"Mahogany" Stains for Birch
Finishers share formulas and methods for staining light-colored woods a dark mahogany color. April 19, 2006
Question
I am finishing a soft maple/birch cabinet to a dark red “mahogany.” I wash coated with Mohawk's Seal and Stain product, then applied their dark red mahogany pigmented wiping stain, sealed with lacquer sanding sealer and sanded. This came out too light, so I applied a glaze (Mohawk raw umber) to darken slightly. I then mixed about 1 1/2 ounces of their ultra penetrating dark red mahogany stain (an almost black red dye stain) to a quart of the lacquer and applied 3 topcoats. I ended up with a color I was satisfied with. I don’t have a lot of experience with manipulating color, particularly on a blotch-prone species taking it that dark.
1. Any thoughts on Mohawk's Sand and Seal? I think it is just their untinted wiping stain base. I used it full strength. I would have liked a little more bite from the stain to perhaps reduce the amount of toning. I am not sure what it can be thinned with, as I do not have any of their proprietary solvent.
2. I mixed the toner in the topcoat Mohawk high solids lacquer (18% solids by volume) cut 100%. Would I be better thinning to wash coat consistency for the toning? I was very pleased with the depth and richness of color added by the toning, but I’m a bit wary of striping or uneven color.
3. I have also played a bit with glue size. I mixed a 1-10 ratio white glue (Elmer’s) to water. Raised the grain, sanded, applied the size and sanded. I have only done one small sample, but this gave me good stain penetration with even color. Would this be a better route?
I plan to do a few more samples, but it’s a fairly large project and I'm a little paranoid about the final results.
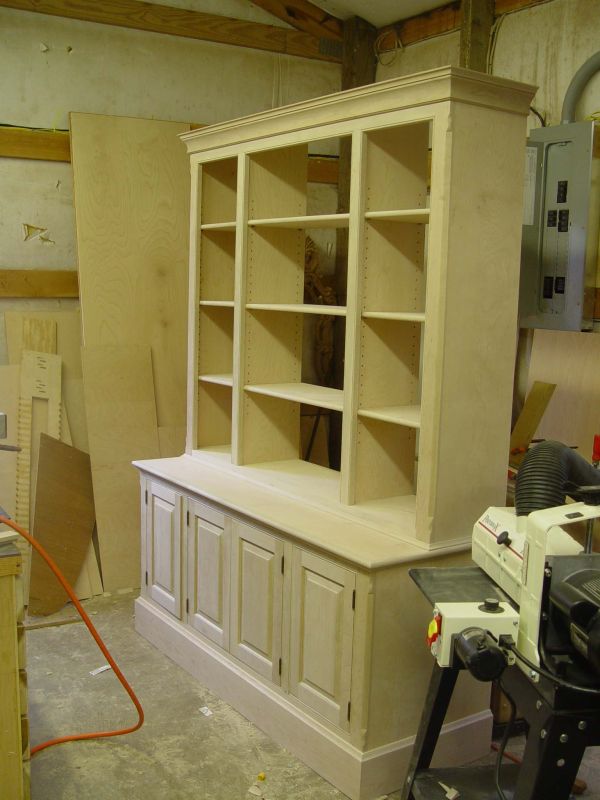
Click here for full size image
Forum Responses
(Finishing Forum)
From contributor S:
You would have been better off spraying the ultra penetrating stain first to get a good base color. You want to do light coats of dye, building to your desired color. Then tone, like you did, with the dye in the sealer or put the seal and stain directly over the straight dye and stain with a wiping stain or glaze. Spraying is actually quite easy, you just want to turn your pressure down and don't overlap your corners. The seal and stain is the same as the wiping stain - just no pigment like you thought. Also, if the dye is too intense, you can cut it with lacquer thinner or acetone.
From contributor M:
Paranoia is par for the course - you just keep going, and be sure to keep a record of each step. Think twice and finish once.
From contributor T:
Here is the recipe that I use for very dark colors on very inappropriate woods like maple and birch (don't ask me how I really feel - we do it, but I hate it!). The results are usually pretty good.
1) Using a good HVLP (very little overspray), spray on a good fast-evaporating dye of the appropriate color (requires some experimenting, but stick with a staple non-custom color as this base).
2) Using a precat, I mix up 25% sanding sealer and 75% thinner. Can be done with any clear. Spray a wet, even coat as a washcoat.
3) Sand nicely. Slop on the appropriate color stain as you normally do. It will not go on as dark with the washcoat, but step 5 will help.
4) Topcoat. Allow to dry.
5) Using appropriate dye toner and topcoat mix (per manufacturer's instructions), apply a toner coat.
6) Final topcoat (or do two more coats if you're using dinosaur NC or CAB lacquer).
This sounds like a pain, but believe me, it works well.
From the original questioner:
I did another sample today with the schedule I outlined, using glue size, but I used a thinned sanding sealer (3 coats) with the dye stain for a toner instead of putting it in the topcoats. The results were about the same and I could continue to tone the top coats as well to darken. Actually, the color is nice and even and would be acceptable to the customer. I have the luxury to experiment with this job and personally would like a darker brown base, using the toner to provide a red hue and not to depend on it to darken as well.
I think you're right regarding the dye as a base. I don't think it is possible to get the base color with a wiping pigment stain. I had some transfast dye, brown mahogany, which I sprayed on without a washcoat. I sprayed a fairly wet coat and got some blotching. Can I avoid blotching by laying down several light or hazy coats to build up to the color, or should a washcoat be applied? I have access to both transtint and transfast dyes. What dyes, solvents, washcoats would you recommend?
From the original questioner:
My cable modem is acting up, so I missed your post while I was composing my last. I agree regarding dark stain on light species. Throughout my career, if I wanted a piece to look like mahogany, I built it out of mahogany and thus avoided these issues. But being a glutton for punishment, I thought I'd confront it this with this job and educate myself in the process. So you would recommend an alcohol solvent dye like the trans tint? I must admit I’m a little uncomfortable with the water-based dye.
From Paul Snyder, forum technical advisor:
When I need a dark color on lighter woods, I usually apply the color in layers. There's a description of one process at the link below.
Related article: Dark color on birch and/or maple
From contributor T:
The only water-based dye I've ever used was regular ol' RIT from Kroger's. Use it on my woodturnings (a hobby - ever seen neon pink maple?). But as for our cabinet shop, we only use MLC's Microton, which is acetone based. I believe it is technically a "micronized pigment," but I can't say for sure. It's a top notch product and dries in seconds. Spray with dye, allow to dry for a minute (literally) and then maybe do a washcoat, sand, and stain. Or no washcoat, just don't use a very dark stain. To dial in the color, have a half dozen test pieces to play with. Add a measured amount of microton to a mixture of 50/50 of topcoat and thinner, and use it as a shade coat. You'll shoot this shade coat, watch it skin over (10 seconds or so), and immediately shoot a final coat of pure, clear unthinned as the final topcoat. Admittedly, the above process works best when the color isn't supposed to exactly match a pre-existing something in the customer's house.
From contributor S:
I can give you a good formula I use for a mahogany color. Burnt Umber Mohawk Ultra Pen. Stain sprayed on bare wood light coats, not flooded on. The more you get used to them, the heavier you can spray them, but it does take a little practice. Give it about 5 minutes, then spray either burnt sienna for a redder finish, or medium dark walnut for a browner finish. Mix the dye into your sealer about 1oz to 20oz. You don't have to use these exact colors, but they look absolutely great together. I usually do 1 to 2 coats of tinted sealer just depending on the look I want. Important... when spraying the dye straight on bare wood, you want to have your air pressure down pretty low. This will keep the dye from rolling off the corners, and prevent waste.
From contributor M:
Give this a try on a sample. First, stain the wood red. Use either a dye or a pigmented wiping stain. You should spray either one of these colorants. Then you can seal the stain, lightly sand, and use a red mahogany wood stain. Allow to dry, then seal, or you can use a shading stain to get your targeted color. You could also seal the stain, and then glaze out the pieces, seal the glaze, and then shade in your mahogany color if you need to. This same technique will works with other colors. Think twice, and finish once.