Table Leg Attachment and Veneer Details
This thread offers good analysis of table structure, veneering techniques for complex shapes, and the business problem of trying to compete with cheap manufactured goods as a custom furnituremaker. October 1, 2010
Question
I've been asked to provide a quote for a walnut dining room table (30" x 60" x 30"). What would the strongest method of joining the legs to the top be (so that 2 leg edges are flush with the edges of the top)? I'm also open to suggestions on the best materials for construction of this table. I'm thinking veneer (paper-backed, bubble-free walnut applied with Weldwood contact cement) to 38mm (1 1/2") European poplar lumber core substrate. My thought is to use the same lumber core material for the legs. I'm thinking I'll use a catalyzed polyurethane finish for durability.
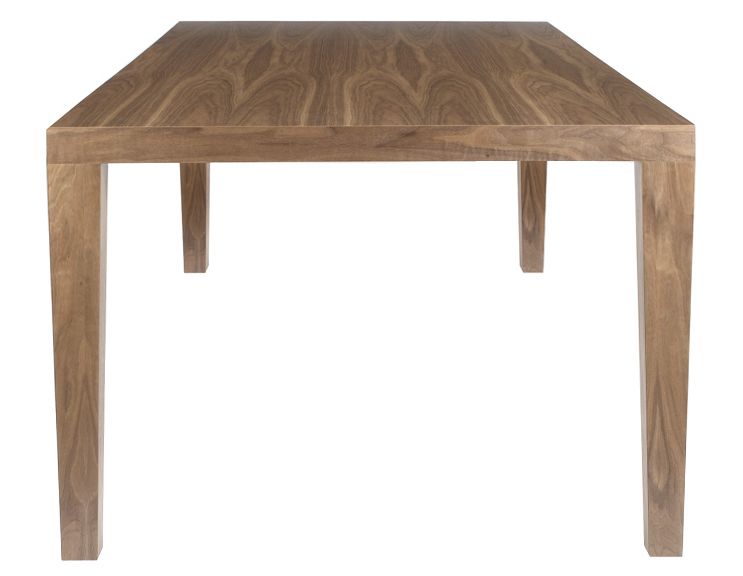
Click here for higher quality, full size image
Forum Responses
(Furniture Making Forum)
From contributor S:
How wide are the legs going to be where they meet the table? With no apron and no stretchers, there will be a lot of racking stress on those joints. My thought is that a mortise and tenon is the only joint that might stand a chance over time. I would have worries about making a table that size with no leg supports.
I would agree on the veneer core as a substrate over MDF, as MDF would be too weak for the leg joints, in my opinion. Solid wood would be an option as well.
Does the customer want a low maintenance finish that will be more expensive to repair in the future, or a more repairable/less durable finish? Do they want a filled look or more natural?
From the original questioner:
Thanks. The racking stress concerns me too. I wonder how the table in the picture was built! The legs appear to be about 2 1/2" or so where they meet the top. I thought about using mortise and tenon as well. Though much less refined, I also wondered about going through the top with two 1/4" lag bolts straight into the legs, recessing the heads/washers below the table top. I could then fill the remaining void, and apply the veneer to the top. I wonder if I might gain more strength with this method. What do you think about this idea?
I think the (potential) client wants a natural finish. She referred to semi-gloss for the sheen. I normally use a catalyzed lacquer finish, but recently learned that this finish can crack when applied to paper-backed veneer that is applied with contact cement. I would opt for a finish that is low maintenance and highly water/stain resistant.
I attached another picture that the client sent me. She seems intent on not wanting to see an apron.
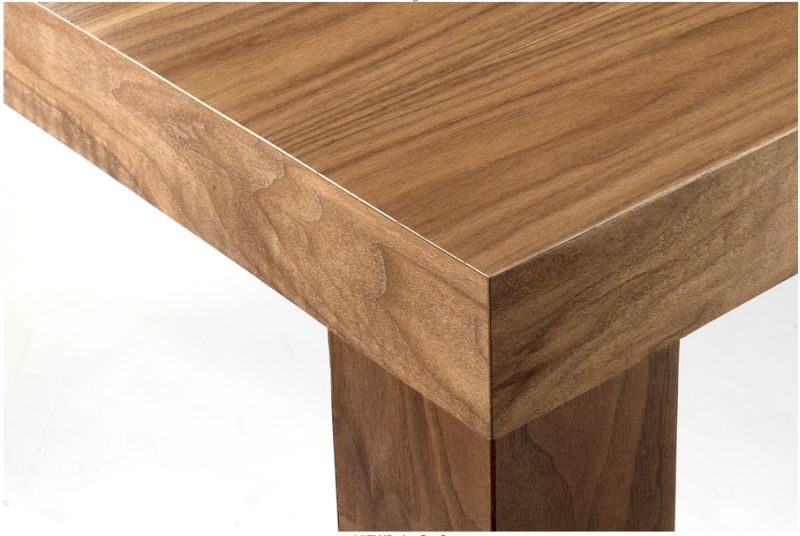
Click here for higher quality, full size image
From contributor J:
If the client likes that table, tell her to buy it. I know times are tough right now, but that's not an excuse to be knocking off somebody else's work. That is either a low quality table that's wobbly as hell, or somebody has a tremendous amount of engineering invested to get the thing to work. And contact cement of any type is never a good adhesive for veneer, paper backed or otherwise.
From contributor S:
Contributor J makes a good point, but if you do proceed... I don't see the table as being robust enough with that construction, but it all depends on the end use. In my house (with two kids) that table would not last - period. However, a childless, refined customer that may rarely even use a table might be happy with it.
If the latter is the case, I still think M/T would be the way to go. I would be afraid that the lags could loosen over time, resulting in wobbly legs. Epoxying them in place could help I guess.
I would explain to the customer the poor design issues as related to the ruggedness of this table. Maybe you could propose a similar but alternate design that she would be happy with. If you do decide to proceed with the table as shown, consider using an offset tenon on the top of the leg that is maybe 1/8" or so from the inside leg edges and at least 3/4" (or more) from the outer edges to allow enough material in the table top to prevent breakage. That would give you a 1 5/8" square tenon based on the 2 1/2" leg that you reference (3" wide leg at the top would be better, though). I would stop the mortise just shy of breaking through the top to ensure that it doesn't telegraph through your veneer. This would be your best chance for success, but I still wouldn't like it!
If she wants a natural (not filled) look, I would consider a thinned polyurethane finish; it offers good protection without the plastic look (low build).
From contributor C:
I am not trying to be rough here, but man, run the other direction right now! You will not build this table and make any money and you will not make this client happy, period. Imagine yourself as a teenaged boy, and ask yourself how long it would take you to bust a leg off that thing. The picture shown here is poorly designed, will not last, and what's more, the Chinese will pump out 50 of them for what you can build one for. If you are intent on working with this client, find out how much money they have to work with and design something that fits the budget, that will stand up to that teenager, and that will still allow you to make a living.
From contributor E:
Oh come on - that table is very buildable. A 2 or 3 layer MDF/yellow glue sandwich with 1/2" poplar edges for the top. The heavier, the better. Veneer the edges before the legs are attached, but not the top. Legs out of solid or laminated poplar, vacuum bag veneered (no paperback) using powdered plastic resin, so you have room to sand the leg/top joint flush. Double-tenon and lag screw the legs from the top, bondo and sand the lag head hole flush, and bag the top. If you can, get your client to agree to a small relief kerf between leg and top. Her design is not as strong as some, but a disclaimer/no warranty expressed or implied statement will cover you. I'd say "Go get the job!" if you've veneered before, but if not, you might be in for a learning curve. Build one for yourself first. The materials will cost you next to nothing, but it's a labor-intensive job that's going to require you to develop some veneer chops. I'd estimate $2k in my neck of the woods.
From contributor J:
How you gonna bag the top after you've glued those legs on?
From contributor E:
Excellent question. Rather than a urethane bag, I make my own disposable bags out of the embossed Airtech plastic joined together with butyl tape. I'd do 4 socks for the legs and join them to the top bag. A roll of that embossed Airtech bag material is expensive, but the stuff is magic, and is worth every penny for bagging oddly shaped parts. I discovered it from my landlord, an aerospace contractor that's building (was building?) F-22 parts. Before I discovered Airtech, I'd been known to occasionally use Visquine for the one-time bags and bubble-wrap as bleeder mesh (face palm).
From contributor N:
Sandwich a quarter inch steel plate at each corner between two layers of whatever substrate you use. Run half inch all-thread down the entire length of the leg. Make a recess at the bottom of the leg and insert a quarter inch thick square piece of steel, put nuts on each end and tighten the heck out of them. Leave the bottom of the leg open so in the future you can tighten them if needed.
From contributor S:
I never said the table is unbuildable, just not the best design for strength. Again, it all depends on what stresses the table will be subjected to, and what the customer will accept.
I definitely agree with a signed disclaimer if she will not consider an alternate design. I am not a veneer expert, so I'm not the best one to comment on that part of the project. Using MDF with 1/2" poplar edging for the top would result in a weak corner in my opinion; just not enough meat at the mortise walls. I would use something stronger than poplar for the legs as well.
Contributor N's idea is a good one as well - I think it would work.
From contributor P:
I'd love to be at that sales meeting: "Mrs. Homeowner, I'd be happy to build you this table. It will cost 15x as much as the Chinese version you found, and I refuse to guarantee it." Should go over great.
You need to think carefully about what aspects of what you do have market value. People assume that custom makers provide a product of higher quality no matter what the design, so if you accept this commission and build it, you are on the hook for it for a long, long time. Even if you build it contributor E's way (good luck!) it will still be a delicate table. If you want to succeed as a furniture maker, you need to develop your own compelling designs that can be produced at a reasonable price. You will then have the opportunity to omit troublesome techniques and details, and build in the quality your clients expect.
People are willing to accept crappy design and construction if it's cheap. So that table with a Chinese price is viable in the market. Put a handcrafted price on it and you need to be ready for a whole different set of expectations. The only way to survive as a business is to control the product design - otherwise you are competing with very cheap labor and very low expectations, a game you will lose.
If I had to do a table like this (and I have), I would make the top out of solid 8/4 walnut, the legs out of solid 12/4 walnut, and tenon the leg through the top, placing the tenon as far from the edge of the table as possible. Then you would have a nice detail that demonstrates that the piece was made by a real craftsman. If she can't afford that, move on. You can't work for everyone.
From contributor I:
I certainly agree with the responses. Recently I was asked to refit an antique full size bed to fit a king size with rounded corners. I told her that any way it was done, it would look like it was cobbled together and I wouldn't have anything to do with it. But maybe she will appreciate the direct reply and ask for something reasonable next time. You can always hope. In the past I have turned down work from her that involved fixing veneer on lesser quality Grand Rapids furniture. Maybe we can train her.
From the original questioner:
I want to thank you all. It's great how people are so responsive at WOODWEB!
As was pointed out, I'd be knocking off another person's/company's design. I'd rather not do that as well, but thought maybe this lady is looking for a particular size, or the table has been discontinued. I did have my doubts about this person, but times are very tough for my business right now, so I feel inclined to take what I can get.
I took the route that some of you have suggested. I have an architectural background and like to do design work. I presented her with two renderings each of two versions of a solid walnut dining table I had designed some time ago. My designs were very clean, simple and contemporary-looking, and maybe along the lines of what she might appreciate. I'm not too experienced with veneer and prefer taking a solid wood option. I also pointed out that the design she is interested in is not structurally very good; that it's on the weak side as many of you have pointed out. It's been 4 days ago now since I presented her with my information.
Like so many people, she is not offering the courtesy of a response. Maybe it's for the best that I didn't get involved with her. The upside is that I got many very good responses to my post. Thanks.
From contributor L:
I built two tables similar to this 20 years ago for my sister and her kids. Still in daily use in her kitchen. Tops 1 3/4" thick solid cherry laminated from squares. Legs, 3 1/2" solid cherry laminated squares. Attachment: multiple through tenons about 1/2" wide, spaced 1/2" +/-.
Titebond glue. Tenons line up with the grain direction of the top. Finish 1/3 gloss urethane, 1/3 Thompson's Danish oil, 1/3 naphtha, 10 coats applied as in French polishing. Shows some wear but has never been refinished. Joints still solid. Tops are about 44" square. The only trick is well fit joints. The style is called Parsons table.