Pitch Build-Up When Planing Air-Dried Pine
There's no way to stop Pine pitch from gumming up machinery, short of kiln-drying the lumber. (This thread has some interesting asides about using your own sawn wood for construction.) April 27, 2011
Question
I'm running a load of air-dried pine through a surface planer and after only a couple boards, the metal plate on the planer gets loaded with pitch and the boards have to be pushed through (with some effort).
I've tried using paste wax on the plate, but nothing seems to stop the pitch buildup. Acetone seems to work pretty well for cleaning the pitch, but is there any way (besides kiln drying) to reduce the pitch buildup?
Forum Responses
(Sawing and Drying Forum)
From contributor T:
Not that I've ever heard. Until you set the pitch, it is going to be relatively soft, and there's nothing short of making it hard that will prevent it from gumming up on the knives/inserts. On top of that, planing it heats it up and softens it even more.
From contributor D:
You really should dry it. Who would want to use it and have pitch oozing out of it for the next 20 years?
From contributor F:
If you adjust your bed rollers up about a sixteenth, possibly a bit more, the pine will feed through easier. Can't help on the pitch problem.
From Professor Gene Wengert, forum technical advisor:
Maybe this explanation will help. There is sap (or resin or pitch) in the tree. Some of this sap is soft, sticky and runny at room temperature. More of it gets soft, sticky and runny as the temperature is increased. However, the sap that gets runny at elevated temperatures will get hard again when it cools.
In your case, the machine is apparently heating up the wood a bit, causing the sap to flow out. When the wood is gone, the metal cools and some of the sap hardens. Heat it again and it will soften.
As mentioned, if the wood is dried at 160 F, the sap that is the most troublesome will be evaporated. What sap is left will be hard at room temperature and at elevated temperatures, but will soften as it gets to 160 (give or take).
As mentioned, opening the feed a bit (less friction and less heating) will help, but if the piece can chatter or does not feed, then we will have new problems. A coating on the steel is not going to help too much as the resin will deposit on any warm surface and then harden on any colder surface (maybe not a non-stick coating, but I do not know if they coat planer tables with that).
But the key to preventing this problem is to have the wood heated in drying. Mineral spirits might be safer for you than acetone as far as cleaning. Also for cleaning, the warmer the surface, the easier (but do not use heat with an explosive or flammable solvent, obviously).
From the original questioner:
Thanks. It also seems to help to avoid the sapwood boards and use them for sheathing instead. I realize that kiln drying would reduce pitch problems, but if I was afraid of a little pitch, I wouldn't be in the wood bidness. In the past, I have had the local mill plane all my air-dried pine and it seems to work just fine for house construction. Here's my current project. All lumber is from my logs and sawn on my bandsaw.
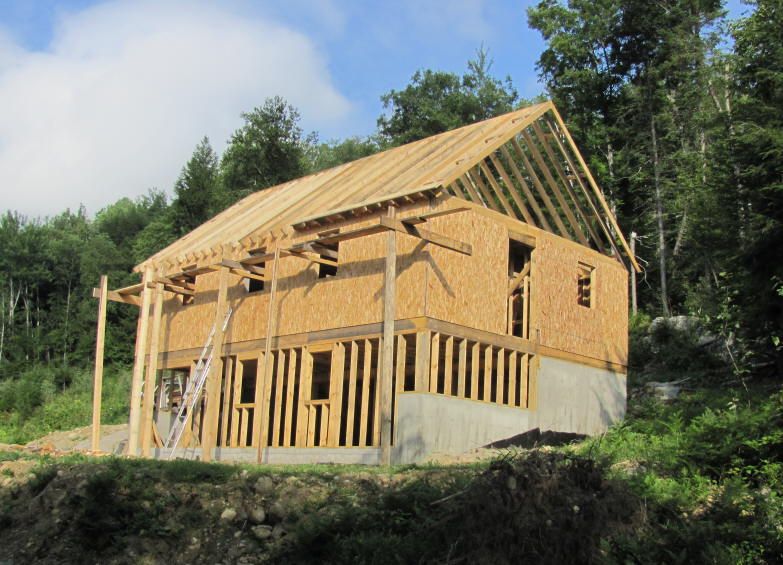
Click here for higher quality, full size image
Here's a shot of the house with some of my lumber that was planed and primed.
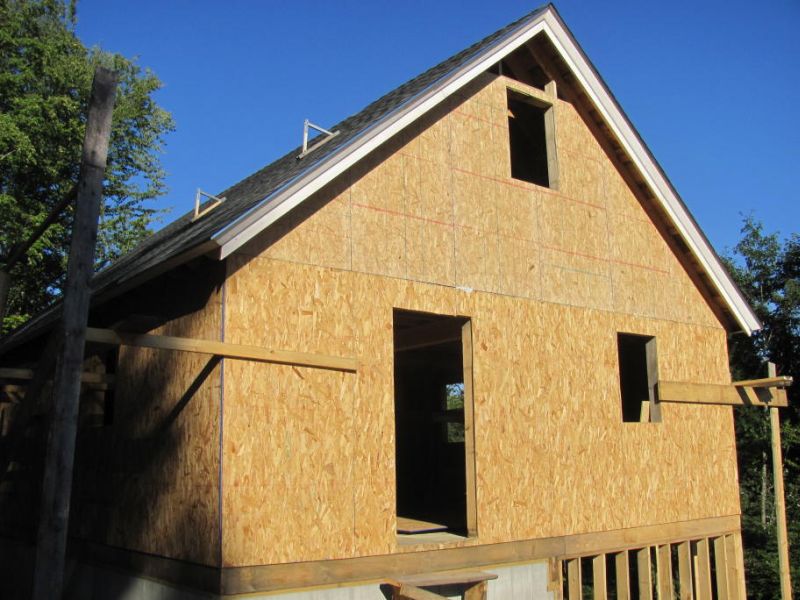
Click here for higher quality, full size image
From Professor Gene Wengert, forum technical advisor:
How do you get this to pass the building inspector?
From contributor T:
Looks like he's in a rural area. In my unincorporated rural location they won't come out to inspect any building construction even if you ask. They do enforce the regulation of septic systems and will send out a county inspector for any new septic system that is installed, but that is it. If I wanted to build a house out of matchsticks, I could. Could not get it insured, of course, but I could build it.
From Professor Gene Wengert, forum technical advisor:
I have seen them inspect in rural VA, GA and WI for graded lumber.
From the original questioner:
Yes, there is no building inspector in my town. Though, if necessary, I can hire a lumber grader. He happens to be the guy who sold me my sawmill. We do have to get a state-approved septic system and have it inspected prior to backfill.
From contributor S:
I didn't know waferboard trees grew that big to yield that size of boards! Nice looking pad. You are very lucky not having to deal with inspectors. So, maybe having troubles with pitch while planing was your small price to pay for no inspectors.
From the original questioner:
Yeah, I hated to use OSB, but the price came back down to $7 per sheet, so I gave up the idea of sheathing it with boards. I did use boards to sheath the roof though.
From contributor S:
On the topic of planing: Does your planer have a bottom roller that can be elevated? If so, raise it and it will reduce friction/heat on the table and the pitch will not soften as much.
From the original questioner:
No bottom roller. Just a cheap 13 inch Ryobi. I usually just have the local pine mill plane my boards for $250/MBF, but I needed to make a small amount of odd-width stuff that I wanted to plane up before I put the windows and doors in. The local mill will also plane my 1x8's into a single board that has two 3-1/2" clapboards and a shiplap joint. They look just like clapboards, but go up quicker and are much thicker.