Setting Up a Six-Head Moulder for Machining Tall Baseboard
Here's a detailed discussion of how to arrange the top knives for cutting of the flat and the profiled part of tall, highly detailed baseboard mouldings. March 31, 2008
Question
I have a question about using different top knives in the same operation. My role here is to create the knife grinding templates. After discussing it with our previous molder operator, we decided that on details such as tall base where there is quite a lot of straight and relatively little detail at the top, we use a combination of detail knives and straight cutters to reduce the grinding operation. (See image.) We have a Weinig Unimat 23E molder. It has two top heads. The problem is that we have been doing this for a while and it works, but our current operator does not know how to set it up. I am not the expert on setup, I just make the knife templates. I have an idea of how it may work, but could anyone explain it to me so I can make sure that our operator does it right?
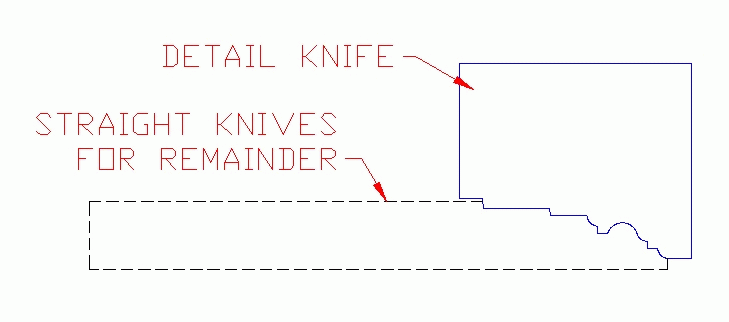
Click here for higher quality, full size image
Forum Responses
(Solid Wood Machining Forum)
From contributor R:
Your theory is correct. First, top head plane to finish thickness. Second, top head detail only. Take the tool radius from where the 60mm line on your template and knife is. I make the template so that the knife extends past the 60mm line by at least 1/16" so you know where to take the tool radius on the knife.
Design the knife and template so the detail is closest to the inside fence of the machine. That way you can change widths if needed in the future. You're on the right path with the picture you posted.
From contributor J:
I am only saying this because it sounds like your operator is new. I would be in favor of placing the profile on the top facer head, and the straight knife on the finish head. The method contributor R suggested will certainly work well; my only concern is that the profile knife looks like it has to be at the same level as the top of the profile to make the appropriate cut? This could cause a problem if the hold down is not perfectly flat, and the beds are not perfectly flat (which could easily happen with a new operator if he runs a piece into the hold down while setting up, or doesn't clean under the bottom beds for a while).
To get to the point, if the profile knife is very close to the finish thickness, and the piece moves a little, it will dig in and leave lines in the top of the board. Then you will lose a lot of time sanding, and could lose material if it is too deep! Either method would work well. If it was me I would call my old operator and ask him what he did, unless he dropped off the face of the planet.
From contributor R:
The hold down on the first top head is just a tension spring bar, not like the second top which is flat and about 10" long. If the knife is designed correctly, then your comment will not be an issue. The second thing that needs to be addressed is if you put the profile in on the first top, you have no straight knife to take away the rest of the detail, causing the hold down not to be steady, and this invites chatter from the wood constantly getting pinched from varying thickness. I stick by my original comment for just those reasons. Try it both ways.
Go past by .062". Take the tool radius from there, then subtract .062" from that number and set that number in your radial counter. This will put the detail right where it is supposed to be.
From the original questioner:
Thanks for the responses. Contributor R, you are the one that set up our machine and trained our original operator. You showed me how to make the templates. I value your input. You just confirmed what I thought was the right way when our operator questioned how to do it. I am considering having our current molder operator retrained, or some other solution. We are not getting the quality of moldings out of our machine that I think we should.
From contributor J:
"The second thing that needs to be addressed is if you put the profile in on the first top, you have no straight knife to take away the rest of the detail, causing the hold down not to be steady, and this invites chatter from the wood constantly getting pinched from varying thickness."
I was assuming the material would be faced to a constant thickness? This would eliminate this concern, wouldn't it? Forgive me if I am just not familiar with this particular machine.
From contributor R:
There is no right or wrong way of running mouldings. Your idea would work as well, and I meant no disrespect to your idea. I have tried to run mouldings just the way you explained but have found better results with less trouble for the operator running it the other way based on the way I design mouldings.
From the original questioner:
When this came up last Friday, I suggested to our operator that he use the first head with the straight knives and the second for the detail. He said that on our molder that head is just for hogging thickness, and does not have accurate enough adjustment. What is your experience with this on the Unimat 23E?
From contributor R:
Both heads have accurate counters. The difference between the first and second top is mainly hold down. The first top has a series of 3 metal plates (contact point on lumber about 1/8"). The second top has the traditional spring tension hold down, contact point on lumber about 10". The first top is known as the planer, but can be used for profiling as well. The reason the first top head hold down is different is because the distance between the two top heads does not allow enough room to fit the traditional hold down.
From Dave Rankin, forum technical advisor:
With two top heads, I would cut the straight on the first top and the profile, located against the fence, on the second top. Just a note for those operators with only one top head - a combination tool can still be used as long as you grind the profile and straight knives in the head. To do this you will need to use the gauges that most grinders have. The gauge for the diamond dresser and the grinding wheel adjustment can be tuned together on most machines. This allows the operator to grind the profile first and then verify the grinder calibration and spark off the straight knives. Without a doubt, two top heads makes it faster and easier. My moulder only has one top head and I have used combo heads for many years.
From contributor J:
I use combo heads as well, whenever possible. It is easier for me to do that, but not for everyone of course. I spent quite a long time grinding the head, setting up the machine, and running the job for small shops. I think it takes a little longer to grind, but you save time on the setup because you just put it on, set the axial, and go. I would say that whatever you feel comfortable with is the way to do it!
From contributor C:
The profile looks like it cuts in at close to 90 degrees at the top. If you run the profile on the 2nd top head I'd be worried about tearout and chipping at that point. I've always had a preference for running the profile on the 1st head for that reason. Planing on the 2nd head keeps that corner clean and crisp. If you do run the detail on the 1st head I would flare the knife off a lot more to make sure the edge didn't dig in on any thicker boards.
From contributor R:
Contributor C, a couple of things about sharp crisp egdes... Your comment is correct - you would have more tearout that way you explained. I design mouldings, so there is not a sharp clean crisp edge where the those two knives meet. Reasons are for me, paint and stains don't adhere to sharp edges, tearout is more likely, sharp edges most likely get broken in the paint shop anyways, and by the time you stack the product face to face, with all that movement on the truck, you're going to have a lot of frayed edges and damage to the product. By putting a small .04" radius on the template and flaring off from there, you can eliminate such problems. It also allows you to set the thickness a little higher and you are able to sand the flat part of the base if required without taking away from the profile. Granted there are some cases you need to have sharp edges in the detail. Then it is what it is. If you're finish grinding with a 2mm (.078") 1mm (.039") radius wheel, it automatically breaks any sharp edges in the profile area. Most people don't even notice it.
From contributor C:
I based my assumptions on the questioner's sketch. Yes, a radius at that corner helps with tearout. I see it is .062". The bigger the better, as I've had problems in the past with smaller radii still chipping and tearing.
From Dave Rankin, forum technical advisor:
One thing that I also use is shear profile heads. This reduces the tearout even if you have a required square profile. I agree with contributor R - I use a slight radius when possible and I try to allow for 1-1/2 -2 degrees from 90 if possible.
From contributor T:
Interesting reading here! A Wienig 6 head performs best using the first top head to hog and size the thickness before the second top. The hold down plate aft of first top secures timber nicely from vibration as it passes under the wheel, and 2nd head chipper tightens it even more to bed, giving you vibration free profile cutting. Second top removes 10 to 20 thou giving much better finish. Set your profile knife inboard as instructed above, but on a 4 knife head. Set S4S knives in opposite gibs of profile knives and grind the flat tool to fit by passing over the roundover you want on the left edge of that profile. You can double check this clearance on your tool stand when you measure the diameter of tool. After a bit you will have a number of base tooling that fits very closely with minimal grinding. I leave the S4S tools in that head and only have to change out the short profile tool which is ground to fit that set of S4S tools. I have done it this way on 2 different Wienigs for several years, always with very nice finish.
One of the secrets to a fine finish with very minimal tool marks, is to hold the timber flat and vibrationless. That feed wheel just ahead of the second head chipper running on a smooth calibrated surface helps a lot. The hold down aft of the second head your running the profile on, if adjusted rightly in combination with last feed wheel and bottom head, completes the fine setup required for best finish. (I am referring to the Wienig Unimat.) You will have absolutely no tear out when running both tools on one head if you grind it correctly. Just be sure to back grind 5 degrees any tooling that runs 90 degrees perpendicular to the bed of moulder, and that includes that tiny roundover you show.
I was trained by a German Weinig tech in the 80's on a Profimat and he only had to tell me once, "There is no 'yeah, buts'!", meaning, yeah, but what if I did it this way?