Making Miter-Fold Corners with Wood Veneer
Detailed advice on tooling and techniques for making miter-fold countertops with wood veneer on an MDF substrate. August 21, 2006
Question
I want to make some miter fold tops out of 3/4"standard hardwood veneer on flake or MDF, similar to what the solid surface guys do. Does anyone have any recommendations on tooling or any tips on depth settings, etc?
Forum Responses
(CNC Forum)
From contributor A:
We have done quite a bit of miter fold work using wood veneer on a variety of substrates and find that MDF cores seem to machine and fold the best. We have used veneer core stock and depending on the core it can either fuzz up terribly or tear out. Feeds and speeds are dependant on the tooling and the job at hand. We have found that we had to experiment with depth settings to keep the fold line from breaking when using different veneers. When you get it set up it works slick. Most major tooling houses have inserted carbide blade cutters and the point is what goes the quickest. Most cutters are ground for a slight overbend to allow for glue so it sometimes becomes tricky to close and glue the miter to a true 90 without the use of an auxiliary block.
From contributor B:
This V Groove tool is a stock item. As mentioned, use an insert type router. As the point dwells in the cut the tip becomes dull first. This insert tool has 4 cutting edges, which can be used twice, reducing insert costs. Also, you have no diameter or Z axis changes, once insert is reversed. Most firms use a tape on the underside, then fold and glue.
From contributor C:
We use the attached picture on a horizontal aggregate.
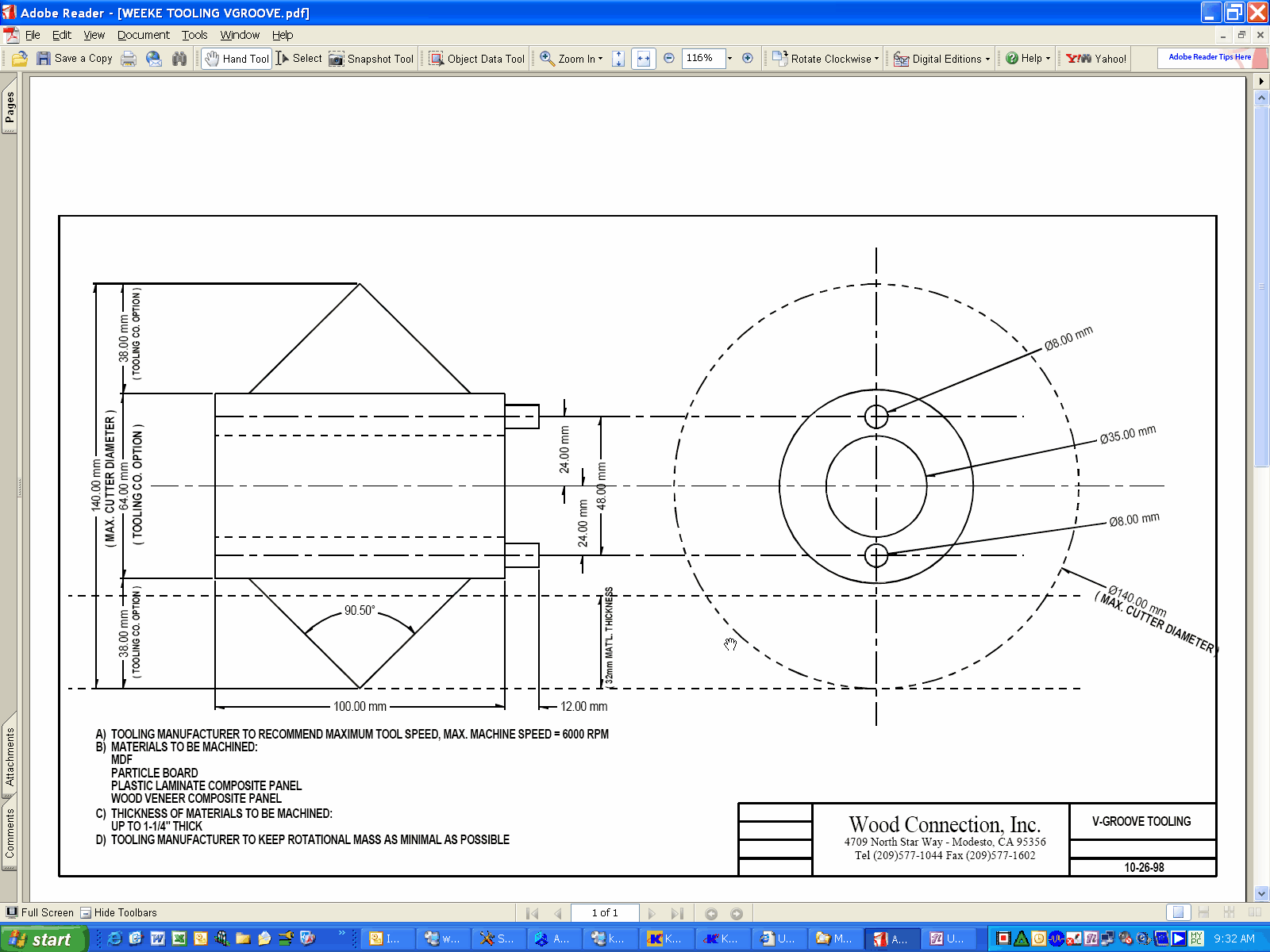
Click here for full size image
From the original questioner:
I thought an aggregate may be the way to go but for only two tops I can't justify the cost.
From contributor D:
If you purchase the right aggregate, you will be able to use it for many other applications on your machine.
From contributor C:
We used to use a specially made saw blade and with a tip on it and a router bit that didn't have a point on it. We use a pod and rail machine so a router bit with a point pushes and one pass pushes the spoilage down and runs the fold so we always did 2 passes. You can use that aggregate for cove splashes on solid surface and we also run bead board with a set of cutters
From contributor E:
I use all of these methods and all will work, but if it is for a few tops why not use a table saw? You will get the best result this way. If not, the two pass method with the cone cutter will be the cheapest and about .005"-.01" from surface will work best (MDF preferred).
From contributor F:
I agree. In our shop we miter fold MDF core maple, cherry, oak all with excellent results just using a table saw. Someone mentioned taping the backside so if you are going to have to tape it anyway, why not go ahead and use the saw? It gives you a beautiful corner, lightly sandable and strong. We use a panel saw to rip the pieces to general size and to get perfectly straight cuts. For MDF it seems like about 97% of the time it will give you a 1-3 mm banana cut. We always straighten these out before putting the miter cut on them with the table saw.
It is tricky - use plenty of glue, but not so much that it opens your corner when folded (should squeeze out the back) and use blue tape so that the veneer doesn't peel out or fuzz up. We use tape across the joint about every 16 inches and then a long piece down the full length. We also tape taught all the way around the piece about every two feet to hold the angle at a 90. If you take your time when making the 45 you shouldn't have a problem getting a new perfect 90 when folded.
Make sure you don't get banana cuts when you cut the material or else when you cut the 45, you have the same banana cut, and then when you glue, same results. If you are having trouble getting the piece to line up when laid flat and the cuts butted up, then most likely you have a banana cut on one or both pieces. This will give you a piece with a bow in it. On short pieces it is not so much a problem but on 8 footers, it is a big problem. This is so much better than the way we used to make fillers and wrap around end panels.