Repairing a Rusty Spindle Taper on a CNC Machine
Cleaning off rust is doable, but more severe pitting could cause trouble. September 23, 2013
Question (WOODWEB Member) :
Is there such a thing as a taper "reconditioner"? From the image below the rust extends about halfway into the taper. It is not bad but there is some light pitting. I know about the spindle wipers so is there something a bit more aggressive? I am thinking the worst case scenario is I use a taper wiper to remove the rust and leave behind the light pitting.
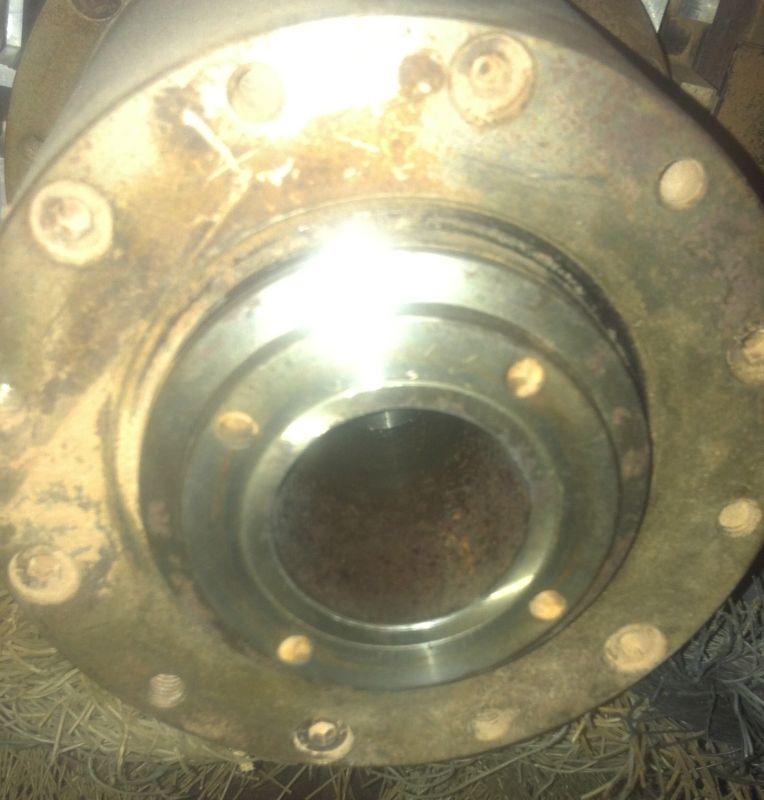
Click here for higher quality, full size image
Forum Responses
(CNC Forum)
From Contributor M:
I’m not sure if a taper wiper is going to remove all the rust. You could try a scotch pad. Have you checked your air supply for moisture? Perhaps covering the spindle nose overnight after the shift would be a good idea. Moisture is never a good thing as it could get into other parts of the spindle (bearings). Ultimately a re-plating and grinding of the taper may be best but if you can get rid of the rust without affecting the overall performance of the spindle you might be lucky. Make sure too that you’re not putting rusty tool-holders into the spindle.
From Contributor J:
If this was mine I would look into a shaft kit to include a new draw bar as you could recondition it with the wiper unit but you still will have the pitting. It could run for years that way but it could also have become weak with the runt eating at the metal and crack after ten hours of use. As far as I am concerned nothing to mess around when spinning at 18,000 rpm and trying to cut material. I’ve only seen them come loose once and caught it before it dropped out. Typically the shaft is split and has a lock nut holding it together. Also I have usually only seen this in very humid conditions or a liquid chilled spindle that is not adjusted correctly at all (set too cold with major humidity in the air).
From Contributor M:
Contributor J has a good point but it will cost you more than $500 to replace the shaft kit in what looks to be a 10hp long nose HSD spindle. Certainly safety is a priority and the condition of the drawbar should be a priority as well.
From contributor D:
If it was mine I would just contact some 600 grit to an ISO tool holder with the pull stud removed and ream out the rust a bit with that. I would not try to get the pitting out as it would remove too much metal - too high a chance of changing accuracy.
A lot of the older tapers such as Morse, etc. were roughed out on a lathe and then a reamer of the right size was used to clean it up. I made a lathe that way once myself. I am sure not as accurate as grinding but it should be fine especially if the rust and pitting are even all around.
From the original questioner:
The humidity here is off the charts. In fact there is not even a word in the local language for "humidity". The nearest word is "hamog" which means fog. I think this is because it is always 90%+ RH. This machine has very low hours on it but every hour was likely ran with no dust collection and no water filtration on the air supply. (I drain more than a gallon from our 5 HP compressor every day). I suspect the machine was left sitting without tools in the spindles for extended times (as in years). The tool holders all look ok, no rust at all. I will clean up the rust and see how it goes from there. We are not doing any heavy cutting so I think the spindle will be ok.
From the original questioner:
It is not my machine so all I can do is pass on the recommendations. I think I understand the function of the drawbar, but perhaps not its importance. Can someone point me to a source of information regarding the function and details of the draw bar? Is this considered a "wear part"? I have heard of tools that measure the drawbar force, is this adjustable? Also do any of you have pictures of a failed spindle and the aftermath?
From contributor K:
The wiper cleaners work well for topical rust. With due diligence and effort you can reclaim the surface of the majority of the rust. Pitting is another matter, and the degree of pitting. Over time the pits transfer to the tool holder, which then create more pitting on the ground inner surface of the spindle. Consider it a downward cycle.
Over time this cause balance and bearing issues. A less costly alternative to field replacing the spindle cartridge, or replacing the spindle all together, is have a qualified spindle repair shop come onsite and regrind your spindle taper to the relevant taper specifications. The drawback for this is if the pitting from the spindle has transferred to all of your tool holders, eventually it will transfer back to your new, reground, or cartridge replaced spindle. Spindle maintenance starts from day one. Following a proper tool holder, collet, and spindle taper maintenance regimen can greatly reduce if or when pitting and rust happen.
From Contributor M:
The drawbar itself is not so much a wear item as are the drawbar fingers (grippers) and springs. I suspect that with all the moisture you may have some problems with the air cylinder in the back of the spindle being possibly contaminated. The air cylinder pushes the drawbar forward to release the toolholder, the springs on the drawbar forces the drawbar back into the spindle when the air is released thereby clamping the toolholder into the spindle. The grippers grab onto the pullstud of the toolholder and these are adjustable.
After cleaning the taper I would do some test runs of clamping and unclamping tools and warm up the spindle slowly to higher speeds (do not run the spindle without a toolholder in it). I have attached a link for the HSD spindle manual I was able to find online. After not running this spindle for a long time it may be a wise investment to have it checked completely by a service technician. Perhaps at minimum replace the shaftkit as was suggested.