Pine Board Sheathing for Homes
Works fine in most cases — here's some useful advice about practicalities and codes. July 14, 2010
Question
It seems that 1/2" OSB has replaced 1/2" CDX as sheathing for most residential construction. In the interest of getting rid of my stacks of excess, lower quality pine boards, I am considering going old school and using it to sheath a spec house next spring.
My questions are:
1) Would board sheathing make a house more susceptible to mice?
2) Would putting a shiplap on the rough-cut boards eliminate the need for let-in bracing or diagonal sheathing?
3) Is there a potential market for board sheathing for people who don't want exposure to outgassing of OSB and Advantek?
Forum Responses
(Sawing and Drying Forum)
From Professor Gene Wengert, forum technical advisor:
The plywood or OSB sheathing provides a much more rigid structure than board sheathing. As most houses use poly vapor barriers on the inside, the off-gas from wall sheathing is not a factor.
1. Properly done, I cannot see a difference.
2. Check with building code people to see what they will accept. At the least, I think you should use OSB for the corners. The higher cost of installation for boards would seem to make this an expensive way to get rid of your surplus.
3. I doubt that this is an issue for a home buyer.
From contributor D:
I am building a cabin and garage in Colorado. Have to use store bought wood for framing but everything else is SYP. Beams are much larger than needed, but with an engineer stamp and his blessings, so far the local inspector is okay with it all.
To answer your question about the pine siding, that is exactly what I am doing. I am milling the wood here in Florida on my Timberking B-20 and hauling it to Colorado. What I have done is sheet it with OSB, cover that with Tyvek and put 8" wide SYP boards over that, then 2" battens.
Looks good and so far is weathering really nice. To speed up the weathering I will coat the exterior wood with a solution made from vinegar and steel shavings for that really old looking effect.
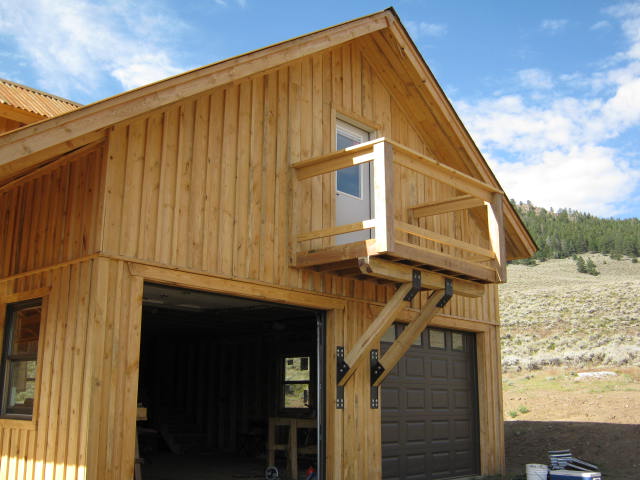
Click here for higher quality, full size image
From Professor Gene WEngert, forum technical advisor:
That is certainly a beautiful looking building.
The original question was the use of pine boards for sheathing and not siding. My response is in reference to sheathing, and not siding.
From contributor O:
Wall sheathing is the cheapest sheathing at under $0.25/bf. Floor sheathing is typically the most expensive running close to $1/bf. Roof sheathing would be in between. In my code book this would be allowed in any of those applications as long as you aren't in a high wind or seismic zone. NH has a native lumber law as far as grading is concerned.
From contributor C:
Many years ago, I was involved in the construction of a couple of homes that used native pine (NE US) for sheathing. The pine was surfaced for uniform thickness, and applied diagonally. When applied diagonally, it makes for a very rigid structure - likely not as rigid as a structure fully sheathed with plywood, but very rigid none the less.
I would recommend surfacing the material for uniform thickness. Otherwise I would think you'll be fighting the rough sawn variances throughout the siding process. Also, some sort of "coverage" joint - shiplap or tongue and groove - should be used if possible to prevent gaps at the joints as the material shrinks and/or swells.
And most importantly, if applied diagonally, book match the application on a wall rather than applying in only one direction. When applied in one direction, the entire house will twist as the sheathing dries. There are a number of old texts I recall reading that were adamant about this.
From contributor P:
I am a cattle rancher, not a carpenter, and now a part to full time sawyer. I built a house last winter using green rough cut lumber all the way, all oak except for some cedar paneling. We full sheathed the roof and walls with rc 7/8'' x 8'', 10'', and wider boards up to 16''. Used tar paper under the sheet metal roof and house wrap under sheet metal on the sides. I so far can tell no adverse effects from this. Sturdy it is, though. I don't know about pine, but oak doesn't shrink length ways much. I can't see how board shrink width ways, when put on a diagonal (how we did ours), could cause a house to twist. I live in northeast Oklahoma, about 2 miles from where the f-5 tornado went in 07. The debris that I was involved in cleaning up had no pieces of ODB bigger than 12''. This convinced me not to rely on that fake wood for the strength on my home.
From contributor A:
We do it all the time. Most is shiplapped 4, 6, 8 inch wide and the corners are put in diagonally. Makes for very strong wall. Also we put siding over it and the homes are very quiet inside. We deck roofs and cover timber frames and it is getting to be a good selling point.
Building "green" here means the boards have not traveled over 100 miles and are not glued together. Yes, it takes longer and may cost a bit more, but then better things usually do.
From contributor B:
I work in the Washington DC Historic Preservation Office. For roof, siding, and porch restorations in our historic districts, if board sheathing has rotted away and needs to be replaced, we restrict against OSB, etc. as the replacement material. We require new sheathing to match the thickness and type of the original, still existing sheathing. This is especially important with slate roofs.
From contributor P:
Contributor B, thank you for pointing this out. The use of boards for replacement sheathing on those historic buildings is a great reason to find a sawmiller to help with restoration. I bet most of the sizes of lumber on those old buildings don't match anything that can be bought at most lumberyards!
From contributor B:
You're exactly right about the dimensional differences between historic board sheathing and modern stock.