Finishing a Walnut Slab Tabletop
Finishers talk about Tung oil and linseed oil. March 26, 2009
Question
What is the best way to finish a walnut slab for a restaurant table? I want the most natural finish with the least plastic type finish, but it must last to the abuse of a popular restaurant/bar scene. The final finish would ideally look like the attached photo.
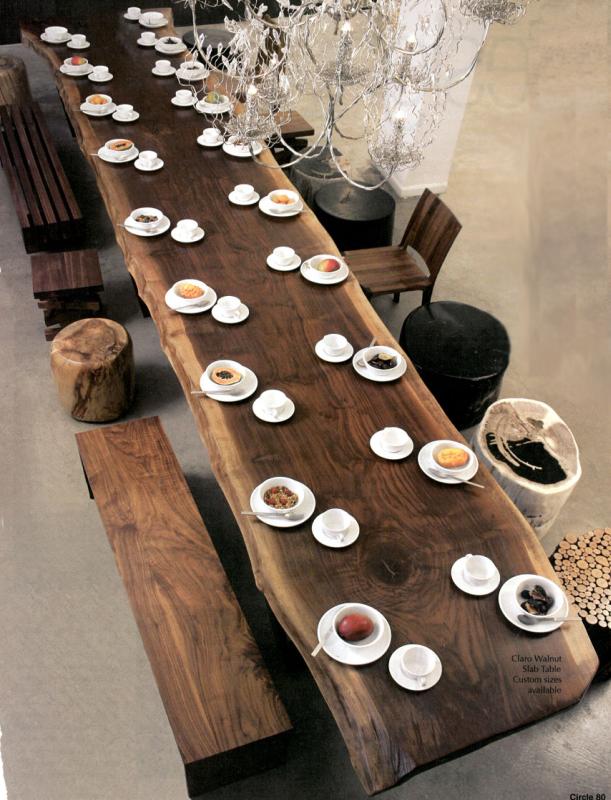
Click here for higher quality, full size image
Forum Responses
(Finishing Forum)
From contributor B:
Wow - what a hunk of walnut. Too bad they couldn't afford to get chairs! The finish looks to me like regular old-fashioned oil finish, like I used to do often. Sand to 220, wipe on slightly thinned boiled linseed oil; wipe clean after a few minutes, then let dry for several days. Clean, and apply a mixture of the lin. oil and satin or flat polyurethane varnish with mineral spirits thinner, and wipe off after a few minutes. Dry for a couple of days, scuff sand with 320 or 4/0 steel wool, and wipe on another coat of the mixture and repeat. I'd do this for about a total of four or five coats, rub down with steel wool, and then use it. Clean and apply thinned down mixture every week or two.
Some people prefer tung oil over linseed-supposed to be harder and more durable, but I think there's nothing like the look of lin. oil on walnut.
Obviously, this method takes a lot of time, but it's easy and almost foolproof (unless you leave unwiped oil on the surface which will get gummy). When allowed to dry, the oil will oxidize in the surface and the molecules will cross-link, making a tough, resistant gorgeous finish.
From contributor R:
Just curious but is tung oil or linseed oil rated for food contact? Also, during the most humid times isn't there the chance that during one of the maintenance coats that it may not be completely dry by opening time thus possibly risking ingestion or staining a customer’s clothing? Not trying to detract from either finish. Both are gorgeous when set, especially on walnut, and I’m just asking and also bringing up a point that I am not clear on. I know I don't have the many years of experience some of the other members have in finishing that is why I am asking, although it would seem to me you would want something that wouldn't risk a call back or worse, trusting to the upkeep to the owners.
Natural aside, in this case I would be more inclined to use something along the lines of a low luster lacquer but will be non toxic and durable when dry - possibly Target's Emtech 6000. I am not positive as to food contact I would call or e-mail the mfg before using it but it would definitely give you a durable finish that you shouldn’t have to worry about and is easily repaired in the field should it be damaged and if you rub it out to a low luster you can achieve that hand rubbed look.
From contributor B:
I want to ask your opinions about the addition of the varnish and its effect on durability and hardness. Does that maybe put it into the tung-oil category? As for food safety - my wife and I take linseed oil (flaxseed oil) nutritional supplement-widely used; but of course it doesn't contain dryers and other additives. But once dry it should be inert, more or less like plastic, and food-safe.
A long time ago Bloomingdales settled a lawsuit from a customer whose books were stained by well-dried (so it seemed) lin. oil finish on shelves we made for them. I didn't believe it at first, until we saw our shelf with precisely imprinted raw impressions where the oil had been sucked out by what was sitting on it. I found out that the oil changes after standing around for a long time. It's then called "stand-oil" or "still-oil", and won't oxidize the same way. It’s an interesting and expensive way to find out.
From Paul Snyder, forum technical advisor:
The only thing I can tell about the finish in the photo is that it is a low sheen. I can't see if the pores are filled, semi-filled, or open to provide a clear idea of how thick or thin the finish actually is. When I enlarge the picture to its full size, there does seem to be a uniform light reflection from the bottom right corner and the jagged wood on the bottom left corner has some brighter areas of reflection on the corners. Both reflection patterns indicate there is some sort of finish on the table and it's a low sheen. Not much to go on.
On a scale of 1-10, with 10 being the most durable, linseed and tung oil rate a 1. One of these oils mixed with oil-base varnish (including
polyurethane) rate between 2-3, depending on the ratio. Shellac rates a 4. Lacquer rates a 5. Conversion varnish rates a 7. Catalyzed
polyurethane rates a 9. Durability inlcudes water resistance, heat resistance, abrasion resistance, and chemical resistance (e.g., cleaning products). A restaurant table will be exposed to extremes of all these factors.
If you want a durable finish that will last for a respectable amount of time in a commercial environment, you should use a catalyzed polyurethane. You do not have to apply a number of coats and build the finish to the maximum dry mils thickness. You can keep it thin enough for an open pore (aka "natural") appearance and still get respectable durability. But if you do build the finish, you will get the maximum durability. Done properly, you will achieve a full filled finish that looks and feels wonderful - not "plastic." Much like the table in the picture you posted. Done poorly, it will look like an amateur poured a bucket of something on the wood and let it dry out.
From contributor M:
To answer the question on a different note, most of the standard table-top durable finishes (like 2K poly) look fantastic and non-plastic so long as you stick with a satin or dull sheen. More than once I've sprayed cabinets with precat or CV and had customers ask me if we put on a hand-rubbed oil finish. You can easily get the same look from 2K poly for a lot less headache, a lot more durability. Personally I think 3 coats of 2K poly, sprayed normally at 3-5 wet mils, sanded well with 320, in dull or satin will look stupendous.