Floating Shelf Installation Methods
Ideas and an example for successfully installing heavy "floating" shelves using rods driven into the wall studs. October 27, 2009
Question
We are in the process of installing floating shelves in a kitchen. They are 60 inches wide, 12 inches deep, and 1.5 inches thick in solid oak, so they are pretty heavy. They need to be able to support plates and glasses, so assume a fair amount of weight. The surface is drywall and the wall is finished, not open.
Our tentative plan is to use 12-inch x 5/8 inch steel threaded rod to support the shelves by screwing the rods about 3 inches into the studs, and then sliding the shelves (with holes drilled in them to correspond to the rods) onto the rods. We also planned to use Liquid Nails inside the holes in the shelves.
There are 3 studs behind the shelves that we can use to anchor the rods. Has anyone done a similar installation?
I am most concerned about being able to drill perfectly straight into the studs, and also perfectly straight through the shelves (to a depth of 9 to 10 inches). We have a drill guide and a 10 inch Forstner drill bit that is 7/8 in diameter to make the holes in the shelves. What kind of drill bit would you recommend for drilling the studs?
Finally, I am aware that there are blind shelf supports available at Lee Valley and Hafele, but unfortunately they are not long enough for this application (only 5 inches long, not enough to support a 12 inch deep shelf that has to take a fair amount of weight).
Forum Responses
(Cabinet and Millwork Installation Forum)
From contributor M:
I wouldn't wish drilling a 9" deep hole 7/8" bore into a 1 1/2" thick edge on anyone. I usually get around this situation by cutting a slot in the drywall over each stud and screwing on a massive steel angle bracket. The bracket leg sticking out into the room slides into a slot in the edge of the shelf which is miraculously formed by laying the shelf up with a hollow space in the center. (1 1/2" thickness = 2 x 5/8" faces with 1/4" thick spacers)
From contributor K:
I have a couple methods of doing this, but I need to know the maximum weight. Does either the left or right touch a wall?
From contributor Y:
Does the shelf have to be solid oak? You could build a torsion box with oak veneer and lag screw it to the wall. The torsion box is extremely strong but lightweight and you can make them in whatever dimensions you need. You can probably still find Ian Kirby's articles on them in Fine Woodworking archives.
From contributor W:
You don't have to drill perfectly straight into the studs. I use lag bolts, pre-drill as straight as you can, drive the lags as far in as you want, cut off the heads, then use a piece of pipe to bend them perfectly level and square to the wall. If you have a horizontal boring machine you could start the holes in the shelves with that then finish them by hand. Although I would opt for the torsion box method mentioned above.
From the original questioner:
Thanks. Unfortunately, the torsion box method is not an option; the shelves were custom-milled and have already been delivered. I *wish* we had gone the torsion box route, but it was not my choice and it is too late now.
To answer other questions: there are no walls on either side of the shelves. The only way to attach them is along the wall running directly behind them.
Regarding the angle brackets suggestion: are these special brackets, or something you can get off the rack? We had considered having brackets made by welding steel rod onto railing, but nixed the idea due to costs and time constraints.
From contributor K:
Is the back open at all or is it banded/solid all around?
From the original questioner:
The shelves are completely solid (we had planned on drilling 9 inches deep into them to make tunnels for the rods to slip into). The wall is closed also, but obviously we could open up parts to expose the studs if need be.
I did find someone who offered to drill the holes in the shelves in their shop with a big drill press, if we get really stuck. But apart from the issue of drilling the shelves, does it seem that the rod approach (i.e., using allthread to support the shelves) would work? We can only go 2 or 3 inches into the studs with the allthread, and would have about 9 inches of rod supporting the shelves. Do these ratios make sense (I am concerned about shearing load)?
The shelves themselves weigh around 60 pounds, and they need to be able to hold plates and glasses safely. Ideally I would like to have them be able to bear 150 lbs total; I know someone who has similar shelves in a kitchen rated to 150 and they work very well.
From contributor R:
I would think you could get all of 3" into the stud with your allthread. Test your idea in the shop. Take an existing stud... mark the idea of drilling a hole into it to the cost of education... or fasten one someway to your wall. Drill your hole and insert the allthread, gluing as desired, and let cure. Then hang a bag or so of rock salt on it and see what happens. Or do two rods and have your 150# employee do a chin up. Does it hold?
From the original questioner:
You know, that is a really good idea. I was thinking along the same lines in terms of weight - if it could handle someone standing on it, I think we would be good to go.
From contributor C:
I would use a spurred ship auger to drill the hole through the shelf. It will stay true going through once you get the setup on the drill press. You may need to grind off the threads on the self feeding tip to take the load off the drill press and/or bring the speed all the way down.
From contributor T:
I recently tried to pull this off, only with thicker salvaged timbers. Started out by cutting a stopped channel in back edge of shelves, and made a ledger strip to fit in that channel. I epoxied and bolted threaded rods into the ledger, drilled corresponding holes into shelves. I drilled the holes on drill press, as deep as possible, then finished by hand. The plan was to screw and glue ledger separately to wall, then slide shelves on. The wall was plaster on lath over block, so it was real uneven - all told, a nightmare waiting to happen. Finally talked the owner into simple angle iron brackets painted to match wall. Much more secure, and I haven't thought about it since (as I would have if I went the way you're trying to go). Still had to scribe back edges of shelves - a little easier because of the channel. You might want to do this (relieve back edge of shelves) to reduce the scribing chore. I guess your plan can work, with a lot of trial and error for each shelf. You'll want to somehow support the shelves in level position for a couple days while the construction adhesive sets up.
From the original questioner:
The salvaged timbers must have looked really nice.
The owner is very particular, so visible brackets are a no go. It really would take away from the look of this particular kitchen, which is ultramodern and sleek. We are going to give it a try with the rods on Monday. Thanks so much for all the tips.
From contributor J:
Use a long lag bolt, then cut the head off after installing.
From contributor V:
I mounted a fir timber mantle, which weighed 120lbs on its own, by drilling holes into the studs as you are planning, and used pieces of black pipe instead of the all thread. The all thread really should be under tension in any sort of structural situation.
From contributor L:
Why exactly do you need to go so deep into the shelves? Drill a 3" deep hole in both the shelf and the stud, and set the rods in epoxy, with spacers running up from the floor. End of story?
From the original questioner:
The idea of going deeper into the shelf was to provide support for the front part of the shelves (they are 12 3/4 inches deep). I have an engineer friend who insisted that an 8 inch deep shelf needs 5 inch deep supports, and a 12 inch shelf needs something more than that. And I know of one person who successfully did the same installation using allthread and he drilled 9 inches into the shelves. Three inches may very well have sufficed, for all I know, though.
In any event, as it turns out, we were only able to go about 8 inches into the shelf with the particular drill bit we had today. That is, into the one shelf that is now drilled with its 3 holes. All the rods are up on the wall; no problems there, and they appear to be able to support plenty of weight. But none of the three drills we had were particularly enthusiastic about their encounter with the oak, so we made a quick phone call to a friend and are using his drill press tomorrow to finish. Hopefully, that will go more smoothly. I also think we should have used a different drill bit, but that is another story.
If I could have done it differently, I think I would have opted for the torsion box method or the method of sandwiching the brackets, which probably would have worked really well here.
From the original questioner:
Thanks everyone for all of your advice. It was very helpful. The allthread worked fine, as it turns out. We ended up drilling the shelves without a drill press (just an auger bit and a corded drill) and that worked out also.
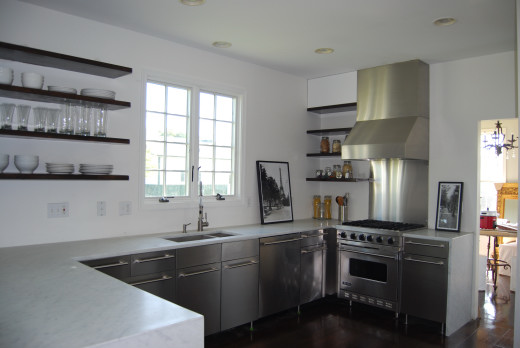
Click here for higher quality, full size image
From contributor N:
Last year I installed torsion box type shelves that, when finished, looked identical to your product. The wall was solid concrete. The shelves were 14"-16" deep, and I specified 1/2" steel rods, set (glued) deep into the concrete wall and likewise, deep (12") into 2x lumber cross members set 16" OC reinforcing the shelf. I haven't heard a word! It must have worked well.