Radius Moulding Machinery Choices
Millwork pros discuss shopping for a radius moulder and the related knives. January 9, 2008
Question
Does anyone have experience with the Micron M645 radius moulding machine? I am looking at purchasing this to do radius mouldings with standard knives and custom knives, versus buying a CNC machine. It looks like it will produce a nice product. Any secrets to making the best radius moulding and jambs?
Forum Responses
(Architectural Woodworking Forum)
From contributor D:
I have used the 645 and I own a 652. The difference is night and day. If you are going to spend that kind of money, spend a bit more and buy the 652. The router feature on the 652 opens up so many milling operations that just would not be possible any other way. As for creating radius mouldings, it works great with very little setup. The floating table allows the stock to pass under the head without binding. With that said, the real challenge is creating the blanks. CNC router is the tool for that job.
From the original questioner:
I have been reading about a lot of different methods for making the blanks to do radius mouldings. What methods do you use? Do you laminate or scarf, and if you glue wide boards up, scarf the end and then cut out blank with bandsaw? Do you get a nice piece versus laminating pieces together? I will check into that other model. I was thinking the one with the router might give me more options later also.
I am also looking for some advice on a small moulder. I have narrowed it down to a Woodmaster and Logosol ph260. This is what I would start out with. Once I got going and business got busier, I would look into a bigger machine. What are your thoughts?
From contributor D:
When it comes to making the blanks, I like to scarf the joints, but I always let the customer make the final decision. The problem I have with bent lamination is the spring back. As for cutting the blanks out, it depends on how many have to be cut. If it is more than six, I job it out to the CNC guy. Otherwise, I cut them on a pin router by calculating the radius and creating a pivot point. I always make a plywood pattern so I can use it again latter. If you cut them out on a band saw, you will have to sand the edges and keep in mind that any variation in the cut will show up in the finished profile. If you go with the W&H, pay extra to get the edges corrugated so they will fit in a conventional moulder 16/60. I think the Mikron is your best bet. It will mill round or straight mouldings. If things pick up, you could buy a multi head machine and keep the Mikron for all the radius work. Also, a straight line rip saw is a must if you are going to do a lot of moulding.
From contributor B:
I had this same conversation this morning with someone who bought a Micron 645. I would seriously consider choosing the US Concepts (Fortis Machinery) machine over the Micron. It offers a much more sophisticated design for the same amount of money.
We use modified W/H moulders day in and day out and I know of other exclusively radius shops that do the same. We're talking thousands of mouldings a year here. There are definite advantages (not just cost) to using the W/H moulders for radius work, versus either the Micron or the US Concepts.
From contributor M:
What are the advantages of the W/H for radius work? I've looked at the US Concepts and am familiar, but would love to hear your take on it. My main concern is different knives, W/H versus corrugated.
From contributor B:
I've made no secret here over the years that I'm a fan of the W/H moulders for radius work. They will do everything (with some clever modifications) that can be done with the big units, including curved crown.
The major advantage of the W/H moulders over the Micron and US Concepts is the cutting diameter of the head. For radius work you want as small a spinning knife circle as possible. The W/H will give you somewhere around a 5" to 7" (point to point on the two knives) overall diameter on your cutting head. This means that as the wood curves below the spinning head, the distortion is less than if the head were larger.
The large moulders start with a 4" diameter head to accommodate the spindle shaft and the corrugated knives. This can put you out in the 6" to 8" cutting head diameter range, which will give significantly more distortion to your profile than the smaller diameter head as the wood curves below the spinning knives.
You have to remember that all moulders are inherently designed for straight run mouldings. The heads spin cleanly above wood traveling through below it in a straight line. Curved work by its very nature stresses this environment. As the knife edge approaches the bottom center of its cutting arc, if wood is curving in and out as it passes below, the knives will hit wood before the knives come to bottom center of the cutting arc. This results in distortion to the profile. The larger the cutting arc of the moulder head, the further away from bottom center it will hit the wood, and the greater the distortion.
For mouldings that have a radius of 12" or greater, this is all little more than theoretical discussion, as all the machines will give a cut very close to what is desired. The difference is when you get into the very tight curves. We can cleanly go down to around a 5" radius on the W/H... even with a typical 3/8" bead on the inside edge of the moulding.
The one major downside to the W/H for curved work is the fact that the overhead rollers are pushing the wood straight while it is trying to go through on a curve. This leads to a battle between the feed rollers and the centering bearings.
What I really like about the US Concepts machine is the floating outrigger feed rollers. These will float with the shape of the moulding on either side of the cutter head. A very nice feature held over from the earlier $30k+ US Concepts and Steherr arch moulders. Enough to justify the cost difference between a new W/H and a new US Concepts machine, though, I doubt.
The Mikron took the one negative feature of the W/H - the straight drive feed rollers - and used it as the basis for the design of their machine. That is the main reason I've always preferred the US Concepts over the Micron.
From contributor M:
Thanks for the detailed response. I take it you don't do straight runs, or at least large straight runs. The only downside I see is having to have two different sets of knives. The positive being able to run small radii.
From contributor D:
I think contributor B hit the nail on the head when it comes to the W&H. I had one and it was a great tool. The only reason for switching over to the Mikron for me was I do a lot of radius work for other shops that run miles of straight moulding. I needed a machine that would accept the knives from their machines. I too looked at the US Concepts moulder and liked the feed system as well. I chose the 652 Mikron because of the ability to remove the moulder spindle and replace it with a router. This option allows you to create almost any profile with just a few router bits. This is great for short runs and samples without having a knife cut. Contributor B mentioned profiling a small radius with a bead on the inside. I had this very problem last week. A 3/8 beading bit mounted in the router and I had no distortion.
From the original questioner:
Wow, what a lot of good information. Can I use the same knives on the W&H on either of the Micron 652r or the US Concepts moulder? What do you use to glue laminate boards or make the blanks for the arch mouldings to be made out of? I see US Concepts has an arched glue rack. Would that work? Otherwise, how do you guys glue boards up? Then the next thing would be me trying to find the best price for these machines that also has great customer service too. Do have any suggestions?
From contributor D:
I have a head for the Mikron that I bought from Schmidt that will work with the W&H knives. You can also buy the knives with both the W&H hole pattern and the 16-60 corrugation. As for the glueup, I make a plywood form. I think the rack takes up too much space in the shop and you can only do a few arcs at a time. As for price, the W&H is the best at around 3k. Mikron is around 20k and US Concepts even more.
From contributor B:
I guess prices have gone up a bit since last I looked. I thought the Micron and US Concepts small machines were around the $15,000 mark... and the W/H closer to $2,000 the $3,000. Oh well - inflation hits everything!
Just curious, the router mount on the Micron... Is that for mounting one horizontally or vertically? I didn't notice that feature on the machines at the shows.
As to knives, contributor D is right. You can get what I call corrugated/combination knives made by any of the shops that grind W/H steel now. The W/H knives bolt to the machine while all the others use conventional corrugated steel. The combination steel is corrugated with W/H bolt holes... a great idea which we use a lot. The only downside is that it is 1/4" steel versus the 5/16" steel that most guys prefer to run on their large straight run moulders. For short runs, though, most shops will put the 1/4" corrugated in their machines. Thicker steel though makes for a safer run.
From the original questioner:
If I get the W&H machine, I probably should not buy too many of their knives because they would not fit in the other machine. Who has the best price, service, quality, and selection of standard knives? Otherwise, do all places make them to fit both machines? Also, when I get the knives, I should get a couple of extra heads too? If I remember right, most of these have a 2-knife head? I see most people recommend running two knives versus one knife for quality. Is that correct? I figure I will need to spend a lot of money on knives to be able to get started and have a good selection for customers to choose.
From contributor K:
I have owned a Mikron for years and have had great luck with it. Mine predates the router option, so I can't comment on that feature. We do a lot of straight moulding so the ability to use our standard corrugated knives is huge. Contributor B is of course correct - the larger swing of the head can cause problems depending on the profile and the radius. The ability to easily tip for most crown profiles with the Mikron made it our go to machine. I do own a W/H machine that has been relegated to storage because the shop just was not using it. The issue of generating the different knives is probably the biggest thing even with the fact that we grind our own internally. The combo steel corrugated and W/H just does not seem to perform for the standard molding runs, so we quickly gave up on that. I do have the luxury of having a CNC that we use for a fair amount of 3D profiling for large and complicated profiles, and also for prepping templates and patterns. As I'm thinking back, I at one time actually shoved a lot of radius pieces through an old 12" Belsaw. The beauty there being only a single knife.
From contributor B:
I use CT Saw and Tool here in Connecticut. Who you use will depend on where you are located, although they all will UPS tooling anywhere. I would suggest if you get into this on a regular basis, you use someone who is one day away for UPS delivery.
As to the combo steel, I suspect it is not as high a quality steel as some of the best that is out there. I don't recommend it for long runs anyway... only if we have curves to make and someone else needs to run a few hundred feet of matching straights.
Two knives always on the W/H. It's a fixed head machine so there is no keeping a second head on hand. I've replaced just about every working part on our Husseys over the years but have yet to wear out or break a head.
Having also owned an old Belsaw years ago and traveled down the "1 knife" road, I can tell you that unless I only needed 10 to 20 feet of moulding, I would buy the 3 knife set for that machine anyway.
From the original questioner:
So if I understand, if I bought the W&H and the Micron 652r and needed to do a couple of radius 1/2 round 3-1/4" casings, the knives for the Micron will need to be adjusted slightly because of how the wood feeds through the machine due to the radius? Or is that only for smaller radius, say a radius diameter of 5' or 6' versus a 2-6" or 3' radius? The tighter the radius, the more it is distorted because of the sharpness of the radius?
Contributor B, of the two machines mentioned earlier, would one be better for smaller radius than the other? In our market area we see a lot of different sizes of casing, from 2-1/4" up to 4". As for base, we see anything from 2-3/4" up to 6-7". Would I be able to make such trims with the W&H and the Micron 652R? What about doing larger casings for customers who request radius casing? Would I be able to produce a nice quality trim piece?
What are the sizes of knives for casings/base for the W&H and the Micron or US Concepts arched machine?
From contributor K:
Lots of questions and BH can probably elaborate better. The WH has a very small diameter head, which means a smaller cutting circle hence tighter radii. Your knife cuts in and drags out of the profile at a longer length depending on the cutting circle. This is a problem with profiles that have deep vertical shoulders and not so much in flowing shallow profiles. I can't give you a minimum diameter because it really depends on the profile.
If I had to suggest a machine for an upstart guy, go with W/H, learn the ins and outs, and then move up to a larger machine. Purchase your knives with the W/H corrugated combo and then you're covered. Both the Mikron and the W/H will give you good finish quality.
My referring to the Belsaw was not a recommendation, but suggestion that there are many ways to get to the final destination, and you could get in to radius work for next to nothing. The single knife can actually give a decent finish because the feed rate on those machines are typically quite slow.
From contributor A:
I have extensive experience with both the W&H and Mikron. These are the machines that my family has made a living with for 20 plus years. First, the W&H is a great machine that will make just about any moulding that you will come up against. An advantage is the small cutting circle. A disadvantage is that the feed rollers do not raise and lower separate from the cutterhead. Because of this, you will have to hog off material by some other avenue. The other disadvantage - slow!
Back in the early 90's I was getting tired of working way too many hours and started looking for other machines. I went to a demonstration of the US Concepts machine. I took a large piece of moulding with me that I needed 300 arches made to match. I was told that this was not possible with this machine due to a large cutting circle. This job was completed on the W&H.
Years passed by and we always discussed what we wanted out of a machine. We came up with the criteria that consisted of a bigger W&H with a bigger motor and adjustable feed rollers. While in Atlanta at IWF we came across the Mikron. Looked at it for about 30 seconds and left. We had one up and running less than one month later.
The first run I did with it was a large order of casings. These were big nasty casings with a depth of cut of 1 5/8. This would have taken days to finish on the W&H. This job was completed in one day with the Mikron. I could not have been happier. I may profile as many as 100 casings in a day.
The Mikron is on an equal playing field with other big machines when it comes to minimum cutting circle. On the other end of the spectrum, it swings 3 inch knife stock much safer than the W&H and you don't have to hog off any material to make the feed rollers touch the stock.
Two aspects that have not been discussed are speed and cost to operate. While the W&H cost very little on the start compared to the Mikron, the W&H will cost more to operate in the long run due to its slow speeds, which directly affects labor costs. The more arches you have to make, the more this shows up. A run that would take 4 hours on the W&H may take 1 hour on the Mikron.
From contributor D:
The price for the W&H was including the elliptical jig. The Mikron 645 is about 15k but the 652 is more (or maybe they saw me coming). As far as the US Concepts, I just assumed it was around 30k. The router for the Mikron is vertical but can be tilted to 0 to 52 deg.
From contributor B:
Thanks. The US Concepts machines used to be $30k just like the Stegherr BOF. However, when Mikron came on the scene, the owner of US Concepts had to come up with a new lower cost design in order to compete.
You can still buy a $30k megaton machine from them, but the $15k unit looks good and solid to me. I've seen it running at shows a number of times. Of course, hands on could be another matter.
If the router mounts vertical on a Mikron, how does that help in running an inside bead? I can see how a roundover bit will do the inside edge, but the outside edge would still be square after a 1/8" bit was used to make the parting slot. How do you round over the outside (towards center of profile) edge of the bead with the router? Or do you cut that with knives and only round over the inside of the bead with the router bit? This, though, would lead to blowout on the tpy 1/8" wide parting slot.
I figured the real advantage to a router mounted to a machine would be for the bit to be horizontal so router bits could work just like shaper cutters, but with a significantly smaller cutting diameter. Vertical, I guess, does present some interesting possibilities, but nothing we couldn't already do on our CNC. I'm not a fan of running mouldings with router bits unless it's a custom bit that covers a whole moulding (or at least half a moulding - 2 bits for the whole moulding, one from the left side and one from the right side). Or of course, ball nose bits cutting 3D profiles on the CNC as well.
From contributor D:
The profile was a 4 inch casing. We had a lot of straight and quite a few small rounds. This is what we did. I had a knife cut to produce 99% of the profile. At the inside edge was left a small amount of stock sticking up (a picture would be worth a thousand words here). I then switched to the router with a round over bit (the bearing on the bottom and the threaded stud were removed) to profile the inside. This left only a small amount of material to work with, too small for a handheld router. I then installed a beading bit with a bearing on the bottom to profile the outside. The nice thing about the Mikron is the table floats, so the bearing could ride along the bottom edge and not leave any bearing tracks. If I had a CNC, it probably would have been easier.
Another profile I did was 5" wide 3/8 round over on each edge and a V groove off to one side about 150 feet. It would have been expensive to cut a knife. Of course, I had to push it through 3 times and change the bit. I also do some work for a local lumberyard and run the slot in the edge of the exterior decking for the plastic biscuit fastener. I guess I could do this on a sharper, but I have a large infeed and outfeed table on the moulder, so it is easy to run long heavy planks. I also can profile the tops elliptical base board.
From contributor L:
We make quite a few curved moldings on a Stegherr that I bought at auction for $2500. Put about $400 in new parts in and it has run very nicely since. I'd like to have the big (8") US Concepts to run bar rail and the like, but have other things to spend money on. Many times we run the same curved and straight moldings, so being able to use the same knives on the Weinig is a big plus. It also means we can quickly turn out a set of knives on the profile grinder. The Stegherr will copy whatever shape of stick you put in ("S" curves) and feeds quite well, since there are 4 feed rollers that float in addition to the rear feed roller. Fortis improved on the Stegherr design with their vertical hold down rollers, the option of two additional top feed rolls and tilt head.
Most of our curved moldings are strip laminated. Strips are cut with a straight line rip saw, then glued on an adjustable form. The curved blanks are wide belt sanded to thickness. The shapes that can't be done on the adjustable form are done by cutting male and female molds on the CNC and putting them on the clamp rack. We also keep a shaper setup to do finger joints. By keeping the parts in order as you cut them from the board, you really can't see the joints in the completed molding. Clamping ears are cut on the parts and after the glue dries, the curves are cut on the Komo. The straight-line-rip leaves an excellent glue surface and we keep the parts in order there too. Curved base is done on a heavy shaper with MDF guides cut on the Komo. You can run straight moldings on the curved molding machines but they are very slow and you have to spend a lot of extra time prepping stock and unless you run a back-out cut first (another slow handling), you will get complaints from the trim carpenters.
From contributor M:
Contributor L, I'm thinking of getting an arch moulder and would probably get the US Concept, I just haven't had the right job come along to push me into buying one yet. If you have made 3" casings with your blank coming off the adjustable form, how do you handle it when the blank comes off at 3 1/16"? Is there a secondary step before going into the moulder, or do you handle it after it comes out?
From contributor L:
The guys are pretty good at hitting the size after doing hundreds of them, but I've seen them sand a little off on the edge sander.
From the original questioner:
Can the knives of a W&H moulder also fit in the US Concepts? I have also looked at the Micron 645 and 652R but it might be out of my budget. I have just received some information from US Concepts and their machines look great as well. I am still waiting for the literature from Micron to make up my mind. The biggest thing would be being able to use the same knives in the W&H machine as well as the arch moulders.
From contributor K:
Just to wet your appetite, here is a crown being cut on my router yesterday. It was already roughed out and is making the finish pass.
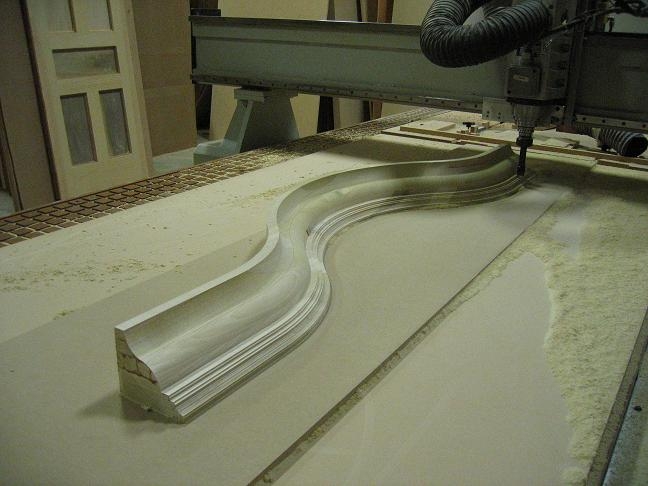
Click here for higher quality, full size image