Grooving with a Shaper: Tearout Prevention
Solutions for a tearout problem encountered while cutting tongues and grooves. March 6, 2008
Question
I set up our shaper to put a 1/4" x 1/4" groove into the back of some S4S. We have been outsourcing this operation and have been thinking about brining it in house. Well, I ran a test phase and when I try to set the shaper feeder on the highest speed, I don't get the clean cut I am looking for. There seems to be some additional tear out that I wish I could eliminate.
Now you might say, why don't you just run it at lower speeds? I am glad you asked. First of all, I do get an occasional tear out even at lower speeds. But if I want to bring this operation in house and make it cost effective, I am going to have to be able to move a bunch of stock through before the cows come home.
I was hoping that some of you wiser, more experienced folks could give me a few tips as to how I could eliminate tearout while maintaining my higher speed. Of course the cutter is probably an important piece to the puzzle. The cutter I am using is fairly new, not quite sure how much we have used it. It is a carbide cutter. The spindle speed - I am not sure what it is. There are two separate pulleys to choose from and we chose both with not much different results.
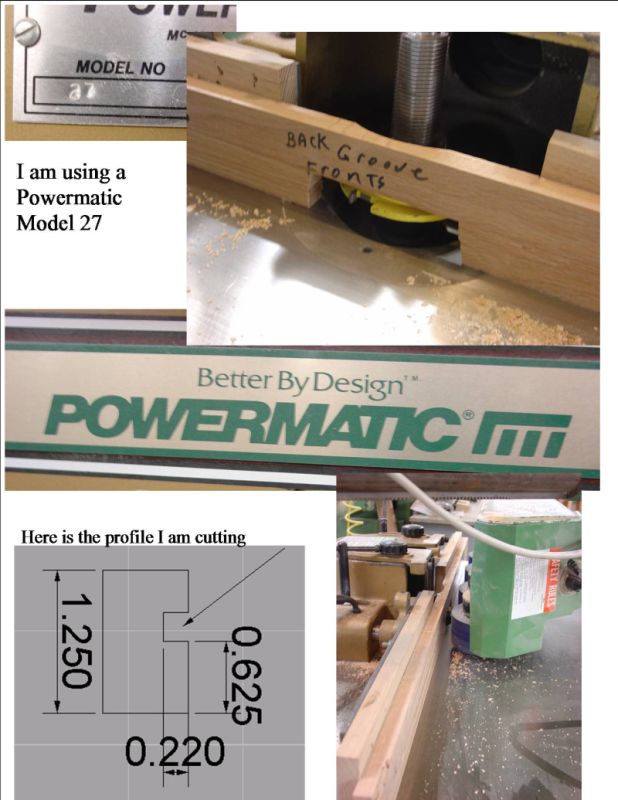
Click here for higher quality, full size image
Forum Responses
(Cabinet and Millwork Installation Forum)
From contributor T:
I would climb cut it. This can be more dangerous if you don't know how. I definitely would get advice before doing it. Also, the fence should give maximum support - hole at cutter is way too big.
From contributor T:
I just took another look. Looks like drawer side material - this should be easy to climb cut and you will have little or no tear out. If you run too slow, it will fry your cutters.
We cut a 1/2" groove in ours. We use table saw, dado blade, and power feeder.
From contributor D:
I know you are trying to speed up production, but you don't want to reduce quality. How about if you cut your groove just a little deeper, say 1/32 or 1/16, and then run it over your jointer? Are you sizing your stock? Maybe you could do this operation prior to cutting your stock to final dimensions?
From contributor R:
Your tear-out could very well be from running stock through in the wrong grain direction. It would be worth the time to mark the stock as you get it out of your planer and stack it. With just a 1/4 X 1/4 cut, you should be using the shaper's top speed.
From the original questioner:
I take it climb cut is running the stock through the opposite way? Can I still do that with my existing power cutter? By the way, this stock comes sized; all we do is put this groove in it.
From contributor B:
The first thing I see is the wrong machine for the operation. A dedicated table saw with the right blade and a power feeder would do a better and more consistent job. I stack two 8" blades with paper shims to get just the right width. Saw blades have more teeth and will "out cut" the shaper knife.
From contributor A:
I had a project a while back requiring numerous width grooves. I bought a 6" Amana dado set and had it bored out to fit my spindle. The bigger shop I used to work at had a nice Forrest 8" bored 1 1/4 for cutting tenons and variable width grooves. The Amana sets are about $130. Running this at 10k rpm on a shaper with a power feed will give the best cut available.
From contributor T:
The immediate fix for you is to climb cut. Just feed from the other end - remember to change not only the direction but angle of power feeder. Turn cutter so it doesn't hit your stock and feed it through with shaper off. Be sure the power feeder is touching the stock evenly and very firmly. The amount you are taking off should be pretty easy to do. Just the same - stay out of the way. We used to run door parts on the same shaper you have. I built an adjustable fence that we spaced desired stile width from the cutters and power feed against it (away from cutters). Stock comes out exactly same width every time.
From contributor F:
I know it's sometimes hard to change course once you make up your mind about tooling for a millwork operation. I have to say that I agree with others that the table saw with the right cutter and a powerfeed is going to outperform the shaper. There are companies that make and sell special groovers for tablesaw use. Straight teeth of the correct quantity for your application will make short work of this task with great results. If you must use the shaper, climb cutting will give you almost 100% tear out free cuts. Another thing to consider is reworking your shaper fence to allow you to keep fresh zero clearance at the point of cut the same as a table saw throat plate.
From the original questioner:
Thank you. Climb cut was the ticket - no tear out whatsoever even on the fastest speed. Now I wish we could run our Maggi feeder even faster :)
On a similar note, we have a Powermatic PM2700. It has a new type of spindle. The spindle itself is not threaded but it has these spacers you put on the spindle and then put a screw in at the top. I was curious if it is possible to run two cutters at the same time to place two operations at the same time. I would want to run two cutters like what I was showing in the pictures above.
From contributor C:
If you're running a power feeder, it helps and limits the movement of the stock as it passes through the cutterhead. During this time is when the stock is moving up or down slightly to create the tear out. Maybe a stronger down pressure, a horizontal hold in increase or feed pressure increase. Back cut it for the best results, with plenty of dust removal suction, and at least clean the cutter. These items should provide a nice feed speed increase.
From contributor U:
I don't see why you couldn't run a second cutter stacked on the spindle if you can get the spacing right. I have the same spindle type on some MiniMax shapers. You can get plastic shims from your cutter supplier for fine tuning. If that is a Freeborn cutter, it is Tantung (yellow paint), not carbide (orange paint) tipped. It wears faster in abrasive woods, but takes a sharper edge than carbide.
From the original questioner:
It is a Freeborn cutter. Are you saying I should be using the carbide? I don't know what constitutes an abrasive wood, but we are using birch and red oak with it.
From contributor U:
Carbide vs Tantung probably not a big deal for you unless you sharpen them yourself. They take different abrasives. For teak and other high silica tropicals, carbide would be best.
From contributor L:
Not mentioned above is the geometry of the cutter. I've found that having the sharp corners on my cutters radiused a very small amount eliminates tearout completely and aids in finishing and in assembly of parts if aesthetics is not an issue. 1/64" rad. does wonders. Stay with the tantung. The tannic acid in red oak eats away the edge of carbide and dulls it much faster, especially with intermittent use. (The acid dulls the edge while you sleep.) I've found tantung to last 3-4 times longer in red oak.
From contributor M:
Has anyone ever seen how a moulding machine, sticker, or whatever you want to call it, works? All cuts are climb cuts - that way there is no wrong grain direction, no tear out - even at the fastest feed rate.
From contributor O:
Using a standard grooving cutter in a shaper will always give poor results unless you climb cut or take additional material off with smaller diameter stacked cutters below and on top of the groover. In the case of drawer sides this would not be practical.
The best way is to use a European adjustable or fixed width groover that has the incisor spurs top and bottom of the cut. We groove difficult material like VG fir all the time with these without any climb cutting. All the euro tooling suppliers carry these, usually starting at about 140mm diameter.