Troubleshooting Cracked Laminate Near a Sink Cutout
Square inside corners and drilled holes are potential trouble spot in a laminate surface. February 17, 2011
Question
We are in the process of repairing a couple of fairly new salad bars that have cracks in the laminate where the grille cutout is. Below is a picture of the existing unit for clarity. We are thinking of drilling a 3/4" diameter hole that will radius the inside corner and eliminate the small hole through the laminate that is used to attach the grille (similar to the pencil line). It will still be hidden behind the grille. Seem logical? I’m also debating whether to remove the existing cracked laminate that is laminated to the stainless steel. Would we be better off leaving that on to act as a sort of buffer between the dissimilar materials? I have contacted the manufacturer and they have not seen this issue before.
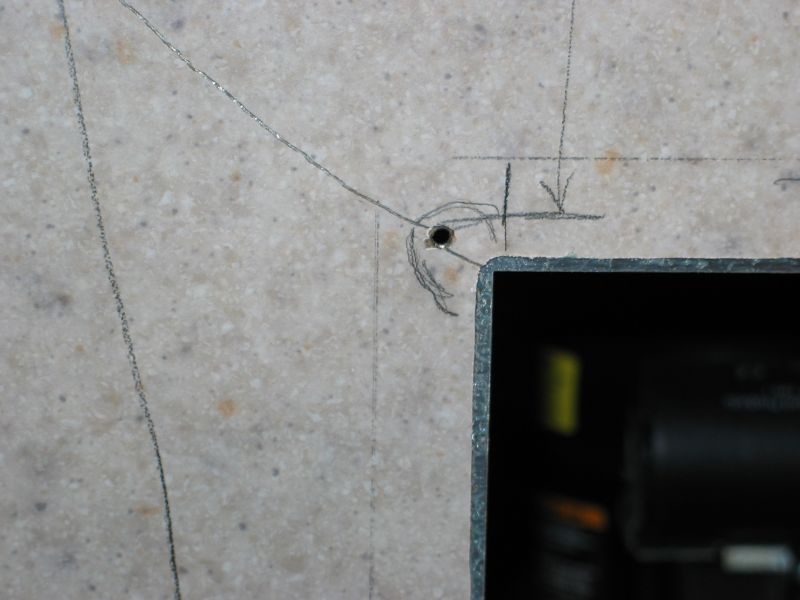
Click here for higher quality, full size image
Forum Responses
(Architectural Woodworking Forum)
From contributor E:
Somehow, I have a feeling that that crack is related to heat from the grill. The screw hole is just a weak point (and looks a little chipped out, also) where the stress can relieve itself. It looks like you can see the stainless under the crack, where the laminate has shrunk enough to open a gap- this does not bode well for future repairs or installations of this type. Maybe you should try to talk the customer into a metal-mica covering that won't have such a difference in material/shrinkage. What kind of glue was used to laminate the top?
From contributor H:
It looks to me that the original screw hole wasn't drilled out but pushed through with the screw - that would cause stress in the corner. The difference in material expansion is the other issue. The laminate is made of paper and expands and contracts with changes in humidity, SS doesn't. The corner cut-out is a stress point. I'd try and fix it as long as I wasn't expected to take on the original design flaws, in other words it might crack again, not my problem.
From contributor F:
The cutout should have some slop in it at least a 1/16" all around for contraction and expansion.
From the original questioner:
To clarify a couple of things: this is a salad bar, no heat generated. What you are looking at is a vertical surface, one side of the cooler, opposite side is mirror image and cracked as well. I believe the laminate and the cut outs are pre-cut on a CNC and is attached with contact cement. The gap between the laminate and the SS is the 'slop' that Alan is referring to.
I am fixing this under a warranty claim and I'm being paid by the manufacturer. The end user is a regular customer (hospital) that I do a lot of work for so like it or not this will become my responsibility. I don't want to hear about it again once this is done since we've had to drill out rivets, etc. to get it to this point. I also think when the screws were installed for the grille that a nominal pilot hole was drilled, not enough to prevent the stress at that hole.
I believe the method outlined in my original post will prevent a recurrence. I am surprised that the manufacturer has not received reports of any other failures. Regarding the dissimilar materials, this is why I'm wondering about leaving the existing laminate in place and just laminating over it. There would be less potential movement and an extra layer that could move independently between the SS and the new laminate. Any thoughts on leaving the existing laminate?
From contributor M:
You say no heat generated, but then you say there is a cooler, which if this is a vent cutout it is there to displace heat. Metal can expand and contract quite a bit and I would bet the screws didn't give when everything else moved at dissimilar rates. Going over existing laminate is not uncommon if the original has a good bond. A good cleaning and light sanding would be required, and I would give a generous amount of room around the screw holes on the new layer.
From contributor G:
Laminate cutouts should always have a radius on the inside corners. It may be the problem or a factor. We used to build photo booths and we had trouble with the laminate cracking (also on a vertical surface) on the inside corners. What fixed it was leaving the inside corners radiused.
From contributor K:
Could you laminate this with strips (stile and rail) that would eliminate the inside corner stress and allow for expansion and contraction?
From contributor G:
Yes it would but the appearance would be unacceptable, with a lot more work.
From contributor K:
Pat, it's not clear from the information I see whether there is much that shows above and below the grill. If it's just a little bit (2" or so) it might not look that bad and would mean no problems in the future. If it's 2 ends how much more work could it really be?
From contributor G:
Good point I was mistakenly thinking of my door problem. The way we would cut laminate that has to be joined in this manner was to lightly glue it to a sacrificial sheet and cut the pieces we need. This is more work but necessary to get a really good joint. I know Betterly has a router setup for this. Additionally joints around water are generally not a good idea. The above aside, it’s still good thinking. I still say the way to fix this is to leave a radius on the inside corner, this method was used on thousands of doors subjected to cross country (a vibration test) shipping and resolved the problem.
From contributor Y:
There are two serious issues here. First is the squared inside corner. Second is the location of that screw. All of the laminate manufacturers address these issues in their instructions and warranties. Here is a quote from the Abet Laminati instructions: "To avoid stress cracking, do not use square-cut inside corners. All cutouts should be routed or filed to ensure smooth edges. A radius of 3.175mm or larger in the corners is recommended to minimize stress cracking. Drill oversize holes for screws and bolts."