Fabricating Radius and Curved Mouldings
Here's a detailed discussion comparing two approaches to creating curved and arched mouldings: the CNC route, or the dedicated moulder and shaper setup (which may involve templates). July 13, 2010
Question
I'm looking to add to our production capabilities by adding radius/arched moulding. I don't have the knowledge to produce these. I'm looking at a purchasing a Williams and Hussey moulder. I'm really in need of some info to learn how to make these. Can anyone help?
Forum Responses
(Architectural Woodworking Forum)
From contributor Q:
That is a good place to start. You will have to add a circle and arch jig that W&H or CG Schmidt sells. I do arched work all of the time. I am sure there is more than one way to do it. I make a template for each window. Then I attach wood to the template. I rough cut the wood along the template with a bandsaw. Then I flush cut to the template with a shaper. Then the blank is ready for the moulder.
I use plywood for the template. I nail it to the casing while I route the bottom of the template by following the casing with a flush trim bit. Then take the template down and then route a 3/16" rabbit one the template then use a flush trim bit to remove the lip. That gives you the bottom of the template with a 3/16 reveal. Then I just mark out with a layout gauge the width of the moulding. I just cut that on a bandsaw and edge sand up to the line. When the temp is complete I just start cutting lumber at whatever angle I need to keep the wood over the template. Once I have the pieces cut I glue the ends together until I have a solid ring. I screw that to the template with DW screws. That is about it.
From contributor D:
We do a lot of radius work with the W&H. We do the same as the first response does but we use MDF for templates. Also you want to join the wood with biscuits or dominos. We use pinch dogs to hold the joints together as glue dries. The most time consuming part is making the template. Don’t rush it though.
From contributor L:
We use an arched molding shaper – Stegherr. No template needed. It tracks the shape you put in. It has enough power and feed grip to cut the moldings in one pass. We make the blanks by ripping thin strips on a SL rip saw; keep them in order with a V mark. Glue them up on an adjustable form. We offer finger joined solid segmented curves but most people opt for the laminated. There is more time in the finger joined moldings. Three point curves can be done on the laminating jig if not too radical. When they exceed the forms capabilities we go to male/female forms cut on the router and glue them on the clamp rack (expensive). We also make curved crown moldings using a heavy tilt shaper and templates and tracks made on our Komo router, this process is time consuming with all the glue up. Shaping goes quickly. We've also done them on the CNC router but it takes a lot of router time to make all the passes and there is still sanding. The shaper is quicker. The CNC cut templates are quick to program, much quicker than all the steps in the router cut moldings. US Concepts makes a solid molding shaper, pricey new. Their bigger model can run big heavy moldings. We have to run curved bar rail on the CNC making it expensive. You can run a lot of nested sheets for case parts in the time it takes to make one curved molding on the router. It would be much quicker with a four or five axis router and horizontal aggregate.
From contributor Y:
I have to disagree on the time needed to do arched moldings on the CNC router. I have three customers doing them this way now and they are all saving time over their previous methods. Depending on the molding, it can be one roughing pass on one side, two roughing passes on the other side, then one or two shaping passes. That may be more passes than a shaper, but the quality is much higher and only requires a light sanding to remove knife marks. There is no need for using the band saw, and there are no templates to be made.
From contributor L:
Sorry but I have to disagree on several points with contributor Y. Let’s assume the arched moldings are the typical window casings, nothing exotic. The prep of the blank has to be the same: rip, glue on adjustable form to the correct shape. We flatten and thickness with a coarse belt on the wide belt. This is similar to what contributor Y is saying for roughing on one side using the CNC. Next we select from over a 100 casing profiles or make a new one and set the head up. It's the same set of knives that we will have run all the lineal trim with on the Weinig molder. Slide the head on the Stegherr, set the depth. Push green button feed blank in. Machine automatically tracks whatever shape the blank is. Quality of cut is very good and no sanding to get rid of tooling lines is needed.
If several moldings of the same pattern but different radii are needed just feed one after the other, no change in setup is required, no programming, one pass. We’ve run casings 16’ long, no different than 4’ long! Cut quality is equal to the Weinig moldings. I've never used a W&H but I think there is considerably more time in running a molding on it than on the Stegherr. There are five driven feed rollers on the Stegherr, all feeding in the correct direction. The W&H’s two feed rollers are always trying to push a curved molding straight through. Depending on the molding, the 2hp can require additional passes on the W&H, with a loss in feed contact.
While we can and do produce curved moldings on the Komo, it takes more time for all the passes, programming, fastening the blank and sanding out the tooling lines. The smaller you make the set over for each pass the less sanding and the more run time on an expensive machine. Having made 100's if not 1000's of curved moldings we've got a good idea of the cost. If you are only doing an occasional curved casing and can't justify an arch shaper then next best is the CNC. The CNC does have one big advantage for those not having a molder, tooling. For the price of a handful of router bits you can make most any profile.
From contributor Y:
I've never seen the Steg-herr in operation, but I know the company makes some very high-quality, innovative machines. After re-reading your original post, I'll revise my stance. My understanding was that you had to make these forms you speak of, but after re-reading, it sounds like they are standard, flexible forms. I'm unclear on how it "tracks the shape you put in". Does that mean the shape of the part has to be near perfect, i.e. better than a band-sawed shape? In other words, does it follow the part with a copy bearing?
For those who have access to a CNC router already, I still stand by our method. You glue up your rough part, screw it to an MDF spoilboard, and program your toolpath. That's pretty simple.
You are talking about 100 different casing profiles. If that is the requirement, I think you are way ahead with the Steg-herr. I deal with companies doing only a few different arched crown moldings. For that requirement, I think our method is better. These parts can be 6" thick and the rough part can weigh hundreds of pounds. You don't want to be pushing that through a manual machine. Going back to the original post, he only says "radiused/arched moldings". I guess we need to understand what he meant to give the best answer.
From contributor M:
In our radius work we utilize a Mikron moulder, WH moulder occasionally, shapers, and a CNC router. Unless your CNC router has a horizontal "c" axis moulder head that accepts standard moulder tooling, which most don't, you are forced to "3d" your profile. Although we have had to do this many times, it is not our preferred method by any means. There is no step in the CNC process mentioned that comes close to being more efficient than contributor L's description if you have the proper machinery at your disposal.
I think there are two different genres coming to the table here. We are a millwork shop, producing our own in house tooling and are in the business of producing architectural wood mouldings and have all the machinery to support it. You run the straight moulding on a moulder, utilize the exact same tooling to produce the radius. The flip side of that is a cabinet or CNC job shop that perhaps doesn't have access or the desire to create high speed tooling. Then his method undoubtedly will be to use his CNC router solely, and can do so effectively.
That all being said, a guy starting out can invest in a WH moulder, bandsaw, and some other small tools and start producing simple radius mouldings far easier than a CNC router with a large learning curve in my opinion.
From contributor L:
A photo is worth a few words! Arch clamp rack with two parts being clamped, works quite well! There is a swing arm and pivot for making true radius setups. Next photo: Stegherr, you can see the feeding rollers left and righ. of the molder head. Red and blue wheels are mounted on swing arms and powered from below through chain drives. There is also a powered wheel directly behind the molder head. In front of the molder head are two small pneumatically loaded bearings that serve to clamp the work against the back feed roller and there are two spring loaded vertical rollers. The total number of powered feed wheels - 5, Idler rollers - 6. Swing arms - 2. The US Concepts machine is very similar but with some improvements. In spite of what looks complicated it is easy to setup.
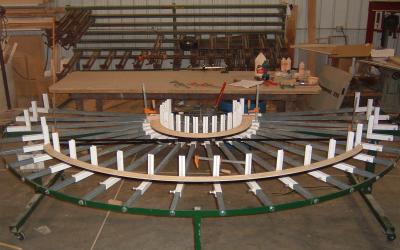
Click here for higher quality, full size image
This is the operating area of the Stegherr arch shaper.
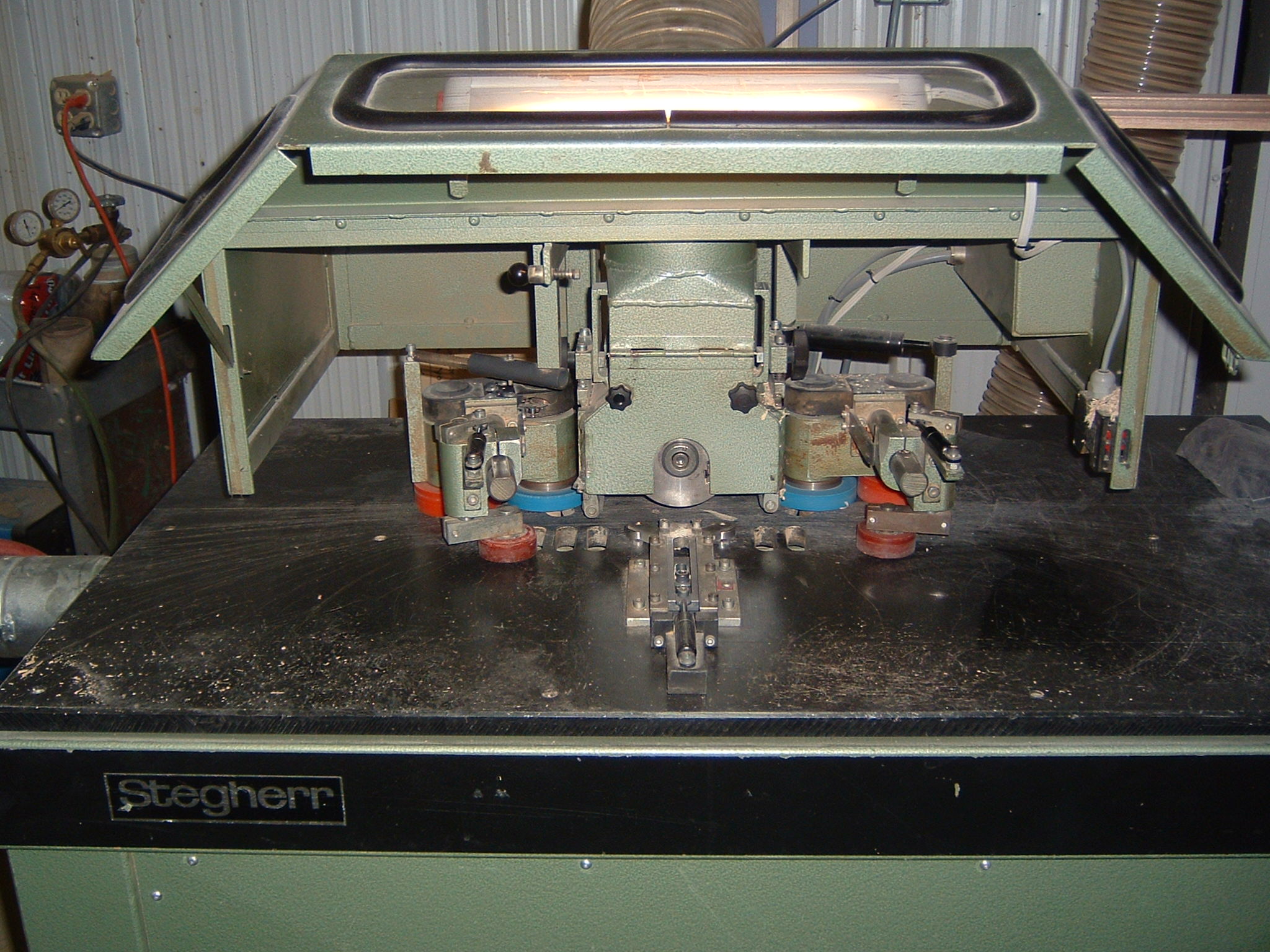
Click here for higher quality, full size image
From contributor A:
The W&H is obviously a good move. He doesn't need the rest until he's making curved stuff on a large scale. Spend the extra cash up front and buy the variable speed.
From contributor L:
Contributor Y: in Answer to your question "I'm unclear on how it tracks the shape you put in" - does that mean the shape of the part has to be near perfect, i.e. better than a band-sawed shape? In other words, does it follow the part with a copy bearing? “Why would you want to make your blanks not "near perfect”? As you can see in the photos there is no reason to use a band saw. The strips come off the S. L. Rip ready to glue.
Sometimes a strip or two will need to be made slightly thicker or thinner to end up right on for molding width, easy, set the fence over a 32nd. The clamp uses 3/4" steel banding for pressure, plenty of pressure! Like contributor M said, I think we are talking about two entirely different businesses here. One that does a few arched moldings a month and another that makes a business out of supplying complete molding/millwork packages. If the guys running a W&H don't have profile grinding capabilities they have a time cost in addition to the additional time costs associated with the slow, often multi pass W&H.
It’s a good little machine if you only need an occasional molding and don't have to constantly match designers profile ideas. He didn't give any clue about what he meant by "add to our production capabilities." If he is already running a molder and profile grinder then he should consider a more productive set of equipment for arched moldings. If he is only planning a few moldings a month then go cheap on machines expensive on time.
From contributor N:
To contributor L: what kind of form do use when gluing elliptical? What number of arches, jambs, curved crown, and base per week would the rest of you consider high production?
From contributor L:
Depends on the variance from true radius. Most of the time we end up having to make male/female molds from P Bd. and clamp them up on the clamp rack. If the shape allows enough pressure to be done over the entire blank we will do them on the adjustable rack. Right now the guys are making 24 - 1 3/4" square, curved blanks that will be run into moldings for a church. Contractor waited till the last minute to order them so we didn't have time to glue them up two at a time on the adjustable form and made five male/female molds out of P Bd. on the router. The M/F molds work well as long as one part is very stiff and the other slightly flexible. We've made moldings with curves in both directions (S) using these forms. Can be a Chinese fire drill getting all the strips in those molds when the bends are fairly tight. The Stegherr will track an S curve just as well as a radius or three point curve. The same type of mold is made for solid surface curves.