Huge Round Conference Table Construction
An extended discussion of the issues involved in extreme furniture building. June 18, 2009
Question
Recently, I was commissioned to design and build a round conference table that will be about 15 feet in diameter. Since I am in the very early stages of planning, I am wondering what the best method of construction is. Since any use of solid wood appears to be out of the question, I am thinking it should be made up of pie shaped sections, joined on site. The plans also call for the table to be wired with pop-up data ports for 20 people. If each slice of the pie was made of 3/4 or 1" MDF, and veneered on both sides, will I have any chance of pulling this thing off? Also, if the bottom of each section was veneered with plain veneer, can the top be veneered using multiple decorative veneers? Can I count on each section to stay flat? Once I figure this out, I will ask how to handle the outer exposed edge.
Forum Responses
(Furniture Making Forum)
From contributor M:
No, you cannot count on MDF to stay flat. It is not flat; its thickness is constant. If you want MDF to be flat, you first have to make it flat (a flat work table helps), then keep it flat (torsion box construction is nice). Then, yes, you can balance a decorative veneer top with a bottom of plain veneer of the same type and thickness.
From contributor J:
MDF is probably an excellent substrate, but its long-term flatness will depend on the support structure it's attached to. How far in from the edges will the legs be positioned? How far does the top need to be cantilevered?
I'd be concerned about the flatness of the floor wherever it will be installed, and would want to incorporate some sort of leveling mechanism. I think you can do it in pie slices, but I would not try to make the slices fit together seamlessly. Instead, I'd play with designs that leave an intentional gap between the slices, as a design feature. Maybe 1/4"?
From contributor B:
I'm certainly no expert on MDF, but I would look into using a double layer of thinner material to build up to final thickness (minus veneer, of course). This double layer with a glue line should help to stabilize the top sections.
Also, you might consider a 3' to 4' round center section that each of the pie cuts meet as they approach center. This would alleviate the need to bring a bunch of points together on-site accurately, and also add a pleasant dimension to the design.
From the original questioner:
Thanks. I have entertained the thought of a center circle for the slices to meet, and thought of leaving intentional gaps for this design. I will also try to figure a way to cantilever the top at least 36"; the torsion box idea should cover that. I will also use some sort of levelers to line everything up. I will think of it as several little tables that just happened to be set in the shape of a circle.
From contributor L:
Don't forget to check the size of the freight elevator.
From contributor S:
From what you said I picture a table 15' across and 3/4 to 1" thick with veneer both sides. It sounds like you are building and designing as you go, which is a dangerous method. We have no idea what machines you have or what your abilities are, so it makes it difficult to suggest building methods or what materials you should even use.
From contributor B:
I got a call from a friend who normally does Corian work. Things were a little slow so he agreed to make a veneer topped conference table for a customer. He has good working skills and this was well within his capabilities... even the veneer work.
The table came out great and he called me to ask if I knew of a finisher he could use. He wanted a professional finish applied and knew well enough that it was out of his league. I couldn't help him with a contact in the area but he did find someone on his own.
About two weeks later I got another call from him... this time with panic in his voice. He wanted to know if I knew of a way to reattach veneer without hurting the newly applied finish. Turns out a lacquer based finish was applied and it penetrated through the veneer butt seams and softened the "contact adhesive" he had used to apply the veneer. Oh boy...
Needless to say, he rebuilt the table top from scratch and didn't make much on the project... unless you consider the experience gained to be payment!
From contributor O:
3/4 MDF with balance veneered is very stable if attached to even the most basic frames. Wouldn't worry too much about that. Anybody else will tell you the same.
There is an old school book called Blackie and Son's, A Cabinet Maker's Assistant. There are a ton of good geometry tutorials relating directly to what you are trying to do. Best of all, you only need a quality compass or two, a ruler, and a pencil.
For what it is worth, I don't think designing in a flaw (gap between pieces) makes any sense. I would think if you can't make slightly chamfered edges meet well, you need to think about your design or machining approach.
From contributor V:
No, 3\4" or 1' thick material over that dimension will sag, bend, warp, and fail. You need to build a torsion box.
Torsion box construction allows you to hide your wire access and data ports.
Construction design and artistic design need to be considered jointly along with access to the site. While the piece may fit through the door... Will the crew carrying it fit also?
From Professor Gene Wengert, forum technical advisor:
If wood changes by 1% MC, it will change size by about 0.25%. So, 15' width will try and change about 1/2" with a 1% MC change. We can expect in an unhumidified building that that MC will change by about 3% annually, which means 1.5".
If the table is round with pie shaped wedges, the circumference will try to change by over 4" with a 1% MC change.
What this means is that to be successful, you will have to make sure that the MC at the time of assembly is perfectly matched to the final MC. Further, the finish (top, bottom, edges) must be the best possible to avoid moisture changes as much as possible and the room should have the RH closely controlled. Can you make sure they understand that without RH control, you cannot guarantee the work? Will they allow you to put an RH measuring device in the room so if the RH varies greatly you will be protected? If this cannot be done, then can a large hole be put in the center?
Can grooves be put between the pie wedges to allow movement? Could you put in a few tongue and grooves so the pieces could move in and out and have it not look like a defect?
Do not try and hold the top stable with metal, as the resulting forces will crack the wood. Rather design it so it can move when the RH changes (which it will). You ask if it can stay flat. Use metal to hold the pieces flat. Use slotted holes so that the wood can move within the frame.
From contributor C:
Gene, great insight there. Let me run this past you since your knowledge of RH and its associated movement far exceeds mine... If this entire assembly was a good torsion box sub frame that was balanced with 1/32" veneer on 5 sides, how is the change in RH going to affect it?
From Professor Gene Wengert, forum technical advisor:
I do not know, as I do not fully understand your plan.
From contributor C:
Each individual section would be made of 1/2" plywood formed into a skeletal subframe. The subframe would then be laminated (glued and pinned) with 1/2" MDF. A 1/8" veneer would be attached to the MDF on the outside to provide the waterfall edge. The two remaining sides (the faces that will be mated to the adjoining pieces) and the top and bottom would be veneered with 1/32" veneer which would mostly likely be vacuum pressed and then trimmed to size before being joined with its adjacent mate.
The theory here is that the torsion box assembly provides a strong, lightweight, stable substrate and that the 1/32" veneer would be much less prone to movement than any of the solid wood. The 1/8" outside edge would be necessary so that you could ease the heavy contact edge of the table.
From contributor A:
If I were you, I would stop trying to figure this project out from the typical woodworking perspective. You need to negate the movement as much as possible. The torsion box method is a good start, however it's not enough. I would switch to a Nomex honeycomb type core with 1/8" MDF. This is a composite panel with very little movement. I would imagine even less than the MDF movement. Veneer all of the surfaces. You will be amazed at the strength of a properly cored panel.
From contributor C:
Good point about the Nomex - very fond of the honeycomb core materials myself. But can you get (or create) a 4" thick slab of it, which is what the original poster needs to do?
Again, I would not be so much worried about the movement of the torsion boxes (in my opinion, that aspect of the design is settled). The biggest concern that I have would be the tendency of the face seams between two different species of veneer opening up/lifting with changes in RH and MC. Any thoughts on that?
From contributor O:
A simple 2" hardwood frame would take anything balance veneered MDF could throw at it. Wood moves a little bit, but on MDF or even plywood, it is almost imperceptible even on big sheets. This has been my experience.
From Professor Gene Wengert, forum technical advisor:
The veneer will still try to move even on MDF or a torsion box. So, will this attempted movement cause a failure of the veneer (buckle or split) and cause warp? I do not know, and certainly the answer depends on the MC change involved. We cannot totally change the basic behavior of wood with the substrate.
Plywood and MDF are more stable than solid wood, but they also move with MC changes. In fact, solid wood moves very little lengthwise, but with plywood or MDF, the core will move and potentially cause some issues too. So, I am not too supportive of the above suggestions.
From contributor G:
20 years ago we had an architect design a conference table with stainless and glass components. We took the job just like you did. We challenged the size and how it would install but the architect was offended like we kicked his mom. He ended up having the windows removed on the sixth floor and a crane brought in.
On your table I would design the base under a smaller round, then build sections around that using a solid wood apron and an MDF and veneer top, then bolt all the pieces together on site. MDF is stable and the apron design will be strong as well as accommodating the racing of wires to the base. You will have joint seams, but no avoiding that on a table that size. I would avoid contact adhesives at all costs and use a bulletproof finish for coffee spills.
From contributor J:
I can't help but think that this problem is insoluble unless you pin down exactly what would qualify as "good enough." Perfect is a target that none of us ever hit.
In any case, if we're dealing with independent pie-slice segments built as torsion boxes with the top and bottom skins taken from 4x8 sheets of some engineered material, then we're looking at a dozen triangular panels, 90" long and about 46.5" wide. Veneered panels of that size seem pretty common, which in turn suggests to me that anyone claiming it can't work well must be basing their thinking on some faulty premise(s).
From Professor Gene Wengert, forum technical advisor:
I think your comments in the second paragraph are correct if quality requirements are not too severe (paragraph one). However, in my experience, table tops seem to have exceptionally high quality requirements where even 1/10" gap or other defect is a defect that cannot be tolerated. I second the concept in your first paragraph and strongly support it.
From contributor S:
Take a look at the Fletcher Capstan table.
From contributor J:
Thanks, Gene. A 1/10" gap in a joint that's supposed to be tight would certainly be unacceptable to me.
One of the premises I'm wondering about is the idea that MDF moves 3 X 0.25% due to normal seasonal humidity changes. I found a PDF published by the Composite Panel Association that says particle board (it doesn't have a stat for MDF) moves 0.25% with an RH change from 40% to 85% (doesn't specify what EMCs these correspond to). If MDF's dimensional properties are anything like particle board, then your claim doesn't jive with this publication. Also, I don't think I've ever met a sheet of MDF that's 3/4" longer in the summer than in the winter, even if that sheet is totally unfinished and sitting in my shop which is heated during the (cold, Great Lakes) winter and not air conditioned in the hot, humid summer. I suspect there's some context missing here, and that movement in real-world scenarios (as opposed to a lab) is considerably less dramatic.
From Professor Gene Wengert, Sawing and Drying Forum technical advisor:
The veneer could move quite a bit, but as you note, composite products are much more stable than "raw" wood. I did not intend to imply that MDF or other composite would move 3/4".
Although changes in RH do not provide a linear relationship to shrinkage or swelling, we can still make a rough estimate that 22.5% RH change (summer to winter in an in-use situation) will cause 0.125% size change. On 8 feet, that will be about 1/8" for composites and 10 times more for veneer or solid wood.
There is one large concern about composites and that is the initial swelling. Pressure was used to make the product, so when the product is wetted for the first time, it will swell excessively (called springback). This can certainly be an issue, even though subsequent movement is small.
From contributor P:
Why not solid wood? This is a table I did 5 years ago (7 feet in diameter) and it sits ocean front in North Carolina. The doors are open half the time and the AC or heat is on the other half of the time. I like to work in solid wood. I find it's easier to fit and more forgiving when it comes time for sanding. The center section of this table is half an inch thick and the walnut circle is three quarters thick. The cherry band is three quarters by one and a half and has a tongue and groove joint that connects it to the walnut. Clear CV for the finish. I see these folks about once a year and they always tell me how nice the table is. You had written about the idea of having a table within a table. I believe that could happen in solid wood. Breaking the wood down into smaller sections gives you the upper hand on wood movement.
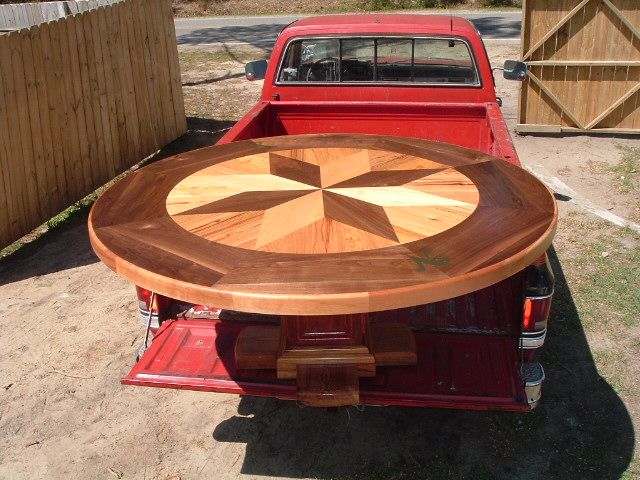
Click here for higher quality, full size image
From contributor J:
That's a very pretty table. I wonder whether the coastal climate, particularly in a state like NC where the temperatures never get that extreme, might be especially forgiving. Just for kicks, I looked up NWS data for Morehead City, and found the average temperature to be 46.3 degrees in January, 80.5 degrees in July. That suggests not much of a heating season and not much of an AC season either. I'm sure you're right that a piece made from many small pieces of solid wood would be more forgiving - perhaps even when the joints do loosen a bit, the cracks will be acceptably small. Ship that table to Phoenix, though, and I'd bet it would soon be kindling. Context is everything.
From contributor U:
Spend some time on the Outer Banks and you will see that the weather data is not the whole story. It gets to 100 in the summer and snow is not unknown in the winter. It is never as dry as Arizona, but for that, we are thankful.
From contributor A:
Beyond the heat, NC has a wide range of humidity throughout the year. That is a beautiful table. When was the last time you personally saw it? I assume that the customer would have been calling if there was any serious movement.
From contributor P:
The last time I saw the table was when my guys drove off with it while I took the picture. That was 4 or maybe 5 years ago. I have since worked for the same guy. He's a builder. This table is on Bald Head Island, NC in his personal vacation home. If there was any problem he would not hesitate to call. He gave me plenty of work and he's that kind of guy.
From contributor T:
A 20 ft diameter solid table is impractical in a number of ways, mostly in that the center area is unreachable and kind of wasted. A company I worked for years ago made a 16 ft diameter conference table that was donut-shaped; the width of the table ring itself was maybe 42 inches or so. It was composed of ten sections, each a truncated pie shape, or section of donut. Each was veneered on 1" thick MDF by a custom veneer house. Inner and outer edges had 1.5" x 3" solid edge applied. The base was a vertical wall supporting the interior of the table top, and a series of commercial metal legs with levelers supporting the outer edge. Finally, two of the ten foot sections along with their base structures were outfitted with wheels so they could be rolled away, making the center of the donut accessible for a speaker.
Getting the edges of the pie pieces (whether full pie or donut) at the perfect angle is a major issue. I remember that when I finally assembled my ten pieces, there was a significant error that accumulated from an undetectable error on each piece. I simply made the adjustment on that last piece. Mating curved trim to top blanks involves lots of shaper work. Everything about a project of this size gets very challenging, starting with the necessary space you need to stage a 20 ft. diameter table. Lightweight core material is a definite way to go.
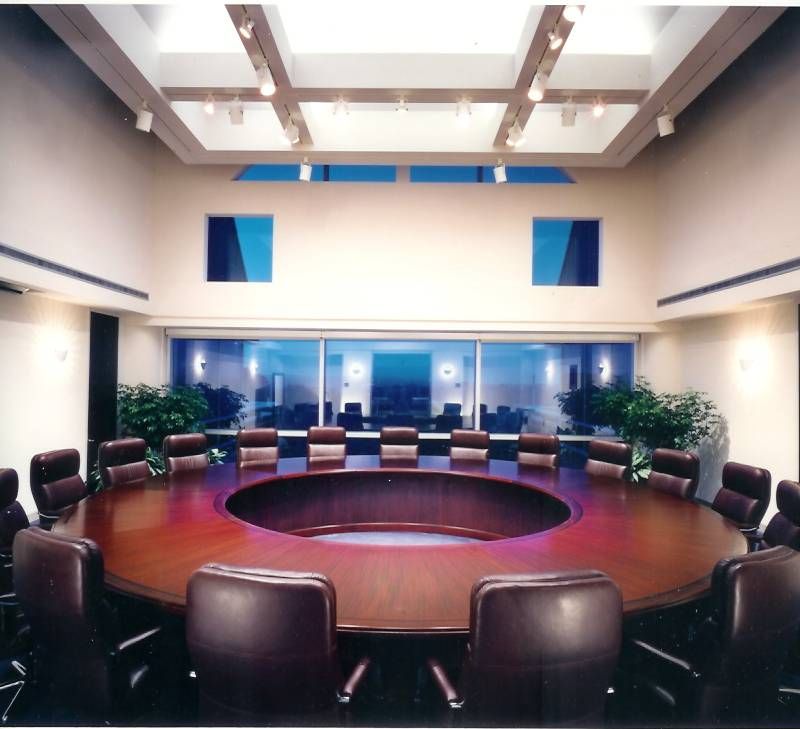
Click here for higher quality, full size image
From contributor Y:
If you make a round table with multiple pie shaped pieces, try to true them up when you have a 1/4 table section, and then again at 1/2 table. I built a round table using 36 wedges - a few minutes of a degree in the angle made a huge difference. It was only a 5' diameter table, so I ran it over the jointer in halves. A 20' table would be a different story...