Sleds and Fences for Cutting Stiles and Rails
Extensive advice on how to set up a shaper for accurate and consistent coping and profiling for door stiles and rails. April 27, 2007
Question
I'd appreciate some help with the way I'm making stiles and rails. When I cut the groove where the stile and rail meet, I make a hash of the job. In the end I have to re-cut the whole lot because the wood splinters out or the spindle grabs a chunk out of the wood or it just does not fit nice and flush. Is there a certain technique or a special tool that could make my life easier?
Forum Responses
(Solid Wood Machining Forum)
From contributor L:
Can you tell us how you are doing it now? What machines and techniques? Normally you use a shaper/router and cutters and there is no problem. Sounds like you are doing it a different way. Tell us how and we can recommend some better techniques.
From the original questioner:
At the moment I'm using a 30mm spindle with a 4 wing cutter. First I cut the side that fits around the raised panel and then I obviously have to cut the two short sides to fit into that groove. I hope this all makes sense?
From contributor L:
All end grain should be cut first, then with the grain. This prevents chipout and blow out. You need to use a featherboard or a stock feeder to keep your pieces flat to the table for alignment purposes. If you constantly have problems with blowout from making the groove for the panel, you may have to make a two-pass cut. The first one would be a shallow cut just enough to groove the wood where it needs to be. The second pass will be done to proper depth. If this still doesn't prevent the chipout, then you may need to make the first cut a climb cut. If you don't have a stock feeder, do not attempt this cutting procedure. It is dangerous and can cause flying wood or, worse, serious harm to the operator or people around him. It sounds to me like you are just doing a tongue and groove style stile and rail. If you are doing a cut with a profile and this is still happening, it may be time to get your cutters sharpened.
From the original questioner:
Thank you kindly for the help. My cutters are sharp and I use a shape for the rail. I use a Robland spindle. When I push the end piece into the spindle, it's fine - the problem comes in as soon as the work piece leaves the fence. When it is between the two fences and still going through the cutter, this is where I get chipout and worse. I suppose it's okay if you only make a few doors a week, but I'm starting to make more and more.
Is there no other tool or machine that I could look at to make my life easier? I already call the spindle a finger chomper and I dread this happening.
From contributor T:
The above is good advice - always do the cross grain first. The easier way to go is CNC. There are several new routers on the market that do an outstanding job with rail and stile doors. It's all automatic, so there are minimal safety concerns.
From contributor H:
I trust you're using some kind of a sled to shape the ends of your rails? If not, build yourself one with a toggle clamp to hold down the rail while you shape the end. This will give you clean cuts as well as save your fingers. Keep safe.
From contributor L:
Make yourself some wood/MDF fences. Then attach them to the fence hold down iron. Don't tighten them down tight, just snug. Then tap them into the cutter so that they get the profile on them. Do this to both sides and this will narrow the gap between the original fences. Tighten them down when you are finished. Are you running a destructive cut or a non-destructive cut? What I mean is does the cutter take off wood so that the outfeed fence needs to be moved out farther than the infeed fence? If so, you may need to play with this dimension; it is critical because it acts like a jointer. Is it possible for you to take a picture of the setup? Get in good and tight so we can see exactly what the setup is.
From the original questioner:
Here is the spindle I use for big doors. I use the same fence on my Robland as I only have one fence between the two machines. I need to adjust the fence in the similar manner you would adjust a jointer. It's okay if I cut with the grain, but to cross cut is a problem. On the Robland I have a sliding table, but on the Casadei I have no table, only a little push block that I built that runs in its groove. Works okay but not as I want it to work.
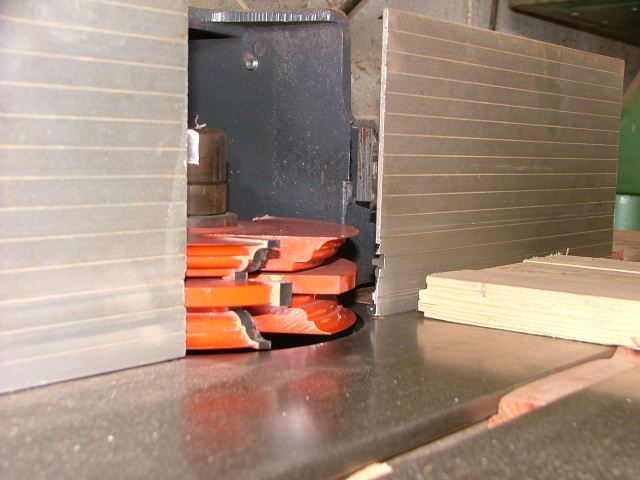
Click here for higher quality, full size image
From contributor M:
Look around Weaver's web site. Although they are primarily cabinet door production, looking at jigs and fixtures might give you good insight as to how to machine your parts.
From the original questioner:
Now there is just what I need - the end of my sleepless nights. Thank you kindly!
From contributor D:
Take a look at the Panelmaster II. You can find it at Hawkwoodworkingtools.com. It can cut all the stiles, rails, and panel in under 2 min and it does a heck of a job. It is usually around $3500. Ask for ext 303. He knows the most about the tool and can send a video for free.
From contributor R:
Here is a picture of the coping sled that we use for
cabinet doors. It has a replaceable backer board to prevent blowout, held by the small middle toggle. The bolts going through the cross piece are what the backer board registers on, so it is easy to adjust to square.
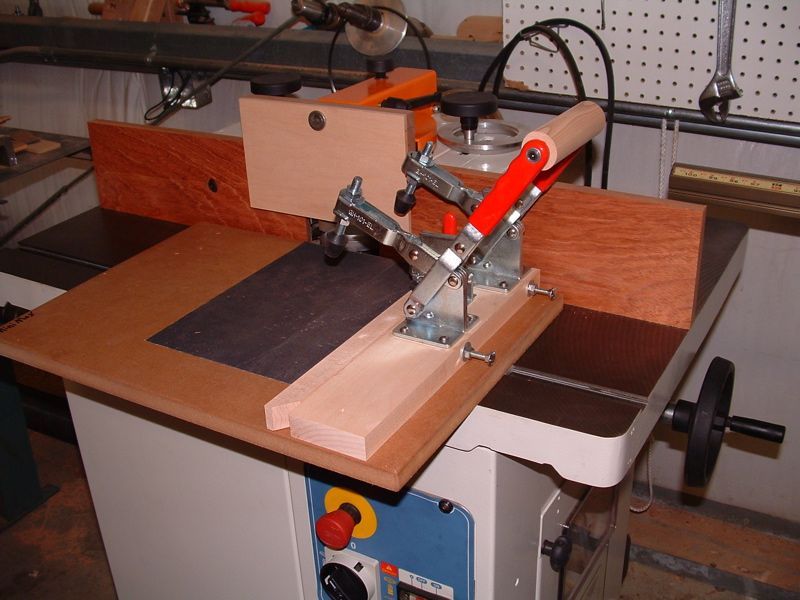
Click here for higher quality, full size image
After the end cuts are done, we run them through the groove/pattern shaper, but not against the shaper fence. Set the feeder to push against another fence attached to the table, away from the cutter. That way, you never worry about parts going into the cutter. If you leave the shaper fence in one place, you can use simple spacers to set various distances from cutter, so you are calibrating the width as you cut the profile groove. Since this picture, we have gone to a belt feed on the power feeder, which can run short rails with no problem.
From contributor P:
I have a Robland also. Contributor J's advice is very good. The problem you're having is that the tooling is eating the end off the stick and causing it to move into the cutter before it gets to the outfeed fence. Even 1/32 of inch will be bad.
Also, you have to have the fences exactly - that is, exactly! - square with your sliding table on the Robland. Then build that sled as above, making sure it is sliding parallel to both fences; bolt it onto your sliding table through that slot the push fence is bolted to (put a wing nut underneath) and put on that backer board to stop blowout and install a good clamp as shown in contributor J's picture so your stick doesn't move.
Set infeed fence to cut off 1/16th inch of end and slowly approach outfeed fence. Shut off machine (you can do that on the Robland with your knee) and set that outfeed fence so it just touches the stick. Back up, start machine and slowly push all the way through, this time making sure stick doesn't hit the outfence. You should not feel a slight bump.
Your sled has to be sliding exactly flat on the machine or your tenon ends will give you fits when assembling rails to stiles. You can adjust your sliding table runners from underneath. Using a feeler gauge or caliper, make sure sled bottom is same distance off table from beginning of travel to end. After all ends are done, change your tooling for the running profile (you will have to lower the spindle because the sled is gone now) and hog off all but 1/8". Last run through with the feeder taking off that 1/8" will give you a fine finish. Always make sure that outfeed fence lines up with the tooling circle! Infeed fence should not take off more than the Robland motor can handle without loading down.
The Robland is heavy enough to do this job for a few doors a week, but if you get into more work, you should plan on investing in a high quality sliding table shaper with a heavy 4 wheel feeder, all the clamps and hold downs such as a SCMI (Italy), a Felder or Hammer from Austria. I have a Felder 700 Pro series and can machine and assemble all parts of 5 to 6 six panel 1 3/4 inch doors in a day… alone. So if you're going that way with production, plan on spending 10,000.00 USD. I wish you success!
From the original questioner:
Thanks for that sound advice. I have since built a sled and now I'm making stiles and rails with a smile. I did invest in another spindle, but an old one – it's a Dankaert that I renovated. On this I only cut raised panels and that leaves my other spindle with the stile and rail free for only that. This forum is great and I have learnt a great deal from you chaps – thanks!