Troubleshooting Hinge Hole Blowout
CNC owners try to help a colleague with a quality problem: blown-out hinge holes. March 12, 2015
Question (WOODWEB Member) :
I'm baffled as to why the 35mm drill bit on our CNC is leaving the holes looking busted up. It's drilling in fine but upon exit is where the issue lies. Does anyone else have this and know how to fix it? I think it might be the depth that I’m drilling. I'm drilling 5/8" deep but the height of the cutter edge is only 1/2" high. Maybe it's the extra depth that is causing it? Oh and it's a brand new bit, but it also happens with sharpened bits.
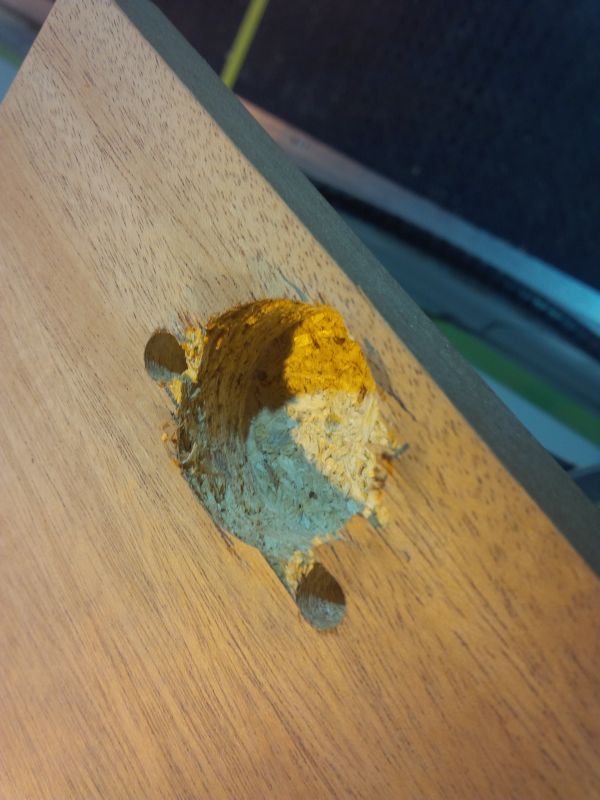
Click here for higher quality, full size image
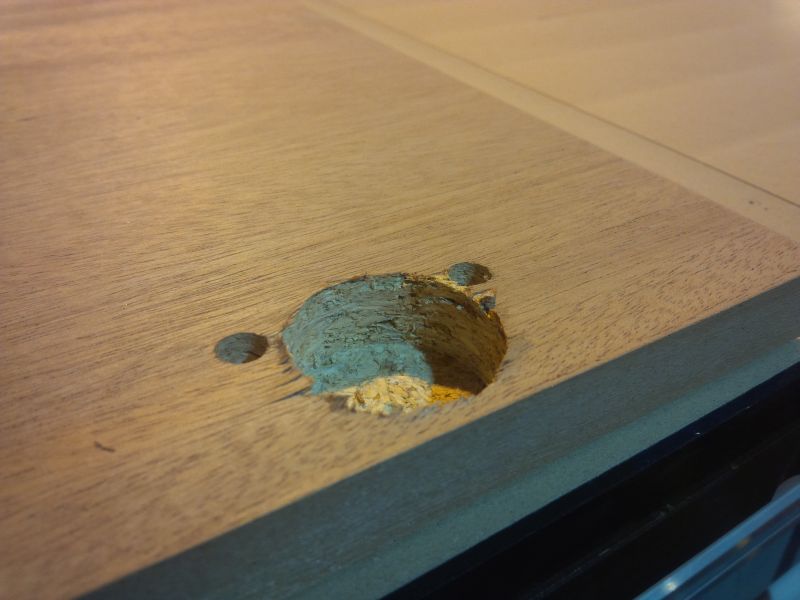
Click here for higher quality, full size image
Forum Responses
(CNC Forum)
From Contributor E:
Looks to me like chips are not clearing and building up above the carbide, then causing side pressure as the bit is extracted. Is it under constant speed when going in and coming out?
From Contributor J:
Try peck drilling and see if that will help.
From contributor R:
Why not tell us the feed speeds, spindle rpm, and drilling program?
From Contributor K:
I run mine with a 1/2 inch bit and let it run a circle pocket. It takes about two seconds per but they are clean.
From contributor T:
Is it being done with a boring block or with a tool mounted in the router? If you think depth is a concern, does it happen if you drill shallower? Are you sure everything is perpendicular? Is the panel moving? Have you tried drilling a pilot hole? Feed and speed as mentioned? There are lots of potential culprits here.
From the original questioner:
The drill is rotating at 4000 rpm, it's a constant speed( it doesn't slow down) and the feed rate isn't very fast at all. I tried slowing down the feed rate to make it easier on the tool, but it may need to be slowed down more. The panel doesn't move so that isn't the issue. I'm using a $150,000 Biesse CNC so the quality of machine shouldn't be a problem. I did speak with tech support about trying to slow down the exit speed, but was told the exit speed is a default speed and cannot be changed. I like the idea of peck drilling. I think I’ll try that next time. I don't drill hinge cup holes every day, so it may be a week before I have more doors to drill.
From contributor B:
Do they need to be that deep? 5/8 seems deep for a concealed cup hole, but I haven't used many different brands of hinge.
From the original questioner:
Yes, they do need to be that deep. We use
Salice soft close hinges. When the hinge closes, the soft close feature of the hinge pushes the plastic cap deeper into the hinge cup hole. The hinges only need a little over 1/2" hole to fit into the door, but they need more than that to function properly. Soon we will be changes over to
Blum hinges so that won't be an issue then.
From Contributor H:
I like the idea of running the hole with a smaller bit doing a spiral ramp. Of course that doesn't answer your question and the process you are using should be able to do the job. What I will suggest is not waiting until your next hinge project. There would be a lot less pressure to get it sorted out if you can find some CNC time before then to work out the problem. That's not so easy to do when there is a stack of doors waiting to be processed.
From contributor R:
I guess it's the engineer in me, but "and the feed rate isn't very fast at all" doesn't help us with your problem. Do you not know the feed rate? A brand and part number, or picture of the bit would also really help. Carbide or HHS? Are the carbides flush with the outside diameter of the bit?
From Contributor W:
We have had issues with melamine blowing out like that. It was the core material. Your core material looks worse, almost like OSB. Try an MDF core. Also check to make sure your bit is in a right hand spindle. I also agree with peck drilling and slow the feed rate going in.
From contributor T:
How old is your machine and is the hinge bit in a boring spindle that is used frequently or used exclusively for hinge bits? Either could cause the springs to weaken in the boring spindle. Also need to verify that the correct fixed cycles are in the correct locations within the machine data. Hinge bits have their own fixed cycle and you may have the wrong cycle in the wrong location. As said earlier, if the material is defective, that needs to be addressed first.
From the original questioner:
The phrase "the feed rate isn't very fast at all" is the industry technical phrase for "It’s Friday, I’m going home, and I won’t have access to that information until Monday". So the feed rate is, 1000mm/min. That’s 39 3/8" per min, aka still not really that fast. I can drill about 90% of the holes with no problem, it’s the 20% of blowout that I can’t have.
The material is 11/16 particle board with 0.5mm of oak veneer on either side. I've also had the issue with plywood core veneered panels, plastic laminate on plywood and particle board core and solid wood doors too. The drill bit is a FSTool 35mm drill bit part no D14A35R and D14A35L. That’ two different rotations therefore two different coupling positions and it happens in both. I've had this same issue on Busellato CNC's and three different types/years of Biesse CNC. I guess I have to be the problem. I am the common factor.
The CNC is a Biesse Rover A3.40 FT. Manufactured in 2007. I've drilled doors on the flat table as well as on the positioned pods, it can happen in both setups. I think I’ll slow the feed rate right down to half of that, maybe 500mm/min or should it be slower than that? What's a common feed rate for a 35mm drill? If I try the peck drilling that should do the trick.
From contributor G:
From my experience, it's 100% core. We do a job cutting store fixture panels that have thirty 25mm holes in red oak plywood. With MDF core panels, I get 100% perfect holes. In Purebond plywood, I get about 30% blown out holes. I had to resort to routing the holes, as no matter what I tried, I couldn't get rid of the bad holes when boring. This was with a brand new 25mm boring bit from Vortex on a Morbidelli.
From contributor C:
The old rule was HSS drills run 3450 rpm. Carbide tipped at 1725. Also when was the last time the collet was changed? Collets work fine for long periods of time and then they fail.
From contributor B:
Peck drilling would answer that problem or even better have the CNC program stop the rotation of the bit and retract itself at 0.00 rpms. You’re asking this bit to go deep so you need to let it clear itself of the cut chips and sawdust.
From contributor L:
To contributor C: It is rare in CNC work to use bits other than carbide. I'd be willing to bet there isn't a drill box made that turns 1725 rpm! It strikes me there are several variables that interact to determine correct rpm - bit diameter, work material and feed speed. Most drill boxes are fixed rpm, typically about 4,000. Our bore and insert machine turns at 7960rpm, 8mm carbide bits. I'd be curious to know where you got the 1725 #.
From contributor C:
I worked at Forest City Tool for 22 Years - 13 Years in engineering and the last 8 years in inside sale - technical info. Smaller diameter bits can run faster. Larger diameter bits run slower. HSS drills are one solid piece of steel. Carbide tipped drills either use a preformed tip or have two chiplifters and two spurs. Solid steel is normally turned and ground and is somewhat balanced. Turned and milled bits are not balanced and suggested to run at slower speeds. Check with your supplier.
From contributor C:
Another thought - I just wonder how well the flat on the drill is interacting with the collet. Not many flats on router bits.
From contributor G:
It's not a collet. It's a 10mm shank boring bit held in with set screws.
From contributor W:
Even more reason to slow the rpm down.
From contributor L:
Reasons for not slowing the bits down: The speed of the direct drive motor is fixed by the manufacturer. The cycle time to drill a hole 19mm deep, 8mm diameter, blow the dust out, inject glue, drive a dowel and move to the next location about 1.2 seconds. Our machine has been doing this for the last six years. Bits (tipped, not solid) last for over 50,000 holes in particle board. Now, about those recommendations. I don't know anything about it other than what I see and have been provided by the German manufacturer. The speed of drilling doesn't so much impress me as the speed to move the drilling units to the next location in what amounts to a fraction of a second. The moves are usually only about 96mm, so not far, but serious acceleration and deceleration!
From contributor S:
To the original questioner: Did you ever get your issue resolved? It almost looks like your bit is spinning backwards to get that much tear out. I run a SCM and get beautiful holes in solid wood, MDF and particle core. How many drill spindles in the block? I would try the bit in a different spindle, and make sure the direction is correct. Even if your spindle is tilted a bit it should drill better than yours is.
From the original questioner:
No. I never did find out the cause. I didn't have any more doors to drill until a couple of days ago. I had 14 doors, 28 35mm holes - 26 of them drill with no problem and two of them are even worse than the picture. I've slowed the feed rate down to the (are you kidding me) speed of 1000mm/min and its step drilling in two passes, but it's still not drilling perfect every time. I'll change the spindle position and see if that makes a difference. Biesse says that the exiting speed of the bit is not adjustable so it pulls up at the same speed every time, I feel that might have some kind of affect to my problem if I could slow that down. It may be a few more weeks until I have more doors to drill.
From the original questioner:
So, I think I figured out the cause or causes of my issue. First off the adjustment grub screw in the end of the shank of the drill bit was backed right out, so the tool wasn't seated as far into the holder as it could be. I did this about a year ago so that I could drill hinge holes into doors that were on a very thin spoil board. The drill wasn't long enough to reach the desired depth without reaching the vertical limit switch. So I adjusted it and seating it right in the holder. I changed the drill bit to another holder position. It’s now in a holder that wasn't used very often. I also increased the feed speed, (not the rotation speed – that’s still at 4000rpm) up to 1500mm/min. I tried drilling at the slower speed in the new holder, it blew out as expected. So far everything seems to be working as it should. With the exception of the feed speed is now too quick to drill through laminate in one pass.
From contributor I:
I had the same problems with hinge boring in laminate. I solved that by regrinding the tool so that the cutting edge is slightly angled up, instead of horizontal. It works!
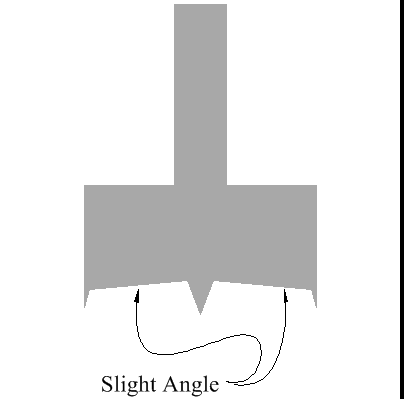
Click here for higher quality, full size image