Flipping a Heavy Table Top by Yourself
Other Versions
Spanish
French
Ideas for muscling around a heavy conference table top in a one-man shop. December 6, 2011
Question
I am a one man shop producing furniture pieces and have been asked to make a large table. How do I move and flip the top over by myself without injury? The current top is 40"x84"x2" walnut and weighs about 180 lbs.
Forum Responses
(Furniture Making Forum)
From contributor D:
Being a one man shop I understand the many tasks made easier and safer with someone on the other end. Sometimes you are just going to need a hand. Figure it into the heavy works for delivery as well. With blankets laid out I usually can handle most pieces, but every now and then I either have to invent some contraption or get help.
How you going to surface that 40" top? Sounds like a nice table.
From the original questioner:
I came across some beautiful 15" and wider 10' long x 2" thick walnut that I will do breadboard ends on. To surface I will do it the old fashion way, by hand. I find it is just as fast and a whole lot less dust that way. Plus I don't have to handle the piece as much, which goes back to my initial problem.
I am going to try and make a couple of A frames with a beam between them and use a couple of come-a-longs. Clamp a pivot piece to my work and lift and flip it in place. Cross your fingers for me!
From contributor M:
I was thinking about suggesting a lift like you are discussing. If you had room and strength in the ceiling above your work area, maybe attaching something to the ceiling instead of the A-frame. Would a pair of pulleys be less cumbersome than the come-a-longs? Looks like they would work since the top is only 180 lbs. If the center of the table would be 20", you will only have to get a little higher to roll it over. I was also thinking instead of the pivot piece, just make two large loops of rope that go completely around the top and up through the pulleys (one on each end). Once the top is 20+ inches above the work surface, as you roll it over, the ropes will roll with it through the pulleys. Might create a rope burn on the top edges, but padding could prevent that.
From contributor J:
If you have enough room, 3 sets of sawhorses will allow you to flip it easily. Table is on one set. When you need to flip, set it up so the edge of the board is in the center of the second set of sawhorses and have the third set on the other side. Now lift one edge so the table top is standing on edge in the middle set of sawhorses. Walk around while balancing it on edge, and lower the top on the last set of horses.
From contributor O:
I wouldn't exactly say flip it easily, but that would work. You are still muscling most of 180 pounds on edge solo. Check out the Flip Assist cart.
Hafele also sells a similar cart. I am thankful to not be in a one man shop anymore. It's always good to have other hands and eyes and ears around. Got any neighbors? A wife?
From contributor C:
Why not just flip it over? In addition to all kinds of woodworking, my business regularly fabricates concrete countertops. I try to keep our castings to less than 350 lbs per slab for ease of mobility.
An 84" x 26" x 2" slab of concrete can easily weigh 350 lb and I'm able to flip it up onto edge and let it down on the other face solo. That is a lot for me, but then I only weigh 145 lbs myself. Most of my slabs weigh less than 300 lbs.
I have to flip these things because they are cast good side down. I slide the slab until it's almost half off the table, along the long edge. Then you can get under it to press upwards (using your legs, not your back!) until you pop it vertical. It will have a little inertia, but the 2" edge is enough to keep it in check once it gets up there. Then I hop up on the table and get on the other side. It's comparatively easy to let it down from a standing position. I let it down onto blocks of 2" thick Styrofoam. This is a great way to store in-progress heavy slab material. It's easy to slide around, stands up to abuse, and will give before the work material does. I use the blue stuff.
From contributor F:
I am also a one man shop. I built a 50" X 10' cherry table and had the same challenge moving the top as well as presenting it for finishing. I built a rolling rack that allowed me access to both sides for finishing. The flipping mechanism in the ceiling requires a bit of explanation. I mounted axles in my ceiling and made straps from seat belt material. The straps could be joined using conveyor hinge. Believe it or not, the pin used to join the two ends of hinge was a plain old paper clip. With the fabric wrapped twice around the table the table could be flipped by myself. It hung the correct height to connect to the rolling dolly. Note two different adapters to hold the table. The back was screwed in (loosely in oversize holes). The attachment for the front was a felt padded piece that hooked the edges.
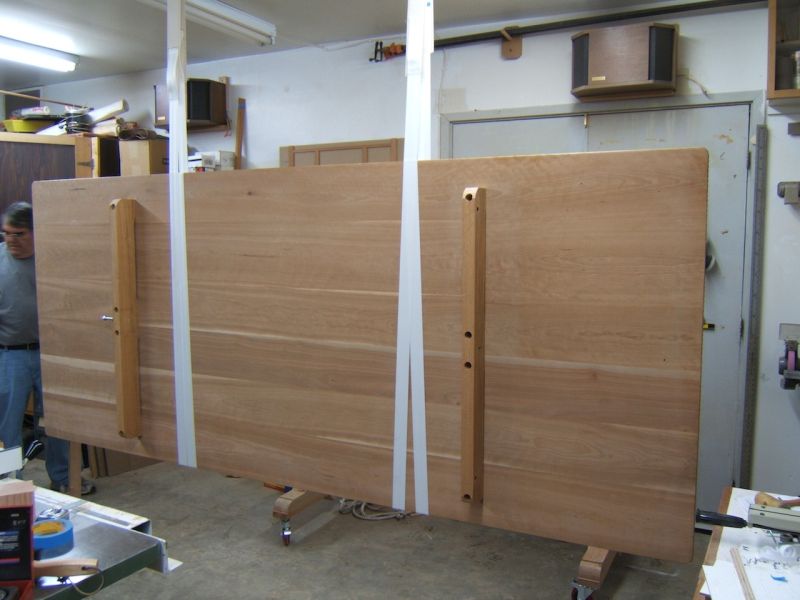
Click here for higher quality, full size image
From contributor S:
Ditto to what contributor C said. 2" foam and I'd be sliding that thing everywhere. I also buy packaging foam from U-Line and use a lot for padding in the shop. Use a sacrificial piece of wood for the edge of the table and tape it on and slide all around on edge. Stand it up on the table and slide right onto the cart.
Sometimes, the more you worry about damaging and the more things you do to prevent damage, the more bad things can happen. I say manhandle with caution.
From contributor H:
I had the same problem with a 90” walnut table I made. I am 40 and I just barely managed to flip it but it was heavy at 2” thick plus the solid oak extension rails and legs!
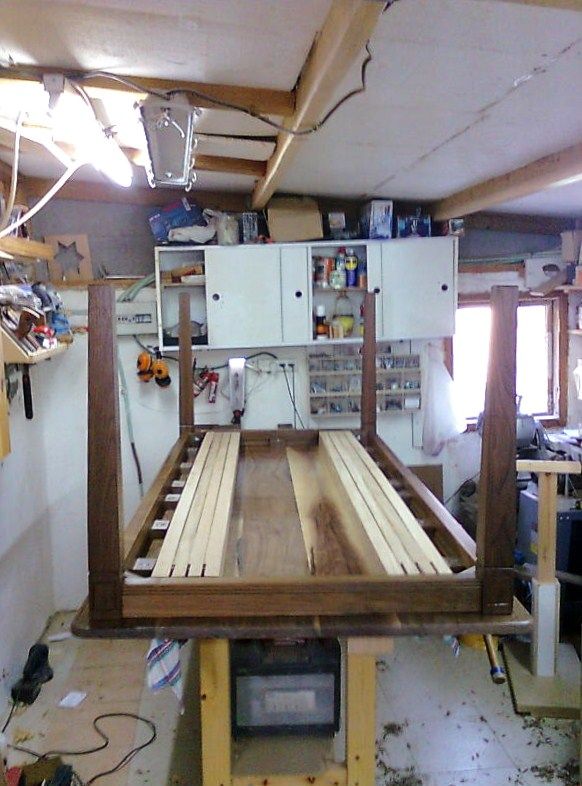
Click here for higher quality, full size image