Solar Kiln at Work
Here's a look at a newly completed backyard solar wood drying kiln with its first load of lumber. March 28, 2012
Question
I just wanted to let Dr. Wengert know that I recently completed a small solar kiln and thank him for the info he has so unselfishly shared over the years.
The kiln is sized to dry 300 bft and is loosely based on the design from American Woodworker. Access to my kiln is from the front as the opening is hinged and lays down to form a ramp. The roof is also hinged and rests on a prop at either end when loading/unloading.
The pictures show it loaded with the first charge of air-dried walnut. The charge has been in the kiln now for almost four weeks and I fully closed the vents a few days ago. With the 100+f temps we have been having lately in East Texas, I'm hoping the wood got hot enough to sterilize it.
Thanks again, Doc, for your knowledge sharing.
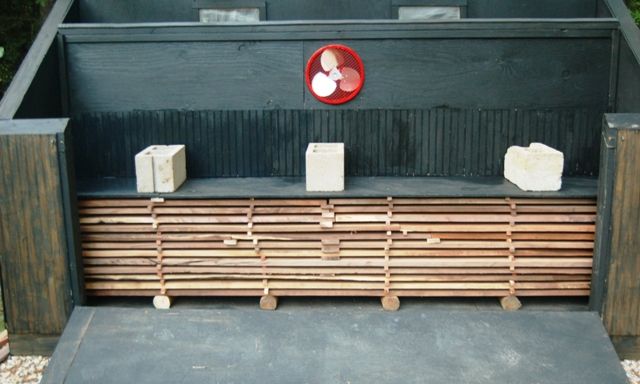
Click here for higher quality, full size image
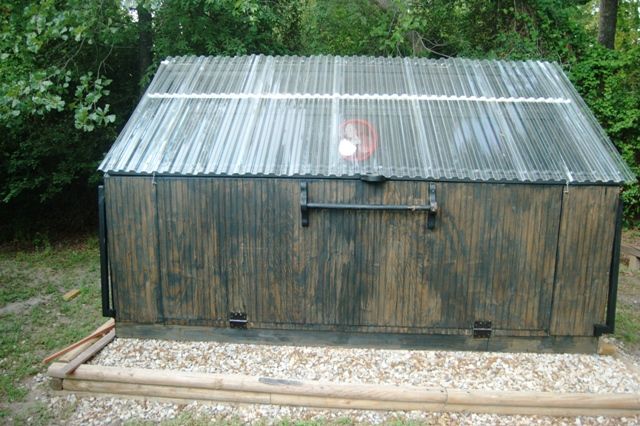
Click here for higher quality, full size image
Question
From contributor A:
Job well done!
From Professor Gene Wengert, forum technical advisor:
Excellent!
From contributor T:
Nice job. You can buy digital thermometers with memory cards now for dirt cheap. This way you won't have to guess at how high the temps got; you can see the full history. In my opinion it's an essential tool for any kiln.
From contributor L:
What length fits in there? I think I have a similar situation to yours. I only need to dry about that amount. Thanks for posting pictures.
From the original questioner:
Thanks for the tip on the digital memory thermometers. I have a regular thermometer hung on the back of the fan plenum and was seeing 140 degree temps in the afternoon with 95 degree days. I'm away at work now so I have no way of knowing what the kiln temp is, but I'm assuming it's higher since we've had 100 - 103 high temps the past few days.
The kiln is sized for 10' long planks and a 30" deep stack. Outside dimensions are 11' x 4' with PT 2x4 framing, r-11 insulation and PT 1/2" interior sheathing. The roof angle is 37 degrees. I picked 10' as the board length because my shop ceiling is 10' high.
I don't have a mill but occasionally take logs to a sawyer for milling. Between friends, my own small acreage and storm-downed trees, I manage to keep a stack air-drying all the time. Now, I can get the wood dry enough for furniture building, which is my primary interest.
From contributor W:
That looks great! Thanks for sharing. I need one to dry about 500 BF at a time, so your experience has been very informative and motivational!
From contributor D:
Nice! Looks like there's a back section... What's in it?
From the original questioner:
There is not a back section. What you are seeing is the fan plenum and extensions. I used some leftover 3/8" beadboard to cover the gap between the bottom of the plenum and the top of the lumber stack. That forces the fan air to go through the stack instead of across the top. I'll eventually replace that leftover plywood with a black tarp.