Slot Mortising Machine Tips and Tricks
Advice on bit choice and other operating tips for a slot mortiser. January 25, 2010
Question
I have an older style Laguna mortiser that mounts on a stand for a router. The router is not in the picture. The basic problem is I have to go very slow, perhaps a 1/16" or less remove per pass, taking several minutes to do a mortise. Sometimes it will grab the piece even though it is clamped tightly. It also seems to dull bits quickly. After reading the Knowledge Base on bits and going to the Onsrud site I wonder if that’s because of too small chip removal, and too high a speed (8,000) I use a Dewalt 625 router. I know of other people having success with this set up perhaps I've got a "lemon".
I use HSS and carbide endmills for routing mortises and wonder about other types of bits. I suspect there is more give between the XYZ platform and the router than there should be but can't get rid of it. and don't have a good reference. Am I expecting too much from this machine? Are there better bit choices ? I mostly see CNC bits.
I'd like to replace the router, partly because I lose 1 1/2" of reach between the collet and the wood thereby requiring long endmills and more vibration and partly to allow for drilling and slower speeds. I've heard of some homemade slot mortises. Are there any really good ones? You can see in the picture one attempt at mounting a shaft with chuck and a slower motor - even with the 5/8" shaft it had too much vibration.
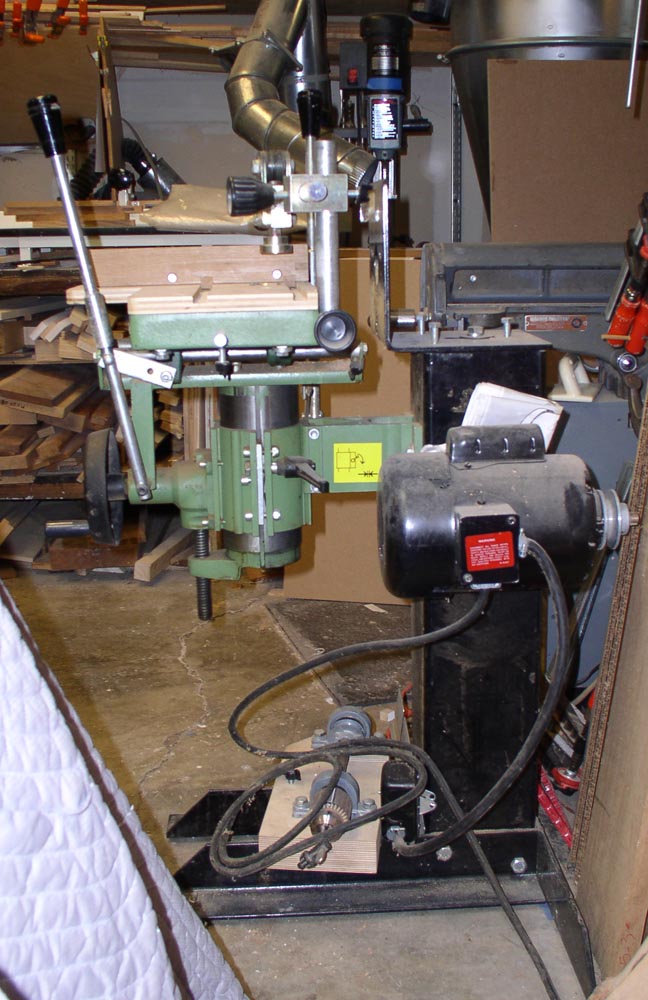
Click here for higher quality, full size image
Forum Responses
(Solid Wood Machining Forum)
From contributor U:
What are you doing with this machine? Why are you running the bits at such a slow speed? What size bits are you using? If you are doing mortises on small pieces like furniture you might think about dumping this machine and the hollow chisel mortiser then buying a Festool Domino. I was able to sell my Robland mortiser with a 3 HP router attached for about $450.
From contributor O:
I have the Felder FD250 mortiser and it has a 3HP motor and runs at 3400 or so RPM. This speed works well with birds mouth bits. I make 1/2" slots 2" deep and 3" wide in about 20 seconds using a back and forth motion and taking shallow cuts in red oak. Spanish cedar is even easier. These bits are available from Felder and are high speed steel and last a long time if you don’t burn them but 8000 rpm is way too fast. If you are going to run that fast you might try a plunge router bit and make several plunges side by side then a sideways pass to clean the mortise up.
From contributor J:
Are you using end-mills designed for metal? If so, are they center-cutting end mills? How long are the mills you're using? Are you sure that the router is absolutely perpendicular to the table surface? Could something be sagging? Think of the mortiser table like the fence of a router table. When cutting from side to side, there's a correct direction and an incorrect direction.
Imagine that you're operating the machine to cut a mortise. The bit is pointed at you, so the cutting end is turning counterclockwise. The side of the bit to your left is moving down towards the mortiser table, while the side of the bit to your right is moving upward. When cutting sideways, you should always be moving the work piece so that the cutting happens on the downward-bound side of the cutter, so that the force of the cut tends to press the work piece down into the table. So, plunge the cutter into the work on the right end of the mortise, then cut sideways by moving the work piece to the right.
If you cut sideways by plunging on the left end of the mortise and then moving the work piece to the left, the cutting is all happening on the upward-cutting side of the bit, which tends to lift the work piece off the table and allow it to move around out of control, a.k.a. "grab."
From the original questioner:
I use the machine mostly to make furniture using loose tenon method most of the time. I don’t think the domino would be flexible enough for my work though it looks like it'd be great to have. I run at the lowest speed because it seems to work better and burns the bits less. The bits I use range from 3/8" to 5/8" and from 2 1/5" to 5" long. Obviously, the shorter and larger ones work best. Most are four flute center cutting metal end mills from MSC. The longer ones are useful for making deeper mortises or through mortises. Are two flutes better than four for this application?
Contributor J - your description of feed direction is very clear and the way I do it as learned by trial error. Perhaps the greatest tendency to grabs is at either end, especially when returning to start another pass when it hits the stop. I need to be real careful and not get impatient. I have checked the parallel as best I can using drill rod – it’s adjustable.
From contributor O:
I think four flutes is too many. More cutting edges means a faster feed rate is possible but if you feed it slowly then there will be more heat and therefore burning. The heat will also cause the cutting edges to dull quickly. When mortising it is also important to clear the chips so they are not cut multiple times and creating more heat. You want a bit that propels the chips out of the mortise. Also, if you are burning the bits then you are probably burning the wood and that will prevent a good glue joint.
On my first mortising attachment the table was not moving in and out parallel to the length of the cutter, this caused much heat and left ugly cuts. Getting the moving table lined up worked wonders. 8k from a router motor would probably work nicely for smaller diameter bits.
From contributor J:
You'd be better off using cutters that are designed for wood (Onsrud upcut spiral bits, for instance). Those extremely long bits exaggerate vibration and grabbing problems. Make it a priority to get that router base out of the way somehow so that you can use shorter bits.Finally, try using the cutter as if it were a drill, and punch a full-depth hole at each end of the mortise before you clean out the stock in the middle. That way you can avoid the grabbing you're experiencing at the ends of the cut.
From contributor U:
I also used only spiral woodworking router bits with the Robland unit I used to have and ran them at around 15 to 20K as I recall. I had no problems with tearout, grabbing or burning. By the way, to improve this machine you might want to replace all of the black plastic wing nuts with the ratcheting handles. Grizzly sells those for a good price in metric sizes. That's what I did with mine.
From contributor A:
I'm not familiar with your machine at all, but it looks from the photo that the router just mounts in a piece of plate steel that is bent at a 90 degree angle to where it bolts to the pedestal? If it were my machine, I'd start by welding some triangular gussets on to keep that thing from flexing, which I'm sure it does.
We use the JDS Multirouter, we've got three of them in the shop. I use titanium nitride coated two flute upcut spiral bits, or the same two flute upcut in solid carbide. Hanita cutters seem to last forever, but are pricey. I also get some from McMaster which are inexpensive and pretty good too. I run them all at full speed, 18-20,000 rpm.
I'm not sure why you're losing so much length in the setup. The plate my Makita router attaches to is at least 1/2" thick aluminum, and I don't need more than a 3" cutter for anything. Maybe you can change to a different router or re-bore holes in that plate to move the router closer to the work? The moving parts of your machine look to be pretty stout, I think you just need to beef up the stationary end.
From contributor F:
I also think your using the wrong bits, four flutes is too many. I have a stationary machine which runs right around 3000 rpm and I use inexpensive two flute end mills from MSC that work very well. I mostly cut hard maple and just finished a batch of white oak as well. No burning, grabbing or other problems to speak of.
From the original questioner:
Are the Onsrud bits you’re talking about the ones the that go for around $70 for 1/2" x 3 1/2"? This mortiser definitely has some design flaws especially the "head". The base was designed to go on the side of their table saw. They just took it, stuck it on a post with the 90 deg plate for the router - I agree that probably flexes. Also the side to side handle is in the wrong place - it ends up between the router and the work piece if you want much movement. Although the router collet gets to within 1/16" of its own base, with plate, etc. it ends up 7/8" from the work piece. Add what you need in the collet and I've used up 1 1/2 - 2" of the bit length before reaching the wood. It’ll be nice to find a different head to mount that would avoid all these problems especially since I'll need to buy a new router eventually. Other than replacing the whole thing which I I'd rather not right now, it'd be great if I could replace the "head". I was disappointed the mandrel and chuck didn't work as others had recommended. It might be worth another try with different bits.
From contributor J:
“Are the Onsrud bits you’re talking about the ones that go for around $70 for 1/2" x 3 1/2"?”
Yes, that's probably them, but it sounds as if the fact that the side-to-side handle prevents you from getting the work close to the router is a big part of the problem. It's forcing you to buy longer, more expensive and more vibration-prone bits than you otherwise would. Perhaps you can re-engineer that handle so it's out of the way?
From contributor F:
Before you go and spend a small fortune on those bits, try out the ones I use and see if they work. I'm using the Putnam end mills from MSC which for a 1/2" x 3-1/2" 2 flute cost $17.02. Your biggest problem is going to be run-out though. If there is any flex in the head, the way you’re describing, your hole is not going to be evenly sized throughout its depth. If you’re going to use this machine a lot I'd suggest spending some time re-engineering it as the others have suggested to try and make it stiff enough to work well. Otherwise now is a good time to be looking for used equipment. Though not cheap, I find my stationary machine to be nice and solid, and perfect for what it has to do.
From contributor U:
One of the things I thought might work better with that unit is to make some sort of a cabinet (beefy) for the jig to mount on with a flat table top for the work piece to sit on. The table top would have a fence setup, a miter gauge for angled mortises and a front fence with stops for repeating mortises. Then you would mount the router to the moving table of the jig so that the bit would be moving and not the work piece. This is based on how jigs like the Felder FD 250 are setup, except that I'm imagining a much larger sized table surface to accommodate longer work pieces. I'm sure there must be someone out there that's already tried this trick.
From contributor J:
It occurs to me to mention that the mortises you're trying to cut seem pretty large for what is essentially a light-duty machine. Deep 5/8" mortises require really solid machinery to do well. You're trying to cut them with a less-than-rock-solid jig, with bits that are longer than they should be and that are not designed for cutting wood. It seems like a perfect storm of compromises and short-cuts. It may be that there's no one simple solution because you're pushing the envelope on all sides.
From the original questioner:
It is "good" to learn that part of my trouble is pushing the envelope of the machine. I can get very good mortises nice sliding fit if I go very slow and not too deep - just seemed to take way too long. It sounds like I can't expect to do through mortises from one side unless I can redesign.
Contributor F - I think the bits you’re talking about are similar to the ones I've been using except I need to go with two flutes and make sure they are designed for wood. I'm willing to invest in a few $70 bits if it would solve my problems but I think not.
Contributor O - the idea of reversing the plan like the Felder didn't occur to me. It might be an "easy" way to get the handle out of the way and get the collet closer. Any drawbacks to this design?
Contributor J - I think you're right about pushing the machine. Luckily I don't get large exterior doors with through mortises very often. These days I could use a few more of those jobs actually. Unfortunately there is other equipment higher up on my wish list than replacing this one, especially if I can get it working better.
From contributor O:
I bought my Felder FD250 used and it had bad bearings. I had the bearings replaced but I still have a little bit of run-out resulting from the chuck not mounting perfectly on the motor shaft. This makes my mortises a little larger than they should be but I compensate by making the tenons larger. Anyway, in an effort to fix this I priced a replacement motor from Felder and a new chuck. The chuck is around $180 and the motor is between $350 and $500 depending on what motor you buy. You could get the Felder motor and chuck and mount them on your set up. Laguna sells a set up like yours with a motor on it. You could probably retrofit one of their motors too.
I started with a mortising attachment for a Felder CF731 that ran the mortising chuck off the end of the planer cutterhead. Having the mortising bit mounted to a 1700 pound machine is nice but the table size for the work piece was a limitation. Now that I have the FD250 with the moving motor and a stationary work piece I find that moving the motor is more work than moving a door part. The heaviest thing I usually mortise is maybe an entry door style around 90" long so not really that heavy. The motor on the FD250 is definitely heavier than that.
From contributor R:
While I agree that the domino would be great for loose tennon joinery, I love my Leigh FMT, while lots of people complain about the price, you've got more wrapped up in that slot mortiser and the hollow chisel. I don't do big production, but the Leigh will handle one man production situations well. Plus you can detach the router for other tasks. I have a Makita 1101 dual base with the fixed base on the dovetail jig and the plunge on the FMT, works great.