Limitations of a Five-Head Moulder
For deep cuts in heavy profiles, a six-head moulder offers better capacity than a five-head unit. May 3, 2011
Question
We are considering our first moulder, a Weinig gold 5 head 06. Our concerns are the left/right spindle are shared 10HP. We have read everything we can on this site and are convinced that for what we will be doing, we should get a 6 head with as much HP possible, but like all things in life, it wouldn't be any fun if you could have it all. So for doing everything from small lip moulding to 9" deep cut crown, door parts, cab and int., flooring, etc., what problems might we expect? Ultimately, because of lack of experience, can it do it... slowly?
Forum Responses
(Solid Wood Machining Forum)
From contributor J:
If you're hogging a lot with both side heads in hardwood, you will most likely trip the breaker after a short time. After that it trips really quickly. Running at slow feed rates will dull your knives quickly. I have found running 3-4 pieces at a time with a small pause in between works. But just understand that if that happens, you are really trying to get more out of your moulder than it's designed to give, and will have to deal with any consequences it might produce.
From contributor S:
Why do something slow at best? Is your heart set on having a Weinig 5 head Gold series?
Right now it's a buyers market. Start looking if you want to run the profiles you said above. Spend the money for a 6 head with combined sidehead hp of 15 -20. There are other moulders besides Weinig that are equally rated and for a lot less money, like Leadermac.
From contributor U:
Right now, you can still make some deals on moulders. Prices are starting to go up for used equipment.
How much production do you plan to run in the beginning? How much production do you plan on running? If you are just producing small orders, a 5 head is fine. If you are planning on really running this moulder, I would purchase a 6 head moulder. A 6 head machine is great for a shop that wants small runs to large production runs. They are also right now still decently priced.
From contributor W:
The Unimat Golds were designed with individual side head motors. A 5 spindle machine should have 5 spindle motors plus the feed motor. If you can provide the machine serial number and sample drawing of the profiles you will be running, we [Weinig] will be more than happy to research the existing horsepower on the machine and let you know if this machine can accomplish your production needs.
From contributor M:
You can produce just about any moulding on that machine that will fit through it. There are very few occasions where your side head profile is so deep that you are even remotely in danger of bogging down your motors. In close to 20 years of running Weinig and SCMI moulders I have never tripped a thermal on a motor, nor have I had to stagger the input of material to the machine.
From contributor G:
2006 model UG-11-001, serial #-2019, B-R-L-T-B, 460V. What is necessary to switch to 208V internally in the machine, if we don't want to go the transformer route?
The first photo is an example of the material we buy (quartersawn sapele). First board has been planed through our 25" helical spiral planer. Second is in the rough, how we get it. I can also purchase skip planned and SL on one side, but would rather keep my guys busy. Will I have any issues feeding in the rough? If so, do we need to be looking for a double sided planer?
We are looking at a Northtech SRS-12 for our SLR and a new version Rainmann for our gang rip. Is a simple way of breaking down a moulder: it's a jointer, planer and two shapers in one machine? Typical material to be run: Doug fir plain sawn and VG, cypress, knotty and sup. alder, Spanish cedar, all types of mahogany, black walnut, etc. - the whole spectrum.
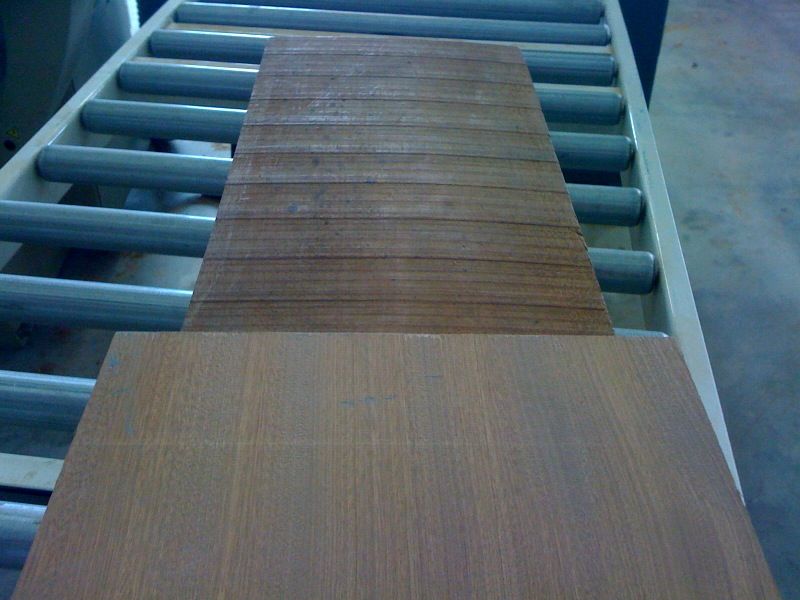
Click here for higher quality, full size image
Here is an example of our interior door jambs. How do you kerf/relief the back on a 5 head moulder with the head configuration being B-R-L-T-B? I'm guessing you run your profiles face down, so the first bottom head cleans it up and the second profiles and top kerf/reliefs. Is that correct?
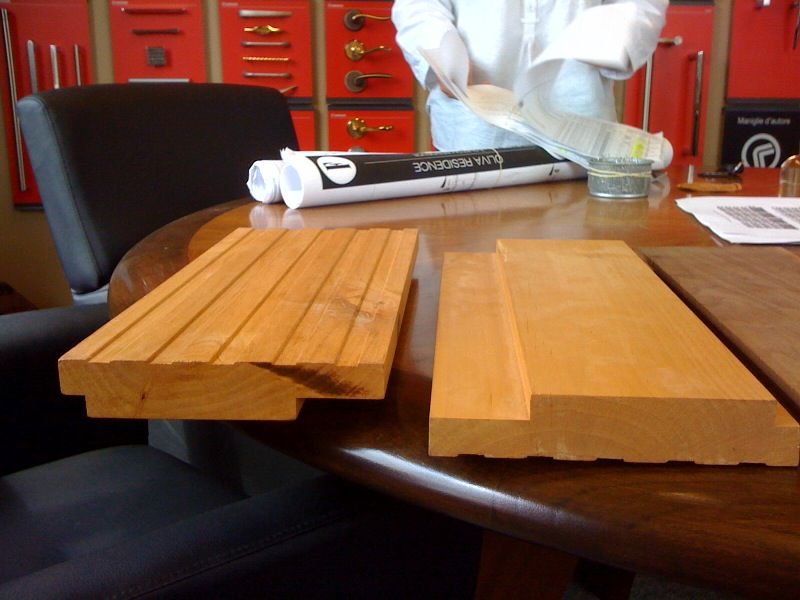
Click here for higher quality, full size image
Here are some more examples of what we will be running. Door stiles will be 1-13/16" or 2-15/16" with either a 1/2" or 3/4" deep profile, casing is 1-1/2" at thickest section and some brickmold and flooring, and then any casing, crown, base, lip mould, chair rail, cab parts, 1x6 T&G - pretty much anything that is up to 9" wide.
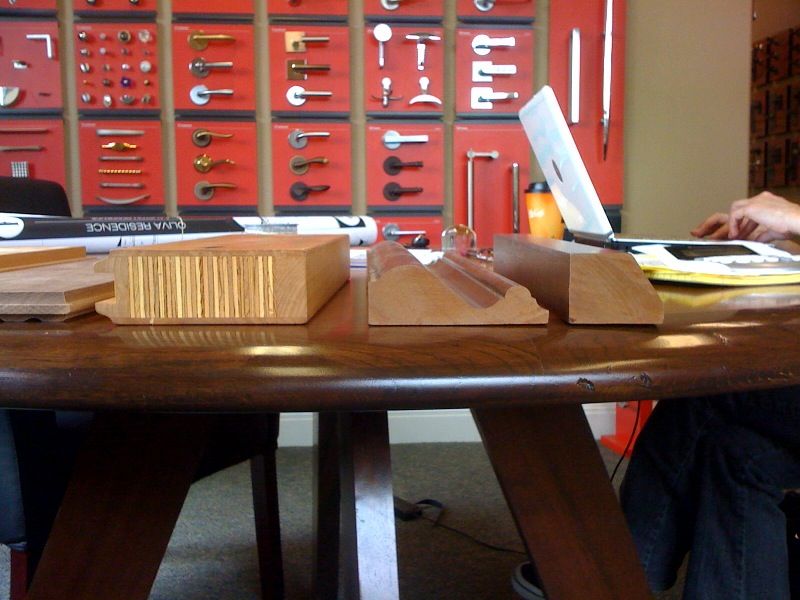
Click here for higher quality, full size image
From contributor W:
Our [Weinig's] records show the spindle horsepower is 10 hp bottom, 15 hp on the right, 15 hp on the left, 15 hp on the top and 10 hp on the last bottom. Should be no problem running what you have shown in your pictures. The infeed table is 2 meters long, so no problem with straightening. Spindle diameter is 1 1/2". Chromed tables and fences. Looks like a good machine.
From contributor V:
If I were running deep profiles like the ones posted, I would feel more comfortable with 1 13/16" diameter spindles. We run 3 moulders with 1 13/16" spindles on all of them. It makes it very handy to interchange tooling between different moulders.
From contributor O:
The side heads will cut the same amount regardless of whether it is a small profile or a huge profile. I stick to about 1/32" or less, more for rough/bent lumber. The machine is designed to do anything that will fit through it, and these machines have an excellent reputation.
I would not be concerned about the 10 hp sides. In 15 years I have never blown a breaker on a side head. Usually a top, but even that is very rare if you pay attention. Keep the tools sharp so they do not have to work any harder then they should.
Deep cuts such as rabbets are best done from the top/bottom.
From contributor J:
We run 3 profiles that trip the breakers. I am sorry for making anyone think I was downgrading anything. We do not all run the same stuff through our moulders so we all have something different to bring to the table and share. Our 3 was not meant to ward off a purchase of the Weinig gold.
I have a problem with the term, "it can handle anything that can fit in it." 1/2" rabbet on the left, 15/16" gallery cut on the right. Oak = trip breaker. I push mine to the limit, but that is not considered normal operations to most. And all other profiles are great running.
From contributor O:
Have you had your breakers checked? Sometimes they become just a little weak. A thorough electrical check, perhaps installing a power flow meter in line to record what is happening, will show if the breaker is being overworked, or is simply popping too early. I have changed these before due to weakening over time. Nothing lasts forever.
Perhaps the term "anything that will fit through it" was a little hasty. I personally stay just below the point of a trip. Say 40'/m trips. I run 35 all day long with no issue. There is nothing more annoying then having to keep opening the cabinet.
From contributor M:
Okay, my statement was a little broad. We also run tons of different profiles, some that require two passes or different strategies that will achieve the finished product. With that said, it requires a seriously deep cut to where we have to go two passes, and most of the time that's not because the machine trips out, but the finish starts to degrade. I guess my point was, with common sense, that machine can produce just about any moulding that fits within the parameters of the machine.
From contributor N:
You mention deep crowns. Why anyone with experience would say a 5 head moulder is adequate is beyond me. Get the right tool for the job or you will regret it later. A 6 head moulder is what you will need based on what you want to do and it gives you flexibility for future use.