Natural Finish for Barnwood Table Top
Here's a collection of tried and proven recipes for finishing furniture built with reclaimed barn siding and framing timbers. April 15, 2013
Question
I recently started to build coffee and dining room tables from salvaged wood I get from my barn demolition business. Most everything I make is out of salvaged barn beams and 2" floor joists that formerly held up the hay mow. I believe the joists to be Douglas fir. The joists get planed a bit to take off the outer rough layer while still allowing some of the deeper character (saw mill lines) to remain. The picture is a typical top.
So far I've been using Varathane products, but I want to do a few in a more natural finish such as wax or oil for customers who don't want the thick plastic look. Essentially I'm looking to keep it as natural as possible with a decent amount of protection for moderate use. Probably won't stain it either. I've searched the internet for hours, and so far I'm just confused. There seem to be endless products and applications. Any recommendations? The easier the better, but if easy doesn't work, whatever it takes for a nice finish.
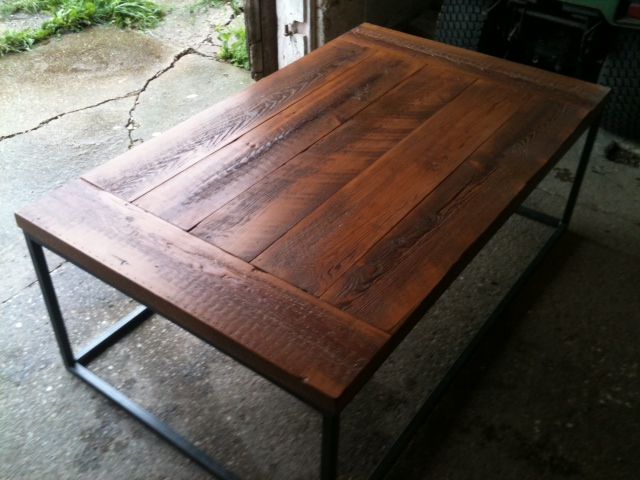
Click here for higher quality, full size image
Forum Responses
(Finishing Forum)
From contributor M:
As romantic as a natural, lovingly applied hand rubbed oil finish sounds, nobody is going to want to maintain it. Even the greenest of the green customers is not going to re-apply an oil finish as often as needed to protect their investment. You can play with Rubio Monocoat (12th century tech) real linseed oil, tung oil or anything laced with polyurethane, but they offer very little protection from every day use. If you do not mind watermarks, alcohol damage or hand oils, then have at it. I make a lot of money stripping that stuff off of next to new Crate and Barrel environmentally grown tables and spraying down a few coats of flat conversion varnish or cat acrylic. Then if they want to lovingly apply wax on top and call it natural, they can, but never will. This way their expensive feel good table will hold up to the kid's homework and not stain when the milk gets spilled on it.
From contributor C:
You can mix up a batch of West Systems epoxy and thin it with lacquer thinner, 3 parts thinner to 1 part epoxy. Brush this onto the table top and let it sit for about 5 minutes. Take a lint free rag and wipe off the excess until you have an even, flat appearance. Let this dry. If you use the fast cure catalyst in the epoxy, this should take about 4 to 6 hours at 70 to 80 degrees. Lightly sand with 400 grit no fill to remove nibs. You should lightly wash this down with a 50/50 blend of denatured alcohol and water to remove any residue from the sanding and epoxy flash off. Now spray a light coat of flat General Finishes water born super poly or Enduro var for a final finish. It will hold up just as well as any cv solvent product and give you a natural look. I've been doing it for years and the customers are always happy with the end product.
From contributor R:
I've used West System epoxy for years and for a myriad of things, but for wood, you should try Smith's clear penetrating epoxy sealer. I'm not knocking West at all, but from someone that's used both, you might find CPES easier and more effective.
From contributor K:
I have been finishing recycled barn wood tables for over 15 years. I use oil based
polyurethane for the table tops. The first two coats are Zar semi-gloss sanding sealer and then two coats of Zar poly in a flat sheen. I end up with a very low sheen, but not dead flat, with the seal under the flat. I very rarely stain this wood unless the customer orders a darker finish. I have never had a table top finish fail in over 30 years in the business.
From contributor P:
Contributors C and R, have you ever tinted the epoxy or applied a dye, maybe even a stain, to the wood prior to the epoxy coat? I have made harvest tables where the clients want something other than natural looking wood and used dyes/stains under CV or wb equivalent. Another option is always nice.
From contributor R:
You can do almost anything you want under the epoxy coat as long as it is given adequate time to cure/dry before sealing it. Remember that both CPES and thinned West System will penetrate the wood permanently, more or less, and provide a barrier to moisture. I have put West on keels that have not been pristine and it stuck like crazy. I have reconstructed rotten transoms and gel coated them afterwards and they were like new. So, yes, do what you want before the epoxy, but don't try to tint the epoxy - it won't allow you to adjust the color during application. Nor will it allow correction afterward unless it is opaque color.