Red Cedar Grain Patterns
A craftsman gets advice on sawing techniques for achieving beautiful book-matched grain effects. June 22, 2005
Question
I am trying to build guitar and music stands from the purple heartwood of dead cedar. After cutting it into usable sizes, what is the best drying and finishing method? To book-match an 18"x12" panel, how large of a block should I start with, and how thick should I make the panels?
Forum Responses
(Sawing and Drying Forum)
From Gene Wengert, forum technical advisor:
Have you done this before? Do you know that exposure to light will cause the purple to fade to a red color? Are you going to book-match edge to edge or end to end? If you book-match edge to edge, and the width is 18", then you need an 18" block.
From the original questioner:
Gene, my experience working with cedar is limited to small carving projects. I do know that it fades. Is there a way of minimizing the fading? I want to try to duplicate a book-matched panel on an old hutch door. I’m pretty sure it is made from a solid block and sawed 4 times. It looks like it was sawn once and flipped, and then both top pieces were sawn again and flipped down. I have recently gotten access to some beautiful wood and want to try this. I need to know how long to dry it as well. I was also wondering, since it has little or no sap/moisture, is there special handling involved?
From contributor S:
To the original questioner: Is this similar to what you are looking at doing?
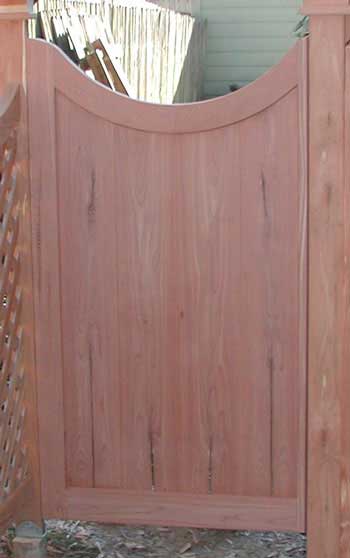
From the original questioner:
To contributor S: That’s not quite what I have in mind, but I may not be precise in my definition of book-matching. The pattern I want to duplicate is as if you sawed a 4x4 post with the heart of the wood at the bottom right corner (the grain rings getting larger toward the top left), flipped the first cut to the right, then sawed both pieces again and flipped both down. The pattern would look almost like a rose flower. At that rate, a 4x4 should end up 8x8 (I guess I still haven't done it). How long did you dry your wood to keep it from checking, and what stain or finish worked the best for you?
From contributor S:
To the original questioner: Are you saying that you want the rings to show on the surface? If so, saw it no more than 1/8" thick, and laminate it to something stable - plywood or MDF. You may also want to stabilize the wood to avoid cracks. This could be done with thin CA or epoxy.
I've had good luck sawing end grain slabs with ERC by cutting it with a 15-20 degree bias. The picture I posted is natural - no finish. It will eventually turn a silvery color.
The only way to keep the color of ERC at all (it won't stay purple - just red), is to coat it heavily with spar urethane or spar varnish. Even then, it will do best if kept out of direct sunlight.
From the original questioner:
To contributor S: The pattern I want to duplicate does have the rings exposed, so it makes sort of a flower pedal pattern. You mentioned cutting on a bias - does this help prevent cracks or is it for strength or looks? How long should my block dry before sawing into slabs? I've already noticed the fading on some experiment pieces. Have you tried Tung Oil to seal? It seems that fresh cut live ERC holds the red center color better than the dead that the pulpwood is gone from. I appreciate all of the help.
From contributor S:
To the original questioner: The cutting on the bias does help immensely in keeping the piece together, and would work well for the pattern you are trying to create. I'd cut it the same as you have it. It should dry real fast anyhow.
Tung oil will make the red much deeper, but it won’t do anything to maintain the purple color. Really nothing will, as its fading is due to exposure to both light and air. The way I'd go after what you want is to wedge a 2-3' length of the cedar in between the bunks of my Woodmizer at a 80 degree angle (end of log sticking up), and saw biased cookies 2" or more thick. I'd then square the cookies on the bandsaw, turn them on edge, and re-saw them at the thickness desired (1/8" - 3/16") to glue up a stable substrate (plywood/MDF).
Once it’s glued to the substrate, I'd use a cabinet scraper or ROS to level/finish it (paying attention to the direction of the end grain/bias if scraping), and lightly scrape or fine sand again immediately before finishing with a UV blocking spar varnish/urethane.