Sliding Table Saws — Choices and Alternatives
A discussion about upgrading the panel cutting capabilities of a shop with limited floor space. July 28, 2012
Question
I've been operating for quite a few years with a DeWalt DW746 hybrid table saw (with sliding table) that I bought 10 years ago as a hobbyist. It's adequate, but with the 1 3/4 HP motor, even cutting sheet goods is a little slow. 8/4 maple, forget about it. It's time to move up to a big boy saw, but I'm not sure what that should be.
My shop space is only 1,000 square feet, and I do both frameless and face-frame cabinets. I am a one-man shop for now, but likely to add help soon. I will be in this space for the foreseeable future.
I could just upgrade to a more powerful table saw, but I'd still need a good way to crosscut panels. So, a new table saw with a vertical panel saw? Or a sliding table saw? I'm on a tight budget, so the solution needs to be affordable or lease-able.
Forum Responses
(Forum Responses)
(Cabinetmaking Forum)
From contributor K:
It really depends on the type and volume of work you intend to do. You need a heavier duty saw for solid wood at least, and if you are intent on keeping your investment minimal, you can get by with a used Unisaw or Powermatic 66, and cut standard cabinet panels with a shop-built sled running in the miter gauge grooves. A step up would be to add an aftermarket sliding table rig like the Excalibur or Jet.
If you just want to cut square cornered, square-edge panels for cabinets, a good vertical panel saw is the way to go for higher production - Streibig seems to be the top of the heap. They use minimal floor space and are easy to load, if you store your panels on edge close to the saw.
For maximum versatility, with the ability to bevel panel edges and cut odd angles, a sliding table saw is great. It takes up a lot of floor space, and is awkward for narrow lumber rips - ideally would be paired with a cabinet saw. Altendorf and Martin are the top saws, and you can find good used units without electronics that will outlast a one man shop in today's market for under $10K.
From contributor L:
Contributor K covered it pretty well. Sliders seem to take up more space but it isn't that much different than the space required for the size of the sheet goods. They are very versatile: cut square, miter, bevel, SL rip to 10', clamp jigs to the slider for repetitive odd cuts and have enough power to rip 8/4. Keep your little saw for small parts and dado. We've got an SCMI that's been a good saw.
From contributor B:
I've got 1000 sf as well, and do everything with my sliding saw. If I had the space, I'd add a Unisaw or Powermatic. I added a vertical saw a few years back, but it was only useful for panel sizing, and was more difficult to load than the slider (with an Adapta panel handler - highly recommended!), so off it went. In fairness, I would have happily kept it if space was not at such a premium.
From contributor R:
I've been doing this for 30 years, and it finally happened to me - one split second of inattention on the table saw (Jet JW 10S 3hp cabinet saw) and everything has changed forever. I lost one finger and suffered severe lacerations in 3 others, and 2 broken bones in the back of my hand that required 2 titanium plates and 18 screws. It's been a month and a half, and I'm still wearing my splint. God knows how much money this is all going to cost me.
Table saw? Only one worth discussion is the SawStop.
Don't think you're immune to mistakes. Do yourself a big favor, and protect your greatest asset - yourself.
From contributor B:
Amen. I wish they had a sliding table version of the SawStop.
From the original questioner:
Thanks for the thoughtful advice. I had mostly given up on the SawStop due to the high price, but you present some persuasive evidence. I've worked in shops that had them, and the false triggers were an issue. I think a riving knife with an overarm guard could work pretty well too.
I don't see my shop building more than a kitchen a month, but the way things are going that could change. I'm perfectly happy cutting sheet goods on the table saw. In fact I learned the trade in a shop that did all the crosscutting on the fence! Few parts were perfectly square but it never seemed to be an issue.
For the price of a cabinet saw and aftermarket sliding table, you can get a complete 5HP sliding saw from Grizzly with a scoring blade. Hard to ignore that option. Are the Grizzly machines such a bad idea?
From contributor B:
You get what you pay for. If you can get by with a cabinet-type saw, the SawStop is a complete no-brainer. I had a minor sawblade mishap a couple of years ago - nothing like contributor R's nightmare, but ER costs and lost time would've bought me a couple of SawStops.
From contributor L:
There are lots of people philosophically opposed to the SawStop. They are high quality, well designed and safer than any other saw. They are expensive, probably about the cost of one trip to the emergency room. I asked my fingers if they thought it was too expensive; they asked me what I thought they were worth.
From contributor S:
I bought a SawStop 6 months ago and a used vertical panel saw in November to replace a 30 year old Sears table saw. I resisted the SawStop for years because I disliked the reported issues about the lawyer designed. I only use the panel saw to rough cut full sheets to manageable sizes and make all final cuts on table saw.
After a long talk with the dealer I bought the industrial model. The difference in the construction between that and the professional model is well worth it. Forgetting for a moment the built in safety features, I find myself more conscious of safety because I am ever mindful of the cost of a triggered cartridge and saw blade. I had a false triggering of a cartridge last week. I think the blade was pulled off zero setting during a blade change and as soon as I started the saw, the cartridge blew. I was really pissed at the 2 hour round trip to get a new cartridge, but still very happy with saw.
While retired now, I still spend 30-40 hours a week building something for someone and even on what is now a hobby basis, the SawStop is worth the asking price.
From contributor B:
SawStop cartridge - $70.
Blade - $125.
Body parts? Priceless.
From the original questioner:
Okay, I think we're a little off topic here. We all agree, SawStop makes a great product, and the value of the added safety is indisputable.
I'd still like to hear more responses about sliding table saws. I have a good setup on my DeWalt that uses the factory sliding table and provides support for crosscutting a 96" x 24" panel. I have never used a Euro-style slider and I'm guessing the process of cutting sheet goods is a bit different. If the slider has a 96"+ travel, would you use that to rip rather than the fence? Can the slider support a full-size panel?
Also, some saws have a track that extends into the space where you might normally stand to rip. Is this as annoying as it looks?
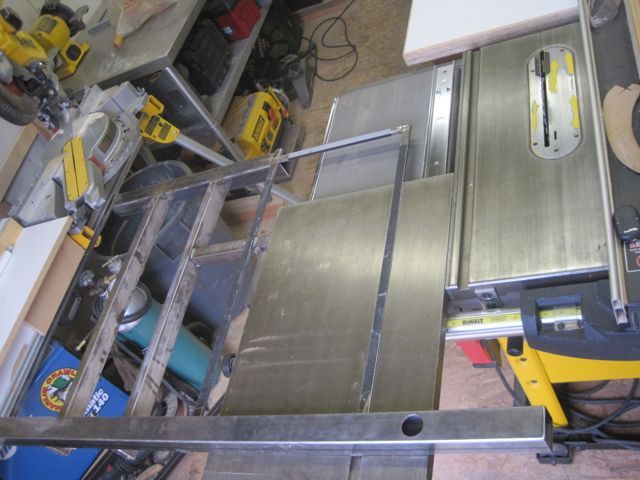
Click here for higher quality, full size image
From contributor B:
I've got a 10' saw, and use the sliding table to straight-line the panel, then against the rip fence. The extension of the undercarriage is only a minor annoyance in comparison to the benefits of the extended table stroke. I stand to the left of the sliding table and reach over for small parts cutting, rather than standing behind the saw. Having an 8' or larger sliding capacity means never having to remove the crosscut fence, which to me is a real inconvenience. I've owned two short-stroke saws, and would never go back, despite my cramped work space. Keep in mind that the floor space required for a sliding saw is similar to that required of a cabinet saw that's being used to cut panel material. With either, you've got to have the full length of your panel stock fore and aft of the blade, as well as to the left of the blade, plus the rip capacity to the right.
For accuracy, versatility, speed, and safety (yeah, I got nicked, but it was my own damn fault, and I really had to work at it), I haven't found anything that compares.
From contributor K:
In my experience most people use a slider as contributor B describes, making an initial straightline or dustcut on the panel edge with the panel supported on the sliding carriage, then using the rip fence to gauge the rips. A full panel requires some support at the back left hand corner while making the first cut, but the carriage takes the weight. Most cuts are largely supported by the carriage. The beam does get in the way on narrow rips as you reach over the sliding table. That's why it's a good idea to have a cabinet saw as well if space is available. The Euro fence bar can be moved fore and aft like a Delta Unifence to act as a crosscut stop to the right of the blade. If you search the Knowledge Base here you will find more thorough descriptions of technique including some advocates of making all rip cuts on the carriage (some saws have a parallel gauge available for this). Go visit a shop with a slider and ask them to demonstrate.
From contributor J:
Contributors B and K have it right. I have added a 10" cabinet saw in the front and to the left of the carriage. It does not take up any more room and it gives me the best of both worlds. I use a 10" saw primarily for ripping hardwood because that's the one thing I don't like to do on the slider. You will also find that if you plan your cuts right, you can cut up a sheet of plywood almost without taking anything off it until you are done.
From contributor C:
I have an SCM 10 ft slider, I love it, and use it for everything. I can cut a whole kitchen or commercial job in no time. I like my saw and use it so much that I might sell my CNC. I guess you have to decide how much space you want to tie up. My slider does require a large area. I believe you can get an 8 ft slider, which would require a little less space. I had a 5 ft slider, which was good for crosscutting a sheet, but every time you want to rip a sheet you have to take the fence off. I was not a fan of that saw. Like others said, a good slider will have a scoring blade, which I think is an important feature.
I have a 3 hp Canadian made General table saw which is similar to the Unisaw and is a great saw. It will easily cut sheet goods and solid with the power it has. Only problem is it doesn't have a scoring blade or a sliding fence, although you can buy a sliding fence as an accessory.
I think Sawstops are way overpriced. They may be good as it is one less item for an employee to get hurt on, but I personally wouldn't buy a tool based on me sticking my hand in it. What happens when you stick your fingers in your jointer or your shaper?
From contributor B:
I fail to see the logic of the previous post. It's like saying "Why should I worry about my smoking? we're all gonna die of something anyhow."
Table saw accidents are horrible, and with a SawStop, preventable. Spending a tiny fraction of the costs of ER/microsurgery/physical therapy/lost time/work comp hassles to have "one less item for an employee to get hurt on" just makes sense.
It doesn't change the fact that jointers and shapers are dangerous, but it seems like most shapers have power feeders, and jointers have push sticks nearby to mitigate the dangers.
I probably log 95% of my "dangerous machinery" time on my table saw, and with the familiarity comes the occasional dip in mindfulness, especially cutting the odd replacement piece for something that's behind schedule. When working on a jointer or (much more rarely) a shaper, I tend to be more focused because they're not tools I use for hours on end every day.
From contributor C:
I fail to see the logic in your post. What does smoking have to do with anything? I wouldn't buy a saw based on one feature, just like I wouldn't buy a truck based on one feature. I want a saw that makes my job easier and makes my finished product better. I never said the feature was bad. It would be great if it was on all tools.
Lots of people like the Holt-zer edgebanders because of the glue cartridges. It is a good feature, but I would never buy that edgebander based on only that one feature, especially If I need corner rounding and that machine doesn't have corner rounding.
A feature is also dependent on how much you use that particular feature or machine. For you it would be good as you use yours for 95% of your dangerous machine operations. For me the Sawstop would be a great saw for installing on job sites. In the shop it is a tool that would be used for only a few small tasks.
I am fairly sure your logic at the end of your post will fly with workers compensation… Good luck with that. When in a cabinet shop, your mind better be thinking safety no matter what you are doing. That is also why my table saw has push sticks beside it.
From contributor L:
I bought a SawStop for that one feature. I replaced a relatively new Unisaw. I personally value my fingers and those of my employees enough to spend the money. A good, expensive saw that could very well turn out to be cheap.
From contributor O:
I would look at the sliding table saw if you can. There are also lots of used ones around. My tech was showing me a 15 year old SCM that he bought that he said was a great saw. He said they are well built and that not a lot that goes wrong with them. There are also other really good name brands, just make sure you can still get parts and service. I know some companies, like Sicar and Lazzari, are no longer in business, so not sure about parts.
Basically, once you have used one, you won't ever go back. All the names I have seen in this post, like Saw Stop, Uni-Saw, General, Grizzly, all have their purpose, but I call them your handy man garage saw. They can do a little bit of everything, but they are not great saws for cutting sheet goods all day long.
As for the safety issue, it's a shoulda, coulda, woulda, issue. If I woulda had my safety glasses on I wouldn't have hurt my eye. Every tool is dangerous if you don't use it properly. How many people have cut themselves with a simple exacta knife? I have. I would sooner put extra money into training and safety courses for all equipment in my shop than replacing a perfectly good saw. I guess it's not a problem if money is not an issue.
From contributor O:
I like your saw set up, contributor J - that is a great idea.
From contributor J:
Thanks. It works real well. I agree with you on the SawStop. But I disagree with you on your feeling about the table saw. If I could only have one, I would have the slider first. I do not like ripping hardwood on it. I do all my crosscutting of hardwood on it because it's dead on.
From the original questioner:
Has anyone ever found a video or guide on the efficient use of these machines for cutting panels? I'm trying to imagine how I'd use each saw with minimal handling of the panel and the straightest/squarest cuts.
From the original questioner:
Well, after a lot of flip-flopping on whether I needed a vertical panel saw or slider, a Holz Her 1203 VPS popped up on Craigslist for $1,875 near my shop. Kind of made the decision for me, and I think it was the right one. It's an older model that has been well used, but it currently works as-is. When I have some time I will give it some TLC. Thanks to all for the great advice. Now the trick is to move the dang thing!
From contributor B:
Take the sliding arm off before moving! If transported with the arm mounted, even a short trip can cause permanent damage.
From contributor H:
Best setup would be a panel saw for sheet goods and a small 10" table saw such as a Powermatic. Really good combo and way less changing of tablesaw blades.