Machinery and Methods for Creating Complex Stair Rail Shapes
Here's a long and detailed thread with photos about the production choices for crafting complex custom railing shapes. June 8, 2011
Question
I recently moved to using a molder head to make stair fittings. The knives tended to be about 3 1/2" tall so I got a 4" tall head which is also 4" in diameter. It was suggested to me to use graduated rub collars to make progressive passes but today I suddenly realized that the inside radius of a level quarter turn is less than 2 1/4". Short of hand carving it looks like I'm back to several passes with different router bits. Am I running down the wrong road? CNC is not an option.
Forum Responses
(Solid Wood Machining Forum)
From contributor W:
Flat handrail fittings are usually CNC or pin routed (as I've mentioned before). If you think the quarterturns are tough, try diving into the bottom of a volute with a shaper cutter! Anyway, it is true that production stair parts manufacturers use to use shapers for everything, but that was thirty years ago.
The old shaper process involved heavy, machined aluminum plate-templates along with fixed toggle clamps and guarded hand-grips. The actual cutting was usually done in two passes against an adjustable lower or upper ring and enclosed dust hood. The cutters themselves were small diameter three-wing type or even a router bit in a collet (for the inside of a volute). For safety sake, several fittings were usually gang-cut from a single block. Two-headed shapers were also set-up with identical cutters to facilitate grain issues.
If all this sounds a bit dangerous, it was. Many a good shaper man has been maimed while making stair parts. Thankfully, CNC as all but eliminated these kinds of injuries. Today, heavy CNC machines can even climb-cut and avoid tear-out and blow-out issues. So yes, I think you're running down the wrong (and potentially dangerous) road. The total inside cutting diameter of a factory volute or quarter turn is often no more than 1 1/2"! Old pin routers can still do the job and Onsrud made a 10 hp inverted router that was really good for stair fittings but nothings better today than CNC.
From the original questioner:
I appreciate your view point and depth of experience but CNC work is not a direction I intend to go. Quite to opposite, I'm going toward hand carved rising volutes, wreathed fittings, etc. and all that entails. If in order to produce full custom work, some router work and carving is involved, then that is what it takes. I would like to limit the amount of hand carving if I can, short of CNC work.
From contributor W:
Below is a picture from an old book (Modern Shaper Practice by W.H. Rohr 1923) showing a workman shaping handrail easements entirely "free-hand" (Please don't try this at home or anywhere else!) I am not actually advocating CNC for everyone (I don't own one myself). I am advocating caution and safety. If you're going to use a shaper, then design your rail fittings around the reasonable capabilities of the machine itself. For example, quarter-turns need to become quarter-bends with a larger inside radius. Regular straight easements can be run with a larger radius as well and will even look better than the factory 9.125". Volutes are made from open segments with inside radii cut first. In the hands of a skilled and experienced man, a shaper is capable of molding nearly all handrail parts, including flat radius and geometric work. The challenge of course is to retain your fingers and hands while gaining that experience.
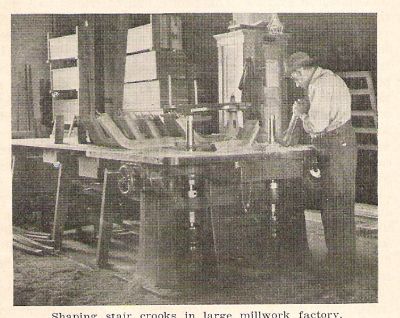
From contributor O:
The inherent danger of making fittings with large shapers is enough to scare off anyone - or should be. Making the custom fittings necessary for a stair shop is probably the most challenging problem-solving line of work in all woodworking - with some serious consequences for failures. The small quantity and unrepeatability require ingenious, out of the box solutions, often daily. Throwing small chunks of wood at large shapers never works.
There is no inherent impurity with CNC work, unless you market it as handwork. I suggest you think of the CNC as we do a computer - something that will do the mundane repetitive tasks to free your time up for more creative things. I am notably CNC deficient since I do not yet see where it will add value to our work. However, that does not mean they have no place. We don't do enough fittings where our ingenuity runs out and we need the services of CNC, but if we did more, the safety aspect would be reason enough to bring one on board.
From the original questioner:
Lately I've been in a circle of customers who adamantly do not want stock stair parts. so for a given house I may need half a dozen fittings of a custom profile, usually drawn by a designer, all having different rise/run ratio's. If I were to go to a CNC shop I suspect that each fitting would have to have program written for it. What would the cost of each fitting then become? Level quarter turns are about the only fitting that I could see this may be cost effective since the program would be the same from job to job, but now I would be paying for set-up to run two, maybe three fittings of that profile and wood species.
From contributor O:
I agree that the promise of mass customization as promulgated by marketers of CNC is far from attainable with one-off stair parts. I have spent years trying to get parts made by CNC, and the cost of programming or other technical requirements has always been the barrier. The investment you would have job to job, on top of the equipment will be a long recoup.
Overarm or undermount routers are the way to go, with the ability to hand grind steel router blanks, and custom carbide for the more common patterns. I have made swinging jigs for up and over easings, and have turned many parts on a lathe. If one looks at a staircase as the best example of craft in a house, your handwork and problem solving will be appreciated.
From contributor P:
I am just about to purchase a shaper to do tongue and groove flooring and the job suddenly turned into a request for a stair railing. I can do a straight handrail but the customer just asked if I could turn it into the Newel post at the top and a custom Newel post at the bottom that doubles as a support post for the second floor.
My thoughts are the hand rail starts out flat, then turns 90 degrees. On both the top and the bottom 90 degree sections, I will have to gradually curve down to meet the handrail as it goes down the stairs and at the bottom turn up to meet the railing as it goes up the stairs.
Is this something that can be done on a shaper, or is it something you think should be done on a CNC machine for safety reasons? I've never used a shaper but I now have a need for one. If it can be done safely on a shaper with the proper attachments, I'll get them.
From contributor W:
Can this be done safely on a shaper? Not really, especially for someone who has never used a shaper (definitely not!) Yes there are guys who can do this (relatively) safe on a shaper. I don't recommend it. Even good shaper men have to be very careful just doing level radius parts while double-curvature or helical parts are strictly for advanced, fearless idiots.
The part you are describing is most often assembled from standard fittings (including a flat quarter turn and a straight up easing). To make it in one piece is a bit of a challenge but possible. On a curved stair, the whole part needs to be curved.
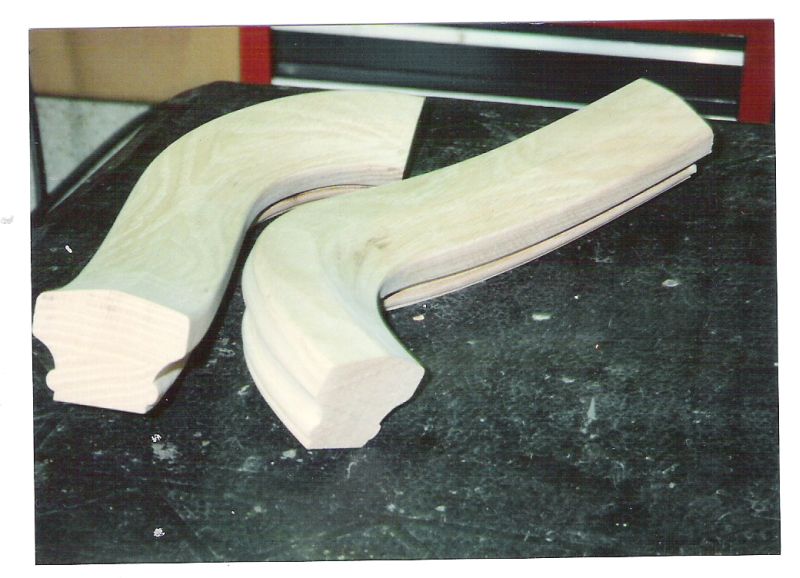
Click here for higher quality, full size image
From contributor P:
I think for safety reasons, I will purchase those pieces needed and I should still be able to cut the straight sections of railing myself.
From contributor W:
It's always best to work as an apprentice and learn from a journeyman or master. Today the industry is nearly all mass production and fully CNC integrated. Anything you might learn from older dudes like me would be considered "paleontology".
On the other hand there is still a small niche for custom work and guys that can still do it. If you want to become one of these guys then be prepared to spend a few years (a lifetime) of practice and learning. I get a little passionate about this work and also worry about others who might get themselves hurt while trying to figure things out. The shaper is a very unforgiving taskmaster.
From contributor A:
We use our CNC machine to craft all kinds of fittings. It is my opinion that it is much faster and more accurate. We have been making one-off fittings, carvings, signs, etc with our CNC and having pretty good luck. The proof is in the pudding. Get bids for the pieces that you need and see what the cost is. We use a combination of CNC work and hand work.
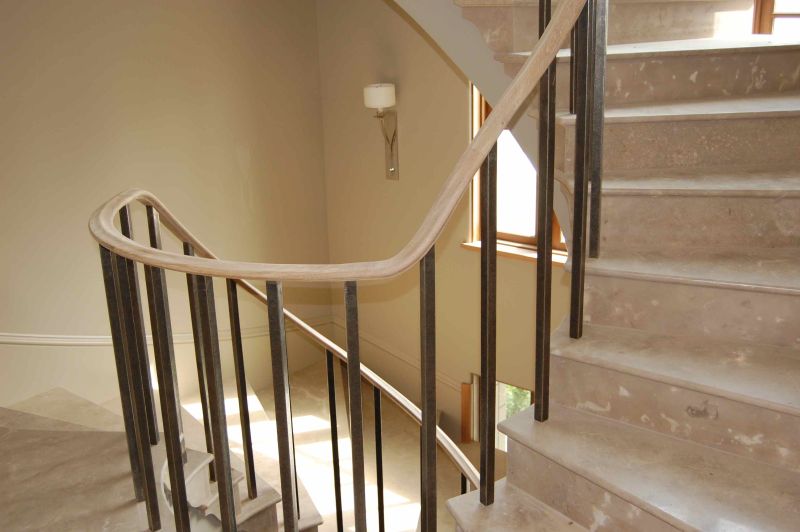
Click here for higher quality, full size image
From contributor A:
We use a 3 axis medium duty machine. I think the key is to use appropriate technology. I do not have any firsthand experience with a 5 axis machine but I believe they are much more expensive and more difficult to program. So we use a 3 axis machine and move our part as needed, followed by hand sanding and carving. Works for us, but may not work for others.

Click here for higher quality, full size image
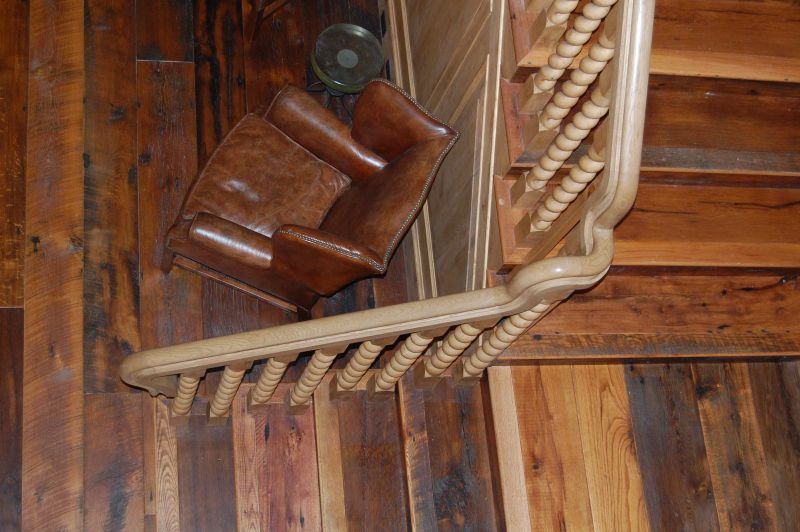
Click here for higher quality, full size image