Troubleshooting Maple Moulder Tear-Out
Too-dry lumber, dull knives, complicated grain patterns, or other maintenance and operational issues could be causing this tear-out problem with Maple wood. February 25, 2009
Question
I am running maple moulding for the first time on my W&H. I am getting huge tearouts on the boards. I thought maybe it was blade sharpness so I sent my blades in to get sharpened. When I got them back I had the same problem. I have a variable speed unit and have been running about 8-10 ft/sec. I just installed a multi pass upgrade. I am doing moulding with the same profile in yellow poplar and haven't had any problems with that.
The guys at W&H said they have never seen anything like it and that maybe I put the multi pass unit on wrong. I guess I could check that seeing it wasn't me that put it in. The one piece I sent in to the guy at W&H said it looked like it had been run backward.
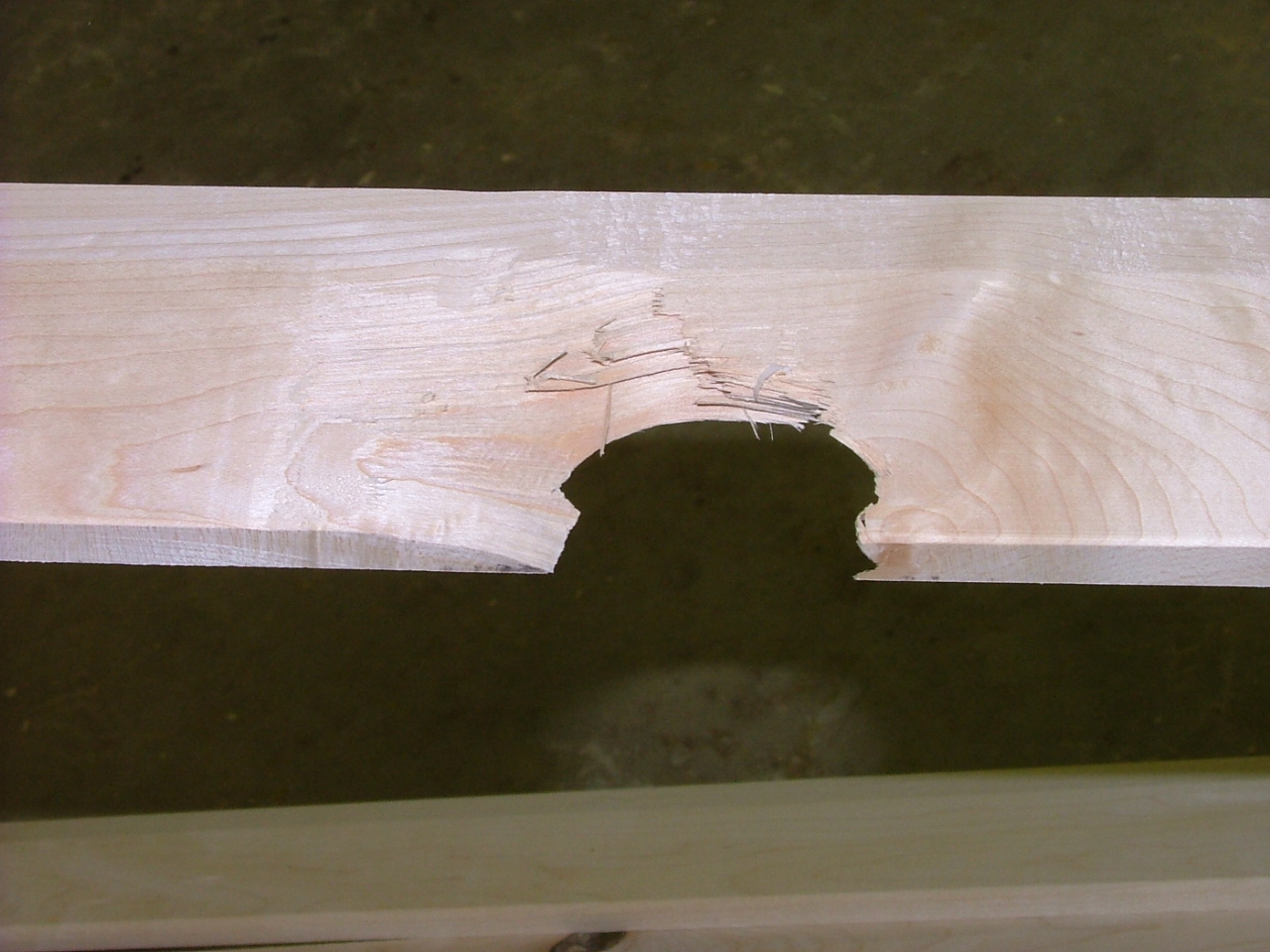
Click here for full size image
** NEEDS IMAGE WORK **
http://www.woodweb.com/images_forums_public/aw/SurpriseMD0024.JPG
** NEEDS IMAGE WORK **
Forum Responses
(Architectural Woodworking Forum)
From contributor D:
Every once in a while I have some tearout problems with maple in my W&H. Taking light passes can help, but feeding so the knives are cutting with the grain usually gets good results. If the maple has grain that swirls or reverses you might want to select boards with straighter grain.
From contributor T:
I had a customer once who got some wood which was too dry. He had the same problems while cutting maple raised panels. He changed wood suppliers and had little or no problems from then on.
From contributor J:
I have to agree with the last person that posted. It sounds like the wood is too dry. I also know that although W/H doesn’t recommend multi passes but I find that it’s absolutely necessary in most situations especially with figured wood or wood that will have a tendency to "switch back" in grain, like maple or birch. Often times I will take my molding rips from the outside edges of wider stock in order to select the more stable, straighter grain stock.
From the original questioner:
Thanks for all of the suggestions. I already try to determine the best way to run each piece. That really helps a lot. And as for multiple passes I always run several passes. I never would have blamed the wood but I can get a moisture meter and find out. There is a noise when I run this stock that I have never heard before. It is like a plucking of the grain. The speed on most of the machines goes from 0-20 ft/sec. I am on the second pass now and am running 8 ft/sec. This pass it much better but still some problems.
From contributor J:
Not to sound like a know it all but I’m pretty sure that the w/h machine isn’t capable of running at speeds of more than 20 lineal feet per minute. 20 lineal feet per minute with a two knife machine would look like you milled lumber with a bulldozer track. The dimensional lumber companies that produce 2x stock for framing etc. are capable of this speed but they have helical or 16-20 knife cutterheads that spin at 7500 rpm's.
Kiln dried native hardwoods and pine have an explosive tendency when they are too dry (6-8 % relative MC) this MC is established not to create a more stable product, but to hold glue for the furniture and panel industries. Wood that is kiln dried and conditioned properly has the least movement. Too dry and it will break like glass. Optimum MC for native hardwood like maple or birch would be between 9-12% . I've milled 6 million b/f of lumber in many different applications including the w/h machines. Don’t be fooled by the woodworking publications that tell us wood must be 6-8 MC. Leave a rip outside overnight (not in the rain) but let it pick up the dew and run that piece and see if you have a better result.
From contributor A:
Another thing to look at is the actual shape of the profile itself and the hold down situation. You got a short flat as the only hold down on the outfeed side and then a long chamfered area that may be "flopping around" while being cut causing tearout. Normally I think you’d be okay with this profile but if you’re having trouble then putting a stiff feather board or some other hold down on the thin outside edge might help a good bit.
Also another trick is that if you’re good with a honing stone, you can make your finish grind less steep by making a small heel on your knives. It’s probably not a good idea to try unless you’re very comfortable with honing stones. W&H come standard with a 23* cutting hook. For maple, most guys recommend 12* cutting. There's not a lot you can do about it but that’s why some woods have more trouble on the W&H (like maple).
From the original questioner:
You are right about the left part of the profile not being supported. I will have to figure out a way to keep that flat.
From contributor L:
If you're running maple at 9-12% in most parts of the country that is way too wet. When we run maple we use 12 or 15 degree heads - 6,000 rpm at 30 to 35'/min. 6" diameter one pass, not jointed. It takes a little more power to run them, probably the reason W&H runs at 23 degrees.
From contributor W:
My vote is for moisture content too high when the moisture content is 6% the chips break up in small chunks and when the moisture content is high it dulls the knifes much faster.
From contributor M:
I have to agree with contributor L. I too run maple with a 12 degree head. 23 degree's is way too aggressive a cutting angle for maple. But having said that, as I look at the picture you posted of your problem, it sure does look like there was a change of grain direction right where your wood blew out and a lesser angle wood have helped in that situation.
From the original questioner:
I can't believe how much great information I am getting. I have one more question. Is it ok the tweak up the blades between sharpenings with a diamond stone? Just hone them a bit on the flat side? Can the angle of the cutter be changed to 12 degrees or are you stuck on 23?
From contributor T:
Due to the design of the machine only one hook angle is available. According to Charles Schmidt Company a stock Williams and Hussey machine feeds at 14 Feet per Minute. They and Williams and Hussey recommend upgrading the machine with a "Feed Master" kit. This kit allows you to adjust the feed rate from 0 to maximum. According to Charles Schmidt Company slowing down the feed rate of the machine can help to reduce the problem you are having on woods with variable grain structure. This allows the machine to take smaller bites so that it doesn't grab onto those direction changes in the grain structure. However, moisture content may still be an issue. Wood with moisture content less than 8 percent can almost shatter like glass.
From contributor L:
Honing on the flat side is probably not a good idea. If you hone a blade it should be done on the bevel and the hone should be moved perpendicular to the cutting edge. If you move the hone parallel to the edge the fine scratches made by the hone will weaken the very edge you are trying to sharpen. If you change the bevel angle near the edge you may introduce a healing action into the cut, which will cause heating and dulling of the knife in addition to glazing the wood.
Glazing can also occur from running too slow of feed speed. The wood needs to advance enough between knife impacts to allow the knife to actually produce a chip rather than just compress the wood. Some compression always occurs just as the knife first hits the wood. Does anyone know of an aftermarket head for the W&H that has 12 degree slots? I realize that this can cause other issues because of the low power available. Any vibration will also increase the chipping problem so you should keep the pressure shoes as snug as possible and still feed OK. Keep the shoes as close to the cutting circle as you can to limit the lifting of the chips, kind of like keeping the throat tight on your hand plane.
From contributor V:
Go ahead and hone the back of the knife on silicon carbide paper spray glued to a piece of thick glass. Work your way up to 600 grit or finer until you can see your reflection in it.
I have done this for years on dozens of knives and I have never had a knife breakage but instead, I have knives that cut better than anything straight off of the grinder. I also recommend buying a set of "Arkansas Files" and use them to hone the bevel/profile of your knives using kerosene as a lubricant. Again, doing this will give you a much sharper knife and nicer cut than any knife that has merely been freshly ground.
I run maple molding on a planer style molder and get very little tearout. The best tip I can give you is to start out with thick enough stock that you have room to flatten your blank stock on the jointer before finish sizing the blanks.
Using the jointer first will enable you to absolutely identify the grain direction in each piece like no other machine or “by eye" method will.
Lastly, an old timer taught me long ago that in most woods you will get less tearout with a deeper cut than you will with shallow cuts because you have a greater thickness of wood "backing up the cut" with deeper passes.