you just don't have it.
From Contributor L:
Contributor O I couldn't agree more. I would guarantee that you already have spent the money for better equipment, you just don't have it. I suspect one of the reasons we see this so much in the US is the lack of education/exposure to the trade. I lived in Europe for a while and the small shops there were much better equipped to do whatever their line was. They have a much better training system. School systems here treat the trades as second rate. Wood shop classes are taught by people with little or no practical experience. Methods and equipment are 50 years behind.
From contributor B:
What is the purpose of the edge is it to be glued up?
From contributor Y:
Panels and drawer fronts.
From contributor B:
In my opinion if you are making doors and using anything other than a SLR saw you should buy doors. A good SLR is magic, the glue line is better than you can get out of a jointer.
From Contributor L:
Contributor B I totally agree.
From Contributor O:
I will be the first to tell you I don't know it all, and am far from perfect, but here is how I would justify the cost of machinery: Let's say I could save two hours a week by changing from whatever method I was doing to a more cost-efficient method. That would be 100 hours a year. Let's say my shop rate is $75.00 per hour - the rate I would charge for a job that is just labor. The two hours I would save with better machinery would allow me to make $7,500 more per year. Often five years is considered a good payback period. That is $37,500!! That is what it costs to use screws and plywood, or toggle clamps, or whatever. You are paying it every time you do that. Instead of screwing around with crap, you would have a machine to do the mundane idiot work, freeing you up to improve skills, learn to carve, sell, drink or do whatever! Also the rippings make good tomato stakes for you and your neighbors, and the sawdust, once it is aged, makes the best tree mulch there is. It is all good, as they say.
From contributor R:
Yes a machine is nice. You need the space, the money and probably 3 phase. It takes very little time to jig SL boards as you need them. Half the stuff from the supplier is not that great, and if is sits a while it gets a hook.
From Contributor O:
If the boards develop a hook after you straighten them, they are not dried properly and will cause problems for you later while in service. Properly dried lumber does not move except in response to changes in moisture content via relative humidity. Three phase comes easily from a phase generator, either electronic or mechanical. They work very well, and are safe, efficient and easy to use. They 'pay their way' like the rest of the machinery. The money makes itself, you just need to get out ahead of the curve a bit to afford the machine leasing is a good way to get serious about your career. If you stay in the dragon chasing tail mode, you will never thrive and always have a 'job' rather than a professional career.
Space can be a problem, but that is also solvable. If one looks at their daily work as a profession instead of a "cabinet shop", then the picture can paint itself as a more viable enterprise, with a real location and presence. The real problem is how we hamstring ourselves rather than accentuate our positives and build on that. Finding more and more reasons to say no instead of making a situation that strongly states a yes. We are often our own worst enemy.
From contributor P:
The
Festool method beats a jointer in a few ways. First, it can be done in one pass. Second, you can easily visualize and remove the imperfections on the edge. Third, it takes less skill than using a jointer to perform. Don't knock it unless you've tried it. Yes, you still need a jointer for the face, but he didn't ask about that.
Editor's Note: To find all manner of lumber, hardwoods, exotic wood, and plywoods, check Steve Wall Lumber, a trusted supplier.