Flattening and Truing Big Matched Burls
A CNC is handy for dimensioning big, heavy awkward pieces accurately. But a shop-built router jig can also get it done. July 18, 2008
Question
I have these 2" thick, 101" L x 25" W nice book matched old growth mesquite slabs. My first thought is make a dining table, but they are so heavy I am wondering what the best way is to get one true inside edge. One slab is slightly bowed up in the center about half an inch. What can I do to straighten the left slab - clamps, pressure and get one true inside edge (straight edge and a circular saw?)? I am going to leave the natural outside edge and inlay the fissures.
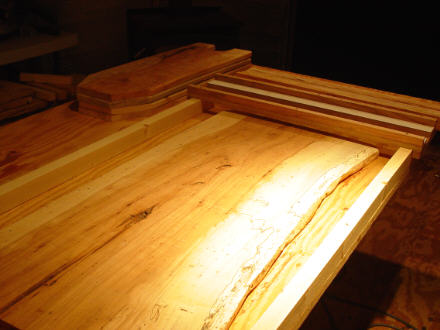
Click here for higher quality, full size image
Forum Responses
(WOODnetWORK Forum)
From contributor A:
Straight line rip to get the straight edges, use a widebelt sander or hand planes to smooth the surface. Probably best to get it smooth first, then straight line rip.
From the original questioner:
Thanks. Yes, I was thinking about using a 30 inch drum sander that a friend has since the slabs are just under 30 inches at the widest part, only I have never used one before. A 1.5 inch top would be fine with me. So would it be best to drum sand the concave side of the slab first, or alternate both sides till I get it down from 2" thick to 1.5" in thickness?
From contributor J:
I use a CNC machine for slabs like that - you can true an edge and flatten the surfaces. Makes working with huge pieces of wood much easier - you put them on the machine, do the work, then take them off - you don't have to carry the wood around the machine.
From contributor B:
If a CNC machine is out of the question, straight line rip the inside edges. Then find a router bit long enough to reach all the way through the width of the slabs. Set them up just a little closer together at all points than the width of the router bit. Clamp a straight edge so that the router will ride the straight edge and the bit will take at least something off the edge of each plank.
You can also flatten the whole thing with a router by setting up a fence on each side that just clears the highest point of the slabs and make a sled for your router that will slide back and forth over the entire area of the slab top. You will have to make several passes and you will wish you had the CNC machine, but you can do it this way with what you have (you may need to buy the router bit).
From contributor E:
If you're going to run the planks through a sander, you'll have to get one side flat first, otherwise you'll just end up with a sanded bowed top. I agree with contributor A - I know nobody really uses them anymore, but if you've got a couple of well tuned planes lying around, you could flatten that top fairly quickly. You could also do it with a belt sander, but I feel like I have better control with planes. You just need to get one side fairly flat, then you can flip it and run through the sander to flatten the other side. Once it's flat you'll have a much easier time of getting a clean straight edge.
From the original questioner:
Thanks. When I was thinking of how the CNC would work, I remembered an article from American Woodworker where a guy was flattening a huge elm slab and he made that sled with 2x4's and used his router with a wide bit. I believe I will do that.
From contributor K:
I use a Makita 6 3/4" power planer for work like this that is too big to run on even a big jointer. I go at it just like I would if I were doing it with hand planes, only with a blade that wide, and capable of cutting 2 mm deep with no problem, saves a lot of work. The front knob is the depth adjustment, so changing depth on the fly is easy. Unlike a jointer where you would work the concave side, I like to knock the high parts down on the convex side. Set it up on a table to work at a comfortable height, and use some winding sticks to sight down for twist. It only takes a few minutes to flatten work like this good enough to go through a thickness planer.
From contributor G:
I'm with contributor J. We use our CNC. Shim the piece for balance and mill off only what you need to make one side flat. Flip it over and mill the other side. We made a mantel top, maple 12/4 thick, 20" wide 11' long, 2 pieces glued up, net after milling was 2 3/4" thick and level.
From contributor M:
In the past with mesquite a little smaller than this with a bow, I simply stickered it flat in the barn with a lot of weight on top and it straightened itself out after a week or so depending on weather. If what I have read is true, mesquite is the world's most stable wood due to the tangential and radial shrinkage being equal. Basically I think that means once you dry it flat, it will stay flat.
From the original questioner:
I finally went with contributor B's idea. I built a sled for my router using melamine faced plywood. I used a 3/4 inch straight bit. The edges of the sled where the router rests against have enough play to make a 3/4 inch cut on the first pass while using one edge and then sliding to the other edge and making another 3/4 pass for a total of a 1.5 inch pass before having to move the sled over. There was not a lot of light, so it is kind of hard to see in the picture, but there are 2 2x2's that the sled runs along for the length of the sled. The runners can be any height you need to accommodate thicker slabs, but I was able to get a flat side for my slabs using inexpensive scrap wood from the shop for the jig.
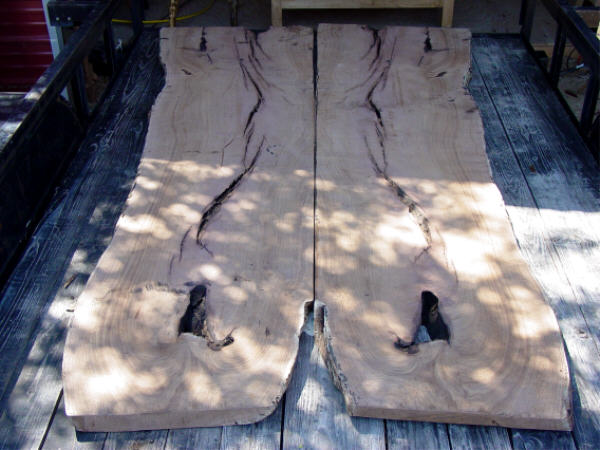
Click here for higher quality, full size image
From contributor Y:
Well done. I was cleaning the attic of my shop the other day and found the router sled that I built years ago for the same purpose - efficient, inexpensive, and it gets the job done.