Shelf Stiffening Methods
Other Versions
Spanish
French
A discussion of shelf spans, shelf materials, and reinforcing methods to prevent sagging. April 10, 2008
Question
I am working on a job that requires some shelves 12" x 50", and I don't want them to bow. The shelves will be used for mainly photos, but some books as well. I was planning on gluing 3/4" and 1/2" ply together, or 2 layers of 3/4" and putting on a hardwood edge, hoping this would be enough.
Then I started thinking, with all the labor to make these, would it just make sense to make the shelves out of solid wood, poplar or soft maple, 6/4 stock? I suppose the solid wood has more strength, but could have a tendency to warp. Just wondering what others have done. I know I don't want to use Medex or MDF, as I have seen it sag over time on other job sites I have been to.
Forum Responses
(Cabinetmaking Forum)
From contributor T:
I have offered this suggestion before, and been soundly criticized for it. It does, however, work. Take two pieces of 3/4 plywood and run them through the planer, removing the top layer of veneer. This will cause each piece of plywood to develop a severe crown where the core is exposed. If you re-glue these pieces of plywood back together with the bowed faces opposing each other, you will produce a pre-tensioned plank that is dead flat. With a 1 1/4 inch thickness you should be able to do chin-ups on 50 inch length without any deflection.
From contributor R:
50" long shelves do need reinforcement and solid wood would be better than plywood. A good combination would be to use 3/4" with a 3" front edge splined or rebated to the edge of the shelf. The 3" front could also be from 3/4" hardwood. If you use a thick shelf for that span that will work also but I'd suggest 8/4 for poplar or soft maple.
From contributor L:
If you take two 1/2" pieces of ply and use 1/4" blocks on the inside going from front to back, you will create a torsion box. Laminate some solid stock on the front and back and it will resist quite a bit of weight before a bow might form. I think it would be cheaper in the long run to use solid stock, less labor.
From contributor N:
Back in the 90's I used to make a lot of computer furniture. We made a line of computer cabinets that had shelves 44" wide by 16" deep that would hold a monitor, a printer, and a CPU. I'm looking at mine right now. All you need to do is use 3/4" plywood and a 1 1/2" solid wood for your edge banding. We made this product for about 14 years with no complaints.
From contributor E:
Here's another vote for solid wood. Easier to make, sturdy as heck, and in the worst case scenario if it did develop a bow over time you could just flip it over.
From contributor A:
1 1/4" x 12" x 50" poplar could be used as a staging plank. Labor outpaces material so fast these days, it is no longer worth it to nail edging on plywood. It takes the same amount of time to mill the whole shelf as it does to mill just the edging. No gluing, nailing, putty, etc.
From contributor M:
I agree about the solid. My only concern with solid is twisting of the wood over time, which you really wouldn't get with the ply. I would hate to see a shelf twist 6 months after the job was complete. I worry about this because it seems that often times the hardwoods I buy will twist over time when they are left in the shop on the racks.
From contributor D:
I've been using pre-tensioned (opposing bits of 1/8" dowel) 1/8 x 1" steel (untensioned aluminum didn't stand the test of time) in the built-up edge of MDF and Classic Core shelves. The MDF edge gets prepped with One Time, the CC edge goes through the edgebander.
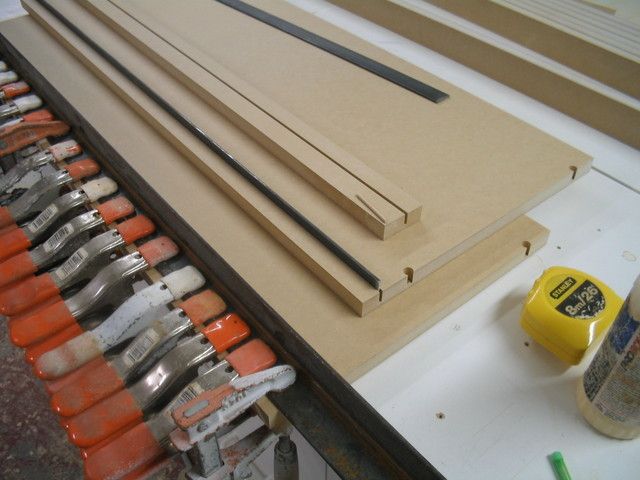
Click here for higher quality, full size image
From contributor P:
Have you tried the sagulator in the software connection on this site? I have had good luck with it.
From contributor N:
You guys are over-engineering this shelf. 3/4" plywood and 1 1/2" solid wood edgebanding. For what he's doing, it will last for years and years. Unless he's going to use it for loading a motorcycle on a truck from time to time when he can't find a ramp, I wouldn't worry about it.
From contributor S:
You took the words right out of my mouth. I'm going to go out on a limb here and tell the questioner to add a 1 1/2 strip to the back, too, if he is that concerned.
From contributor N:
With the extra 1 1/2 strip on the back, you could use it as a ramp to load a motorcycle.