Scalloping Marks Left by a Helical Jointer Head
Helical heads reduce tearout, but leave a scalloped surface that some find objectionable. Here's a long and detailed discussion. April 10, 2008
Question
I started out needing some setup info on a parallelogram jointer since I was new to these, but I ended up getting things dialed in very nice. Something I did not expect, however, was a bit of disappointment with the much-touted Shelix head I installed. As far as the lack of tear out, I'm wholeheartedly impressed. The quilted maple sample shown here (the heavy quilt does not show well with the lighting I used) was even run backwards as far as the general grain direction to really put it to the test. Quietness has been significantly increased. The problem is the scalloped cuts running lengthwise down the board. I understand how they are occurring because of the nature of the cutter head, however I'm dismayed at how pronounced they are. Admittedly, I used the cruelest raking light I could to show the scalloping, but it is easily felt with the hand. I'm wondering if this is normal for these indexed heads? Also, does anyone know why each individual cutter has a slightly radiused cutting edge? I'm assuming this is where the scallops are coming from. Would a straight edged cutter create more problems than it solves? I'm sending a couple of images to Byrd tool to get their reaction.
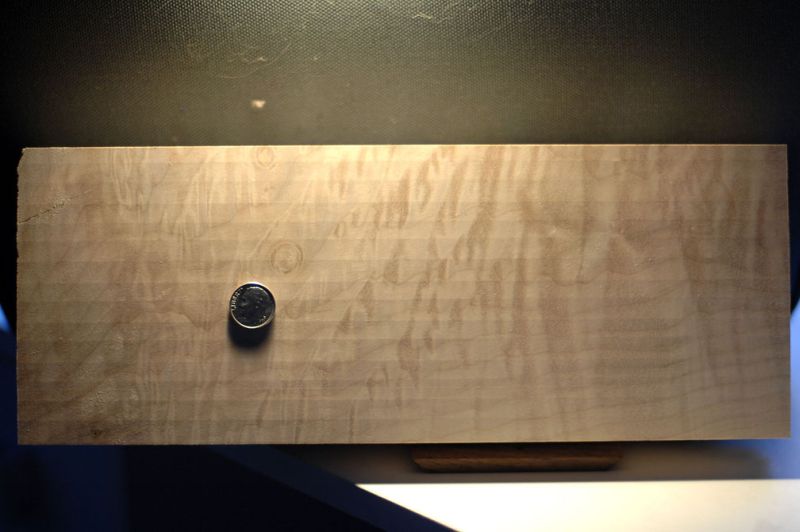
Click here for higher quality, full size image
Forum Responses
(Furniture Making Forum)
From contributor J:
My cutterhead leaves very light lines which you can only see in raking light, but yours look like they may be deeper? Those scallops are obviously caused by the slight radius on the carbide inserts, but I was under the impression the radiused edges were supposed to leave a better finish?
The lines left by my cutterhead (straight edged inserts) cannot easily be felt by hand. They are more pronounced in softer woods (poplar) than harder woods (maple, ipe), but even in poplar they are too slight to be of concern.
I guess my non-expert opinion, without seeing it in person, is that the scalloping you are experiencing is normal for that cutterhead. I am surprised, though, as I thought the quality of cut from a Shelix would be superior to others.
From contributor A:
I have a Shelix that I put on my cheap Grizzly 20" planer. The lines are nowhere near that distinct or consistent. I was a little concerned about the slight waviness, but found that they weren't an issue - glue lines right off the planer were acceptable, and wide belt sanding quickly took out the slight irregular scalloping. I'd be curious to know the actual depths of your scallops. Any chance you could use a feeler gauge and measure them? How much sanding does it take to eliminate them? I actually have a custom jointer head on order with Byrd, so I'm wondering if their quality is slipping, or are lines more severe on a larger diameter head?
From the original questioner:
Here is an attempt to measure the deviation in the scalloped surface. There is about .001 difference between valley and ridge of each scallop. We currently are without a widebelt, so I'm feeling a lot of scraping/sanding is in order. Unlike a few nicked knife ridges to bring down from a straight knife head, we will need to take down the entire surface. Granted we had to really rake a light across the board so others could see what we can feel, but... are we just whining here, or do others feel this is unacceptable?
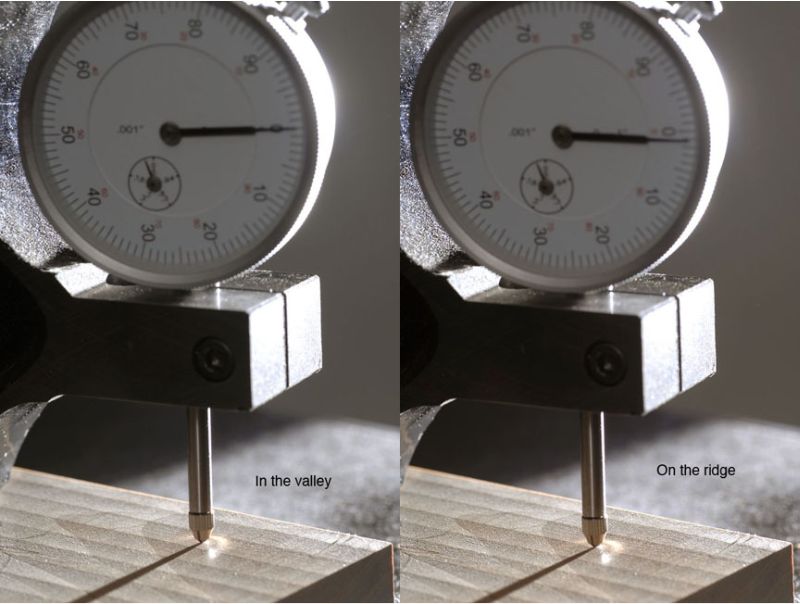
Click here for higher quality, full size image
From contributor P:
Personally, I think it is acceptable. Neither planers nor jointers are intended to provide a final perfect finish. Jointers flatten a face, planers machine to thickness. If the scallops are smooth and tear free, you are way ahead. Just think how deep even light tearout penetrates into the wood. Even after running through a widebelt, unnoticed tearout will cause finishing problems, splotching, etc. I really do not think .001 would effect edge gluing. You could run boards for edge gluing through the machine at a skew; that may help in that case.
From contributor B:
I am a bit surprised by the general tone of the responses here. I know planers don't give finished surfaces, but I don't see anything remotely that poor looking coming out of my old 3 knife Powermatic 100 12" planer. In your shoes I'd be calling the manufacturer asking for either a fix or a refund. Don't mean to contradict others, it just looks unacceptable to me.
From the original questioner:
Thanks. I do feel a bit discouraged by the results. An indexed shelix head, by most everything you hear, including Bryd Tool (the manufacturer), is the end of all your woes. It has shown a pretty amazing ability to handle figured grain, and the significant reduction in noise is a welcome plus. The scalloping may be my tradeoff for those benefits. However it is not one I expected. So you have an older Powermatic 12"? Want to sell it!? Nice! Without selling your firstborn, it's hard to come by quality, wide jointers these days.
From contributor J:
I hate to have to say this, but you may be better off with a cheaper insert cutterhead. As I said previously, the finish I get isn't perfect, but it is pretty darned good. I'm surprised you can actually measure the depth of the scallops! My Bridgewood has the normal inserts and leaves fine lines in the surface of the wood. You couldn't measure them; you can only see them in a raking light. Similar to lines you get from straight knives after they've been used a little bit. Other than that, the finish needs only the lightest sanding, though almost everything goes through the sander anyway. I don't know if your head is defective or not, but I would certainly not be happy with the quality of cut you're getting.
From contributor J:
One thing I forgot. I was thinking of getting an insert cutterhead for my jointer. (Though I don't think it will be a Shelix after this thread!) Would you say the insert cutterhead requires more force to feed boards through? Or is it even a noticeable difference?
From contributor G:
Completely acceptable. .001 is a number most people can't even relate to. It is 1000 little marks to an inch. It is so small you should be able to sand those lines out by hand in no time at all. If you're getting a quieter shop and good throughput, I would buy a sander. You will find it a very valuable addition to your shop.
From contributor P:
Well, I got quite curious about this. Since I have an engineering degree and most of my regular day job revolves around designing machine tools, I thought this would be a good candidate for some further analysis.
What I found is very close to what contributor B has discovered. I had to make some assumptions because I obviously do not have Byrd's engineering drawings. I assumed the inserts were 15mm, flat on top, straight leading edge. I guessed a shear angle of 10 deg.
I used a 4.0 diameter cylinder and optimized the insert placement so the trailing edge would just clear the generated path.
What I found is that when you take an insert like this and orient it for shear, the resultant generated profile is a slight arc. Mathematically speaking it is not an ellipse or any pure geometric form, but an arc with a max height of .0014 about .36 in from one side, not in the center of the insert. Byrd staggers their inserts in such a way to deal with this. The best I could do was to get no better than about .00074 arc height. Very close to what the questioner found with his indicator. A smaller cylinder diameter will cause this arc to be even greater, maybe the .001 that was measured.
So, there is absolutely no way the Shelix can cut a flat surface. There will always be scallops due to the set shear of the insert. The radius edge did not seem to make much difference. If you want flat, go with a Terminus; that is what I have and it is awesome.
From contributor R:
Funny, as some say acceptable, and some would suggest going with something else. I say let’s see first what Byrd has to say. For laminating, in my opinion, I agree this is not acceptable. But for surfacing and/or planing a plank prior to assembly, in my opinion, it may look disappointing, but acceptable, and surely it is as easy and fast to remove as you would get out of a regular planer knife that leaves nick marks, which you would see going from any regular sanding steps prior to attacking your finishing steps! This type of head will/should give you more advantages and opportunity than pain!
I hardly get a perfect assembly joint, glue-up and/or matting faces, that does not need little sanding. Any assembly needs some little sanding prior to attacking your finishing steps.
In my opinion, with a half decent orbital sander and a regular pre-finish hand sanding job, you should see those go away. If not, than you can say it is not working right!
From contributor O:
I have a Shelix 8" head on a jointer and I get nothing like you're showing. To me it seems like there is a problem with the head. I hope the Shelix Corp. can straighten it out for you. This should not happen.
From the original questioner:
Wow, contributor P! That's some serious analysis. I'm not familiar with Terminus. Now you have my curiosity up. Thank you all for the input. I have sent all pictures shown here to Byrd Tool over the last couple of days for their input. I have not gotten a direct response as of yet. I have a suspicion that with this style head, you get what you get. You take the good - no tear-out, quieter, with the bad - scalloping.
From the original questioner:
Well Byrd finally got a hold of me. They said that .001 is within their specs but that it looks worse than that. I think they're assuming the raking light makes it look worse than it is. Indeed I did everything I could to show the problem so you all could discern my situation. Byrd asked me to send them a couple of the sample boards that were in the pictures. They are sent. We should know in a week or so what their take is on it.
From contributor U:
I run a Shelix head in my 12" jointer and 24" planer. I know exactly what you mean about being disappointed by the scallops. You just spent a pile of money and thought it would be like straight knives, only better in every regard.
But over time, my original concerns have faded away. For me, the benefits of the Shelix outweigh the very minor surface deviation. Quiet, fast, extremely little tearout. Those marks sand off very easily even with a ROS and 150 grit. Unless you are face laminating, and concerned with visible glue lines, it shouldn't be an issue. How often did you get away with going right from machine surface to final product before?
From contributor Y:
What about edge jointing for panel glue-ups? Do these scallops create a more visible glue line?
From contributor U:
Regarding edge gluing and glue lines - I have not tried it, so I don't know. I have two jointers. The Shelix head is in the one that is setup with a feeder for facing boards. I don't edge joint on it.
I did notice that the scallops were greatly reduced after I rotated the inserts, cleaning the inserts and seats as I went. It would only take some machining swarf/grit under a small percentage of inserts to make scalloping more prominent. Also, the cutterhead diameter plays a role in my experience. My first Shelix was in a 3" diameter planer head. It has more scalloping than the 4" jointer head, which has more than the head in the RC-63.
From contributor F:
We have two of the Grizz 10 inch jointers with their index head and the finish is nowhere near as pronounced as you show. Check your insert seating, table alignment. As contributor J says, it is very important that the insert seat is clean and seated correctly. Even if it is factory new, I would check these two conditions, as sometimes you will get a Monday, Friday product even from Byrd.
From contributor A:
I don't agree that Byrd heads leave a surface too irregular for lamination, but would appreciate some input from the technical experts on the subject. Assuming regular or semi-regular undulations of .001", would this significantly weaken the bonds, given the recommendation for glue joints seems to be about .004"? Especially if one sends boards through a planer at an angle, or is careful to offset surfaces straight through a jointer, these little undulations shouldn't be a problem, right? My experience, making butcher block and end grain blocks gluing right off the Byrd head, has been positive. You really need a magnifying glass to see the difference between glue lines coming from straight knife head and those from the Byrd Shelix head. I was very worried about this, and tested it before making the switch.
From contributor E:
Okay. So color me totally impressed by the responses this question/concern has garnered. This is what this community is all about, in my opinion. I have to say, I looked at the indexable cutterhead scenario, and could not (then) justify it. I did, however, start to back-bevel the knives in my surfacing machinery, and the results are vastly improved, especially on figured solids. Maybe that's too old school, I dunno? I do not have to contend with volume. But the money I saved got me into digital readouts for everything - planers, sander, and ts... and a few rather choice
Festools. ;)
From the original questioner:
I valued all of the opinions over my concern with our new Shelix insert head a few weeks past. I have been able to put some more stock through it lately, and I think that I concur that the positives outweigh the negatives. It seems to effortlessly do the job of flattening the stock and leaving me with no tear out. Once flattened, if I'm using fairly straight grained wood, I can always remove scallops in my (currently) straight knife thickness planer once I have flattened and trued both sides.
I finally received a response from Byrd Tool for all of you that asked. Here is the quoted response, "The cut is normal for this type for head. If you cannot use it, we will give you a refund, sorry it didn't work for you. The angle of light that was used did make the finish look more pronounced than what the samples looked in person. I sanded the ends some with a 180 grit and the finish became smooth in no time.”
The reply felt a little like a take-it-or-leave-it response, but the offer to take a return on a slightly used head was appreciated. I agree that lighting exaggerated the scallops to a degree, but as I mentioned in my earlier post, it was so you folks could see what I feel, and included an actual depth reading (.001) to give a real world sense of the situation. I was trying to get a sense as to whether this was a typical result for this type of head from those of you with more experience with them. After I use this shelix head for a while and get a feel for the finishing aspects, I will consider if a shelix head goes in my Delta 4 poster planer.
From contributor R:
Thanks for the posting on the Shelix. I read everywhere I could find and a few said they got no "scallops" but most did and, while a few were upset that it did, everyone said it took very little sanding/scaping to get them out. On that I ordered the head (20") which is now waiting to be installed. My thought is that it takes a bit more than a "light" sanding to take care of an 1/8" deep tearout.
From contributor T:
I just installed a 20-inch Byrd head in my brand new 209 Powermatic and I am not happy with the results. Before I ordered the Byrd head, I talked to the Byrd people and they assured me that the wood would come out "smooth as glass" so that I could lightly sand and they apply the poly. Well they told me what I wanted to hear and now here I am - I'm going to have to buy a stroke sander or a wide belt now. I mass produce 16-inch curly cherry Lazy Susan’s and was looking for less time hand sanding. It's going to take me a long time to get an investment of $10,000 back (planer, wide belt).
From contributor M:
I had exactly the same problem a few years back when a tooling supplier gave me two 4" Byrd Shelix heads to use on the side heads of our Weinig moulder. We have used Weinig and Gladu 9" insert heads, top and bottom, for years and the finish is excellent.
We tried the Shelix heads and what a piece of crap! The finish was terrible to say the least. We tried all different woods and feeds to no avail. The supplier said they should cut better than that. He took the heads and I have never seen him again. We then purchased 2" and 4" side heads from Weinig and the finish is glass smooth. They were more expensive but they produce.
From contributor T:
It seems like with the fixed 4" radius on the inserts, the cutter diameter plays a big role in the surface quality. I've had 3 different Shelix heads from 3" to 4-5/8". The smallest head had the most pronounced scallops.
I think that these heads do very well in situations where you are not milling a finished surface. We sometimes hand sand a planed surface, and it does take longer than a straight knife finish. But if you can't have tearout, and need speedy throughput, then the Shelix head seems to do very well. I ran some end grain butcherblock through my planer last week and it didn't bat an eye. My Shelix heads have saved many hours of figuring out which way to run boards through for least tearout, not to mention getting useable parts from stock with crazy interlocked grain. But we machine sand any flat surface that is going to be finished. These heads can't eliminate that.