Troubleshooting CNC Crash Issues
This thread never gets to the bottom of the problem, but the conversation about why a CNC is repeatedly crashing does shed a lot of light on programming and mechanical issues with CNC control.May 26, 2011
Question
We own two German CNC’s from a reputable Distributor in the US. We are having continued crashes that amount to $ 20,000 by now. The machine is built in 2006 but is not capable of knowing its own tool information. The clearance between router and drilling block is very narrow and we have now a lot of instances where all the tool data is correct, the program generate just fine, but when the router performs a routing operation the drill bits and saw aggregate are one inch too low at times, hit the part and bent everything that is in its way with serious damage. The machine distributor says that it only has one z-achses and needs manual supervision, therefore it is operator error.
We have now serious precautions but today our operator entered tool 182 instead of 128 and we have the same huge mess on hands again. Me as an owner and my operator are completely frustrated how easy it is for this nested machine to crash. All other CNC’s we’ve owned never had this problem.
My questions are this: Doesn’t a CNC machine self diagnose what it can and cannot do during the NC-Generation? Does anybody else have a similar problem?
Forum Responses
(CNC Forum)
From contributor F:
It does sounds like operator error. If you tell the machine to pick up tool 128 instead of 182 then that is operator error. Everyone wants a machine that is idiot proof but no one is willing to pay for one. If a machine could be completely problem free and prevent all operator mistakes you could not afford it. If you put diesel and not gas in your car it’s your fault. If you hit something with your car it is not the car’s fault. People/operators must be responsible for their actions. I of course do not know your operator but many companies have button pushers not operators. These are complex machine performing complex operations they require operators not button pushers.
From contributor D:
Leitz tooling was developing a tool identification system a few years ago. It involved a chip imbedded into the tool body and a scanner on the tool changer. Even if the operator loads the changer improperly, the wrong tool couldn't be picked up. I never followed up to see if they ever implemented it, but it seemed at the time they were almost done. Recession hit about then and buying new stuff seemed superfluous though, without us having a problem. A consultation with your factory CNC tech and possibly Leitz along with them would be a good idea. You may have to do something as easy as greasing the drill bank assembly to insure it doesn't jam in a lowered position. A good tech will not only fix broken things, but diagnose what caused the problem in the first place.
From contributor H:
If the problem is always a low Z-axis, and most of the time the coding is correct as you specify in your first paragraph, then perhaps you need to look at the mechanical support of the Z-head. Is it drooping during operation? After a crash can you confirm the actual Z-height vs. the programmed height?
From the original questioner:
The machine is a 2006 Weeke BHP-200. Let me be assured the tool data is correct but the clearance between router and drill head is ridiculously small. Any operator can enter a wrong tool # and I can see the collet hitting the part, but this should not mean that all other tooling are in the way as it is in our case. Does anybody have a older BHP-200 with similar problem? My understanding is that newer machines have 2 z-axes for routing and drilling to control the issue we are having.
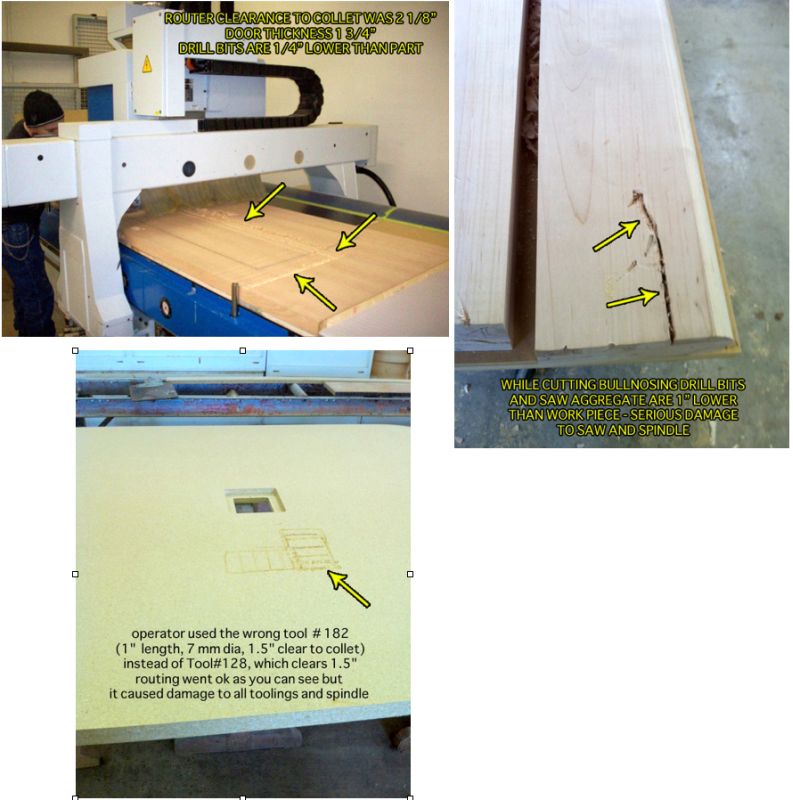
Click here for higher quality, full size image
From contributor H:
Could it be possible that your spindle has been replaced and is mounted too high?
From contributor M:
There is definitely a problem with the machine design. I have seen this with this particular manufacturer, as well as others. I am sure it was just an engineering oversight, but you are stuck with the end product. If your operator is programming at the machine, I don't see a way around the potential for crashes. If you are using Mastercam, Alphacam, or similar software to generate code, then there is always a possibility for safety checks in the post processor. If unsafe, predictable mistakes are made, then the post processor can bail before the bad code is output. You can contact your software specialist for more information if you have the third party software, otherwise, you are stuck with the machine dealer for a solution. Good luck, I know your situation is frustrating.
From the original questioner:
All the accidents happened with programs generated in Interiorcad/Vectorwop and reviewed and adjusted in Woodwop. The damage with the 2 3/4” bullnosing happened after carefully reviewing the operation by dry running the program with two people watching. We simply did not expect this to happen when we actually ran the program with the part in place. What I am trying to say is it can happen very easy that one thinks about the part and the involved tooling and focus on the tooling that is simply riding along. I am shocked that there are machines out there with problems like this and this is acceptable. I would not call this a CNC but a dangerous weapon that self destructs itself.
From contributor M:
I am not familiar with Interiorcad/Vectorwop, so I don't know if anything can be done on that side. Looking at the machine, I see that it was designed for panel processing, but you are using it to do other types of work that is causing impact issues. This stuff happens, but it needs to be planned for. I have a couple of questions. First, is it possible to switch from 70mm to 57mm drill bits? If nothing else, that will buy you 1/2" of clearance.
Second, can you switch tool holders that will give you more length from the spindle face? Without knowing the type of spindle you are using, I can't be sure, but most tool holders can be obtained with a longer gauge length. This will buy you more room for drill clearance. It is not a lot of room, but it sounds like every mm counts. Sometimes you have to think outside the box to obtain the clearance you need. This includes removing tools during certain operations, clearing you tool changer of tools or changing their position, editing code so that the machine moves in rapid from a safe angle to the target position, etc.
All of us that do architectural work have to work around machine, or software limitations, regardless of the manufacturer, or dealer. With enough thought, I'm sure you can get it done without damaging the machine further. As for getting any retrofit from Stiles, or reparations for past incidents, I wouldn't think you have much legal standing, but you can always ask them about what they can do to make you a satisfied customer.
From contributor T:
I've seen this happen before. Here's a simple question. When your router is in the down position for working what is the vertical clearance between the tip of the router and the tips of your drill bits? I'm willing to bet it's somewhere around 1-5/8" which means you can't route 1-3/4" deep without causing what you see.
From the original questioner:
My 2 flut cutter is 1 1/4" cutting length - collet nut to tip 2.125". The drill bits are only 3/4" higher when routing through 3/4" material. What is a normal clearance? I tried extended tool holders but I get an error message that the tool is too long when trying to deposit. What is strange is I took this picture with the air disconnected and I have almost 5" clear. Thanks for your continued input.
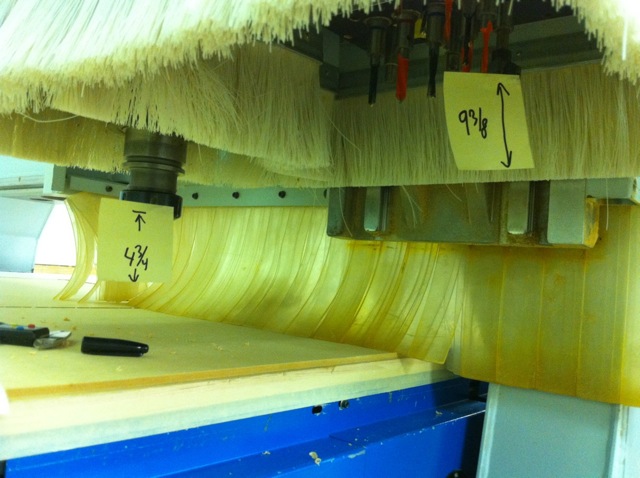
Click here for higher quality, full size image
From contributor H:
Perhaps your drill bank is being sent down to the lower height when it shouldn't be? Perhaps you could look into the mechanical settings of the drill bank.
A few more thoughts on that last point. Our CNC sends out signals to the air cylinders to open or close, thus activating and deactivating devices. If you drill bank is dropping for the fully raised position to a mid-point position when the machine starts then it is likely a command is being sent to instruct it to do so. You can look into that command sequence to see what is happening. Have you shown this photo to the distributor? This might help them help you solve the problem.
From contributor M:
Ok, so there is a chance that the drill block did not drop when the air bled out of the system. There could be a bind, or a reason why the drill block did not drop to the mechanical stop at the bottom of the slide. So, is it possible that when the crash happened that the drill block stayed in the work position, or dropped when the machine was routing? You should have way more than a couple of inches clearance on an industrial machine like that. I'm starting to wonder if it is a mechanical or electrical issue.
From contributor E:
The status shows in the picture is the right condition when the router is routing, there is no way the machine was designed to run only 3/4" different between router bit and drill bits. If air was connected then the drill block will drop then it means that the air was direct into cylinder to lower the drill block. You might want to check the solenoid valve which control the cylinder the spool may be got stocked or may be the valve was manual active and in lock position. The other possibility is the control relay was short and provided power to this valve all the time to lower the drill block all the time.
From contributor H:
Another possibility that comes to mind is the electrical power supply. We had an intermittent problem that was very difficult to isolate. One of our air solenoids would cut out (deactivate) at odd times and our dust skirt would pop up. This could happen at most any time and it literally took a number of years to figure out - all with extensive help of the machine manufacturer and the control software company. In the end it turned out we had a slightly underpowered power supply. Every now and then when the power demands of the controls (not the spindle) would be just a tad higher than usual and the dust skirt would pop up. This of course was more an annoyance than a critical problem such as you have (what's a little more dust left on the part) but if you are having an intermittent problem with your drill bank this is another place to look.
From contributor D:
Depending on whether or not you really need the drill bank, one option no one has mentioned yet is just to remove it entirely. I had an issue with a Pnuematic chip deflector shield on a Masterwood that got stuck once in a down position. It's been in a drawer in a toolbox for about seven years now. If you aren't drilling a bunch of holes with this machine, I wouldn't hesitate to remove it. It really only saves time when drilling dozens of holes at a time anyway, like on bookshelf and cabinet sides. A few dowel holes can be made with the main router pretty dang fast with this machine, and you still have the other machines which can handle your production drilling.
From the original questioner:
I don't know how the drill bits could not be in the correct position? While I agree 3/4" clearance is asking for trouble, wouldn't we get wrong drilling z-results if that would not be the intended height? What I find hard to swallow how Weeke can get away with the left hand does not know what the right hand is doing. We had at least seven crashes during tool change. The router lowers to pick up the tool, the drill bits dig into the spoil board and the machine stops.
Below are two images showing the holes in the spoil board ones on the left, ones on the right side. Thanks for all your ideas. Removing the saw blade is a good idea, it would have us the biggest damage during the last crash. I will also use 57 mm drill bits in the meantime.
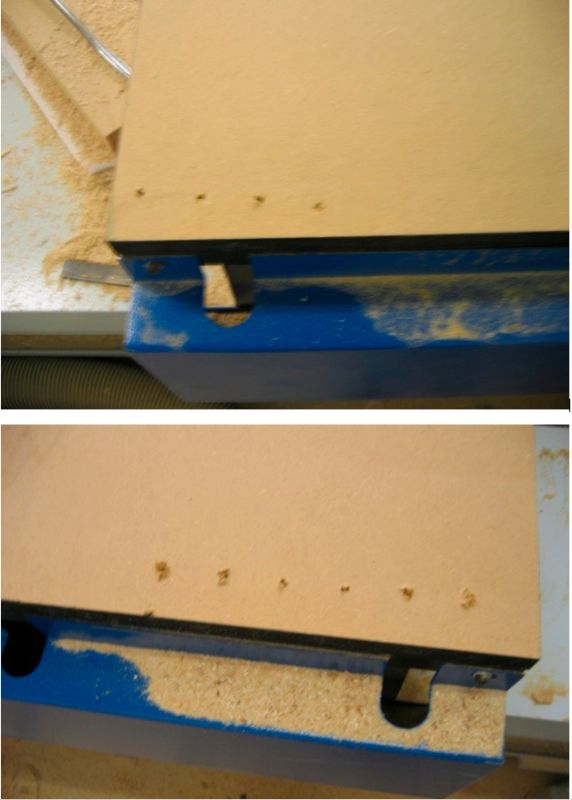
Click here for higher quality, full size image
From contributor M:
It sounds mechanical to me. There should be two proximity sensors on the drill bank ensuring that the work unit is in the proper position before attempting anything, including tool changes. Have you had an actual tech come out to inspect the machine? What you just included in the post about the tools hitting the spoilboard during a tool change is an important clue as to what is wrong and you just now mentioned it. Have you told the techs about this when you talk to them about the drills hitting the work piece?
From the original questioner:
I sent a detailed report to Stiles with all the pictures previously showing more than a year ago. We mentioned to three technicians the spoilboard issue. They said there is nothing they can do since it is not crashing while they are looking at it. We also sent as recently as one month ago requested files to Tech support but never got an answer back. I will talk to them where the sensors are and look into it.
From contributor Z:
This is definitely an interesting issue. I really doubt that entering T182 vs. T128 has anything to do with the crashes. Normally, this would only result in the wrong tool going deeper or not going deep enough based on it's different offset values. If I were there trying to diagnose the problem, the first thing I would do would be to remove the drill bits, saw blade and router bit in T182. I would then run the same program with a +Z shift and watch the drill head. If the drill head came down, I would look at the code to see if there was an M code (like M21) to see if it is being told to go down. If there was no evidence of a code to drop the head I would then check the relay that controls the solenoid for lowering and raising the drill head. If the relay is getting energized then you know it is a signal from the PLC. If it is not getting power then it would point to an intermittent contact issue. At the end of the day, my opinion is that the PLC should be handling this issue.
The PLC should have a logic that would prevent any axis movement if both heads are in the down position (checked by proximity switch) or prevent axis movement if both heads are down but the drill head contactor is off. The reason I say this is because some machines can do a tool change while drilling but most machines with this function will hold the tool change if the Z axis is below a pre-set value. The proximity sensors are there for a reason which is to monitor the state of the machine. With all of the possibilities (M-code, coil, solenoid, and PLC) the chain of command ends with the PLC which should not allow the machine to move under these conditions.
From the original questioner:
I received an email from Stiles that the crash is operator error which brings me to the question if Weeke can just say it does not do collision check on this machine. Stiles shows a diagram and points out that the operator should check manually the difference in the tool length between router and drill head and check for crash possibilities. My question: Isn't it the machines job to check for collisions or can a vendor just blame the operator when its own software Woodwop/NcGenerator doesn't do the job of checking for clearances?
From contributor M:
No. It is not the machines job to make sure that a crash will not occur. It is assumed that the machine is programmed and set up properly. If you handcuff a machine to the point of never crashing due to operator/programmer error, you would never be able to machine parts outside a narrow scope of machining processes. For example, if I need extra clearance for a part that is extremely thick in some parts and I need to cut with the spindle out of the work position (up), then I want to do that while accepting any risks to the machine that is involved. I want to make that call, not some engineer trying to make a machine novice proof. I understand your frustration, but from the posts, it is not real clear whether all the trouble is control related, or simply bad set ups. By your admission, operator error played a key role in the crash involved. Getting the machine to repeat the errors will help a whole bunch. Getting video of the issues would be even better.
From the original questioner:
Contributor M - per your recommendation I tried out the extended toolholders that Stiles provided after our first crash but all I am getting is an error that the tool cannot be deposited ( 151mm is to long). It seems extended toolholders are only for extremely short bits like 1/2" x 5/8" cutting length. Below is the height difference 6 3/4" on our BP150 versus 3/4" on the BHP200. Anything other than 3/4" Material thickness is asking for trouble and extreme risk of crashing this machine.
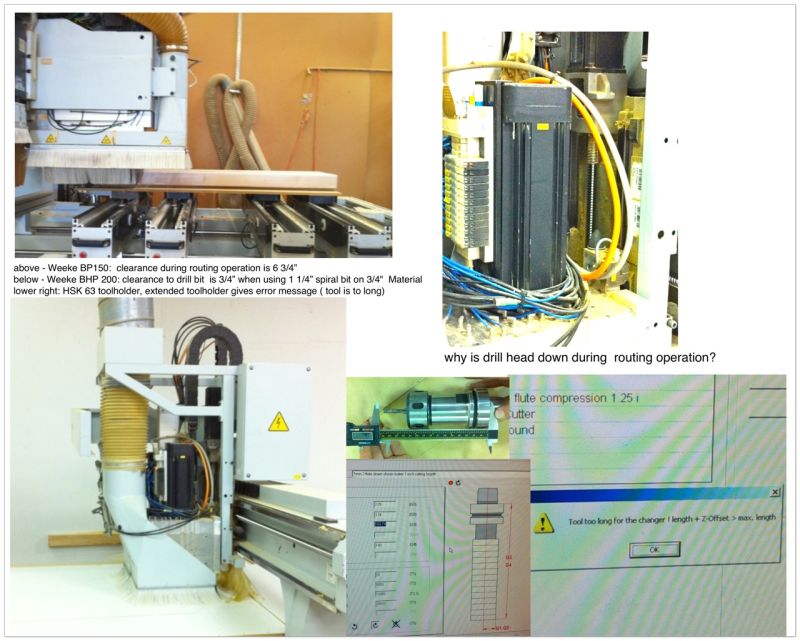
Click here for higher quality, full size image
From contributor A:
I understand what you are saying and there is something definitely wrong. My question is if the router is down in the cutting position, is there actual physical travel for the drill bank to retract higher? What I mean by that is linear slide and screw to retract it? I understand it's not but can it? If there isn't, obviously the machine's not going to do what you want to do period. If there is, you need to have Stiles reprogram the macros or if it uses limit switches to retract the drill bank higher.
There is also obviously a maximum length tool that the machine can handle and if the extended tool holder is to long with the bit you are using, the combination of a different holder and cutter might get you just under the maximum. Somehow you need to find that magic number for the tool length and determine if at the maximum length you will achieve the depth of cut you need.
Maybe you need someone to come in and give you a few minutes of consulting and see if the machine is even capable of functioning the way you want, whether it’s a wood guy or machine shop type person.