Sawmilling, Work, Love, and Money
Here's some thoughtful discussion about work, the love of work, and the value of money, set off by a posting from a guy who misses his sawmill. January 25, 2010
Question
Approximately a year ago I had the opportunity to sell out. At the time I made a good decision! I was burnt out from working 80 hours a week. I now miss the business! I don't want to own another mill. Does anyone have any ideas how to get back to what I love?
Forum Responses
(Sawing and Drying Forum)
From contributor A:
Yep! You come out to my mill and I will work you for a week and then you will remember why you sold out and be thankful.
From contributor X:
Get into another sector of the business. Take some forestry courses and get into consulting landowners. In addition to that, find a young kid who is struggling to make it in the business and needs some direction and maybe even some sweat help. Labor is good for the soul. We are not designed to sit around twiddling our thumbs it is proven to be very unhealthy for our mind, body, and spirit.
From contributor B:
Do you guys sell online and ship the slabs?
From contributor A:
Yep!
From contributor H:
Are you guys just grade sawing, or doing custom work? I'm in northern Wisconsin. We saw for our mill and also go out to sites for other people charging $70/ tach hour. Any given year I'll saw about 4-5 hundred thousand feet. Regarding the blues, if you love doing it, keep doing it.
From contributor B:
What’s a tach hour?
From contributor L:
I would assume he means hours on the meter.
From contributor X:
Tach is short for tachometer. It's a quick way of saying unless the engine is running they are not charging the customer for time "at the job site". Some mobile sawyers start the clock when they pull out of their driveway and some have a "set-up" fee or "trip charge" and as stated some start the clock when they arrive at the job site.
I assume contributor H is saying they do not charge any of these ancillary fees and still make good money charging just for the actual sawing. Putting ten hours a day on the meter at $70/hour is good money, but in my opinion you could not charge any less and still cover overhead and the plethora of confiscatory taxation, especially in Wisconsin where I understand the cost of living and taxation is rather high.
From contributor S:
I've been in the lumber business for more than ten years and I'm skeptical about putting 10 hours "on the meter" on a consistent basis doing work for clients with small amounts of wood. How many people even have enough logs to keep a decent sawmill busy for ten hours? But I agree if you charge less than $65 or $70 an hour you are just spinning your wheels and not making much profit.
From contributor H:
We do have a minimum charge of $280 but four hours of sawing takes care of that. Most jobs are 6-12 hours. We don't supply any help or equipment - just the mill and sawyer. At our mill facility people bring logs to us we then charge by the b.f. only because it's easier to figure when we k.dry and plane their wood. To make any money in the wood business you need to do secondary ops.to wood such as kiln drying and planing. That way it's more one stop shopping.
From contributor A:
My tach will not log ten hours in a ten hour day. The tach works on rpm and it seems my engine is on idle most of the time which logs few hours. If the rate was high enough then you would make enough money. You will not be paid for the other stuff the logs owners will get you wrapped up in. If you go by the clock they will not waste your time as they know it is costing them money.
From contributor H:
What we do when scheduling the job - first tell them what is expected from them.
1. Have eq. to move logs.
2. Provide at least two people.
3. Wood always has to be removed, logs loaded on skidway, or we will pack up and leave no questions asked!
The typical day we will put 6 hours on the mill so my question to contributor A is - do you saw just to make as much money, or to provide a good service at a fair price? I saw to provide a good service at a fair price. This always leads to more work via word of mouth advertising. Sawing five days a week at $420/ day is better than days at $700/ day.
bronx
From contributor B:
I’m still a bit lost here. Do you guys cut logs into slabs for the owner of the log who wants to clear land and then you take the slabs or do you work out something and cut the log into slabs for the land/log owner to sell? My other question is for whoever gets the slabs to sell, how do you advertise? As a furniture builder my first thoughts are grain, grain, grain. How can furniture builders know what you have if they can’t see it? Slabs are really expensive and so is shipping so it’s really important to know what kind of grain and figure I’m getting.
From contributor J:
I have stated this before, I charge $100.00/hr. with five hour minimum. The clock starts when I show up. It takes 30-45min. to set up and the same to clean up and tear down. I supply no people. Being the only sawyer for three million plus people is nice but things for me are even slow this year. Most of my jobs last one to two days. So two day average is about $1300.00. If they are not ready for me then they pay for moving logs and tailing boards if no one is there to help. A couple of jobs ago the customer asked me how many people are ready when I get there. 85-90% is common but this guy knew going into what I was needing, and I spent more time moving logs and materials than sawing. He paid for it. I will be going back again to do more work for him. I can cut two to three logs at a time, anything up to multiples of 30’.
Last year I work a job where I went through four guys in 12 hours and cut close to 10,000 bf that day. I don’t like days like that. The last job I did, the customer cooked steak dinner and tipped me on top of that. That is for my portable mill. The mill at home is same price with no minimum. This has worked for me for eight years now except for the price increase early last year from $75 to 100.00/hr. I only custom cut for others. I will not complete with Home Depot or Lowes. I tell people that when they want 2x building materials.
From contributor H:
Two-three logs or cants at a time? If your laying them end to end you aren’t sawing lumber you are wasting good logs! How do you turn your cants - by hand?
From contributor J:
I have a pair of Cook’s mills. I built the long frame I use in the field from scratch myself and it is 35 feet long. I also have a 15 foot frame that I use when I get in the downtown area of Seattle when there is not much room to work. I have posted pictures in the past. I show up with a single axle semi truck towing the trailer. The picture will tell it all.
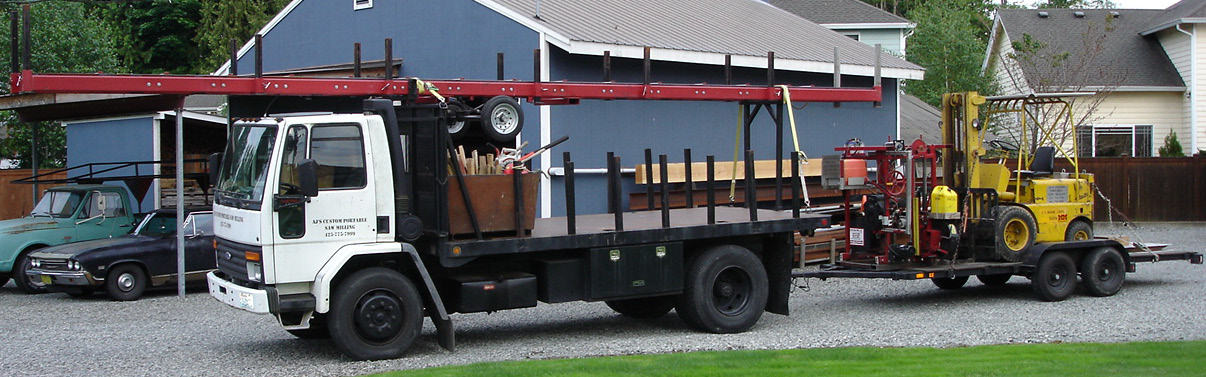
Click here for higher quality, full size image
From contributor J:
There is nothing I enjoy more that showing up WM, with their LT-70, when they come to the log show every year. I will cut three logs when he can do one. I wish the bi-annual shoot out would come to the west coast so I could show what a little thinking and design can do. People cutting one log at a time just seems slow to me now. It is hard work and for the really big logs I use the forklift to turn them. I have refined every move in setting up, milling and tearing down. The mill can be cutting one log when I am turning or moving another. I have found this very efficient. There are few wasted moves when I mill, and it shows up in production. The reason why logs are shorter most of the time is I am cutting hardwoods and you really do not need long wood. When conditions are right a can cut a 50’ log. Architects love this for some of the fancy houses I do work for. With the two mill heads and three frames I have the capacity to do many different things. I did buy a Morgan resaw last summer and it is really fast. What would take me 9 hours to do with the mills can be done in about 25- 30% of the time with the resaw. I charge $200.00/hr. for this.
When I bought the all electric head six years ago, my neighbors did not like the gas powered head too much because of the noise. They stopped complaining about what I was doing when I got it. The electric head is in a 32’x 36’ shop so when it rains, I do not have to be in it, and in Seattle, it rains here a lot. Most of my work is here at the house.
From contributor A:
When I show up.
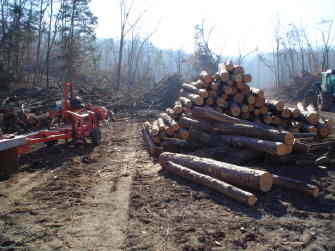
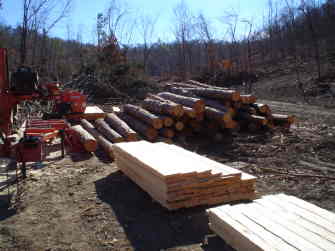
When I get done then my dog gets on there and grades the lumber. It is all well sawn and to what the customer wants if the logs will make it. I live in a rural area of less than 100,000 people and I know of six other portable mills within 50 miles of me. I stay covered up and people are willing to wait weeks for their orders. Good work at a fair price keeps them stacked up at the gate. We are doing just shy of a million bdft a year and getting more behind. Seems new customers are becoming repeat customers and liking what they get. I have people who haul logs over 100 miles to me to have me saw them. They pass many mills on the way here so I got them fooled somehow. Tools do not make the craftsman, the craftsman makes the tools.
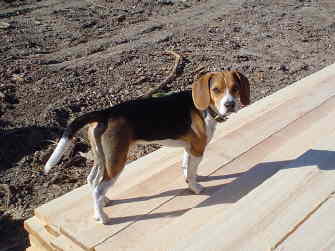
Oh yes we have slabs.
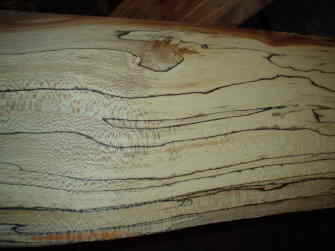
From contributor A:
That is SYP and it makes great 1x and 2x stock. It made a lot of clear wood as it was undergrowth of an oak stand.
From contributor Y:
I sold my mill and all my timber land in 2006 and I miss the hard work and low pay too. I have those lonesome blues too. I don't think there is a cure for it!