Feed Rates and Speeds for Scribing Metal-and-Plastic Composite
CNC owners offer advice for engraving letters in an unusual composite panel (metal laminated to plastic). December 31, 2012
Question
I just purchased Amana's "In-Groove CNC insert engraving system" and am trying to engrave a name on a plate using the 30 degree V bit. I am running it at the recommended 142 inches/min at 18,000 rpm but still get burning on the piece. I don't have a lot of pieces to practice on, so I could use some help on recommendations. I am going to go in today and try to use a slower setting. The piece I am cutting is around 3mm thick plastic with a thin layer of metal on top and I am only going in about 0.1mm.
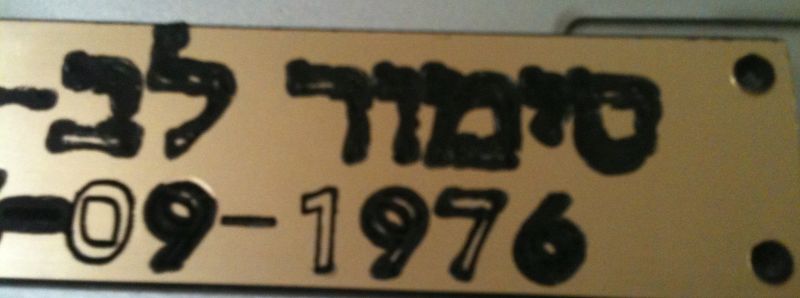
Click here for higher quality, full size image
Forum Responses
(CNC Forum)
From contributor D:
Only suggestion I can offer is try to separately machine a thin metal sheet screwed down to a block of wood and a plastic sheet alone, and then glue them together with contact cement. Every time I've cut aluminum it gets hot and is a fire hazard - much hotter than just hot enough to melt plastic.
From contributor H:
18,000 rpm’s are too high. We recommend about 14,000 for our tools. Plastic is a tough material to cut. You have to make the tool take a good chip because that is what carries the heat away from the tool.
From contributor P:
Try decreasing your spindle speed to 12,500-13,500 and increasing your feed rate to about 250-300 inches/minute and take a bigger bite to keep the bit cooled down as the previously mentioned. Sometimes these bits are designed to cool themselves down as they run.
From contributor V:
I just looked at that feed speed/rpm for that tool on Amana’s website and I see a difference to what you are saying, are you going .1mm deep or .01" deep?
From contributor R:
If it’s an ACM material like Nudo cut it as fast as your machine allows while still getting a good finish. We cut it every day and it cuts like butter. I think this is one of those times where tooling manufacturers haven't done enough testing to have baseline charts.
From contributor W:
That’s way too fast. I cut at 10,000 or less and it’s as fast a feed as I can go.
From contributor K:
Slow down the rpm’s and if you’re going to be doing a lot of this type of work get yourself a cold air gun. We use a vortex mounted onto the spindle housing with a flexible segmented hose and nozzle allowing the cold air to get right at the cutting zone. It really does work well. We have used the in-groove system and had mixed results. I’m not convinced it's that good of a product.
From contributor W:
I have the In-Groove as well. I recently switched to Southeast Tools engraving bits.
From contributor K:
You switched from the In-Groove to Southeast, what is your feedback on the In-Groove tools?
From contributor W:
It is one of those things were one came loose and I just never tried it again. I have a bunch of other end tips and may try one more time.
From the original questioner:
I ran the program again. I kept the rpm’s at 18,000 but slowed the speed down to 57 inches/min and it worked great.