Troubleshooting a "Wandering" Problem when Shaping Door Panels
A look at power feeder, fence, and cutter issues to address snipe at the trailing end of door panels being shaped. January 25, 2010
Question
I’m just wondering what everyone’s thoughts are on shaping door panels. We are currently trying to do it in a single pass, but are getting a bit of wandering on the end of the panel. Should we be milling less material away and finishing with a second pass or is there a good way to keep the panel from pushing away from the cutter?
Forum Responses
(Solid Wood Machining Forum)
From contributor R:
What equipment are you using? I would say the bulk of us are doing it in one pass with the correct machinery.
From the original questioner:
We're using a Steton 733 shaper with a Steff 2034 power feeder. They're both very heavy duty. I don't think the machine has any problem with the material as much as the operator has a problem keeping it flush to the fence as the initial feed goes into the cutter. It looks like it creates a fulcrum at that point and wants to push the tailing end of the panel away.
From contributor D:
Sounds more like an issue with the feeder setup.
From contributor R:
It has to be a feeder or fence issue. You should be able to start it feeding and let go. Sometimes with dull tooling it will put extra pressure on the wood and force it away.
From contributor P:
I am thinking the tooling is dull, or has improper rake or shear geometry. Unless this is a monster size panel raiser, you should be able to take one pass and not push away. An alternative would be to use an outboard type fence, thus the panel cannot move away. You would have to change this for every panel size, kind of a pain.
From contributor O:
Sounds like you are talking about snipe on the ends. Typical raised panel cutters are large diameter so if you are using a typical setup, infeed and outfeed fence there is a very large gap between the two and the ends of the panels are prone to dip into the opening due to lack of support. Depending if you are cutting face up or face down you can attach an auxiliary "fence above or below the cutter to provide continuous support to the panel edge. The drawing below shows a setup for running face up.
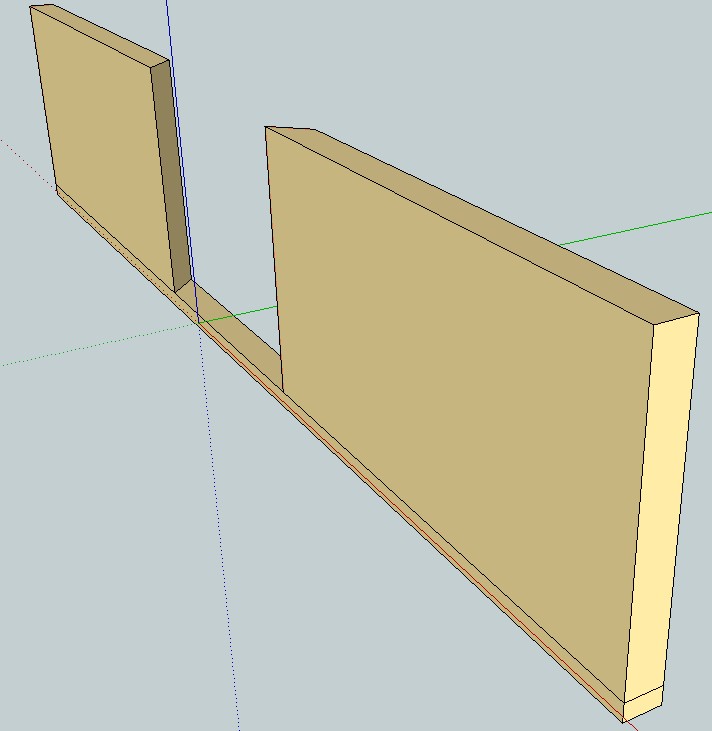
Click here for full size image
From the original questioner:
Thanks for everyone's response. I think the problem is our setup of the power feeder. All the tooling is sharp, and our fence is set up as the diagram in the above response shows. I'm going to adjust the top pressure of the power feeder and perhaps tilt it just slightly toward the fence in an effort to force the material to stay flush. I'll post my results.
From contributor O:
You must always angle the nose of the feeder slightly inward (towards the fence). That is basic for any shaper setup, unless the piece is captured on the outer edge with a feather board or aux fence. If you are unfamiliar with this type of setup remove the cutter and make some dry runs. Be careful, a lot can go wrong on a shaper if you are not thoroughly familiar with it. Be sure to make sure all those adjustments on the feeder are tight as well. I always grab the feeder and physically try to move it around before starting the run.
From contributor H:
The other option is to look for a used Unique Door Machine. It’s way safe and doesn't need a feeder. Plus it will do curves and shapes as well as straight parts.
I use a backcutter with a ball bearing or a spacer between the cutters. It holds the cut at the correct distance so the cutter doesn’t pull the wood in at the opening of the fence. A ring fence does this also.
From contributor Y:
Don't discount contributor P’s thoughts. Improper rake or shear geometry can serve to push the part away from the fence. Our standard insert head is about 15 deg. rake and 10 deg, up shear. The rake angle actually helps pull the part into the fence. I've seen reputable companies make big mistakes when it comes to raised panel tooling.